本节书摘来自异步社区《3D打印:正在到来的工业革命(第2版)》一书中的第2章,第2.3节桶式光聚作用,作者 【英】Christopher Barnatt(克里斯多夫),更多章节内容可以访问云栖社区“异步社区”公众号查看
2.3 桶式光聚作用
正如我们已经看到的,材料挤出是3D打印输出多种现有材料的一种形式。这是一项相对容易操作的技术,因此使用该种工艺的3D打印机售价也比较低廉。也就是说,虽然目前几乎所有的消费级3D打印机都基于材料挤出工艺,但是工业级3D打印机因其造价昂贵的黏合粉末、固化液体或黏合材料层等工艺,使用起来更加精准。这些技术中的第一类是“桶式光聚作用”,通过使用光源固化桶内液体感光树脂表面或底部的连续物体层。虽然这听起来十分具象,但是桶式光聚作用已经通过“光固化快速成型工艺”、“DLP投影技术”、“扫描、旋转和选择性光固化”、“基于光刻的陶瓷制造”,以及“双光子聚合技术”这五种不同的方法实现了商业化。
2.3.1 光固化快速成型工艺
光固化快速成型工艺是有史以来第一个3D打印技术,它是在一桶(或一池)液态感光性树脂内通过使用计算机控制的激光束来构建3D物体。第一台光固化快速成型3D打印机由3D Systems制造,也被称为“光固化快速成型设备”或“SLA”。
在大多数的SLA硬件上,物体都是在穿孔的制作平台上进行创建,这个平台位于桶中感光性树脂表面。然后UV激光束在液体表面勾勒出物体的第一层形状,这可起到固定作用,然后制作平台稍微降低一点。接着更多的液态感光树脂流到物体第一层的上面,或者通过机械装置使池中表面液体强行穿过物体第一层,再用激光勾画出下一层并固定。反复重复此过程直至打印完整个物体。最后制作平台回到表面并与物体脱离。图2.6展示了传统的光固化快速成型3D打印法的过程。
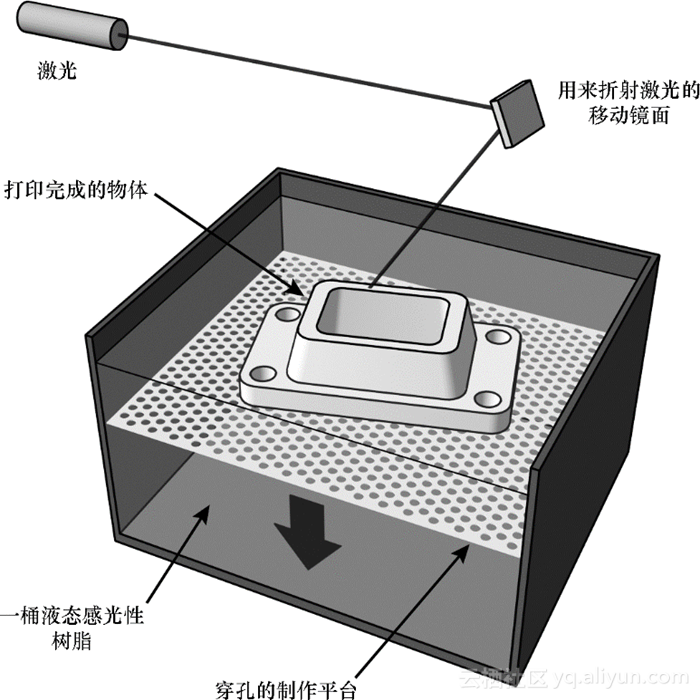
注意:
有些打印机的技术是反向的,激光束由透明感光性树脂桶底部开始固化物体层
和材料挤出工艺一样,使用光固化快速成型技术3D打印的物体通常也需要附加的结构来作为延伸和孤体的支撑点。打印完成后将这些支撑点分离或用工具去除。然后再使用溶剂对物体进行清理,最后用水冲洗,就可以得到一个完整清洁的物体。很多物体还需要在UV炉中进行调整。如果将在透明树脂中打印的物体暴露于阳光下,那么要对其喷漆以防止变色。有时物体还可以利用玻璃珠来改善表面质量,或者用喷气磨砂法来进行抛光。
与材料挤压技术不同,光固化快速成型技术是十分精确的,由它打印出来的物体表面都很光滑。目前最大的生产型光固化快速成型打印机是3D Systems公司的双激光3D打印机ProX 950,它的打印体积可达1500毫米×750毫米×550毫米(59英寸×29.5英寸×21.65英寸),最大打印重量为150公斤。该硬件X轴和Y轴的精度为0.025毫米,而其售价则为99万美元。
