电磁感应理论成熟,感应加热是已经得到了广泛应用的加热方法,尤其在表面热处理中,具有工艺简单、变形小、效率高、节能环保、工艺过程易于实现自动化、淬硬层性能优异等优点。随着工业技术的不断进步,感应加热也越来越绽放其灿烂的异彩。
感应加热设备按电源频率可分为工频、中频、超音频、高频,其各自的频率范围和加热的功率密度见表1 。
▼表1 感应加热频段的频率范围和加热功率密度
一、感应加热原理
感应加热原理图
感应加热的主要依据是:电磁感应、“集肤效应” 和热传导三项基本原理。
当交变电流在导体中通过时,在所形成的交变磁场作用下,导体内会产生感应电动势。由于越接近心部,感应电动势越大,导体的电流便趋向于表层,电流强度从表面向心部呈指数规律递减,如图1 所示。这种现象即所谓交变电流的集肤效应。
▲图1 交变电流在导体中的分布情况
图2 所示,为两根矩形截面的导体同向电流和反向电流时的磁场分布情况。由于电源电动势和自感应电动势的作用,同向电流系统中最大的磁场强度产生在导体表面的外侧,反向电流系统最大磁场强度产生在导体表面内侧,这就是邻近效应。
利用邻近效应,可以选择适当形状的感应器对被处理零件表面的指定部位进行集中加热,使电流集中在与感应器宽度大致相等的区段内。
导体间的距离越小临近效应表现的越强烈。
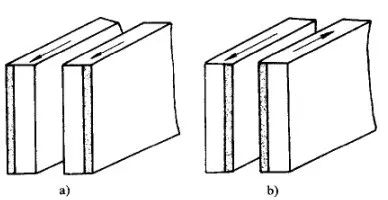
通过感应圈的电流集中在内测表面的现象称为环状效应,见图3 。环状效应是由于感应圈交流电流磁场的作用使外表面自感应电动势增大的结果。
▲图3 交流电流的环状效应
加热外表面,环状效应是有利的,而加热平面与内孔时,它会使感应器的电效率显著降低。为了提高平面和内孔感应器的效率,常常设置导磁体,以改变磁场强度的分布,迫使电流趋近于零件所需加热的表面,见图4 。由图可见,导磁体有把电流驱向其对侧的作用。
▲图4 加导磁体后电流在感应圈中的分布
a)内孔加热 b)平面加热
表面效应、邻近效应、环状效应均随交变电流频率的增加而加剧。此外,邻近效应和环状效应还随导体截面的增大、两导体间距的减小和圆环半径的减小而加剧。
由磁场强度分布方程可得出
式中:
若将上式画成曲线图,其结果如图5a)所示。
▲图5 涡流强度由工件表面向纵深的变化
I0-表面涡流强度 I2-距表面 x 处的涡流强度
从式中得知,K=;但由磁场强度分布的基本方程式得知,K²=8πμf/ρ,故
K==
式中 ρ——材料的电阻率(Ω·cm)
μ——材料的磁导率
f ——电流的频率
磁场强度分布的基本方程表明,涡流强度随表面距离的变化呈指数规律。涡流高度集中在表层中,它随距离的增大而急剧下降。在工程应用中,规定 Ix 降至表面的 1/e (e=2.718) 处为电流透入深度,并用δ表示。如果 ρ 的单位为 Ω·cm ,则可用下式求 δ(mm)
由于涡流产生的热量与涡流的平方成正比(Q=0.24I0²Rt),所以从表面向心部的热量的下降比涡流下降更快(见图5 b))。计算证明,86.5%的热量是发生在δ 的薄层中,而在 δ 薄层以外的部分没有涡流。上述规定在实际应用中已具有足够的精确度。
