本文基于车型开发过程中遇到的螺纹连接失效问题,建立螺纹连接失效模型。
通过对引起扭矩衰减、磨损压溃、螺纹脱扣及松脱失效的各项关键因素进行理论分析,提出通过结构设计优化、扭矩优化、零件质量控制及拧紧工艺优化等改善措施进行验证,最终有效保证整车螺纹连接可靠性。
前 言
螺纹连接由于具有结构简单、装配方便及连接可靠等优点,是整车装配中最常用的连接方式,占总装车间装配连接工作量的 70%。
同样螺纹连接失效问题在维修记录方面占比较大,据统计 23% 的维修问题都是由紧固件失效引起的,12% 的新车存在紧固件拧紧度不正确问题。
连接失效主要表现为螺栓断裂、螺纹滑牙、螺栓螺母未发生转动但扭矩明显下降及被连接件压溃或塑性变形等现象。
本文主要以实际生产过程中常见螺纹装配失效问题为基础,对失效问题进行原因分析并提出有效改善措施。
一、螺纹连接失效模型
螺纹装配采用扭矩法施加扭矩,扭矩分为两部分,分别克服螺纹副摩擦扭矩和紧固件法兰面与被连接件支承面间摩擦扭矩后使螺栓产生弹性拉伸获得适当的轴向夹紧力:
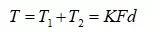
(1) T—总扭矩;T1—螺纹摩擦扭矩;T2—支撑面摩擦扭矩;K—扭矩系数;F—轴向预紧力;d—螺纹公称直径;
根据相关文献,在拧紧扭矩作用下,螺栓既受到轴向夹紧力产生的拉伸应力,还受螺纹摩擦扭矩的扭转产生的扭转应力,在分析螺栓连接是否失效需要判断其复合应力是否小于其屈服应力:

(2) 其中扭转应力为:
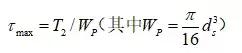
(3) σred,B—复合应力;σmax—拉伸应力;τmax—扭转应力;Rp0.2min—屈服应力;ds—等效应力直径;wp—抗弯截面系数。
同时,在进行被连接失效分析时,需要根据实际判断连接承压面,常见有平面和锥面等连接形式,如图1所示,保证连接承压面不产生压溃或塑性变形,即最大表面压力不超过被连接件材料限制表面压力:
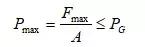
(4) Pmax—单位面积压应力;PG—临界应力;A—应力截面积。
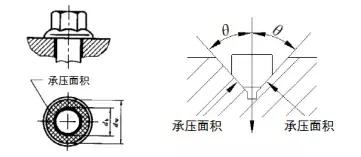
图1 螺纹连接承压面形式
二、连接失效原因探讨
螺纹连接失效最终原因是轴向夹紧力不足。结合实际生产装配过程中遇到的连接失效问题,主要表现为扭矩衰减、被连接件压溃、螺纹滑牙、螺栓松动断裂等,针对各失效形式进行原因分析并提出有效改进措施。
3.1 软连接引发的扭矩衰减
一般认为,硬连接和中性连接不存在扭矩衰减,软连接扭矩衰减较为严重。
但在实际生产、使用过程中,对于任何连接,随着时间的推移都会有一定程度的扭矩衰减,软连接中扭矩衰减尤为严重,扭矩衰减不能完全避免,只能通过对各种影响因素的控制和优化来改善衰减状况,确保扭矩衰减后的夹紧力不低于设计夹紧力的最低要求。
以某车型行李架螺栓连接(中间具有防震棉)失效为例,螺栓规格为 M6x1-8.8,目标扭矩为 8N*m,利用电枪拧紧到设定扭矩后,经过颠簸路试后检测左右两侧连接点扭矩数据如图2所示,扭矩衰减严重甚至出现松脱现象。
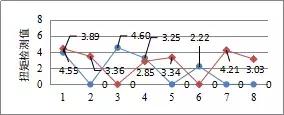
图2 检测扭矩分布图
针对该软连接引起的扭矩衰减控制措施有转速控制及分步拧紧,降低转速和分步拧紧有效缓解高转速造成的应力集中及短时间内应力无法释放。
