冷挤压成形是一种常见的材料塑性成形工艺,它具有成形零件力学性能高、精度等级高、表面粗糙度较低、生产周期短、节约资源、节能环保等诸多工艺优点,在许多工程领域得到广泛应用,尤其是在汽车工业中。水阀套零件是液压系统中节水阀的一个重要零部件,由于是在汽车液压系统中进行工作,水阀套零件与阀芯相连接,因此需要满足较高的尺寸精度。目前切削加工是水阀套零件较为常用的加工工艺,但相较于切削加工,冷挤压成形材料利用率高,更环保,生产周期也更短,可大大提高生产效率。
水阀套零件挤压成形工艺方案设计
在进行水阀套零件挤压成形工艺方案制定前,需要先对相应零件坯料进行热处理,本文选取的水阀套零件材料为20Cr,其材料力学性能参数及化学成分如表1、表2所示,退火处理方式如图1所示,坯料加热至860℃,随炉冷20℃/h,冷却到300℃后转为空冷。然后,对零件坯料进行表面润滑处理,本零件采用传统表面润滑处理工艺—磷皂化处理,其主要目的是减小坯料和模具之间的摩擦力,有效提高工件表面质量及挤压成形模具寿命。
表1 20Cr化学成分表

表2 20Cr基本力学性能

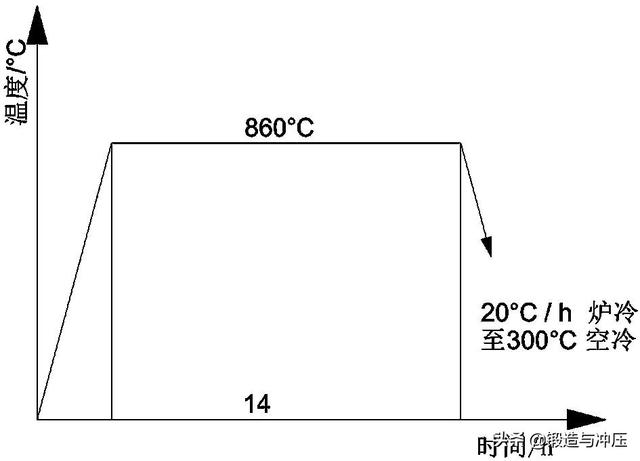
图1 20Cr退火工艺示意
为了确定合理的水阀套零件加工成形工序,需计算其断面缩减率,进而制定其成形工艺的工序,根据公式