钢铁材料的电阻率 ρ 在加热过程中随温度的升高不断增加(在800-900℃范围内,各种钢的电阻率基本相同,约为10E-4 (Ω·cm);磁导率 μ 在失磁点以下基本不变(其数值与强度有关),但在达到失磁点时,突然下降为真空的磁导率 μ=1。见图6 。因此,当温度到达失磁点时,涡流的透入深度将显著增大。超过失磁点的涡流透入深度称为“热态透入深度”。低于失磁点时称为“冷态涡流透入深度”。
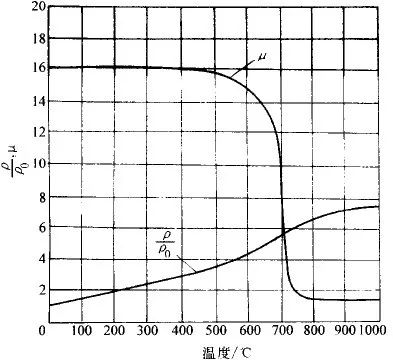
热态涡流透入深度比冷态透入深度大许多倍,见图7 。
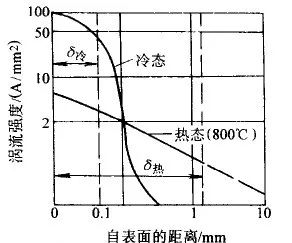
在感应器接通高频电流,工件温度开始升高前的瞬间,涡流强度自工件表面向纵深的变化是按冷态特性分布的,见图8 中曲线1 。当表面出现超过失磁点的薄层时,在和薄层相邻的内部交界处的涡流强度就发生突然变化,工件加热层被分成两层,见图8 中曲线2、3 。外层的涡流强度显著下降,最大涡流强度处于这两层的交界处。因而高温表层加热速度迅速降低,交界处升温加速,并迅速向内推移。
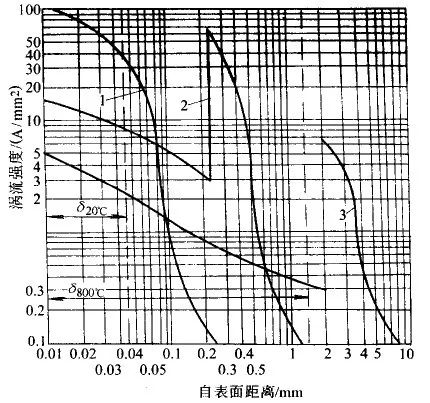
表2 和表3 列出了在各种频率下的电流在纯铜与45钢冷态与热态中的涡流透入深度。
▼表2 不同频率电流下45钢与 Cu 的电流透入深度(mm)
▼表3 不同频率电流在45钢中的透入深度
这种靠涡流不断向内部 “步进” 的电加热方法是感应加热所独有的,在快速加热条件下,即使向零件施加较大功率时,表面也不会过热。
当失磁的高温层厚度超过热态的涡流透入深度以后,加热层深度的增加主要靠热传导的方式进行,其加热过程及沿截面的温度分布特性同用外热源加热的基本一样,此时加热效率要低得多。
进行一定深度的表面加热时,应该力求用涡流“透入式加热”。为了做到这一点应该正确选择电流频率,同时所选择的加热速度应能够在尽可能短时间内达到规定的加热深度。
在选择电流频率时,必须遵守下列条件:
(1)对于一定尺寸的工件和感应器来说,所选择的电流频率不应低于某一数值f1,否则工件只能加热到失磁点左右的温度,见图9 。
(2)所选择的电流频率最好高于图9 中的f2 。当频率为f2时,感应器效率最佳。当采用f1与f2之间的频率时,感应器效率较低。
(3)在所有情况下,应尽可能采用涡流 “透入式加热” 而不采用热传导加热。
为了满足上述条件,f1、f2与工件尺寸应有如下关系:
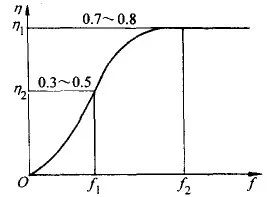
表4 是根据上述关系所要求的电流频率与所对应的被加热工件最小直径和合理的淬火深度范围。
▼表4 工件直径、合理的淬火层深度与电流频率的关系
二、钢件感应加热的相变特点
感应加热属于快速加热。加热速度对相变温度、相变动力学和形成的组织都有很大影响。
