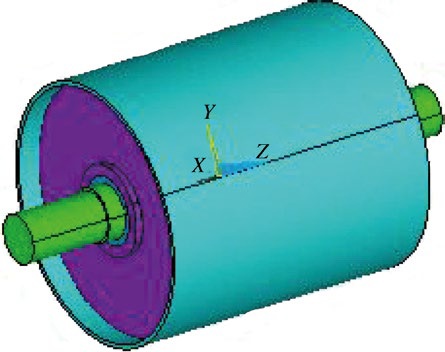
陈万宁 汤敏超 张亮有
作为带式输送机的主要部件之一,传动滚筒的设计往往使用经验公式法,采用较高的安全系数来保证滚筒的可靠性,这种方法的缺点是造成滚筒结构尺寸过大,质量增大,成本大大增加。本文利用Ansys 软件对滚筒装配体模型进行分析,找出应力应变分布规律,对应力应变云图进行分析,方便对滚筒进行优化。
1 滚筒装配体三维建模
传动滚筒由滚筒壳、辐板和轮毂、轴套、滚筒轴4部分构成,按照其承载能力分为轻型滚筒、中型滚筒、重型滚筒三类,按照滚筒表面构造又可分为光面滚筒和陶瓷滚筒等,根据功能又可分为传动滚筒、改向滚筒、增面滚筒和卸料滚筒。本文的滚筒类型为重型传动滚筒,辐板和轮毂铸焊成一体,滚筒轴和轮毂之间使用胀套连接,可以承受更大的载荷,而且拆装方便。
滚筒装配体建模的方式有两种,一种是在三维软件中创建好模型然后通过Ansys 和三维软件的接口导入Ansys 软件中;另一种是在Ansys 中直接建模。本文采用后一种建模方式,在Ansys 软件中自底向上分别对滚筒轴、胀套、辐板和轮毂、滚筒壳等进行建模,见图1。为了提高计算率和精度,在建立模型时进行了以下简化处理:
1)将胀套看成一个统一的实心体,不考虑内部结构;
2)各零部件的倒角、圆角等一些小特征忽略不计;
3)将轴承座对滚筒轴的约束简化为简支梁形式;
4)略去次要部件,如轴承座、胀套预紧使用的螺钉、螺孔等。
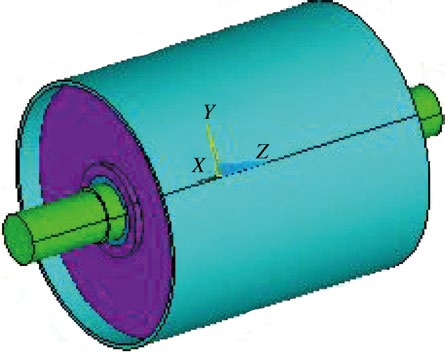
图1 传动滚筒三维模型
传动滚筒主要参数:滚筒直径D=1 250 mm,输送带宽B =1 800 mm, 滚筒长度L =2 000mm, 筒体厚度t =25 mm,轴长为3 000 mm,胀套处轴径为400mm,轴承处轴径为360 mm,胀套类型和尺寸为ZT9300×375,围包角为210°。
2 滚筒有限元模型和定义接触对
对滚筒实体模型进行网格划分,不同的零件赋予不同的单元类型和单元属性,同时对不同的零件进行不同的网格划分,本文中先使用Mesh 200 对轴的面进行智能网格划分,然后使用Solid 185 单元进行旋转,即可得到轴的网格划分。对其他部分均采用扫略网格划分,但网格划分的单元数目设置不同。由于轴是主要受力部件,所以网格的划分比较细。网格划分完后,对轴和胀套、胀套和轮毂建立接触对。轴和胀套、胀套和轮毂的分析属于非线性分析,本文将这部分考虑在内,以便得出更可靠的结果。滚筒的有限元模型见图2,滚筒轴和胀套建立的接触对见图3。胀套和轮毂的接触对有限元分析类似。