虽然在分辨率和表面质量方面,光固化快速成型是一项高品质的3D打印技术,但是其昂贵的价格把专业消费者和小型企业都拒之门外。然而,最近由于市场上出现了几款小型低成本的光固化快速成型3D打印机,这种状况正在逐步改变。2011年11月,Asiga公司推出了一款桌面光固化快速成型打印机,售价在7000美元以下。2013年5月,Formlabs推出了一款叫作Form1的桌面光固化快速成型打印机,售价为3299美元(2014年6月,Form1升级为Form1+)。
Form1+在制作平台底部固化物体层,制作平台先与感光性树脂浅池基接触。浅池基是一个涂有硅的光学透明盒,激光束投射在上面,从而固化物体层。当各层打印完成后,浅池基稍稍倾斜,随着制作平台的上升,在浅池回到水平位置之前将物体的底部与硅层分离。该动作为最后一个物体层重新涂上新的感光性树脂,如此反复。
Form1+的打印体积为125毫米×125毫米×165毫米(4.9英寸×4.9英寸×6.6英寸),可实现的最小层厚仅为0.025毫米。由于其反向的工艺,Form1+和相似的硬件可能需要在物体上添加坚硬的支撑结构,如果没有支撑结构,零部件会在打印过程中回落到感光性树脂桶中。
3D Systems同样不甘示弱,于2014年3月推出了一款名为ProJet 1200的“微型SLA”打印机。它的售价是4900美元,打印体积为43毫米×27毫米×150毫米(1.69英寸×1.06英寸×5.9英寸)。2014年5月,软件巨头Autodesk还宣布其打算推出一款基于新型“Spark”开源平台的桌面光固化快速成型打印机,预计售价约为5000美元。
当光固化快速成型技术最初被发明出来的时候,只能使用脆性树脂打印物体。因此,它通常用于制造生产模具,或者制作概念模型和展示模型。现在已经开发出了各种形式的感光树脂。包括橡胶状塑料、ABS和其他热塑性塑料的替代品、阻燃材料、纯树脂,以及专门用于牙科模型和珠宝设计的特殊感光树脂。所以,光固化快速成型技术还在继续生产模具和试制模型,同时也开始用于制造最终产品或零部件。但是感光树脂的价格仍然高于热塑性挤压材料。例如,Form1+消耗一升树脂的费用为149美元。
2.3.2 DLP投影技术
第二种桶式光聚作用3D打印方法是DLP投影技术。你或许对DLP(数字光处理)技术已经有所了解,许多电影院、阶梯教室、学校或家庭中使用的视频投影机内部都使用了这种技术。DLP投影机有一个微小的成像芯片,里面包含一组显微镜面或“数字微镜元件(DMD)”。这些镜面可以迅速旋转,将光线从投影机镜头、散热片或“光储”中反射出来。通过控制镜面排列方向可投影出高品质图像。
你可能会问,有了DLP投影机就可以3D打印了吗?答案是只有能够选择性固化液态感光性树脂的DLP投影机才可以。在一台类似结构的倒置的光固化快速成型打印机中,DLP投影机被置于一个装有液态感光性树脂的透明浅池基的上方,然后投影机在制作平台的底部固化物体的一整层。