在分析示波器记录的钢在感应加热时的温度-时间曲线(图10)时得知,钢铁材料在失磁后,加热速度下降数倍,这是感应加热的特性。
分析感应加热中加热速度对有关相变过程的影响时,应采用失磁后的加热速度,它能客观地反映相变温度区间的加热条件,可称为相变区间的加热速度。相变区间的加热速度可以由实验确定。
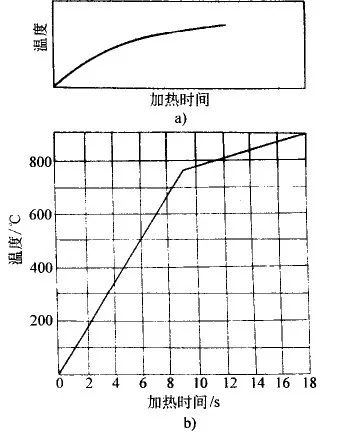
2.1 快速加热对相变温度及相变动力学的影响
2.1.1 加速度对 Ac1、Ac3、Accm 的影响
图11 所示,是纯铁、亚共析钢中自由铁素体和各种不同原始组织的共析钢(T8)等材料的临界点与加热速度υH的实验结果。
加热速度(℃/s)
▲图11 纯铁、亚共析钢和T8钢的临界点与加热速度的关系 1、2、3-T8钢,原始组织分别为淬火、正火、退火 4-纯铁 5-亚共析钢的自由铁素体由图可见,对所有试验材料,其临界点均随加热速度的增大而提高。铁素体-碳化物组织越粗大,临界点上升也越快。在快速加热时,珠光体向奥氏体转变是在图12 所示的平台以上几十度的温度范围内完成的。该图表明,加热速度越快,相变进行最激烈的温度和完成相变的温度越高,但亚共析钢中的自由铁素体向奥氏体转变的温度上限不会超过910℃,因为此时α-Fe 可以在无碳的条件下转变为 γ 相。
▲图12 w(C)0.85%的钢在各种加热速度下的温度-时间曲线
2.1.2 加热速度对相变动力学的影响
在一般等温条件下,珠光体向奥氏体转变的速度随等温温度的提高而加快,见表5、图13 。
▼表5 珠光体在不同温度下转变为奥氏体的时间(w(C)0.86%)
▲图13 珠光体转变为奥氏体的等温温度与时间的关系(GCr15)
1-转变开始 2-转变完成
在连续加热的条件下,珠光体向奥氏体转变动力学也可用图3 来说明。由A1 点出发的不同仰角的射线表示相变区的各种不同的加热速度。他们分别与曲线1和曲线2相交于 a1、b1......和a2、b2......显然,加热速度越大(v2>v1),进行相变的温度就越高,而所需要的的时间就越短。
以不同速度加热所得到的奥氏体,冷却时的等温转变动力学曲线如图14 所示。
▲图14 40Cr和40CrNi钢过冷奥氏体等温转变曲线
与加热速度的关系(奥氏体化温度为950℃)
a)40Cr b)40CrNi
×-感应加热,v=225℃/s
○-感应加热,v=120℃/s
△-炉中加热 ,v≈0.2 ℃/s
由图可见,在加热温度相同的的条件下加热速度越高,奥氏体的稳定性就越差。这是由于加热速度越高,加热时间越短,形成的奥氏体晶粒越小,且成分不均匀。提高加热温度,奥氏体的稳定性将会增加。
2.2 快速加热对相变后的组织与性能的影响
2.2.1 加热速度对奥氏体晶粒大小的影响
实践证明,对具有均匀分布的铁素体和渗碳体组织的钢进行快速加热时,当加热速度由0.02℃/s 增高到100~1000℃/s 时,初始奥氏体晶粒度由 8~9级细化到 13~15 级。加热速度为10℃/s 时初始奥氏体晶粒度为11~12 级。要得到14~15级的超细化晶粒必须采用100~1000℃/s 加热速度,见表6 。
