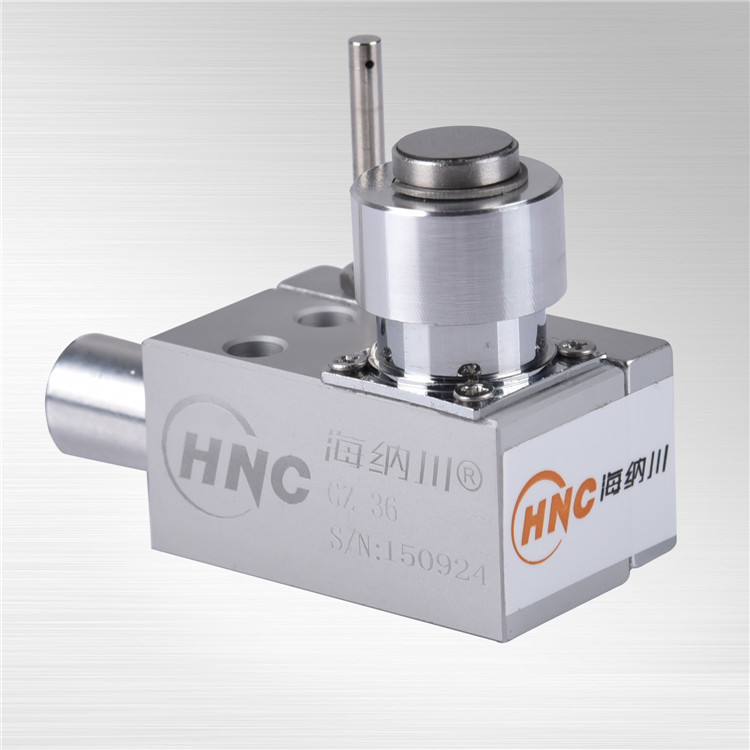
一、在我国使用的数控加工设备中,通常采用对刀装置测量刀具长度,采用红外触发探头,然后红外接收器向数控系统发送开关信号,实现刀具长度的测量。对于直刃刀具,需要测量刀具的角度,这是红外触发探头无法实现的。如果配备专用角度测量仪,不仅成本高,而且解决了与数控系统的通讯问题。因此,根据被测刀具角度模拟值的大小,利用数控系统的模拟输入接口,实现数控机床直边刀具的自动对刀,是一种简单、实用、低成本的有效对刀方法。
二、对刀装置原理设计
如图1所示,采用激光传感器和宏程序实现自动对刀功能。尖直刀的角度对刀首次采用模拟量对刀技术。尖直刀的角度对刀,是找刀刃的准确角度,将激光传感器中获得的模拟值传送给数控系统,由数控系统通过比较计算,系统自动记录下刀刃在的机械坐标的位置,自动设定刀具角度坐标,完成刀刃角度的自动对刀功能。
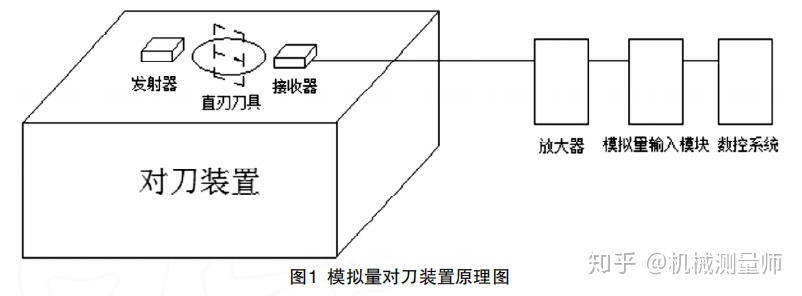
三、设计实施方案
利用基恩士 IB10激光传感器作为超声主轴直、圆刀具的基准刀具。其中,FU系列传感器用于参考刀具长度的设定,IB系列传感器用于参考直线刀具角度的设定。为了完成直刀角度对刀功能,首先尝试利用数控系统中传感器输出的模拟信号来识别刀具角度。传感器输出的模拟信号通过HIO模拟输入子模块传输到数控系统。当设定刀具角度时,系统首先获得刀具在刀刃位置的最小模拟值,即传感器中遮光最少的刀具位置。刀具刀刃的位置坐标由最小模拟值确定。整个对刀过程由对刀宏程序完成。在加工程序中,只需输入相应的刀具号,系统就会自动完成刀具长度和角度的参考刀具设定,并在系统中自动设定和补偿,无需做任何其他操作,有效提高了加工效率。
使用激光传感器中直刃挡住的光量来确定刀刃的位置。将激光传感器遮光强度的模拟值传递到数控系统,通过PLC程序和数控系统自动对刀宏程序的处理完成刀具角度的设定。
四、PLC程序对模拟信号处理
(1)获取最小模拟量:用M35和M36分别指定为开启和关闭获取最小模拟量信号。开启后,刀具旋转半周以上,获取模拟量最小值。
(2)刀具角度测量:用M32和M33分别指定为开启和关闭刀具角度测量。开启后,通过刀具旋转角度的实时模拟量与刀刃位置模拟量最小值进行比较判断,获得刀刃所在的位置。
五、结语
采用模拟量刀具角度对刀方式,成本低,操作方便。应用于某飞机制造厂超声数控铣削直刃刀具的标定。在加工程序中,只需输入相应的刀具号,系统会自动完成刀具角度的参考标定,并在系统中自动设置。而补偿,无需做任何其他操作,有效提高了处理效率。
——海纳川机电