与基于激光的光固化快速成型打印机类似,DLP投影3D打印机同样可以达到很高的精度。而且,小型打印机的精度要高于大型打印机,因为投影图像只需集中在较小的区域里。目前最大的DLP投影3D打印机能够打印的最小层厚约为0.025毫米,构建体积为267毫米×165毫米×203毫米(10.4英寸×6.5英寸×8英寸)。
多种感光树脂可用作DLP投影3D打印机的制作材料,包括传统塑料的透明或不透明的替代品,以及蜡基聚合物和一些牙科或医疗级塑料。事实上,EnvisionTEC公司的DLP投影3D打印机已经广泛用于3D打印助听器外罩及牙科专业领域。接下来的几章将详细介绍它的应用范围。
2013年12月,Prodways公司发明了一种名为Moving DLP的技术。这项技术与标准的DLP投影技术类似,但是通过一个移动的安装于顶部的投影机在液态感光性树脂池的表面投影物体层,进而达到更高的分辨率。Prodways公司称其为“MOVINGLight技术”,并且通过使用最新的UV LED作为DLP投影机的光源来提高打印速度。
2.3.3 扫描、旋转和选择性光固化技术
扫描、旋转和选择性光固化技术(3SP)由DLP先驱EnvisionTEC公司于2013年12月推出,这是一种新型桶式光聚作用工艺。在3SP打印机中,光通过一个旋转的桶反射,经过一系列光学元件将光束聚集到Y轴感光性树脂桶的表面。然后,UV光源和其成像组件根据需要在X轴上移动。3SP允许比DLP构建更大的尺寸,其中EnvisionTEC公司生产的Xede 3SP打印机的构建尺寸为457毫米×457毫米×457毫米(18英寸×18英寸×18英寸)。
2.3.4 基于光刻的陶瓷制造
第四种桶式光聚作用技术由奥地利的Lithoz公司开发,即独特的基于光刻的陶瓷制造(LCM)工艺。这是DLP的另一种有效形式,而不同之处在于它可以选择性固化包含陶瓷颗粒的感光性树脂。打印完成后需要进行相当广泛的后处理,以便去除感光性树脂,然后烧结其余的材料,进而形成紧凑的陶瓷部件。所有工序完成后,由LCM技术打印的物体将完全由陶瓷材料制成。
2.3.5 双光子聚合技术
最后一项桶式光聚作用3D打印技术是双光子聚合技术(2PP)。这是一种“纳米光学”3D打印法,类似于光固化快速成型技术,未来可能会成为主流3D打印形式。世界各地的几个研究小组正在开发2PP,包括维也纳技术大学由Jürgen Stampfl领导的增材制造技术(AMT)小组,以及德国卡尔斯鲁厄理工学院(KIT)的衍生企业Nanoscribe公司。
2PP通过使用“飞秒脉冲激光”选择性固化感光性树脂。这听起来似乎像光固化快速成型,但2PP 3D打印机能够实现的最小层厚和X-Y轴分辨率在100~200纳米之间。鉴于传统的光固化快速成型技术中X和Y轴的分辨率为0.025毫米,最小层厚为0.05毫米(Z轴),也就是说,2PP使所有轴的分辨率都达到了0.0001毫米。换句话说,目前2PP比传统光固化快速成型技术大约精准了250倍,打印出来的东西比细菌还要小。2PP也远远快于光固化快速成型技术,甚至能够每秒钟打印几米物体层。
