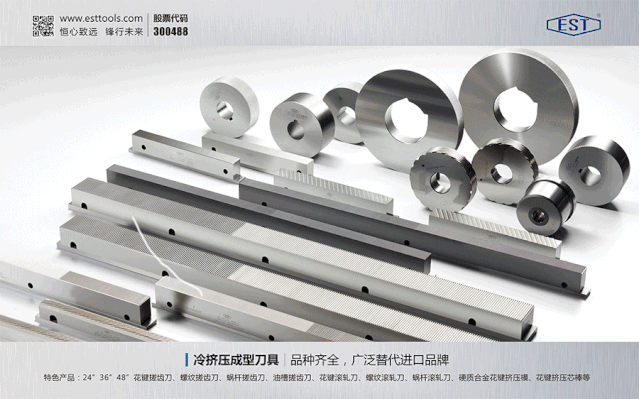
机械零件在生产过程中,由于受到轧制工艺、生产设备等因素的影响,导致加工工件表面出现凹槽、孔洞和划痕等缺陷。目前,工件表面缺陷自动检测方法主要有射线检测法、超声波检测法和机器视觉法等。射线检测法通过射线强度的不同检测工件表面形态,检测灵敏度高,但放射源使其存在安全隐患。超声波检测法穿透力强、操作安全,但检测效果受传播方向的影响,漏检率较高。机器视觉检测法利用CCD相机拍摄工件表面形貌,通过图像识别检测工件表面缺陷,适用范围广、检测速度快、灵敏度高,但只能检测工件表面二维信息,无法检测三维信息。
近年来,光栅投影三维检测技术由于检测灵敏度高、速度快等特点已经被应用到工件缺陷检测中。陈松林等针对飞机蒙皮对缝阶差与间隙的数字化检测问题,以光栅投影技术为基础,实现了飞机蒙皮对缝的检测。Zhang Y.等研究了小波变换轮廓术(WTP)方法,通过对云纹图像小波变换实现了动车组车轮表面等大尺寸物体的三维重建,且可较好地识别车轮的表面缺陷。周贤善等针对焊膏印刷质量三维缺陷检测存在速度慢和精度低的问题,提出基于光栅投影相位测量轮廓术的三维测量方法,快速准确地检测出SMT焊膏印刷的缺陷。