拧紧转速控制即降低转速,将手持式直枪更换为脉冲气动弯头枪,转速由1500r/min 变为 430r/min;分步拧紧即两步拧紧,间隔 0.5s 继续拧紧。
采用上述两种方法进行装配,经检测扭矩维持在 6N*m-8N*m 范围内,衰减比例为 25%,满足性能要求。
3.2 被连接件磨损及压溃
3.2.1 磨损现象
被连接磨损主要原因为表面嵌入。表面嵌入主要因为螺纹拧紧过程中,螺纹接触面、紧固件支承面和被连接件接触面存在一定程度粗糙度、垂直度及平面度,拧紧后粗糙表面相互嵌入,不平整的表面会产生很大的局部塑性变形,造成扭矩衰减及轴向夹紧力减小;
针对该种失效模式,设计初期考虑连接嵌入造成的夹紧力损失,相应增大轴向夹紧力,通过嵌入量的变形补偿轴向夹紧力,见示意图3,即:
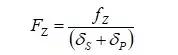
(5) 式中:fz—嵌入量(嵌入导致的塑性变形);
δs—螺栓的回弹量 ;δp—被连接件的回弹量
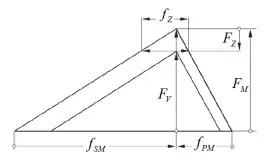
图3 嵌入量的变形引起夹紧力的减小
3.2.2 压溃现象
被连接压溃主要原因为扭矩设计过大或承压面过小,导致被连接件所受压力大于其自身限制压力,被连接件出现塑性变形,内部应力减小,引起扭矩衰减;针对该情况,需要正确设计扭矩控制轴向夹紧力;也可通过增大法兰面、增加平垫圈和减小通孔直径等方法增大螺栓螺母与被连接件接触面积。
3.3 摩擦系数对夹紧力一致性影响
装配拧紧后对连接件进行残余扭矩测量是判断连接可靠重要步骤,一般在装配后 5min 内进行扭矩测量。
以某车型副车架与车身连接螺栓为例,检测扭矩超差达±30%;经过排查分析主要原因为零件摩擦系数散差大,即支承面摩擦系数波动范围大(紧固件摩擦系数为 0.13±0.03,但支承面间摩擦系数为经验值),拧紧检测时克服支承面摩擦扭矩与设计状态不一样,必然出现扭矩超差现象。
将螺栓规格(M12x1.25-10.9)参数代入公式(6)可知摩擦系数不同对夹紧力的分布:

(6) 扭矩转化比例:
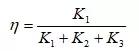
(7) K1—预紧力扭矩系数;k2—螺纹摩擦扭矩系数;
K3—支撑面摩擦扭矩系数;η—转化比例;
表1 摩擦系数对夹紧力影响
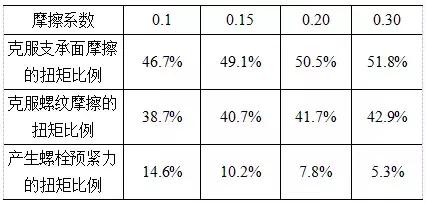
由表1可知,摩擦系数 0.15 相对 0.1,扭矩转化比例减少 40%,由此可知控制摩擦系数稳定性是保证夹紧力一致性的必要条件。针对该问题可采用增加平垫圈方法改善,见示意图4。
由于平垫圈具有增大接触面积、摩擦系数稳定等特性被广泛应用于底盘重要连接点,最终通过增加平垫圈措施将副车架与车身连接点扭矩衰减控制在±15%以内,属于正常衰减。
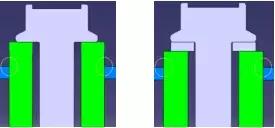
图4 增加平垫圈改变接触面及摩擦系数
3.4 螺纹脱扣
3.4.1 失效原因分析
某车型铝合金副车架采用螺栓与铝内螺纹连接结构,螺栓规格为 M12x1.25-10.9,啮合长度为 20mm,如图5所示,扭矩为 145±10N*m,耐久试验发现螺栓松脱导致副车架异响,经排查发现螺纹滑牙脱扣,详见图6,通过分析其主要原因是由于其啮合长度不满足要求。