未来2PP可以十分精准地打印很微小的东西,如微电子和光电子电路,还可以快速制造大型物体。特别是,2PP能够让未来的3D打印物体既轻巧又坚硬,因为它们的制造材料不是实心的,而是中空的纳米晶格材料。目前,纳米晶格结构只存在于自然界中,典型的例子包括人骨和木材。通过允许人为创建此种结构,2PP可能因此开拓出一个全新的制造领域。
为了开发2PP,维也纳科技大学众多学科的科学家们一直共同致力于提高感光性树脂性能和镜像技术。他们开发的感光性树脂含有特殊的“引发剂”分子,确保只有在同时吸收两个光子时才能固化周围的树脂单体。因为这只发生在激光束的正中心,所以使其成为一种极为精确的3D打印工艺,它允许在感光性树脂桶内的任意位置固化材料,而不仅仅在其表面上。
谈到移动的3D打印机激光束,这个来自维也纳的团队已经开发了一个非常高速的系统来保持镜子不停地运动。这减少了加速过程和减速过程时所丢失的时间,因此缩短了3D打印的过程。
为了证明他们的系统,维也纳的研究人员已经用2PP 3D打印机制造出了一台0.25毫米长的一级方程式赛车模型,耗时4分钟。他们还制造了维也纳圣史蒂芬大教堂模型,如图2.7所示,长度仅为0.1毫米。
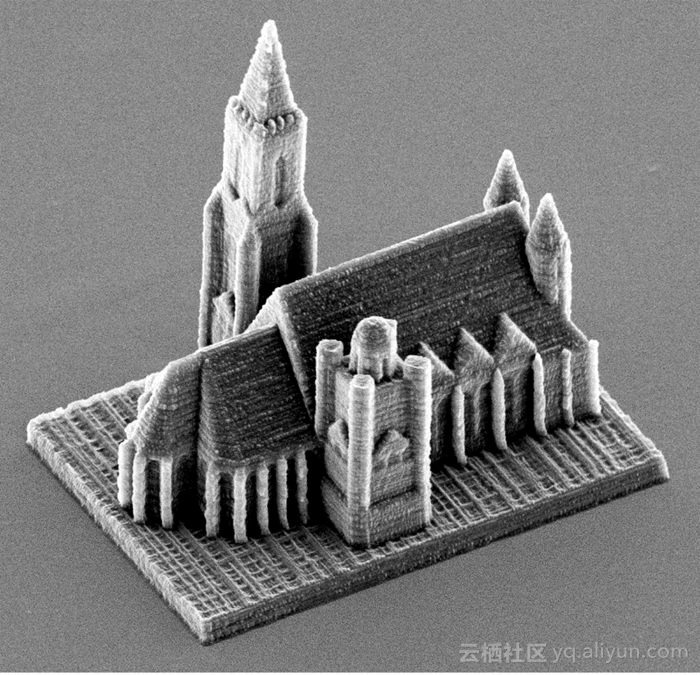
此打印模型为维也纳圣史蒂芬大教堂,由维也纳科技大学Jürgen Stampfl领导的AMT团队合作完成,长度为0.1毫米。图片转载已获得Robert Liska许可
在德国,Nanoscribe公司上市了一台名为Photonic Professional GT 2PP 3D打印机。这个屡获殊荣的硬件是当前市场上分辨率最高的商用3D打印机,目前正用于众多前沿研究领域。其中包括组织工程、新型电子设备的创建、生物黏合剂以及纳米微型机械。
2.3.6 材料喷射技术
回到我们的话题,另外一项基于固化液体的3D打印技术是“材料喷射”。这种技术有多种形式,大部分是将液态感光性树脂从多喷嘴的喷墨式打印头中喷射出。如图2.8所示,这种类型的3D打印机喷头在制作平台上移动以沉积一层液态感光性树脂。然后被从上述打印头中发出的UV光固化。3D打印机制造商Stratasys公司基于该技术所销售的硬件注册名称为PolyJet(“感光性树脂喷射”的简称),而3D Systems把此技术称为“MultiJet Printing”或“MJP”。
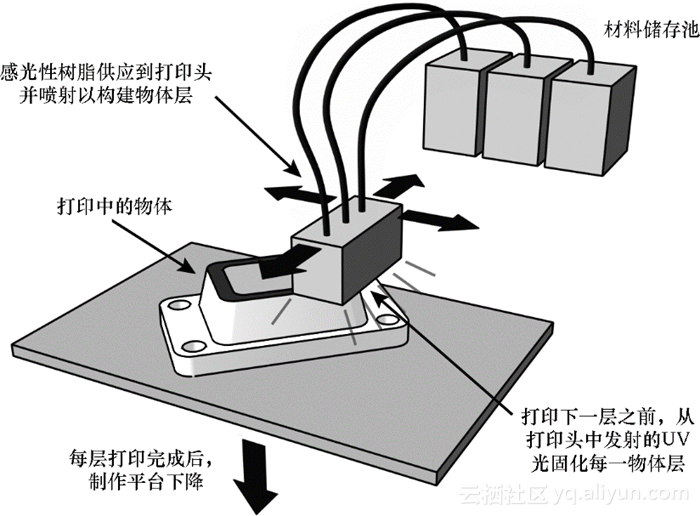
材料喷射打印机通常先使用凝胶状物质做成支撑结构,物体打印完成后再用手、刷子或喷水工具将其去除。当所有支撑结构被去除之后就不再需要进行后续处理了。这也使得材料喷射技术比传统的光固化快速成型技术操作起来更快捷方便。