▼表6 几种钢在不同加热速度连续
加热条件下,转变终了温度与
初始奥氏体晶粒面积的关系
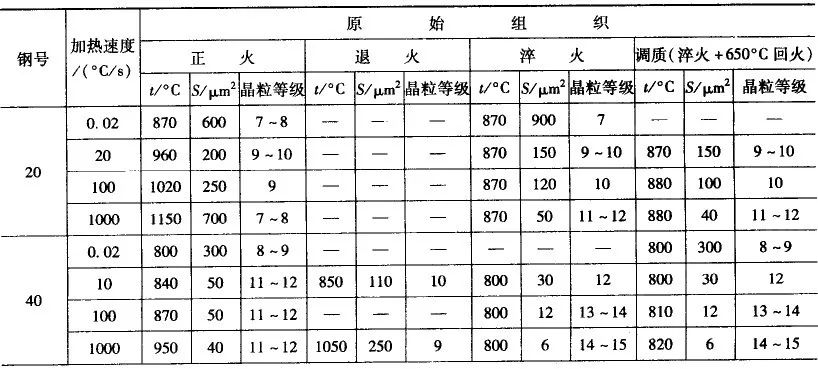
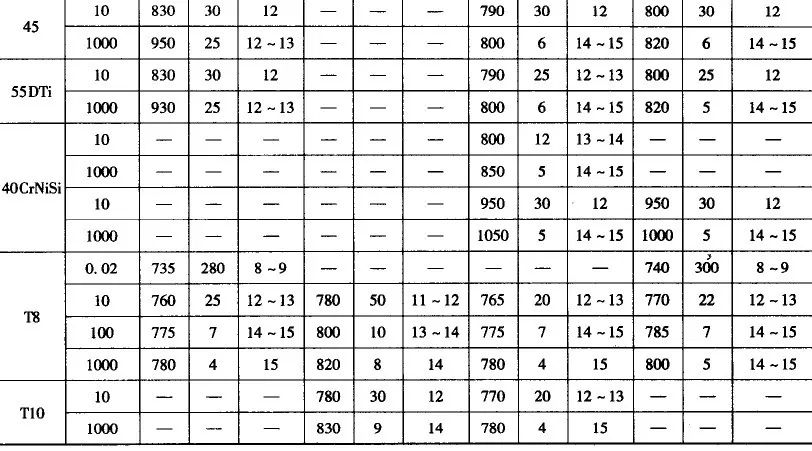
在生产中采用大于3~10℃/s 的加热速度可得到11~12 级的奥氏体晶粒。如果要得到 14~15 级的超细晶粒,必须先进行淬火或调质处理以消除自由铁素体,并采用高达100~1000℃/s 的加热速度。
2.2.2 加热速度对淬火钢组织的影响
在快速加热的条件下,珠光体中的铁素体全部转变为奥氏体后,仍会残留部分碳化物。即使这些碳化物全部溶解,奥氏体也不一定会全部均匀化。淬火后将得到含碳量不等的马氏体。提高加热温度可以减轻或消除这些现象,但温度过高又将导致奥氏体晶粒粗大。
对于碳钢,即使加热到910℃以上,在快速加热条件下,仍难于完成奥氏体的均匀化,有时甚至会在淬火钢中出现铁素体。
当材料原始组织一定时,加热温度应根据加热速度选择。
2.2.3 加热速度对表面淬火件硬度的影响
感应加热表面淬火时,在一定的加热速度下,可在某一相应的温度下获得最高硬度,见图15 。提高加热速度,这一温度向更高的方向推移,见图16 。
▲图15 表面硬度与加热温度的关系
(加热速度为380~400℃/s)
▲图16 在不同加热速度下的表面硬度与淬火温度的关系
对相同材料,经过感应加热表面淬火(喷射冷却)后,其硬度比普通加热淬火的高2~6HRC(见图17)。这种现象称为 “超硬度”。

2.2.4 表面淬火的耐磨性
零件工作时的磨损量在很大程度上取决于硬度。对同样的材料,高频淬火零件的耐磨性比普通淬火零件高得多(见图18)。
▲图18 淬火过的45钢的平均磨损
2.2.5 抗疲劳性能
在采用正确的表面淬火工艺获得合理的硬化层分布时,可以显提高工件的抗疲劳性能。
如果工件表面有缺口,采用表面淬火几乎可以完全消除缺口对疲劳性能的有害影响(见表7)。
▼表7 高频表面淬火对40CrNiMo钢疲劳性能的影响
表面淬火能提高钢疲劳强度的原因除表层本身强度的提高外,还在表面形成很大的残留压应力有关。表面残留压应力越大,钢制工件的抗疲劳性能就越好。淬硬层过深会降低表面残留应力,只有选择最佳的淬硬层深度才能获得最高的疲劳性能,见图19 。
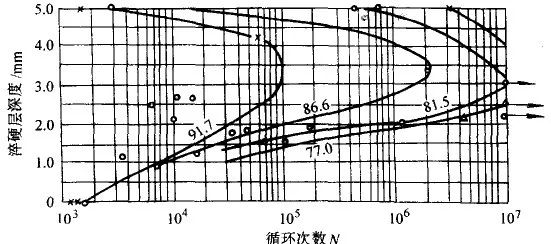
若硬化区分布不合理,例如过渡层在工作长度内露出表面,此处就往往成为疲劳裂纹源,其结果将使疲劳寿命比不淬火还低。
2.3 原始组织对快速加热相变的影响
钢的原始组织不仅对相变速度起决定性的作用,而且还会显著地影响淬火后的组织和性能。原始组织越细,两相接触面积越大,奥氏体形核位置就越多,碳原子扩散路程越短,越会加速相变。对组织和性能要求严格的零件,采用感应淬火时,事先应对钢材进行预备热处理。结构钢的预备热处理多为调质。
end