以上方法在测量较深缺陷时,由于缺陷边缘的遮挡会形成投影盲区而导致云纹的中断,无法准确重建阴影区域,导致缺陷的重建误差较大,难以保证检测结果的准确性。
本文在光栅投影的基础上,提出了一种双投影的工件表面缺陷检测方法,以实现工件厚度和表面缺陷的准确测量。该方法在两个方向上设置数字投影仪并交替投射光栅场,CCD相机分别采集工件表面云纹图像,利用相移法求解出两个方向的相位,并将重建的三维轮廓进行融合,实现工件厚度与表面缺陷的准确检测。
1 系统原理及设计 (1)检测系统的设计工件表面检测系统由数字投影仪1、CCD相机和数字投影仪2组成。系统成像结构如图1所示,数字投影仪交替投影等间隔明暗分布的光栅场,CCD相机分别采集工件表面云纹图像,对左右两个方向投影的同一区域进行三维重建,经过重建数据融合得到工件表面三维轮廓。
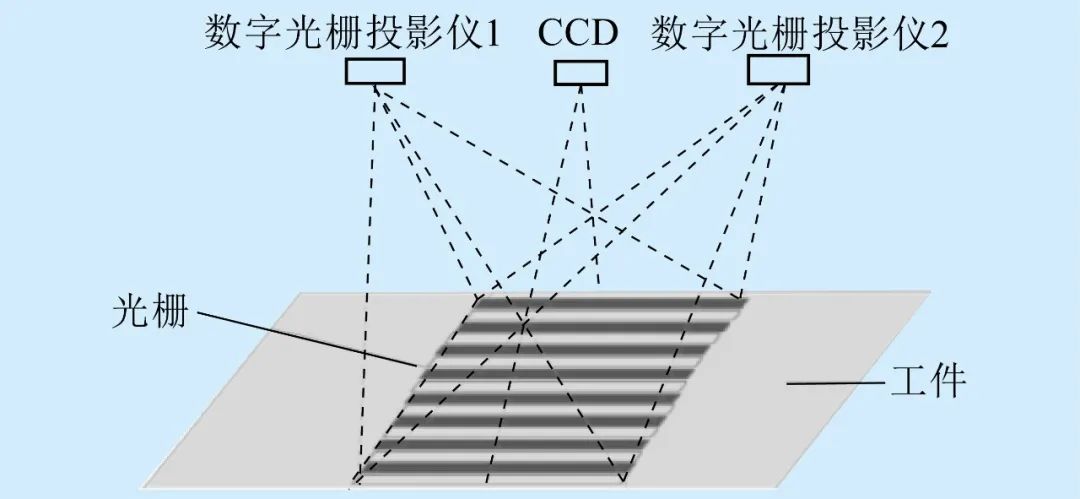
相位测量轮廓术是一种重要的被动三维形貌测量法,具有高精度、不受物体表面反射率影响等特点。数字投影仪投影光栅条纹到工件表面,由于受到工件表面的高度调制光栅条纹发生变形,其变形光栅场的数学公式可以表示为
