一、定义价值流图析(VSM)

1.VSM的定义
VSM(Value Stream Mapping)是使产品或者服务通过物料流和信息流所需的所有创造价值和不创造价值行动的快照,用图示方法进行描述表达。
2.VSM的组成部分
现状价值流图、现状价值流图标记、未来价值流图、价值流计划。
3.重要特征
- VSM是一种使用常用制图语言的形象展示;
- VSM提供识别改进机会的基础和方向;
- 力量存在与该计划中。
4.价值流图和过程图的不同之处
- 价值流图:是端对端业务的概要快照、用来识别哪里存在改进的机会、没有结合决策环路;
- 过程图:对制造或者业务过程的详细图解、用来识别具体的改进、将决策环路结合在过程中。
5.VSM的目的
清楚识别关键的端对端制造和业务过程中的浪费,并创建可执行的改造计划。
6.VSM的优点
- 关注有限的资源;
- 确定预期绩效改善的时间线;
- 避免在浪费的大海中出现成功的孤岛;
- 使每个人都能对目前状态和未来远景有共同的了解。
7.什么时候使用VSM
- 指出开始精益之旅的方向;
- 执行由战略开发和关键业务必做事宜驱动的改进;
- 获得端对端过程真正的跨职能理解。
8.价值流图析和战略的联系(图形表述)
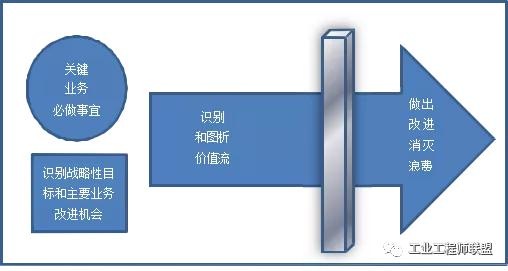
二、价值流图析过程

1.VSM规划步骤
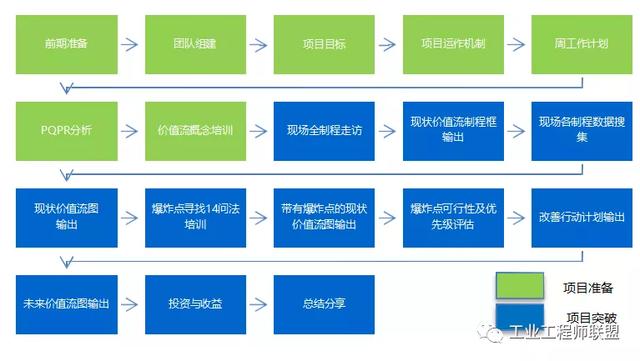
2.选择产品族和服务族
1)定义“价值流”:必须有所有的这些行动使产品或服务通过主要流程,从起始点到被顾客接收,该流程对于提供产品和服务来说必不可少。
2)识别价值流中的“价值对象”:
A、单一实体或者信息对象,经过从起始点到顾客接收的价值流中所有的过程步骤;
B、用来按图析沿价值流移动,并计算各生产过程的库存水平;
C、用来展示其通过生产过程向顾客移动时如何创造价值流。
3)确定和选择产品族
A、产品族:下游生产过程有相似加工步骤、使用共同设备的一组产品;
B、产品族矩阵:一种数据分析工具,根据同样的生产过程和总需求百分比确定并将产品分入产品组;
C、记录信息:产品族名称和描述、列出产品族中的 SKU和描述、生产每周产品所需的过程次序、对每周产品的需求数量和频次;
4)计算价值流的总需求
产品组中所有产品的合计需求将被用来计算价值流的节拍时间;
3.识别出“客户是谁”
客户:其他使用产品的人(用户或者经销商)、下一工序、公司、老板。
4.创建目前状态图的方法
- 小组沿过程逆向走,从客户端往前追溯;
- 我们从客户的视角来看这个过程;
- 从尾走到头使小组能看到浪费。