当啮合长度过短情况下,外螺纹强度(1040Mpa)大于内螺纹强度(220Mpa),则会在内螺纹根部易发生剪切破坏,反之,剪切破坏将发生在外螺纹根部;故铸铝合金啮合长度一般选取 2d-2.5d。因此通过副车架内螺纹啮合长度优化提升连接可靠性。
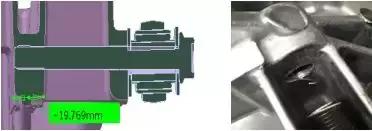
图5 内螺纹啮合长度 图6 螺纹脱扣
3.4.2 螺纹脱扣模型建立
通过对失效案例进行分析,建立螺纹脱扣模型,防止螺纹脱扣,必须保证外螺纹断裂应力小于内螺纹剪切应力,螺纹副接触模型见图7,即:
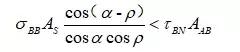
(8) 其中:
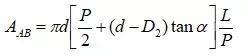
(9) σBB—螺栓抗拉强度;τBN—内螺纹剪切强度;
α—牙侧角;ρ—摩擦角;P—螺距;L—螺纹啮合长度;D2—内螺纹中径;
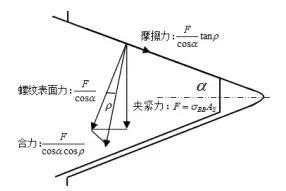
图7 螺纹受力模型
将公式(8)代入(7),可知螺纹不脱扣所需最小螺纹长度
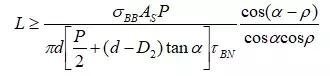
(10) 由此可知,为保证可靠连接,在选取螺纹啮合长度时需要对内外螺纹强度进行校核。
3.5 横向振动引发的螺栓松脱
3.5.1 失效原因分析
某车型稳定杆拉杆紧固扭矩严重衰减,由初始螺母(M10x1.25-10.9,摩擦系数 0.13±0.03)扭矩 50N*m 衰减至 10N*m,且支架孔变形、接触面凹陷,如图8所示,最终导致严重异响。
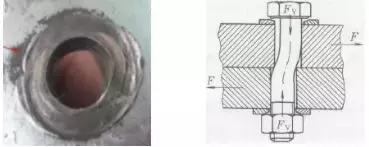
图8 孔变形及凹陷 图9 横向载荷引起振动
针对该失效问题进行分析,可能导致的原因有两个:
a.轴向夹紧力不足,紧固点受到横向交变载荷会导致螺栓轴线的倾斜,如图9所示,造成螺纹受力不均,受力小的一端摩擦扭矩减小不足以抵抗外螺纹扭转力,产生微滑移,静摩擦变为动摩擦;随着时间的推移,螺纹副之间的滑移愈加明显,最终导致螺孔挤压变形、松脱甚至断裂。
b.结构缺陷:支架双层板间有间隙,导致扭矩验证衰减重要原因。
3.5.2 控制措施
首先,通过工艺保证支架双层板零贴无间隙,消除板间间隙引发的扭矩衰减风险;第二步对拧紧扭矩进行分析验证。
该连接点受到三个方向的力Fx(0.6KN)、Fy(0.4KN)、Fz(4.5KN)。转化成紧固点轴向与横向受力,即轴向载荷由 Fy 组合,横向载荷由 Fx 与 Fz 合力组成。
经过分析,当抗滑移安全系数为 1.1 前提,抗滑移最小夹紧力为 33.3KN,将夹紧力代入扭矩公式(11):

(11) 式中:F—轴向预紧力;d2—中径;μsmin—螺纹摩擦系数;μbmin—支撑面摩擦系数;Dw—等效支撑面直径
经计算得出最小扭矩需要 66.6N*m,而设计扭矩仅为 50N*m,不能保证可靠连接,故通过提高扭矩至 70N*m,保证足够轴向夹紧力有效解决连接松脱问题。
总 结
针对车型开发过程中遇到的螺纹连接失效问题,建立螺纹失效模型,并列举常见的扭矩衰减、磨损压溃、滑牙脱扣及松脱等现象;通过对各项关键影响因素进行排查及理论分析,提出对结构设计优化、扭矩设计优化、零件质量控制及拧紧工艺优化等措施有效解决连接失效问题,从而保证螺纹连接可靠性。

原创: 王晓斌、刘艳兵