本文采用四步相移法准确求解相位值,数字投影仪投影相移为0、π/2、π、3π/2的光栅场,CCD相机采集到对应的四帧条纹图分别为
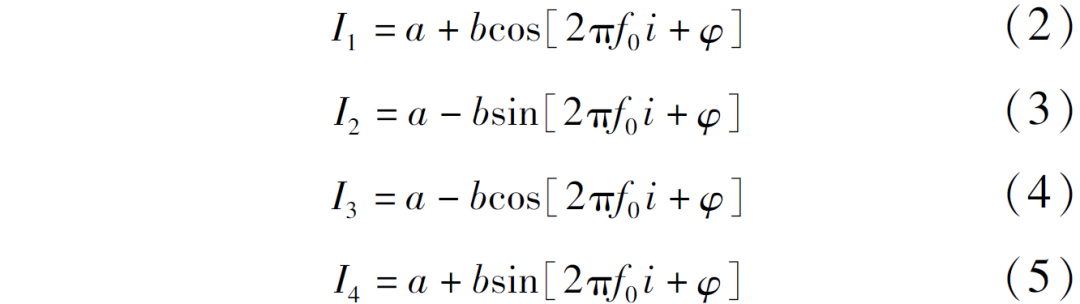
从上式表示的4幅云纹图像中可以求出被测工件表面的相位分布φ(i,j)为
由于相移法得到的相位φ(i,j)是由反三角函数arctan计算得出,因此求解得到的相位值φ(i,j)分布范围为[-π,π]之间,需要将工件包裹相位展开成真实相位,进而恢复工件表面的三维轮廓。
目前相位展开算法有枝切法、质量图导引法、最小二乘法等。最小二乘法相位展开效率高,但是展开结果误差较大,无法准确重建工件轮廓。质量图导引法展开相位精度高,可以准确重建工件轮廓,但是展开时间过长,效率低。枝切法展开相位运算速度快、相位误差较小,能准确恢复工件三维轮廓,满足工件表面缺陷检测的精度要求。
(3)重建数据融合原理CCD相机采集4幅相移云纹图像为I1(i,j)、I2(i,j)、I3(i,j)和I4(i,j),条纹背景图可以表示为
对条纹背景图二值化,得到左右两侧阴影区域位置为II1(i,j)和II2(i,j)。