5.图析目前状态的步骤
1)图析顾客数据(每日需求=月度需求/上班天数);
2)计算节拍时间(T/T=可用工作时间/顾客需求);
3)图析过程步骤和库存水平(a、过程框被描述成流动停止或者库存有机会积累的地方; b、DOI:单件产品或者服务在一个过程结束是制成的频率,DOI 比节拍时间短);
4)图析供应商数据(采购材料供应商名称、订单发送频次、送货方式);
5)计算和图析加工时间和生产交付时间(a、加工时间:(DOI=OCT+MCT)图中反映的就是单个操作工加工“价值对象”所需时间;b、每个过程交付时间=库存/每天需求量;c、总时间= 每个过程的加工时间+交付时间);
6)图析信息流。
6.询问现状价值流图的问题(14问)
1)你们的产品是进入成品仓还是发运出去?(订单拉动还是市场拉动)
2)你会在哪个店(定拍过程)是确定生产进度?(确定 N 点)
3)目前的过程符合节拍时间吗?(T/T 与DOI、C/T 比较)
4)哪些过程可以采用连续流结合在一起?(寻找连续流机会)
5)哪种连续流模式?(单件流、小批量流、批量流)
6)在哪啦拉动体系可以结合不能流动的过程?(设计拉动)
7)拉动模式是什么?(按任务拉动还是超市)
8)拉动看板如何投递、管理?(看板设计)
9)其他信息流如何设计?(看板设计)
10)库存模式如何设计?库存标准如何设定?(库存设计)
11)在哪里需要考虑切换时间?(畅流相关)
12)在哪里需要考虑机器连续工作时间的改进?(畅流相关)
13)哪些过程需要改进质量?(一次通过率)
14)除了主要痛点,还有哪些过程可以改进?(畅流相关)
7.绘制未来价值流图的步骤
1)从有标记的现状价值流图开始;
2)绘制图中相同的部分;
3)将流动的过程合并;
4)加入超市和kanban看板;
5)加入另外的信息流;
6)计算交付时间和加工时间;
7)识别图上的环路。
8.环路的定义
- “环路”是为实现未来状态而需要对目前状态所做改进的逻辑分组;
- “环路”杯用来将价值流计划中的重点改进活动围绕未来状态中的某个具体新功能联系起来;
- “环路”杯用来将价值流机会中的改进活动按逻辑排序,这样通过逐步分解贯彻以实现未来状态,而不是“一蹴而就”;
- 价值流图中的四个“环路”:定拍环路、信息环路、供应商环路、制造环路。
价值流图范例:
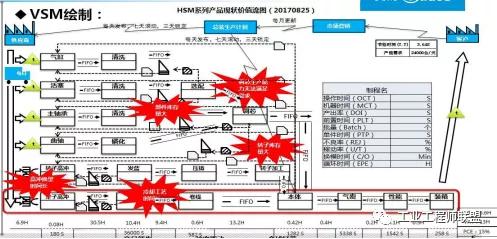
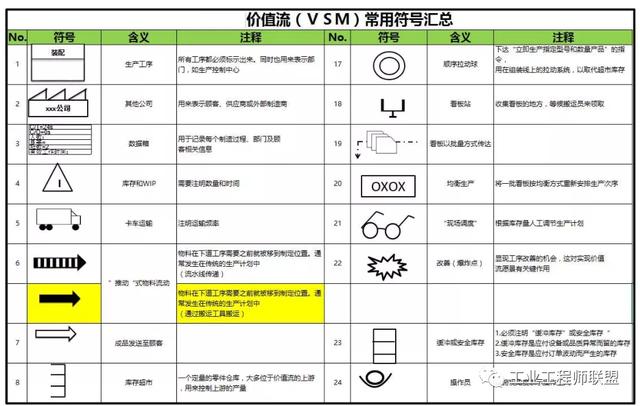
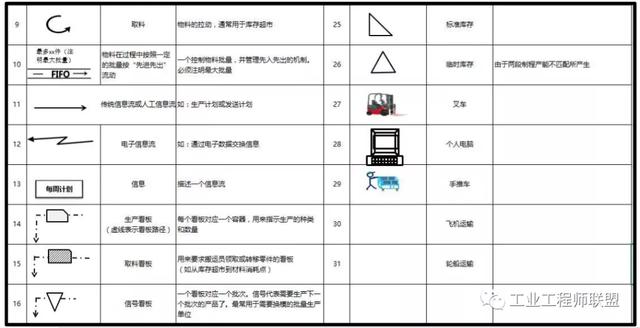
三、确定价值流计划

1.确定价值流计划的目的
