
Cpk这个词儿,各位在制造业打拼的小伙伴们应该都耳熟能详了吧,Process capability index,意为过程能力指数,是在生产过程处于统计控制状态后,用来判定过程能力是否达到顾客要求的指标。简单说来过程能力指数越高,生产可能出现的不良率就越低。
Q:如何判断生产过程是否处于受控状态呢?
A:查看控制图和正态性分布。
通过控制图来确定组间数据的波动,通过正态性分布来确定组内数据的波动。从而确定生产是否处于受控状态。
下表展示了过程能力指数,西格玛水平和百万不良数之间的关系。
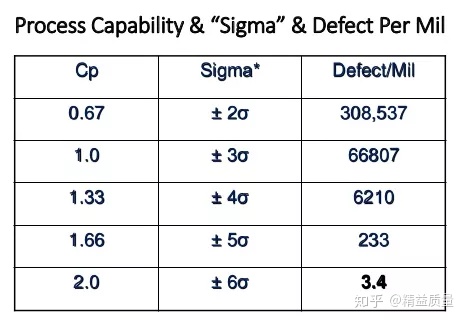
过程能力指数有两种,Cp和Cpk,这里“k”是日语“片寄り(katayori)”的首字母,意为偏倚。
同样的,过程绩效指数也有两种,Pp和Ppk。
Cp,Cpk反映的是短期内过程输出满足产品质量要求的程度,Pp,Ppk则是反映过程长期的总波动满足质量要求的程度。
Cp 潜在过程能力指数
Cp和Cpk都可以用来衡量过程能力,但是Cp由于不考虑中值偏倚,所以在Cp很好地情况下依然可能会出现大量不良,所以Cp又被称为潜在的过程能力指数,既中值不偏倚情况下能达到的最好的过程能力。
Cp的计算公式如下

可见,Cp的含义就是规格范围与6σ的比值,与分布在规格范围内的位置无关。
所以,如下图那样,即使Cp一样,但是由于分布的中心点位置的偏倚,导致良率是完全不同的。
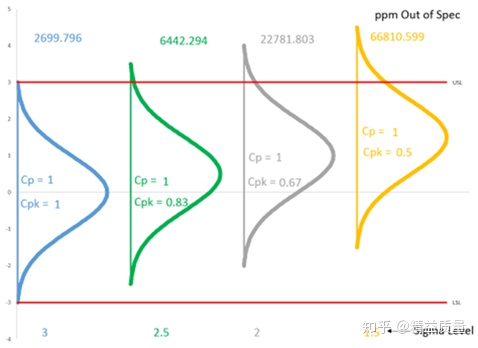
所以,为了反映实际的过程能力,既将过程能力与良率相关联,就引入了Cpk的概念。
Cpk 过程能力指数
Cpk的计算公式如下,分别计算分布中心到规格上下限与3σ的比值,得到Cpu和Cpl,Cpu和Cpl的最小值即为Cpk。
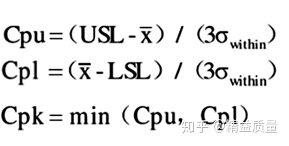
由于Cpk的计算考虑了中值偏倚的问题,所以现在都用Cpk来评价产线的过程能力指数。
下图是不同Cpk的分布曲线的图示,我们所追求的六西格玛水平的Cpk值为2,但是在实际生产中,从成本收益等综合因素考虑,Cpk大于1.33即可。
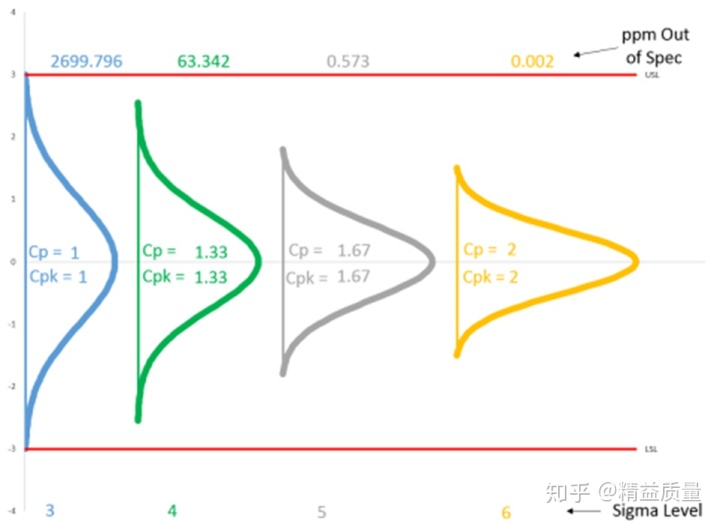
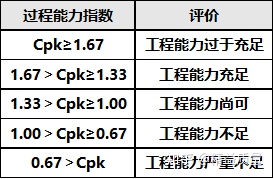
过程绩效指数 Pp和Ppk
我们用Cpk过程能力指数来评价短期的工程能力,那么长期的过程能力要怎么评价呢?如下图的例子,周一到周五,每天的工程能力Cpk都会略有不同,不同日期的分布曲线形状虽然相同,但是在中值得偏倚上却是不一样的,将一周的分布曲线叠加后,就会形成一个新的分布,这个分布所代表的的工程能力就是长期的工程能力,即过程绩效指数。
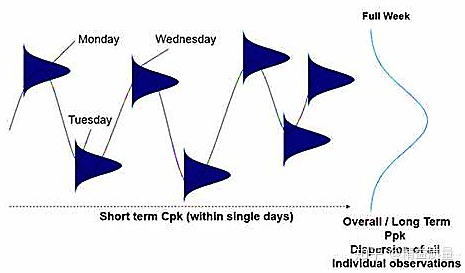
我们将不考虑中值偏倚的过程绩效指数Pp称为潜在过程绩效指数。
计算公式如下:

可见,与Cp的计算公式不同点就在于,Pp的σ值取的是全体样本的标准差。
与Cp和Cpk的关系一样,Ppk即为考虑了样本中值偏倚后的过程绩效指数。
计算公式也和Cpk一样,只是σ的取值不同。
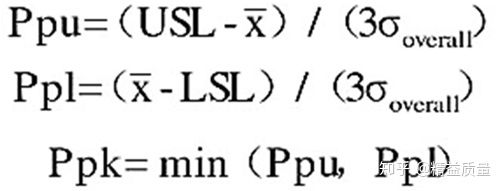
欢迎关注我的公众号:“精益质量”
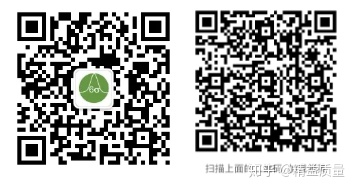