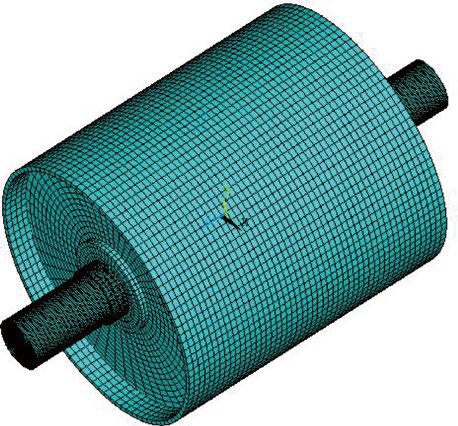
图2 传动滚筒有限元模型
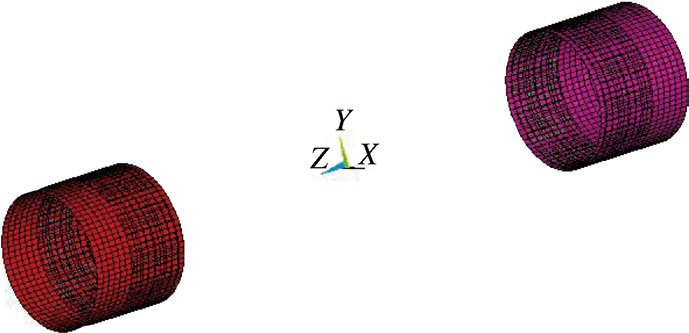
图3 滚筒轴和胀套建立的接触对
3 施加约束
在划分完网格后,对有限元模型施加载荷,必须先设置约束,有限元中的载荷包括边界约束、位移约束和力约束。一般将载荷分为6 类:自由度约束、力载荷、表面载荷、体积载荷、惯性力和耦合场载荷。本文在轴承处施加约束,限制轴的轴向(Z 轴)和径向(X 轴)的移动自由度,同时轴还受到联轴器的限制,要设置传动滚筒轴扭矩输入端绕轴线转动的自由度。
4 载荷的确定
驱动滚筒的受力分析见图4,驱动滚筒是传递动力的主要部件,为了传递必要的牵引力,输送带和滚筒之间必须有足够的摩擦力。根据欧拉公式S 入≤S 出eμα
式中:S 入为输送带绕入端张力,S 出为输送带绕出端张力,e 为自然对数的底数,μ 为输送带与滚筒间的摩擦因数。
在欧拉公式中S 入/S 出的比值要小于等于eμα。小于是指围包角没有被全部利用的情况,因此,要有围包角的利用弧α N。
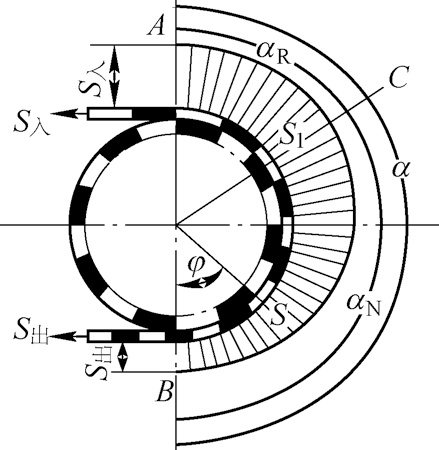
图4 驱动滚筒的受力分析
利用弧表示欧拉公式
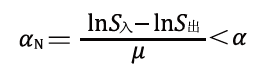
以极坐标表示的输送带沿弧的张力图解是按螺旋对数的,见如图5。对任意的φ <α N 一般表达式为
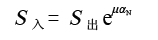
静止弧表示圆周力的一种储备,用来克服起动时出现的阻力和未估计到的阻力。所以也可以把它看做是一种安全系数。一般出现静止弧的情况是在输送机稳定时。如果S 入和S 出出现最大值,静止弧消失,则全部的围包角用于动力传递,此时S 入= S 出eμα。
根据摩擦驱动理论,滚筒的绕入端与绕出端遵循欧拉公式,滚筒的围包角为230°,静止弧为30°,利用弧为200°。在静止弧内,输送带与滚筒之间没有滑动,而存在着静摩擦。而利用弧的情况则完全不同,在该弧段滚筒受力由绕出端向绕入端符合欧拉公式并逐渐增大,即输送带张力在滚筒表面沿周向是变化的,符合欧拉公式。同时还受与滚筒表面相切的摩擦力,这部分用