(d0为挤压变形前毛坯直径,d1为挤压变形后杯套外直径,d2为挤压变形后杯套内直径),分别计算出零件上半部分的断面缩减率为13.82%和下半部分的断面缩减率为63.84%,查阅相关文献可得,20Cr反挤压许用变形程度为30.05%~64.31%,正挤压最大许用变形程度为76.20%~81.20%,采用复合挤压一次成形即可完成零件的成形,因此对该零件设计了两种复合挤压成形工艺方案,如图2、图3所示。
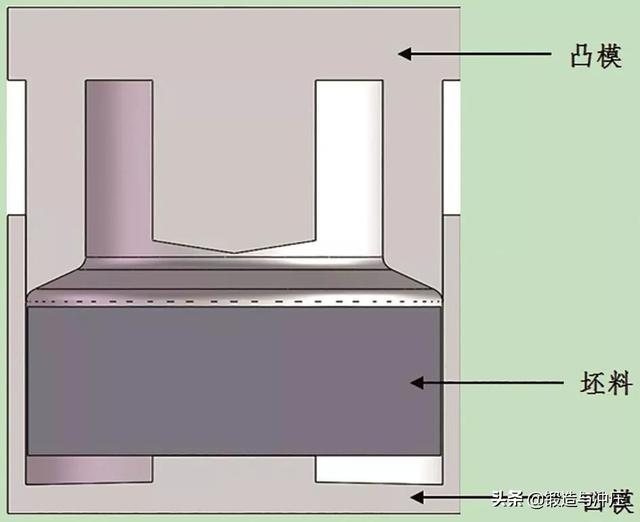
图2 复合成形方案一
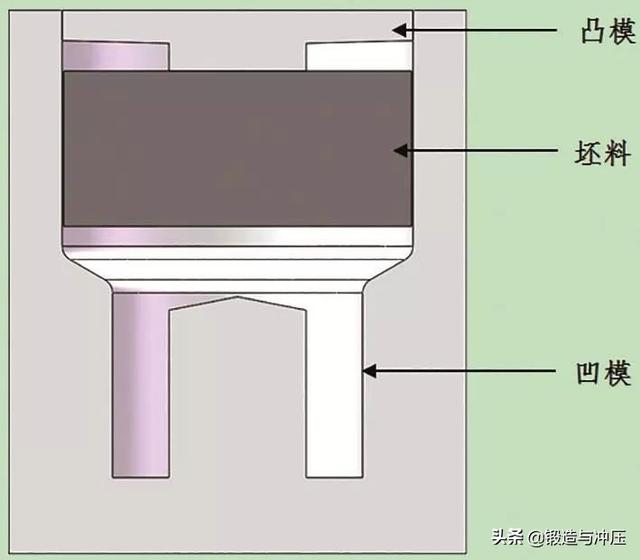
图3 复合成形方案二
方案二由凸模自上而下运动,一次复合挤压成形。根据拟定的两套复合成形方案分别在SOLIDWORKS软件中建立相应的工模具几何模型,然后在DEFORM-3D软件中导入其工模具几何模型并进行相应的FEM模型建立,后续数值模拟试验均采用DEFORM-3D软件完成。
数值模拟试验及结果分析
为了节约成形运算时间,提高运算效率,在模拟试验中,两种复合成形工艺方案均采用1/4模型进行数值模拟,所获得的成形件等效应力、等效应变、变形速度矢量以及损失因子分布云图,分别如图4、图5所示。由模拟试验结果可知,方案一和方案二都能实现该零件的成形,且等效应力、等效应变、变形速度矢量以及损失因子分布差异不大,但众所周知,在冷挤压成形中,挤压力是决定挤压成形的关键因素,挤压力大小对模具寿命及设备选择等都起着关键作用。方案一和方案二所获得的挤压载荷曲线如图6所示,根据图6可知,采用方案一时,最大挤压载荷为8.97×105N,采用方案二获得的最大挤压载荷为5.02×105N,得出采用方案二可有效减少挤压力。由此可知,在一次复合挤压成形中,金属流动方向与冲头运动方向需要认真考虑,尽可能将金属流动最大部位做正向挤压,这样能有效减少挤压力。
