
项目背景及主要业务挑战

航空发动机燃油管路系统仿真分析为燃油系统及其控制系统的设计和产业化提供支持,同样也适用于发动机控制系统的设计和优化。由于燃油管道系统涉及的专业面比较广,有机械、液压、控制等,因此用于产品设计的仿真工具必须具备多学科专业建模和分析的能力。
对于燃油管道系统设计,需要从时域了解系统的动态和稳态特性,以及从频域洞悉系统的内在特性,从而设计控制系统的控制算法。要求系统仿真软件具有丰富的标准库元件模型,如液压库、液阻库等。具备液压管路三维几何模型自动转为系统模型的能力,具有元件参数化研究和优化功能。

项目目标及总体方案

使用仿真分析软件,通过专用的模型库搭建燃油调节系统功能模型,设定管路直径、长度、流体阻力系数等参数条件,计算不同工况下动态流量和压力特性,根据得到的数据对产品结构、管路流道进行优化设计。按照上述设计流程进行反复迭代,最终得到最优化的产品,从根本上解决燃油调节系统在外场出口流量波动问题。
在系统工程设计仿真平台上,用户可以建立复杂的多学科领域系统模型,并在此基础上进行仿真计算和深入的分析。利用系统仿真的频域分析工具,可以求解系统的特征值;绘制Bode图、Nichols图、Nyquist图;进行根轨迹分析、模态分析和频响分析。
通过系统仿真系统中的三维降阶工具,能将三维CAD模型自动或半自动转换成一维系统仿真模型,自动提取CAD模型的长度、半径、面积、体积等参数,并将参数自动赋值给系统模型,从而完成燃油管路关键参数的分析和优化。

