旋流分离器机械密封的改进
1. 概述
旋流分离器是近年来用于油田污水处理和污泥分离的主要设备,是当前污水处理效率较高的液-液、固-液反应分离设备。由桶体、导流罩、螺旋式搅拌、机械密封、电动机组成(如图-1示)。是当前污水处理工艺中用于污水反应和分离的高效反应分离器,广泛应用于油田开发行业。当电动机以1470rpm的速度旋转时,在螺旋搅拌叶轮的作用下,叶轮的上部和下部分别产生强大的吸力和推力。把容器中间的物料迅速地吸入器底的底部,在推力的作用下通过器底反射罩的回旋转向作用,迫使物料在分离器的空间向上翻动,通过高速循环,使药剂和污水获得充分的反应与混合。
釜内的操作工况:最高工作压力0~0.8MPa,最高温度100℃。
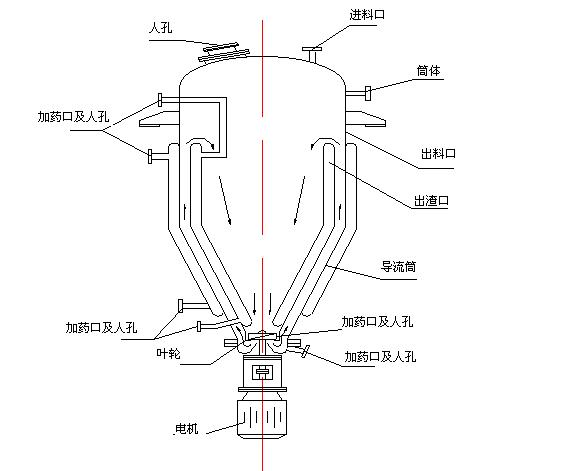
图—1旋流分离器结构图 1.进料口 2.筒体 3.出料口 4.出渣口 5.导流筒 6.电机 7.加药口及人孔
2.现状分析
该旋流分离器自2012年投运以来,原设计的机械密封频繁损坏,导致密封失效,对生产带来严重的影响。并且由于电动机和搅拌器设置在分离器的底部,结构特殊,机械密封的检修更换工作难度大,装配精度难以保证。为此,我们对密封失效的原因进行了分析:
a.分离器内压力波动范围大,而封油压力恒定(或不足、或太高),无法适应变化;
b.密封比压不够;
c.搅拌器的轴向冲击力较大,造成石墨环易损坏;
d.封油过滤精度不够,杂质易进入密封腔;
e.装配精度不够;
3.关于机械密封的计算
由于药剂和和污水在分离器内是一个逐渐升温升压最终又冷却转输的过程,操作工况随时在变化,因此对机械密封的可靠性提出了近乎苛刻的要求,该机械密封原设计选型为103DgMK3-60型,内装式单端面单弹簧非平衡型机械密封,其摩擦副动环材质为硬质合金,静环的材质为石墨,O型圈材质为氟橡胶。
密封的端面比压(Pc)的计算如下:
3.1弹簧刚度:
K1=GD4/8nd3=2.94N/m2
式中:G——弹簧弹性模量,G=78400N/m2;
D——弹簧丝径,D=1mm;
n——静环支撑弹簧有效圈数,n=14;
d——弹簧直径,d=6.2mm
3.2弹簧工作负荷:
F=n1K1f1=70.56N
式中:n1——静环支撑弹簧个数,n1=6;
f1——压缩量,f1=4mm;
3.3弹簧比压:
p1=F/A=0.05MPa
式中:A——静环端面面积,A=17.427cm2;
3.4载荷系数:
K=(d22-d02)(d22- d12)=0.81
式中:d2——静环端面外径,d2=116mm;
d0——静环座内径,d0=108mm;
d1——静环端面内径,d1=106mm;
3.5端面比压:
pc=p1+p(K-λ)=0.51MPa
式中:p——压力,p=1MPa;
λ——液膜反压系数,查《机械密封手册》,密封面介质若为柴油,λ=0.34
为解决机械密封润滑,冷却,冲洗,增压的问题,原设计制造了封套由系统与密封腔相连,流程如图--2示。封油装置供油压力(即密封腔内封油)的压力比分离器内压力高0.05~0.1MPa。
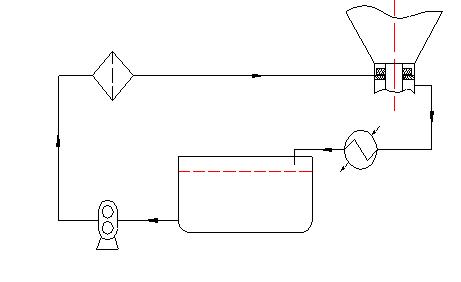
图—2泵机械密封系统油循环管路图
1.齿轮泵 2.过滤器 3.机油箱 4.冷却器 5.筒底机械密封
4.改进方式:
1. 增设差压变送器,安装自动调节阀,根据分离器内压力变化调整封油压力,使封油压力始终高于分离器内压力0.05~0.1MPa;(改进后的封油系统流程如图-3示)
2. 增加密封比压;
3. 改变摩擦副材质,静环由石墨改为硬质合金;
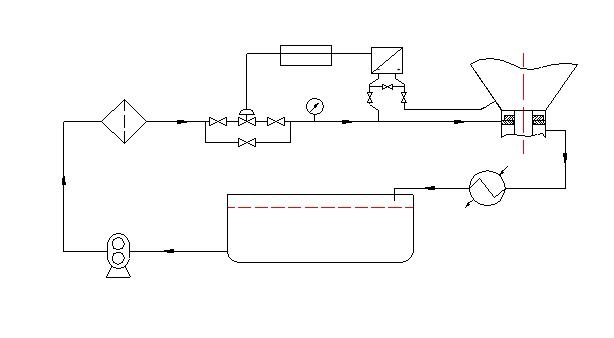
图—3改进后的机械密封油循环管路图
1.齿轮泵 2.过滤器 3.调节阀 4.差压变送器 5.筒底机械密封 6.冷却器
4. 增加过滤设施,净化封油系统;
5. 提高密封和搅拌装置的装配精度;
5.结论
通过上述改进,污水处理装置旋流分离器运行状况良好,机械密封一直处于稳定状态,使用周期由以前的20天左右提高到连续使用一年以上,为油田注上水、注够水、注好水提供了良好的保障。