表面单元来模拟。根据理论分析,在轴向滚筒表面的力不是恒定的,而是呈半正弦函数分布。为了简化计算,文中假定沿轴向滚筒受的力是恒定的, 这样做对结果影响不大。
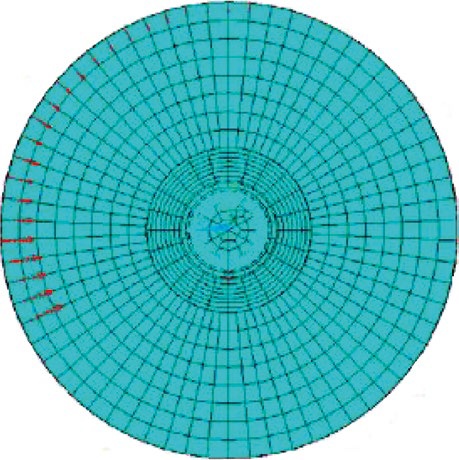
图5 施加载荷
5 求解及后处理分析传动滚筒的受力状况
做完前面一系列工作后,在Ansys 的求解和后处理模块对滚筒进行求解和后处理,得出筒壳的应力分布图和筒壳的变形图见图6、图7,理论上传动滚筒在受到输送带的作用力后,主要受力部分是轴和轴承、胀套和轮毂以及辐板与滚筒内壁的接触部分。Ansys 的求解,可以列出单元节点的应力分量、主应力、位移等,也可以用其他方式来显示位移和应力,这些能从整体上描述传动滚筒模型的分布状况,并确定哪个部分受力最大,哪个部分最危险。
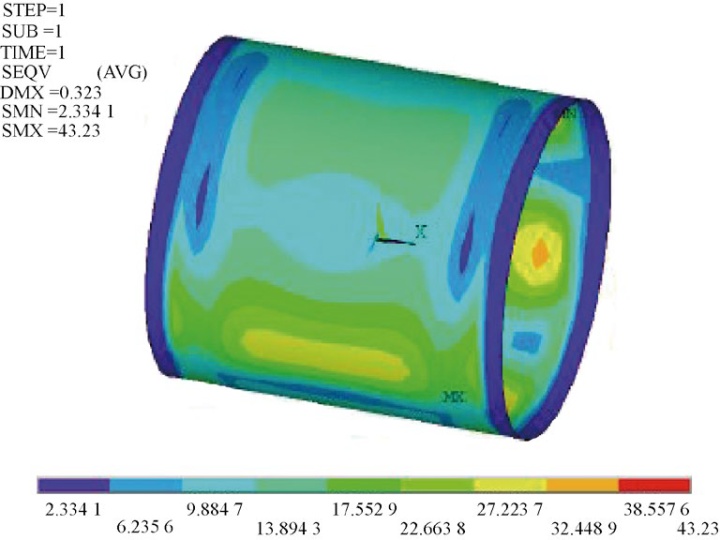
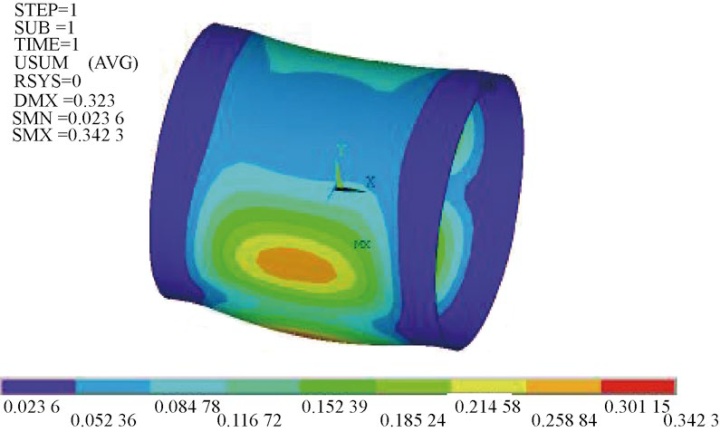
图7 应变云图
本文对重型传动滚筒的分析考虑了滚筒轴和胀套建立的非线性分析以及轮毂和胀套的非线性分析,通过对应力变形云图的分析,可以看出最大的位移坐标为(300.86,412.89,1 688.91),它出现在传动滚筒壳中间部位。最大值为0.342 3,从传动滚筒的应力分布图可以看出,滚筒的实际受力和理论分析的受力相差无几,即都出现在轴和轴承接触处,坐标为(136.08, 25.430,
880.72),最大应力为43.23 MPa。根据强度理论,轴采用45 号钢,调质处理后许用强度可达到65 MPa。传动滚筒符合强度要求,轴的许用强度远远大于轴的实际应力,故还有很大优化空间。
6 结论
1)利用Ansys 软件更好地判断传动滚筒的受力状况,从变形图和应力图中查看结果,更好地为优化提供依据。
2)分析了滚筒的变形图和应力分布图,得出滚筒的实际受力和变形情况,滚筒变形小,强度远小于轴的实际承受强度,可知还可以对滚筒的尺寸和质量进行优化。
3)本文在建模时进行了简化处理,实际的滚筒受力情况可能更加复杂,由于条件有限,未能对实际的滚筒进行建模分析。