通过确定优先顺序、清楚识别行动、详细制定严格的时间线、清楚识别所有权,来创建计划实现未来状态。
2.价值流计划的时间安排
- 时间安排必须与预先确定的未来状态的贯彻一致;
- 识别执行计划时间安排所需的行动;
- 确保团队完全有能力实现未来目标;
- 创立回顾步调,定期更新价值流计划目标的状态。
3.价值流计划的跟进和监控
- 监控共进度对成功与否至关重要;
- 没有跟进就不能完成;
- 与价值流所有人进行每周状态回顾;
- 价值流经理应每两周回顾进度一次;
- 回顾在现场进行,重点放在未完成的项目上;
- 应与业务单位所有人每月回顾进度一次。
四、PSI规划

1.PSI体系定义
PSI是大数据分析,是产销协同预估结构的体现,改善价值链的计划,控制库存,有效平衡需求与供应。
2.PSI的功能
1)动态平衡:削峰填谷,通过库存进行动态平衡,规划生产实现平缓“爬坡”和“下坡”,避免人员大进大出(成品、半成品、材料同理,部件库存储备影响拉动规则);
2)资源匹配,决定型谱:分产品、分规格到关键部件逐层检讨月度最大需求与资源的匹配度。
3.资源缺口补充
按缺口量检讨形成产线兼容技改计划或者瓶颈资源扩能计划(型谱变更影响拉动规则),总装—部装产线型谱同步调整,尽可能保证对应关系变量最少。
附图 1:PSI体系流程图
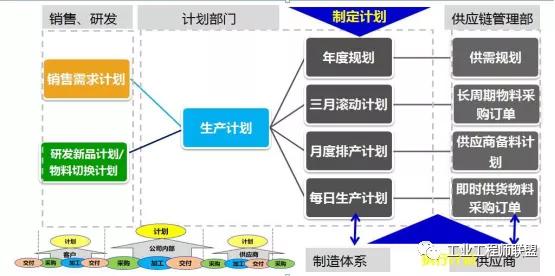
附图 2:PSI动态平衡表
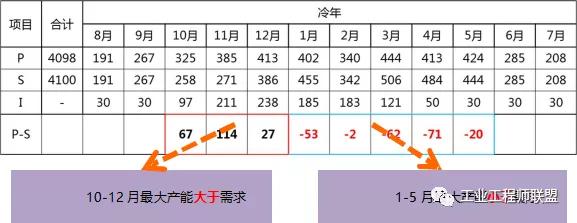
附图 3:生产节奏曲线
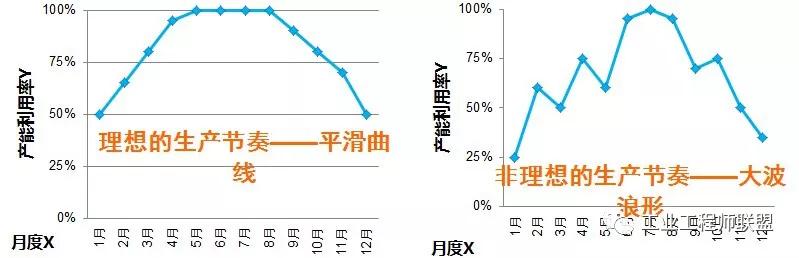
附表 4:月度资源检讨
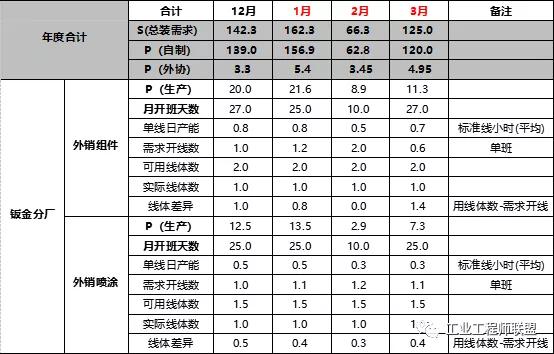
五、拉动的步骤

1.拉动五步法
型谱匹配、计划模式、看板设计、库存设计、目视化管理。
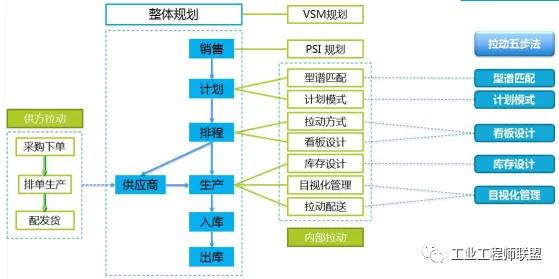
2.型谱匹配
1)几个重要名称概念
A、连续流:能做到前后段生产任务一致的即称之为连续流;
B、连续流包括三种:单件流、小批量流(按容器流动)、批量流(按任务批次流动);
C、物流断点:连续流前后工段无连接的地方;
D、断点:非连续流前后工段无连接的地方;
E、基准节拍点(N):最后一个连续流的起点。
2)型谱匹配的作用和目的:
建立“产品与产线匹配+总装产线与部装产线匹配”规则,匹配让计划更简单,为拉动实施奠定基础。
3)“产品与产线匹配”模型
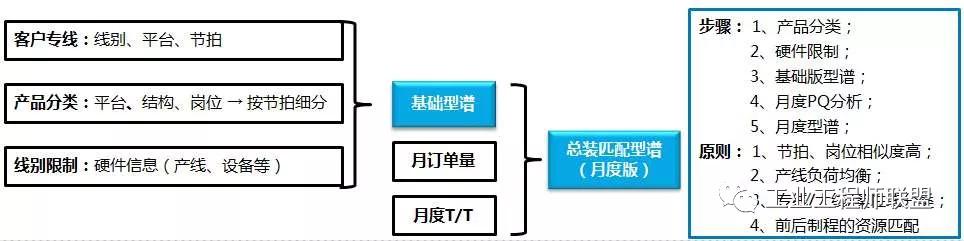
