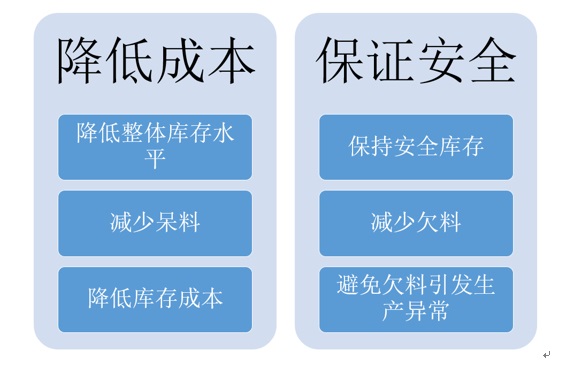
制造企业的物料问题:
料况是困扰企业生产的关键因素之一,有些物料的采购提前期很长。供应商的物料供应常常不能满足生产需求。生产一个产品如果需要100种物料, 只要欠一种就不能生产,其它99种料都占用库存和资金。所以,产品订单的物料不能在相近时间齐料,就会导致一方面仓库爆满,大量占用资金,另一方面,又因欠料不能按时生产和交货,引发客户不满
欠料问题也造成产线生产效率降低。急单因欠料不能生产,只好先做不急的单。材料一到,需要紧急切换,造成产线工时浪费,WIP延长。
如果企业为了避免欠料的发生,维持过高的库存水平,材料提前很久就买回来,一方面占用库存资金,增加仓库成本。另一方面,因客户订单在不断变化,过早采购有可能造成呆料,不得不报废,也造成资金损失。
不只采购的物料有库存问题,公司内部制造的半品也有库存问题。库存过高,可能会造成呆料。不生产库存,紧急订单无法满足。很多公司半品管理混乱,车间内半品到处堆放, 没有账目,无人管理,员工凭经验取用,年底盘点不得不大量报废。在制造业微利时代,这种浪费应该避免。企业利润不只来源于销售,减少浪费也是重要的一环。
APS生产排程系统帮助企业优化库存管理:
库存优化需要从两个方面入手:
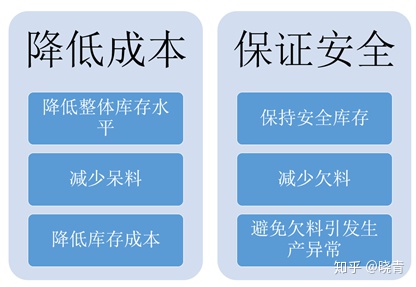
怎样才能同时满足以上两个方面,维持一个合理库存水平?答案是准时生产、准时采购
怎样才能做到准时生产,准时采购?
准确的长期生产计划优化采购物料库存管理水平
最关键的因素是长期生产计划的准确性。我们以按订单生产的企业为例。目前普遍采用的物料采购策略是MRP,即按客户订单和生产计划的需求,考虑物料的采购提前期,下达采购订单,让物料在需要的时间交货。
因为有些物料的采购提前期长达数月,供应商接单后再安排生产。在没有APS辅助的情况下,企业无法排出准确的长期生产计划,ERP只是根据订单交期产生物料采购订单。而ERP在确定订单交期时,并没有按照设备产能进行详细规划,而是假设产能无限,这样必然导致计划时间不准确。
只有计划准确,才能产生准确的采购计划,降低无效库存,减少欠料,从而提升准时交货率。而要制定准确的长期生产计划,需要APS高级计划排程系统的支持,靠人工是无法达到的。
PlanMateAPS中的长期排程,可以进行未来1-6个月的生产排程。
从理论上,短期排程与长期计划并无根本差异。长期排程主要的困难在于优化时间,PlanMate长期排程使用一种快速简化算法,排程结果与完全优化算法,在订单生产时间上基本一致,只有设备选择有差异。
PlanMateAPS自动排产系统优化零部件库存管理
原则上,零部件的生产应该遵照成品组装计划安排。但是实际上,因为零部件的生产会提前于总装,经常有不能配套的情况发生。造成零部件库存过高或呆料的原因很多,主要包括几条:
1. 总装因欠料发生计划变更。本来安排要装配的产品,因欠料临时延期,但是该订单的半品已经生产了。后面的工单被提前,但是半品的生产没有完成,又不能进行组装。多次修改计划,造成混乱。
解决方案:PlanMateAPS中的按库存约束排程可以完全避免这种情况发生。组装工序的生产计划依据在库与在途库存约束制定,所有订单均排在齐料时间之后,因此不会发生因欠料临时延后的问题。半品的库存和未来几天的产出计划也作为总装排程中的约束条件,协同排程,避免了计划的频繁修改。
2. 前后工序缓冲时间过长,工单整体生产周期太长,应对变化的能力变弱
a) 零部件生产提前时间越长,组装段计划发生变化的可能越大
b) 工序之间延迟时间与在制品数量是成正比的。 半品大量堆积在车间内,易造成混乱也容易发生损坏
解决方案:导入自动排程系统,首要的变化就是工序之间的缓冲时间大大缩短。在人工排程方式下,因为计划修改困难,计划员通过延长工序间缓冲时间的方式简化计算,一般都至少维持一个班次(12小时)的延迟。在导入PlanMateAPS后,工序之间的延迟时间缩短到2-4小时,生产周期整体缩短。使用APS排程后,半品生产一个工序完成后很快就转移到下一个工序,停留在车间产线边的数量和时间大大减少。同时,半品生产与成品组装之间的时间间隔也很短,成品订单变更的概率大大降低。
3. 半品车间生产多余的库存
用量大的零部件会生产安全库存。但是,安全库存的生产应该严格管理,不能凭借员工个人经验。安全库存应考虑零部件平均消耗速度、未来订单等多种因素,经过严格计算后,正式生成库存生产计划,不能凭经验决定。PlanMateAPS的需求管理模块,对安全库存订单的管理提供了解决方案。具体可参考网站另一篇文章:安全库存管理。