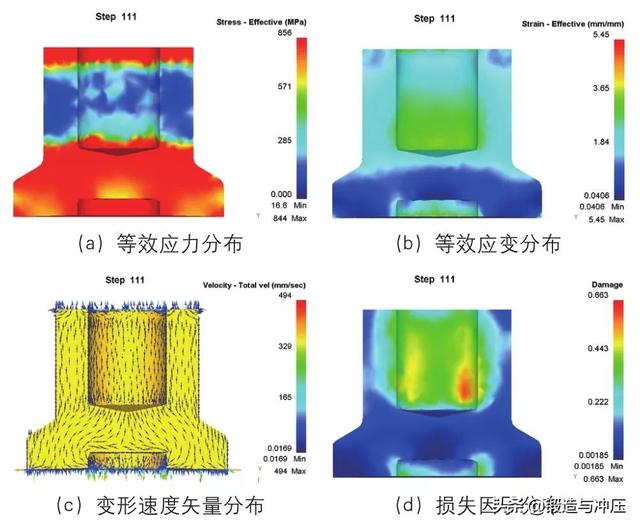
图4 方案一模拟试验结果
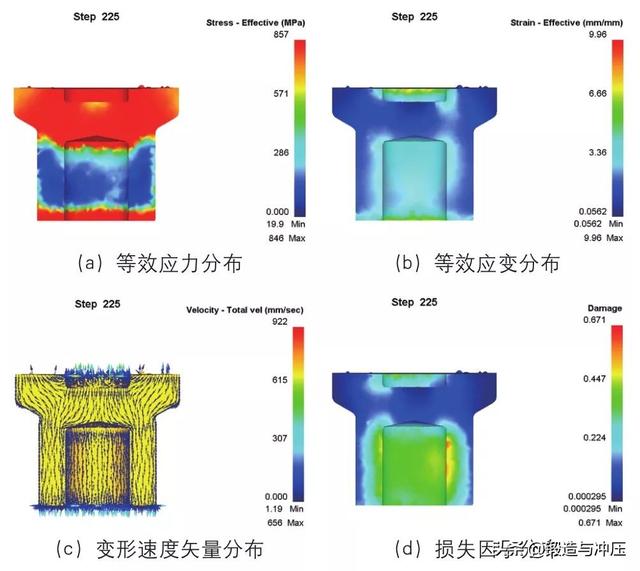
图5 方案二模拟试验结果
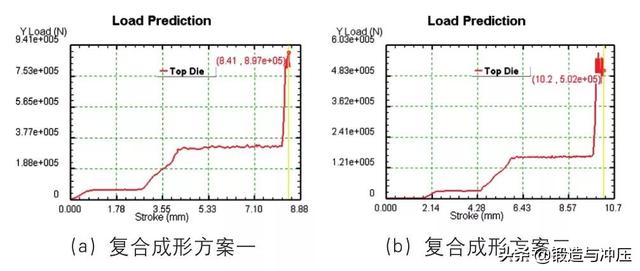
图6 挤压载荷曲线
对主要成形工艺参数进行正交优化数值模拟试验及分析
正交试验的基本流程如图7所示,先根据正交试验所要达到的目标对各项参数进行筛选,在选定参数后,确定各项因素及其水平数,然后再根据正交试验所要达到的目标对各项因素建立合适的正交表。

图7 正交试验基本流程
在进行水阀套零件冷挤压成形数值模拟试验研究中,选取了挤压速度、坯料倒角以及摩擦系数三个不同的工艺参数进行正交试验,采用3因素3水平正交试验设计,如表3所示,9组具体的试验取值如表4所示。
表3 正交试验3因素3水平选取表
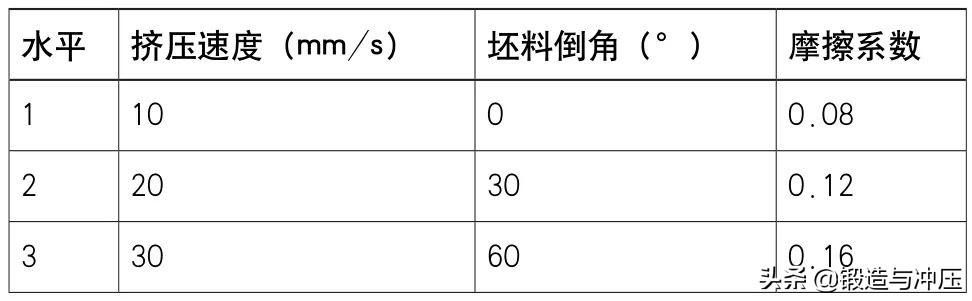
表4 正交试验模拟参数表
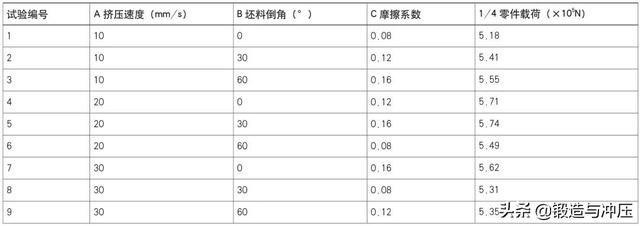
根据上述参数制定正交试验的参数表,并生成项目文件。根据上述设定参数进行数值模拟试验,从而得到各组参数下的挤压载荷数值,如表4所示。绘制正交极差分析的流程,如图8所示。
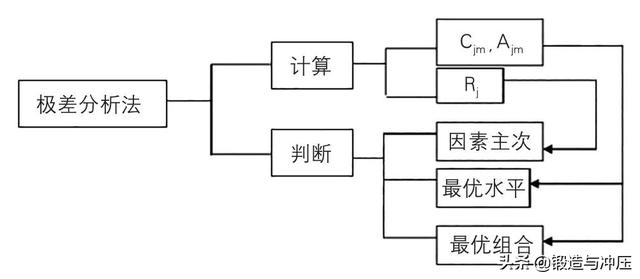