4)“总装与部装产线匹配”模型(规划连续流)
A、基本形式:一对一、一对多、多对一、多对多(基于客观条件及成本考虑,可能同时存在多种形式);
B、改善方向:由“多对多”向其他简单匹配方式转化。
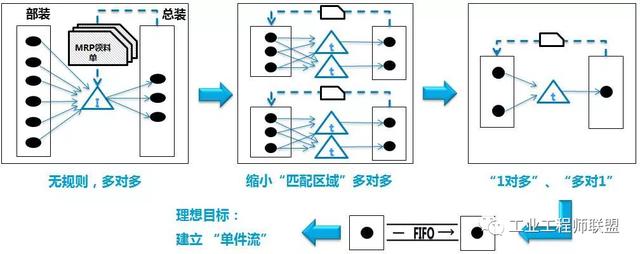
5)“产品与产线、总装与部长产线匹配”案例
把排产要考虑的关键因素列为制造附件属性,成为线内优化排产的逻辑; 型谱是订单自动分线的指路人,部装瓶颈是总装计划自动的粘合剂。
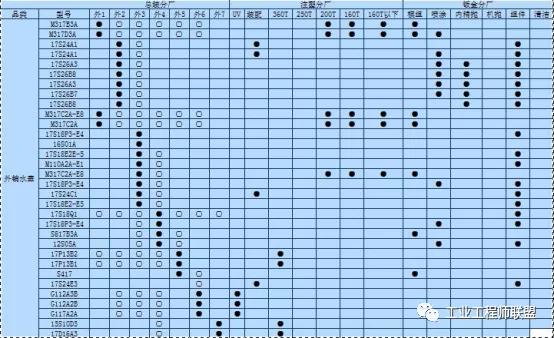
6)“总装与部装产线”联动排产模型
总装与部装计划“线对线”,总装计划顺序、数量变动,部装计划跟随变动,计划员很轻松, 让部装与总装直接点对点对接,协调效率提高。
7)注意事项
A、不能连续流的常见工序(改变了生产顺序),要建立集约规则
- 必须集约的工序,例如喷粉、搪瓷、热处理、浸漆
- 换模影响大的工序,例如高冲、注塑
B、尽量连续流,但不要免去变成连续流,需要考虑成本;
C、没有连续流动时,工程之间会变成每一个小孤岛,连续流动之后,几个工程变成大岛;
3.计划模式
1)推式生产与拉动生产的概念
推式生产:在每个制程断点下达生产指令,前工序生产不受后工序影响;
拉式生产:只在基准节拍点(N 点)下达生产指令,前工序由 N 点抛出看板,只能生产后工序需要的东西。
2)拉动生产的三种计划模式
A、跟随模式:适用于连续流生产线,自制件与总装生产任务顺序一致,与总装上线时间提前期为固定值,前工序为 1对 1匹配后工序,或者前工序为混流,且产能大于后工序。
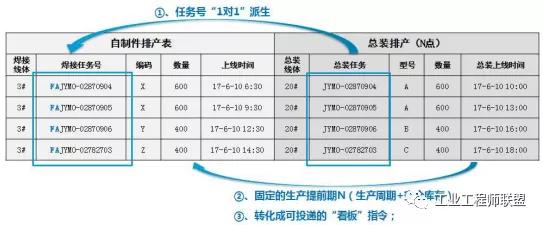
B、跟单模式:适用于非连续流生产线,是否集约取决于工艺条件或换模时长,总装与自制件仅任务号关联排产,生产顺序不一致,集约范围需在设定的一定范围内,提前期不固定(多对多、多对 1、1对多)。
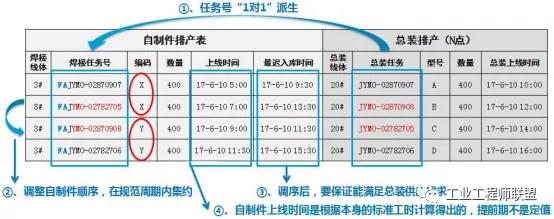
C、超市拉动:适用于通用性强的物料
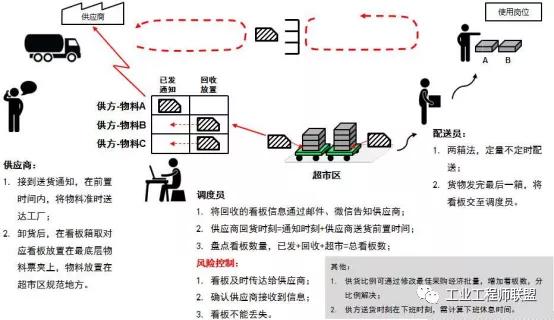
4.看板设计
1)看板设计总原则
A、N点投单
保证所有部装生产都是有总装需求才安排的,与总装计划按型谱匹配关系并按同一任务分层关联排产,形成定向拉动(部件战略储备可以理解为是有 PSI 依据的预测订单);
B、见单生产
单即是 MO票,就是生产指令,没有指令不能生产,保证生产执行受控,不做多,不错做, 制定 MO票“生成”、“发放”、“使用”、“管理”的每个细节,不是有 MO票就叫见票生产,更深层指的是员工有没有按照 MO票信息执行生产及物流配送,每个细项都要有人确认,MO票涉及到人员至少有:前工序作业员、巡检员、物料员、后工序投料作业员,MO票的使用和管理是重点;