重构的阴影区域工件表面轮廓HA1和HA2可以表示为
两次投影后工件均不受阴影影响的区域为HB,其重构的轮廓可以表示为
重构工件的表面轮廓H可以表示为
采用倾斜投影和垂直拍摄的方式采集工件表面云纹图像,CCD相机与数字投影仪距离为300mm,CCD相机与参考平面距离为500mm,投影光路与CCD光路夹角为30°,试验装置见图2。
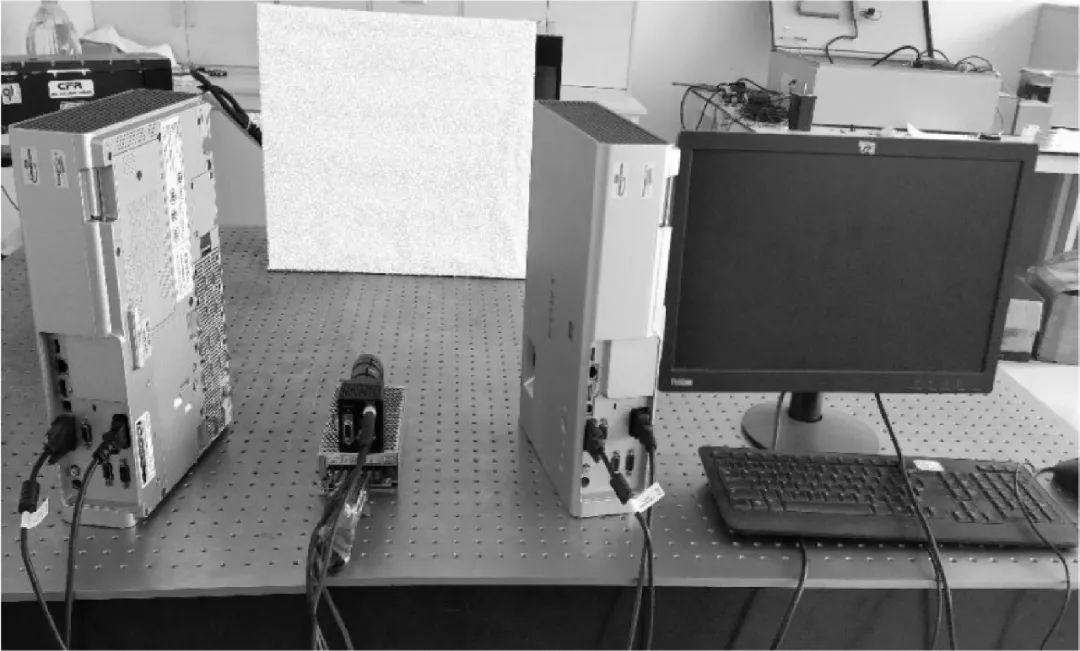
图3为工件孔洞缺陷的检测结果。图4为单投影仪检测方法与本文提出的检测方法重构缺陷的某一横截面检测结果对比,a代表单投影仪检测方法的重建结果,b代表本文方法的重建结果。工件表面划痕缺陷检测结果见图5。
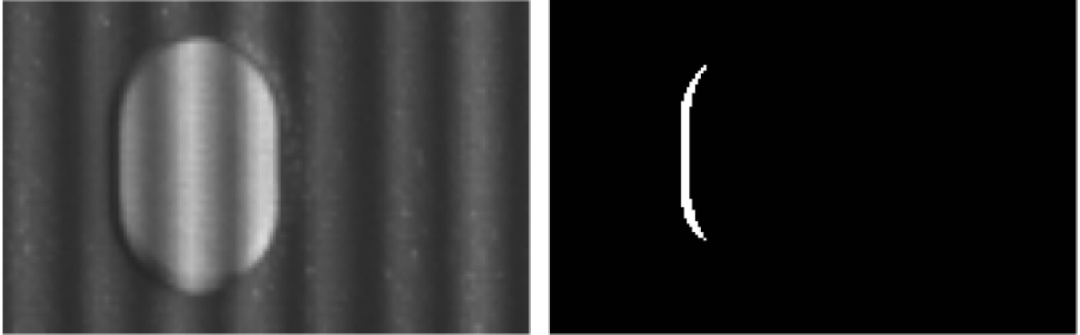
(a)孔洞缺陷光栅条纹 (b)阴影区域位置
(c)孔洞缺陷三维重构结果
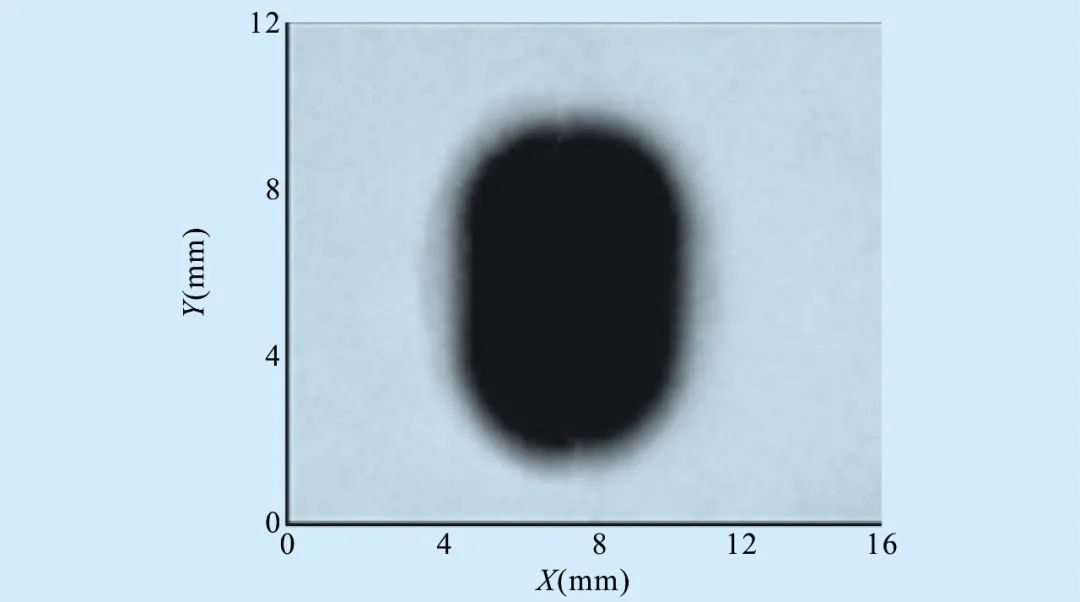
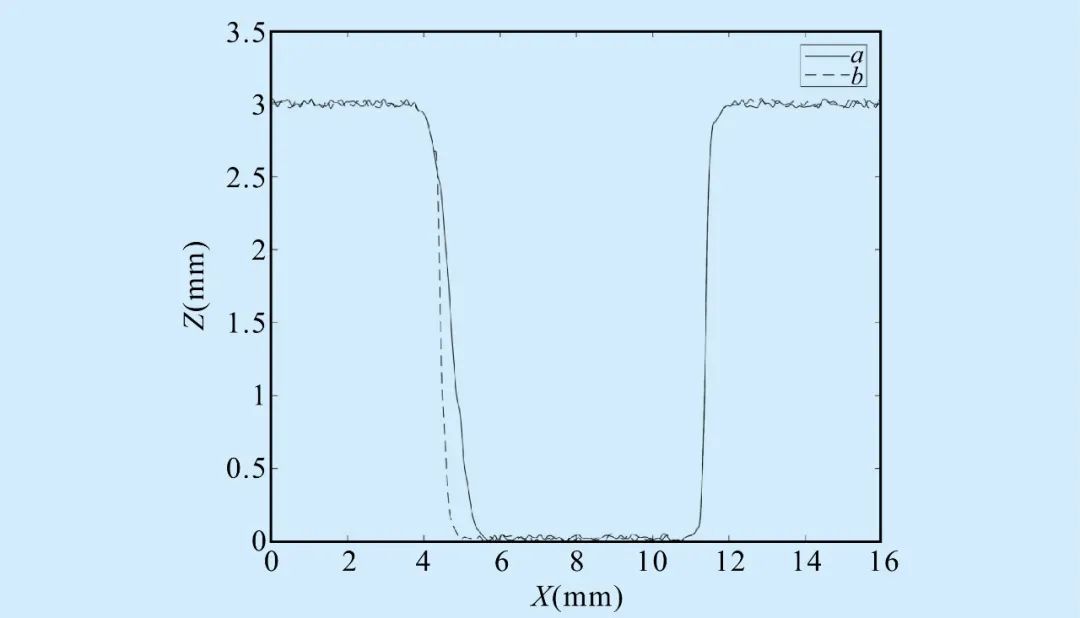