图8 极差分析法流程图
在图8中:(1)Cjm中j为第j列因素,m为第m行水平数,Cjm代表了第j列因素的第m行水平的试验值;(2)Ajm则是Cjm的平均值。当j因素的水平进行变动时,通过Rj能够得出试验指标的变动幅度,根据Rj的大小可判断出因素的重要性,从而对因素进行排序,如表5所示。
表5 基于载荷值评估的极差CAE分析试验结果
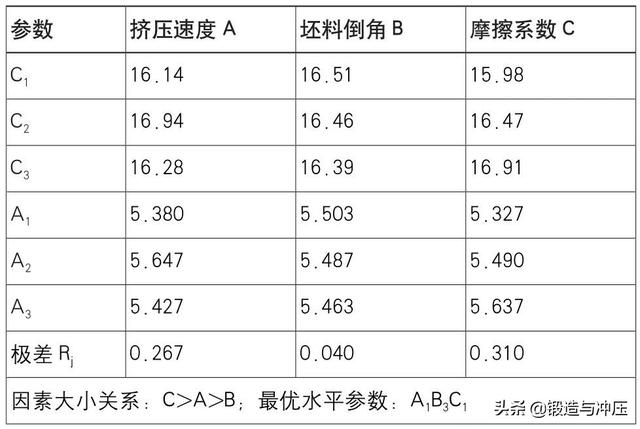
通过上述极差分析法可知,得到的最优化工艺参数如图9所示,其最优工艺成形方案是:在凸模挤压速度为10mm/s、坯料倒角为60°、摩擦系数为0.08的情况下,获得的挤压载荷最小。
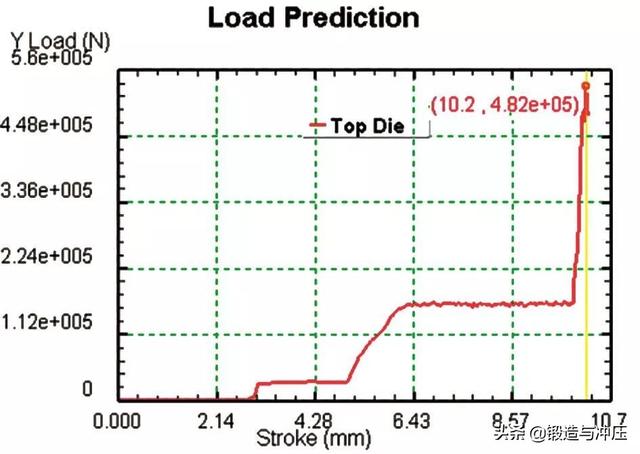
图9 最优工艺参数挤压成形凸模载荷曲线
结论
本文对一种典型的车用水阀套零件进行了冷挤压成形数值模拟研究,获得的主要研究结论如下。
⑴根据理论分析,采用了两种一次复合挤压成形方案,通过数值模拟试验得知,采用方案二获得的试验结果更理想,由此可知,在进行一次复合挤压成形中,要尽可能将金属流动的主要部位设置为正向挤压,这样可以有效减少挤压力。
⑵选取挤压速度、坯料倒角以及摩擦系数三种工艺参数,根据3水平3因素正交数值模拟试验,获得了水阀套零件的冷挤压成形最优参数组合为:凸模挤压速度为10mm/s、坯料倒角为60°、摩擦系数为0.08的情况下获得的挤压载荷最小,其挤压载荷为4.82×105N。
—— 来源:《锻造与冲压》2019年第17期