C、票随实物、物在票在,到最后投入完成后在回收;
D、为了让拉动可以固化并日常化,建议把拉动的品质体系与财务体系结合。
2)看板种类
A、生产与配送看板:适用于部装与总装跟单任务的生产与配送;
B、生产看板:适用于部件战略储备库存的生产;
C、配送看板:使用于库存物料的投料配送,并与生产看板关联使用;
D、循环看板:适用于超市模式的生产;
备注:前三种都是一次性看板,第四种是可循环重复使用看板。
3)看板的内容
A、看板信息设计
遵循能准确表达“我是谁、从哪来、到哪去、停多久”,同时根据实际设计其他信息需求:型谱系列、工艺要求、品质要求、人力配置等;
B、看板是拉动信息的重要载体,具体内容:
——我是谁(物料名称、编码、任务号)
——从哪来(前工序产线)
——到哪去(后工序产线)
——停多久(前工序完工与后工序投入时间差,即提前期大小,同时反映了WIP 的大小)
4)注意事项
A、看板以能运作的最少数量为好
——多对多一定要使用看板
——连续流中单件流可以不用看板,小批量流和批量流要用看板;
B、 FIFO是为了不要排单,对品质追溯也是有好处。
5)生产与配送看板“生产”、“发放”、“使用”、“管理”细则
A、 看板生成:
a.内容要求必须符合看板信息设计要求;1.2 看板录入系统或下达:
b.看板录入系统/下达由专人(计划员/票据员)负责或系统联动自动读取;每天至少一次更新录入系统/下达的看板,更新频次依分厂标准而定,看板周期根据计划稳定情况依分厂标准而定;看板审核:系统或人工对生产提前期、任务重复、任务遗漏看板进行审核。
B、 看板发放
a.看板发放由专人(计划员/票据员)负责或系统自动发放;有发放提前期(x 时),依分厂标准而定。
b.看板打印确定责任人权限(计划员/票据员/班组); 需根据看板生产顺序打印;需根据器具装量拆分或系统自动拆分;打印频次(单个任务/x 时/单班/双班),依分厂标准而定;看板可投产前打印或打包后绑定器具信息打印(线头有生产指令看板)
c.看板传递需明确责任人(计划员/票据员/班组),保证看板不丢失。
C、看板使用
a.现场放置:非打包后打印看板卡的生产现场需确定唯一、固定、可直观指导生产的位置摆放看板。
b.看板移动:跟随件、跟单件:生产配送看板,跟随实物移动,按任务配送;共享件:生产看板,跟随实物移动,先进先出;共享件:
配送看板,与生产看板配套使用,依据需求任务-需求型号-共享件编码系统依先进先出原则分配并绑定需求任务与共享件生产信息。