许多坚硬的、柔软的、不透明的和透明的感光性树脂被广泛用于材料喷射技术。其中包括ABS、聚丙烯、聚碳酸酯和橡胶。许多材料喷射打印机在一个打印作业中还可以输出多种材料。这是通过向打印头中提供不同的感光性树脂基,并且在打印过程中将其混合为不同的组合来实现的。例如,Stratasys公司的Connex系列打印机能够创建一个由14种材料组成的物体。Objet500 Connex3 3D打印机甚至可以输出多种材料的彩色物体。本书编写时,材料喷射3D打印机能够构建的最大打印体积是1000毫米×800毫米×500毫米(39.3英寸×31.4英寸×19.6英寸),由Stratasys公司的Objet1000材料喷射3D打印机实现。
硬件除了可以喷射和固化液态感光性树脂,还有一些材料喷射打印机能够通过喷射热蜡滴构建铸模。例如,3D Systems有一系列ProJet 3D打印机使用其专业的VisiJet蜡和蜡质辅助材料,通过材料喷射技术构建“RealWax”物体。
Stratasys公司有一种基于“蜡沉积模型(WDM)”材料喷射工艺的材料喷射打印机,可用于为牙科和珠宝制造行业构建蜡模。它由SolidScape公司(现属于Stratasys公司)开发,并命名为“热敏按需喷墨法(DOD)”。与3D Systems的RealWax技术类似,它由特殊的蜡样塑料构建物体,与大多数材料喷射技术不同的是,该工艺的构建材料无需UV光固化。相反,“TrueWax”的固态热塑性塑料和辅助材料从打印头里输出之前需先在池中预热变成液态。喷射后,由于迅速冷却而自然变硬。
最后一种材料喷射3D打印技术是Printoptical。该技术由荷兰的LUXeXceL公司开发,用于制造原型或功能性光学部件。
Printoptical使用的是“One-Step-CAD-to-Optic”打印工艺,根据CAD设计的形状,用其3D打印机喷射透明感光性树脂的液滴。然后,LUXeXceL的软件在每个液滴喷射之前决定其是否应该由UV光立即固化,或者是否应该随其滴下以增强平滑度。随着这项技术的发明,LUXeXceL已经非常巧妙地开发出3D打印光滑镜头的能力,而无需任何抛光或其他后续处理。这意味着,LUXeXceL已经拥有一项可直接在打印床上使用的精准、高速且易扩展的工艺,实现3D打印坚硬体积的高质量镜头。
目前,LUXeXceL正专注于3D打印安装在LED照明系统中的照明用镜头,而不是用于成像的镜头。第4章将详细介绍LUXeXceL。
2.3.7 黏合剂喷射技术
介绍完固化液体的3D打印机,再来了解三组黏合粉末构建材料的技术。第一种是黏合剂喷射技术,如图2.9所示。制作过程开始时,把一层粉末置于制作平台上形成“粉末床”。这通常是通过提高相邻的“粉末池”和使用清扫刀片或滚压机来推动粉末到达粉末床。然后一个多喷嘴的喷墨式打印头穿过粉末床,选择性地喷出黏合剂溶液,以此来形成第一个物体层。接着粉末床稍稍下降,另一层粉末被推过来,黏合剂继续喷出,如此反复。