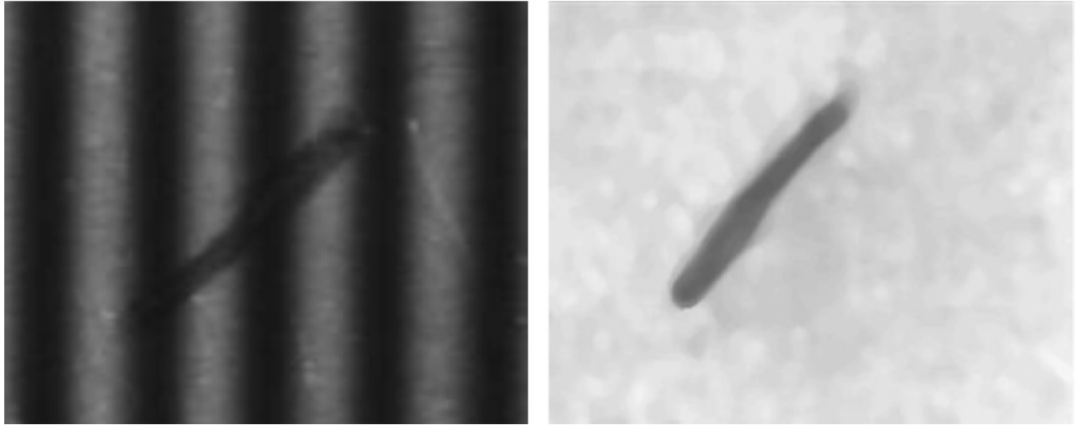
为了验证方法的准确性,分别检测了5块不同厚度的块规样品。表1为使用基于双投影的块规厚度测量结果与基于单投影的测量结果的对比,提取测得的块规厚度最大值和最小值作为检测的厚度范围。以深度较大的孔洞缺陷为例,表2是对工件不同孔洞缺陷最大直径测量结果的对比。第1组数据为单投影测量系统对于工件孔洞缺陷的测量结果,第2组数据为采用本文方法的测量结果。
表3是检测缺陷最大边界距离的对比。第1组数据为游标卡尺测量结果,第2组数据为单投影检测结果,第3组数据为采用本文方法的检测结果。
表1 两种方法的厚度测量结果(mm)
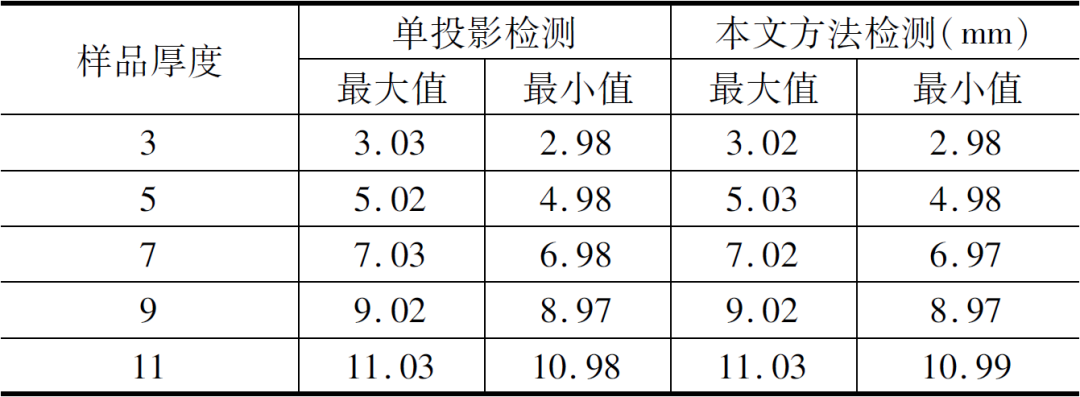
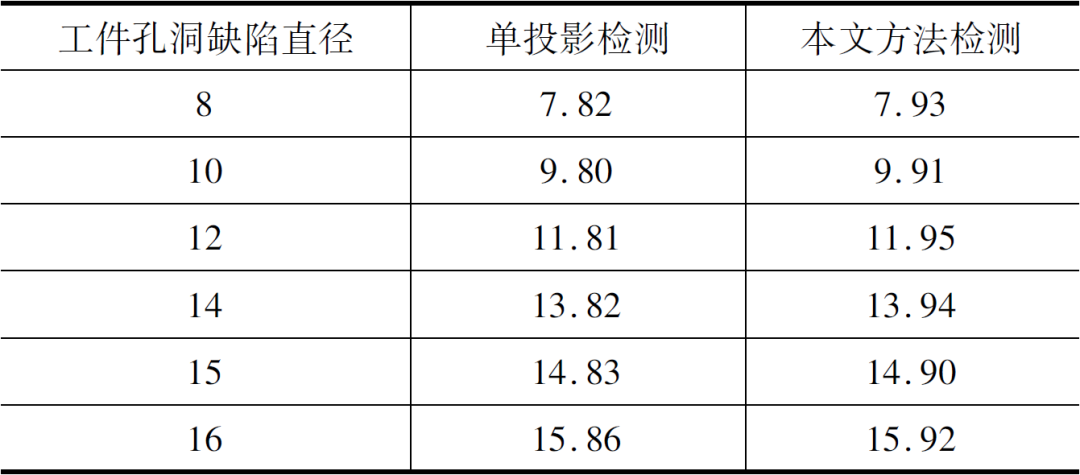
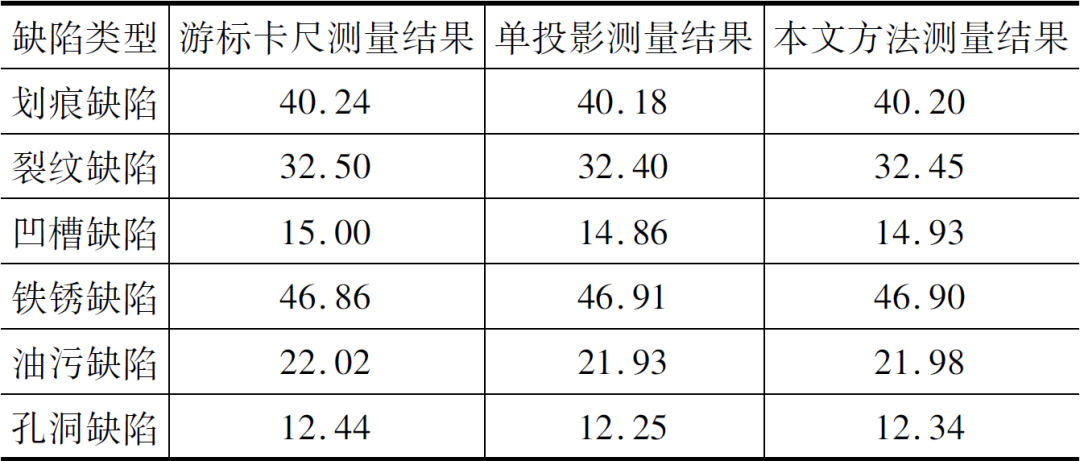
由表格测量数据可以得到,基于单投影的检测方法的厚度测量精度与本文检测方法的检测精度一致,都在0.05mm之间;单投影检测方法的表面缺陷检测精度为0.2mm,本文检测方法的检测精度达到0.1mm,检测精度相对于单投影测量方法提高了0.1mm;划痕、裂纹、铁锈等缺陷由于深度较小,无法正确重建缺陷的三维形貌,只能重建该类缺陷的二维平面信息,凹槽、孔洞等深度较大的数据可以重构出缺陷的三维形貌,但边缘阴影区域的影响造成该类缺陷重构误差较大。本文方法避免了投影盲区对工件表面缺陷三维重构的影响,提高了检测精度。
4 小结根据现有工艺,提出了一种基于双投影的工件检测方法,实现了工件厚度与表面缺陷的同时测量。相比于单投影的工件检测方法,该方法能准确测量深度较大缺陷。经过试验验证,此方法检测工件厚度的精度可达0.05mm,检测表面缺陷的精度可达0.1mm。
原载《工具技术》 作者:常轶民
书讯
⏩《现代刀具设计与应用》
⏩《工具热处理技术与实践》
⏩《常用孔加工刀具》
⏩《高效高精度孔加工刀具》
欢迎关注工具技术微信公众号:gjjs1964 E-mail:toolmagazine@chinatool.net toolmagazine@163.com 论文投稿系统: http://gjjs.cbpt.cnki.net http://gjjs1964.com.cn http://www.chinatool.net
|