c.看板填写:本工序看板打印时,制卡人确认看板信息无缺失,签名确认; 本工序生产完成时,打包员填写完成时间、完工数量,签名确认;下工段生产上线时,上线员填写上线时间,签名确认;品质人员盖章或签名确认;异常情况退料、收料、尾数等情况在备注填写说明。
D、看板管理
a.多联看板已完工的定人定向(生产/仓储/财务)回收保管,核对生产情况;
b.看板传递至终端,终端接受员工确认、使用完成后保留回收,保留期限依各分厂标准而定;
c.计划变动或异常产生的废票,备注废票,看板打印者签名确认回收; d:看板数据统计分析专人负责(纸质看板取数或系统取数)。
6)循环看板“生产”、“发放”、“使用”细则
A、看板生成:内容要求:必须有使用工段、型号、单包装数量、该型号总看板数,此看板数。根据设计库存量标准、标准器具装载量,制定一定数量的看板卡。
B、看板发放使用
a.水位看板数量确定(低水位/高水位);
b.看板发放由专人负责,从超市至生产机台;
c.当低于启动水位时,看板发放者投看板生产,已补仓看板跟随实物,未补仓看板在水位揭示板,总装投料后回收放回揭示板,先进先出,看板可循环使用。
7)MO 票现场执行流程图及标准要求
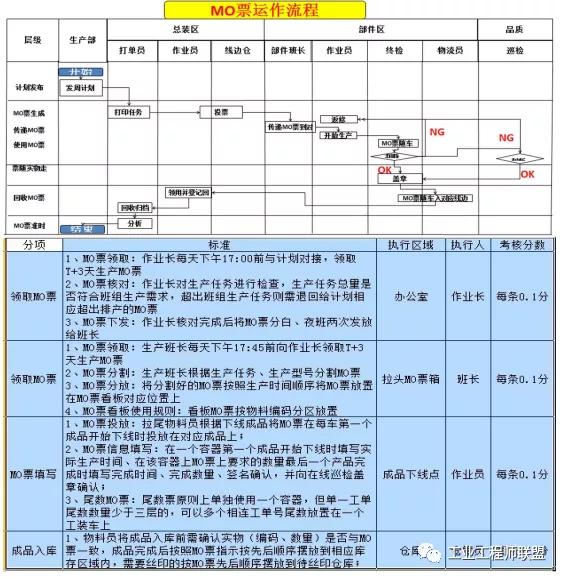
8)MO票作业指导书SOP
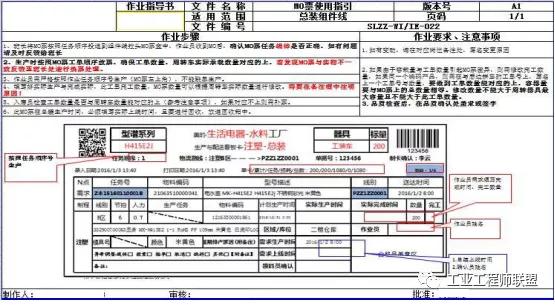
5.库存设计
1)库存模式
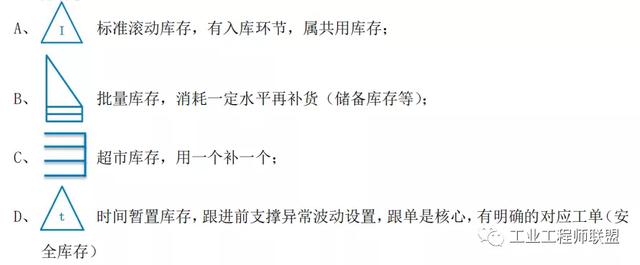
2)库存量计算
A、 各工厂可根据产品工艺实际情况,对《库存设计课件(赵国制讲)》公式进行微调;B、 目的:库存设计有据可依,有源可寻;
6.目视化管理
1)目视化管理的作用
辅助控制库存、易找料、易发现问题等。
2) 目视化的类型
A、 库位定制
——跟单库存按后工序线体定置,库位数与设定库存标准相匹配(建立线边仓);
——超市或战略储备库存按照编码定置;
——尾数区、异常区隔离定置;
B、 现场管理板
——操作流程管理板
——超市水位管理板
——库位管理板
C、 标识牌
——先进先出标识
——超期库存标识
——齐套料标识
7.拉动配送
1)自制件拉动配送模型
A、 小批量流,按容器流动;
B、 批量流,按工单流动;
2) 采购件拉动配送
A、 按任务拉动(两箱系统);
B、 补仓拉动式;
C、 按灯叫料式;
3)美的“协作云平台”整体设想:通过拉通供方内部信息,实现“Control Tower”全流程实施管控;
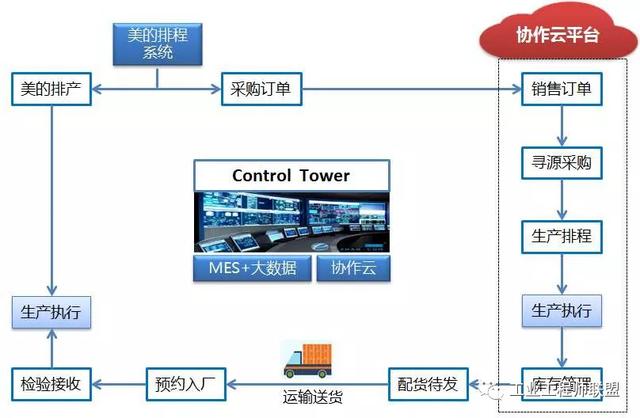