整个物体打印完成后,使用真空系统自动去除散粉并回收未使用的粉末,以便以后继续使用。然后手工取出打印物体,转移至“去粉室”中,使用压缩空气喷掉物体表面粉末,直到它完全干净。最新的黏合剂喷射3D打印机有内置的去粉室,还有能够回收多余粉末的闭环负压力真空系统,几乎不会浪费未使用的打印材料。
黏合剂喷射打印有时也被称为喷墨式粉末打印法或“Zprinting”。后一个名称源于该技术最初是由Z Corporation开发,并且销售了一系列“ZPrinter”型号打印机。然而,早在2012年,Z Corporation被3D Systems收购,同时ZPrinter的工艺被重新命名为ColorJet Printing。
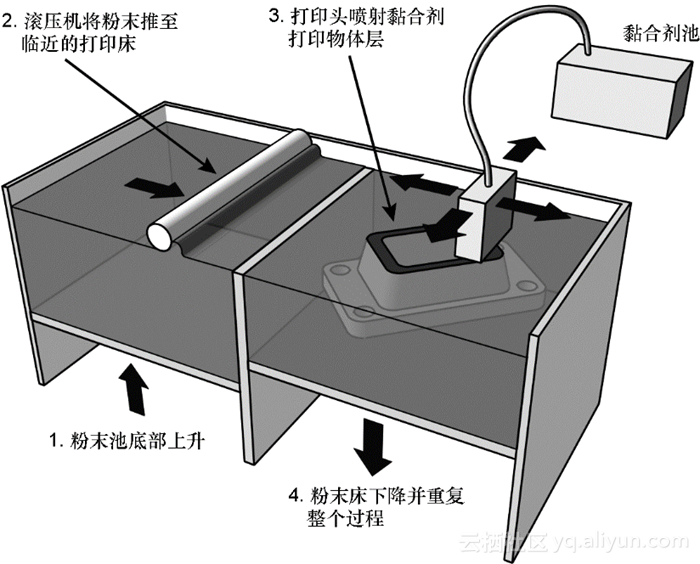
黏合剂喷射技术比其他3D打印技术具备许多优势。首先,对比大多数基于粉末的3D打印工艺,其打印过程无需制作和去除支撑结构,因为延伸和孤体部分可由周围的散粉支撑。其次,该技术能够比上述两项工艺更快速地构建物体。第三,该技术的制作成本低于其他3D打印技术。最后,黏合剂喷射3D打印机可以实现全彩打印。
黏合剂喷射3D打印机在粉末层上同时喷射黏合剂和彩色墨水就能够打印出彩色物体。这项技术和传统的2D照片打印机所使用的工艺是一样的,将绿色、红色、黄色和黑色墨水适当混合从而打印出全彩照片。3D Systems的黏合剂喷射打印机更有优势的一点是,它可以只喷入物体表面几毫米深处,从而节省墨水的消耗。
3D Systems销售的大部分黏合剂喷射3D打印机都通过一种名为VisiJet PXL的基于石膏的专有粉末材料制造物体。使用这种材料打印出来的物体,在从打印机中移出之前需要进行固化(大约一个小时)。即使在固化后,物体仍然相当易碎。虽然它们可能会被用来当做展示品(比如陈列模型),但大部分物体还需要一定形式的后续处理。即所谓的“浸渍”,这涉及到刷、喷或用其他化学涂层等操作,从而填补物体表面的微小气泡和坑洞。
使用VisiJet PXL材料打印的半成品可以用多种化学物质浸渍。有些物体用“盐水固化法”就能够处理完成。而有些需要重点处理的则可使用“ColorBond”加固胶水,如果物体需要强力浸渍,则需要高强度的“StrengthMax”加固胶水。处理后的物体会变得十分坚硬,甚至可以用作功能原型和最终生产零件。例如,黏合剂喷射结合StrengthMax浸渍已经成功制造出了扳手和机器人零件等物体。用黏合剂喷射3D打印机制作出的物体一旦经过适当的浸渍,可以满足打磨、钻孔、油漆和电镀等需求。
