前言
BMS设计是一个复杂的系统工程,能用一篇文章想讲透一个问题都很困难,想穷尽所有问题更是难上加难。本文仅从当前大家关注的几个核心问题入手,尽量深入的剖析其中的核心要素和设计思想,并会穿插一些设计案例。
本文的脉络是:安全、可靠的产品,准确的状态估算和故障预测,全寿命、全环境的适应能力。
BMS概述
电池管理系统(BMS)是可充电储能系统(RESS)的大脑,负责管理RESS系统的使用边界,保证电池工作在合理状态。
国内动力电池系统的BMS,大概是从2006年,北京公交采用大容量铅酸电池,改造部分“辫子车”开始的。当时的系统大概600V左右,BMS功能还仅限于一些物理量的测量,比如每个铅酸电池的电压,系统电流,绝缘情况,电量状态;硬件设计都是采用分立器件,大量采用模拟电路进行信号调理和隔离采集,成本高,设计难度大。
随着国家2009年《节能与新能源汽车示范推广财政补助资金管理暂行办法》发布,尤其2013年《关于继续开展新能源汽车推广应用工作的通知》政策的出台,BMS随着新能源汽车的崛起,飞速发展。
11年来,BMS系统在硬件设计上,得益于上游芯片厂商的不断努力,集成度越来越高,可靠性和安全等级越来越高,成本也越来越低。系统功能性能上,大家的关注点也从BMS系统的采集精度,逐步转移到BMS和电池的匹配,以及各种控制策略的设计上。而且随着动力电池系统的使用,大量的数据积累,让工程师能够窥探电池系统在全寿命周期和全天候条件下的表现,进而通过BMS的设计,不断优化系统。
安全设计
首先电池本身的特性决定了,它有很多失效模式。过充电,过放电,温度过高等,严重的会导致起火、爆炸、有毒气体泄漏等安全事故。BMS首先要做的是安全管理。
怎样的设计才是安全的设计呢?类似火车路口,通过火车轨道这个功能,图1的设计就是功能安全的,图2的设计就是功能不安全的。
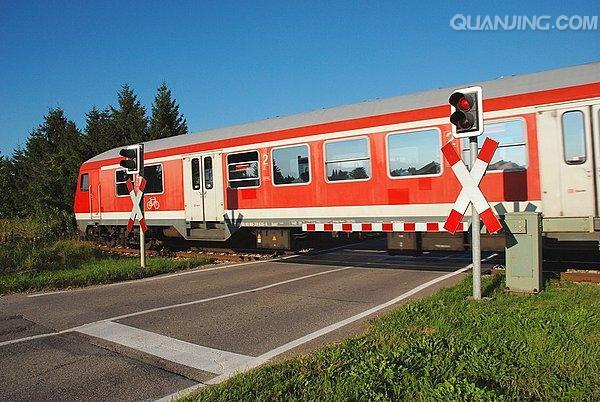
Table 1功能安全
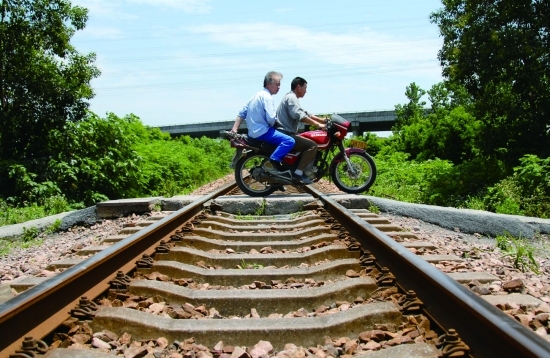
Table 2 无功能安全
具体到BMS系统的设计,在汽车行业有标准的设计指导文件ISO26262,美国和欧盟已将ISO26262作为传统汽车和新能源车辆安全事故召回的依据。
这里不画V流程,不讲功能安全概念,这些教科书上都有。我们想强调得是安全是系统性工程,不仅仅是流程安全,更要有扎实的软硬件设计功底和对电池的深入理解,不仅是BMS功能安全,更是电池系统以及整车的功能安全。
那怎么设计呢?例如针对单体电池的充电功能,我们设计了8个维度的防护措施:包括多重的硬件冗余和软件算法冗余设计。硬件主要从不同的维度,包括电压,温度、电流以及时间上,通过电池模型进行相互校核,保证电池信息采集的完整性,软件上通过不同的算法,如离散度以及极差等进行对比,最后基于所有信息进行安全状态判断,进而控制电池的充电过程。
Table 3单体充电功能,8重安全防护设计
可靠性设计
汽车零部件有着苛刻的可靠性要求。可靠性不仅靠研发保证,更要靠从研发到生产的全流程保证。这里的核心问题是可靠度价值和可靠性模型。需要工程师平衡和把握。
可靠度价值=研发成果*成果价值/研发时间*研发成本
可靠性模型:
Table 4可靠性模型
简单来说就是设计边界怎么确定,怎么进行开发,怎么进行验证。这里的核心理论是阿氏模型,这是加速实验的理论基础
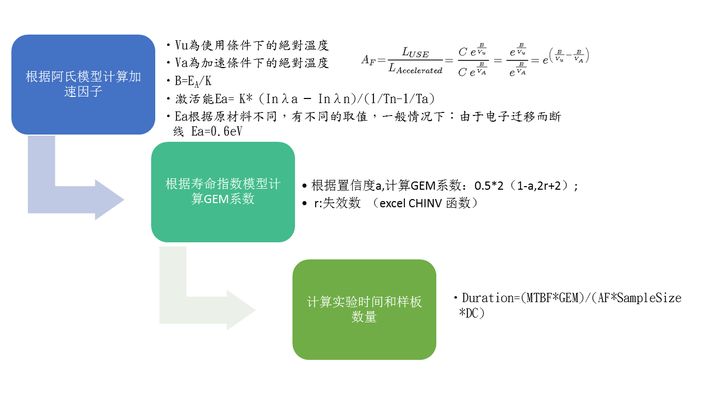
Table 5加速实验理论
AF:为加速试验的加速系数。K:玻尔兹曼常数电子元器件的失效原因与器件本身所选用的材料、材料之间、器件表面或体内、金属化系统以及封装结构中存在的各种化学、物理的应有关。器件从出厂经过贮 存、运输、使用到失效的寿命周期,无时无刻不在进行着缓慢的化学物理变化。在各种外界环境下,器件还会承受了各种热、电、机械应力,会使原来的化学物理反 应加速,而其中温度应力对失效最为敏感。实践证明,当温度升高以后,器件劣化的物理化学反应加快,失效过程加速,而Arrhenius模型就总结了由温度 应力决定的化学反应速度依赖关系的规律性,为加速寿命试验提供了理论依据
BMS系统有上百种物料,这里拿BMS系统里面的一个HCU子系统中,一个最最小的被动器件,电容的选型,来讲讲BMS的可靠性设计,这里也仅从机械应力失效角度做分析。