8.供方拉动
1)供方拉动生产模式
A、模式一:供应商完全线对线跟随美的生产,拉动供应商的生产、出货;
B、模式二:供应商集约任务排产,生产顺序与美的不一致,但出货顺序与需求一致;
C、仅拉动供应商仓库,按需求顺序回货,供应商按共享集约生产、编码管理;
2)回货模式
A、跟单回货(定时、JIT)
B、共享回货(定时、定量、JIT)
9.拉动需关注事项
1)拉动的确定:备料的周期太短;
2)透过预测让供应商备一定的原材料库存(含中长期物料、产能有瓶颈的物料);
3)当生产周期
4)第一阶段不要做别的改善,先做拉动;
5)小心:错误的方法去解决问题时问题会更大,要用精益的 方法来解决;
6)跟单是拉动的核心;
7)建立规则是拉动的基础;
8)当断点在靠近 N点出现时,尽量要用超市库存而不用时间暂置库存,这样对前部装工序影响最小。
内容补充:物料看板

1.看板介绍
老师所说的“看板”与美的推行价值流的“循环看板”基本符合一致,非在XX推动的看板(MO票/包含四种类型)的;尤其注意这个概念的理解,不然后续内容理解会有所偏差。
1)看板是一个拉动系统
2)看板用于控制过度生产,目视化控制及作为一种将流程联系起来的方法;
3)看板使用的三个情况:
- 在无法连接工作单元的各个流程时;
- 当流程交付时间大于固定主日程计划范围时;
- 针对价格低廉二公司不愿为其耗费管理资源的物品。
4) 思维上:看板是承认在单件流上的失败;
2.“推动”与“拉动”系统
1)“推动”和“拉动”的对比
A、推动系统与拉动系统的主要区别在于信息与实际产品的相关联方式;
B、拉动:订单信息从销售部(计划物流部)到工厂逆向流动;
C、推动:订单信息从计划部到工厂顺向流动;
2)什么是拉动系统
A、材料拉动系统的定义:下游流程(后工序)仅在需要的时候从上游流程(前工序)中取用必须数量的所需产品(必要的时间领取必须数量的必要产品);
B、使用的情况:操作周期时间限制、不可靠流程、交付时间长的流程、上游流程批量运行模式;
C、注意事项:拉动系统中产品差异可能是一个复杂因素;
3)推动系统的定义
推动系统或者材料需求计划(MRP)是一种复杂的计算机化库存生产计划体系,期规则与程序可以支持推动批量制造。
3.拉动体系的目标
- 同步化、流水线化、单件流生产;
- 任何时间生产一个单位的产品;
- 为顾客提供完美的质量;
- 接近于 0生产交付时间;
- 生产计划与订单调度之间更加密切的配合;
- 只有计划的库存和必要的库存;
4.拉动系统的实现
- 实现的基本条件:“均衡化生产”,根据客户需求以固定速度生产重复结构次序;
- 缩小并标准化批量,最终目标为实现每批次梳理为 1;