除了使用石膏粉末的硬件,3D Systems还销售全彩黏合剂喷射打印机—ProJet 4500,它使用的材料是VisiJet C4 Spectrum塑料粉末。该打印机于2013年12月推出,具有构建无需后续处理的半刚性塑料部件的能力。ProJet 4500的制作区域大小为203毫米×254毫米×203毫米(8英寸×10英寸×8英寸)。如图2.10所示,这是由ProJet 4500制作的3D打印样品。
虽然3D Systems是唯一一家能够用塑料粉末进行彩色打印的公司,但德国一家名为voxeljet(以小写v开头)的公司已经开发出使用喷射黏合剂工艺制作大型单色物体的硬件。这些硬件使用由丙烯酸树脂玻璃改良的PMMA粉末进行构建,打印完成后需要单色浸渍。PMMA还可以与蜡浸渍用于铸模。一些voxeljet打印机的打印体积十分庞大,其中voxeljet 4000可以打印4米×2米×1米(约13.1英尺×6.5英尺×3.3英尺)大小的物体。
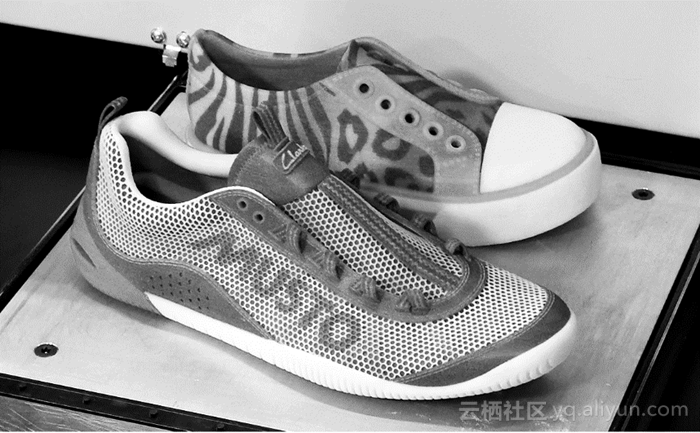
2.3.8 黏合剂喷射砂型铸造模具和模芯
除了使用石膏或塑料粉末构建物体,有些黏合剂喷射3D打印机(包括voxeljet 4000)还可以使用铸砂作为制作材料,从而实现模具和模芯的3D打印,这对于工业领域有着非常显著的影响。
几千年来,砂型铸造一直是生产铁、青铜、黄铜、铝和黄金等金属的常见制作工艺。该技术主要使用一种特殊的树脂浸渍砂,根据物体“模板”进行制造。这种模板一般是用木材等相对容易塑造成型的材料做成。
砂在模板中压实之后,就要将模板从组装的模具中拿掉,这个过程可能需要将模具拆分再重新组装。然后将熔融金属倒入模具形成模板的形状。最后,等金属凝固后,把砂型模具分离掉就得到了最终的物体。
黏合剂喷射砂型铸造模具3D打印机使用完全相同的工艺,如图2.9所示。唯一的区别是在较大的打印机中,特别设计的砂平铺在打印床上方的料斗中,而不是在上升的粉末池中推滚或扫过。打印完成后,周围松散的砂被回收,再用普通砂型铸造工艺往组合模具中填充金属。
3D打印砂型铸造模具工艺最大的优势在于它在打印前无需制造物理模板(这个过程需要时间和精巧的工艺技能,或者使用其他3D打印技术)。它还可以制造十分复杂和大型的模具,而且在浇铸之前不需要为了移除模板而打破模具。因此,这项技术的应用能够节省大量时间和金钱,同时制造出更多新颖的产品。虽然这样的打印机只是生产砂型铸造模具,而不能直接打印物体,但这仍然是一项非常重要的技术,它大大加快了这一最古老的制造工艺生产速度并降低了成本的。
2.3.9 黏合剂喷射金属打印
Z Corporation开发的黏合剂喷射3D打印机本来是利用石膏复合材料来打印高分辨率的陈列模型和原型的。但是一家创新公司ExOne打破了这一界限,开始开发以青铜、铁、注入青铜的不锈钢或镍合金Inconel 625为材料制造物体的硬件。和图2.9一样,平铺一层金属粉末,移动的打印头在适当的地方喷射黏合剂使金属颗粒黏合在一起。接着加热灯将该层干燥,之后再平铺一层新的粉末。如此反复直至打印完成。