- 使用拉动系统控制材料;
- 从 MRP推动系统过渡到材料拉动系统;
- 随着需求及交付时间出现变化,维护补充系统。
5.看板类型及其工作方式
1)看板类型:运送看板、生产看板
A、 运送看板:当一个零部件容器移动到生产线时用于指示发生这种移动;授权从进料操作中取用;用于供应商(供应商看板)或者工厂(取用看板);
B、 生产看板:当需要生产一个或多个零件容器时候用于指示出现这种情况;授权进料操作部门生产零件;仅用于工厂(常规生产看板、信号看板);
2)看板工作方式:两箱系统
A、 一个在消耗材料的单元存放两个相同零件容器的系统;
B、 可以避免操作员使用时缺零件;
C、 第二个容器可以为材料处理员提供充足的时间来补充第二个容器材料; D、 目标:库存到达安全库存是下一个订单到达;
6.看板计算
1)安置轮(Setup Wheel)的定义:根据需求和切换以及设备的可用时间,用一个设备运行(生产)所有零件所需时间;
2)生产交付时间:从发出信号到收到零件(零件运送时间)+生产零件所用时间(零件生产时间);取决于生产安置轮,该安置轮决定通过设备的交付时间;
3)运送交付时间:从信号发出到收到零件,运送零件所用的时间;
4)计算交付时间
A、 确定对设备生产零件的每日需求;
B、 确定每个零件的运行时间;
C、 以分钟为单位计算设备的可用时间
D、 计算可月用于切换的分钟数=设备每天可用时间(分钟)-(每日需求*运行时间)分钟E、 确定零件到零件切换时间
F、 确定交付时间(天数)=(机器上零部件数*零件到零件切换时间)/(每天可用于切换的分钟数)
7.实施看板
1)看板实施的步骤
A、 工作单元就位,标准工作已完成;
B、 评议进度/需求管理,均衡化生产进度负荷;
C、 在供应工作单元建立生产看板;
D、 装配工作单元必须设置使用点储备,将看板卡放在零件上,并建立过程流程与责任划分, 以触发供应商;
E、 多余物料比移回供应区域,并提醒优先使用这些材料,这些材料放在超额区域中;
F、 制定看板系统及责任流程管理‘
G、 对操作员及供应商培训;
2) 衡量标准
缺货次数、库存水平、占地面积、库存交易数量、供应商交付表现、交付时间。
3) 看板八大原则
A、 后制程只向前支撑提取所需的物料;
B、 前制程只生产被提取的物料;
C、 无缺陷的产品才能并提取;
D、 看板容量要装满;
E、 在生产排程计划内建立平稳生产(这是关键及基本条件);
F、 假如实际的需求变化比计划偏差超出 20%,就要重新计算看板
G、 看板要与物料一起移动;
H、 定期维护看板,看看是否要改进;
I、 不要违背上述 1~7条原则;