打印完所有层后,装有易碎和多空物体的“粉盒”被送入175℃的固化炉中保持24小时,目的是蒸发水分并固化黏合剂。接着去除所有未使用的和松散的金属粉末,露出仍然未成型的物体,它大约包括60%的金属和40%的空气。
为了使物体更坚固,还需要注入更多的金属。方法是将它放在一个盒子里,里面装有金属粉末,四周用氧化铝粉固定。然后放到温度为2000℃的窑中继续烧制24小时。此温度能够将青铜粉末液化并浸润到物体中,使其成为金属含量99.9%的固体金属。
冷却之后将物体从窑中取出。之前帮助浸渍的所有支撑点或“熔渣”都要手工去除。大多数使用黏合剂喷射金属打印方法制造的物体都需要进行抛光。
正如你所看到的,黏合剂喷射金属打印或多或少都要涉及到烧制(幸亏很多物体可以在窑中同时进行打印、固化和浸润)。即便如此,目前该技术却是最廉价的3D金属打印形式,利用Inconel 625制作的零件甚至可以用来制造航空航天、涡轮机和其他高端工业部件。黏合剂喷射金属打印还有一系列表面抛光等工艺,包括镀金。因此,该技术在那些制作珠宝的艺术家中十分流行。ExOne的M Print机型目前能够实现的最大打印体积为800毫米×500毫米×400毫米(31.5英寸×19.68英寸×15.75英寸)。
2.3.10 黏合剂喷射陶瓷打印
陶瓷同样可以用于黏合剂喷射过程中。逐层平铺硅酸铝陶瓷粉末再喷射黏合剂。所有层都打印完成后,将物体置于烤箱中进行干燥并将多余粉末去除。然后再放到窑中烧制、预上釉、再烧制、上釉、最后再烧制一次。富有光泽的陶瓷成品具有高耐热性并达到了食品安全级别。
率先将这一技术推向市场的是ExOne。然而,2014年1月,3D Systems宣布新型3D打印机CeraJet将能够制造适合烧制和上釉的全彩陶瓷物体。正如来自3D Systems的Buddy Byrum所说,CeraJet“令数字化时代的陶瓷制作更加大众化,它是传统艺术向新时代科技转变的最好例证”。
虽然最终成品是光滑的,但以这种形式3D打印的物体各轴的分辨率被限制在2毫米,尤其是上釉的过程会影响细节。然而,对于生产花瓶、盘子、杯子、碗、蛋杯等餐具还是可以的。现在有些在线3D打印网站提供黏合剂喷射陶瓷打印服务,为那些想要拥有个人定制餐具的人们提供了方便。
2.3.11 黏合剂喷射玻璃打印
ExOne的黏合剂喷射硬件还可以制作玻璃物体,这是该技术的另一种变形。即平铺一层粉末状钠钙玻璃,它的细小颗粒与被喷出的黏合剂有选择性地黏合在一起。打印出来的物体在脱粉之前先在烤箱中进行固化。然后将其装入到盒子中,与添加的玻璃粉末一起在750℃的窑中烧制。窑中的物体被玻璃粉末浸润,将其表面空隙填满从而变得更加坚硬。
目前这种技术可使用的材料为白色或黑色玻璃,摸起来多孔、易碎且粗糙。该技术只能生产相对较小的物体(约75毫米×75毫米×75毫米,或3×3×3英寸),一般用于制造雕塑及其他装饰品。