实施内容

此项目以Simcenter Amesim为基础平台建立燃油管路的系统仿真模型,通过子模型的选择和参数定义,探索研究管路系统内部各种物理量的动态变化规律。燃油管路系统包含液压油、各种液压泵、液压阀和流体管路,整个系统模型中包含了机械、液压、管路等多种元件和多个学科,需要考虑流阻效应,专用阀门和阀套等部件设计。帮助用户基于动态建模方法建立物理元件的数学模型,利用软件专业应用库和辅助工具,快速创建燃油管路的系统模型,对管路中的液压泵功率、阀芯形状尺寸、传输管路弯曲曲率等做了深入研究和计算优化。
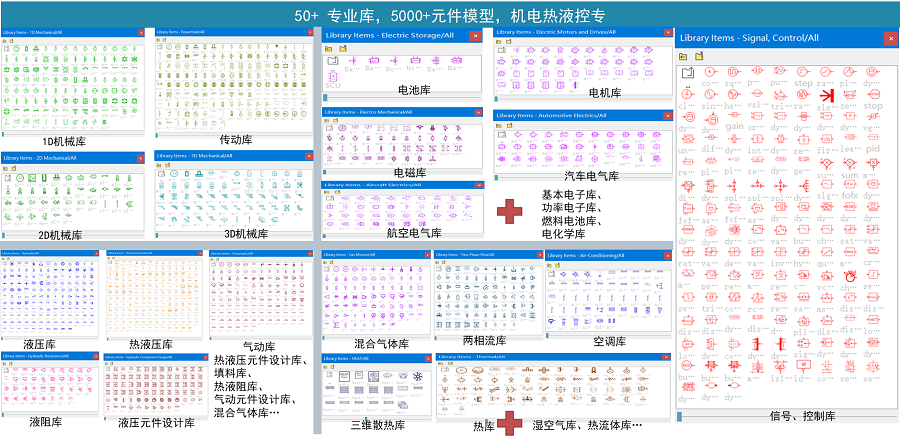
在燃油管路系统建模时,使用Simcenter Amesim液压库中标准元件,如管道、节流口、油箱、可变容积、液压泵等多个标准模型,只需要选择合适的子模型和参数设置,即可完成液压系统性能仿真。帮助用户利用液压元件设计库,不用通过编程,直接根据液压元件CAD几何图纸尺寸,创建燃油系统液压部件中阀芯、阀套的详细系统模型,对元件几何参数进行优化分析。在液阻库模型库中,使用了弯管、分叉管、渐缩管、渐扩管、突缩管、突扩管等元件模型,很方便地搭建燃油管路液压系统,并计算管路系统管网中各处的压力损失和流量分布。
根据某厂不同的设计阶段和分析目的,灵活选用液压库和液压元件设计库中的元件模型,创建燃油管路系统不同复杂度模型,以液压泵和液压阀为例,创建了功能级和性能级的系统模型。
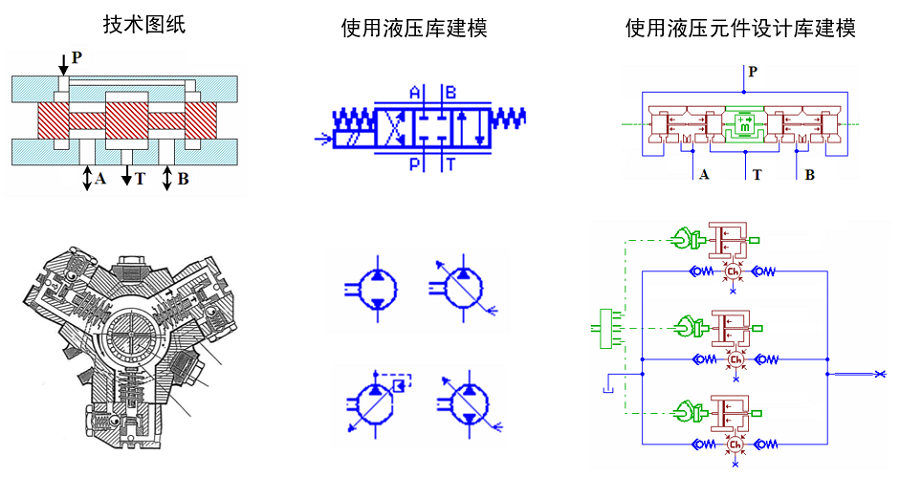
通过三维CAD转一维模型工具,对导入的燃油管路系统进行自动几何参数识别,通过自动和手动的模型关联,自动将参数赋予给参数模型,用于燃油管路系统建模和仿真计算。
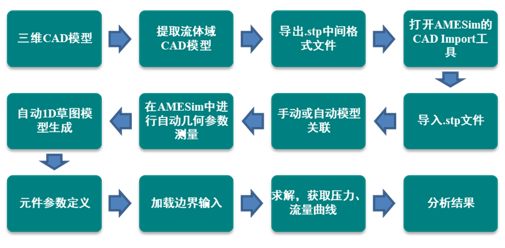
燃油管路系统仿真流程如下:
1) 打开系统的CADImport导入工具界面,导入.stp流体域(燃油管路系统的部分模型举例)。
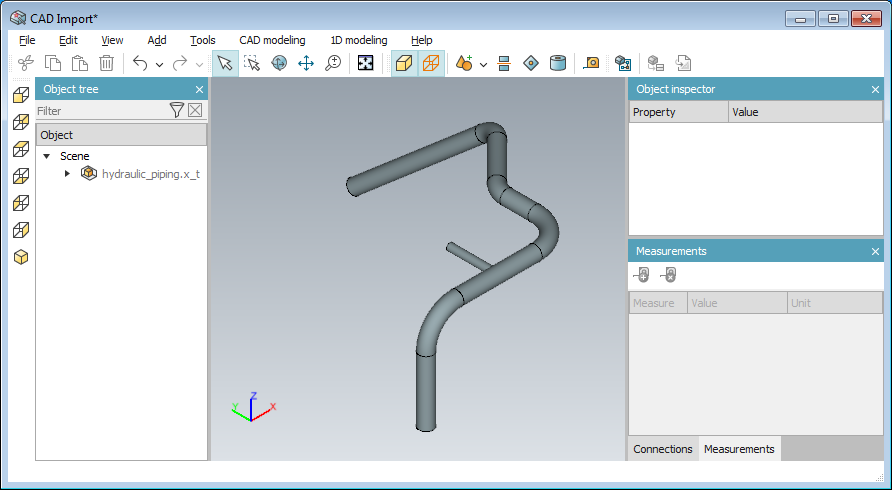
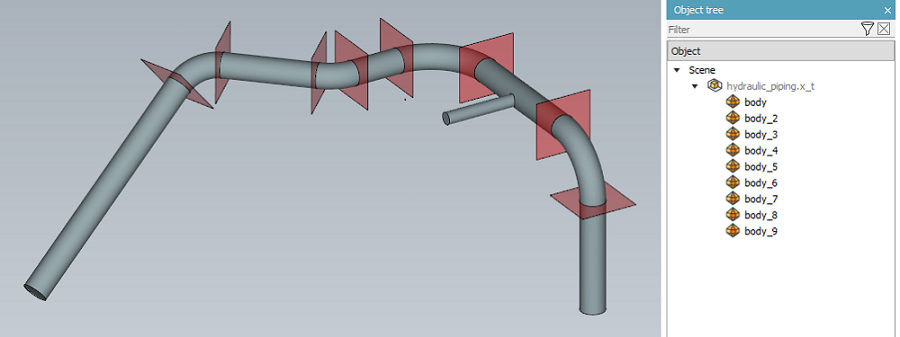
3) 创建模块连接关系,可自动创建所有的连接关系,并检查连接关系是否正确或者遗漏,如有可以手动修正和补充。
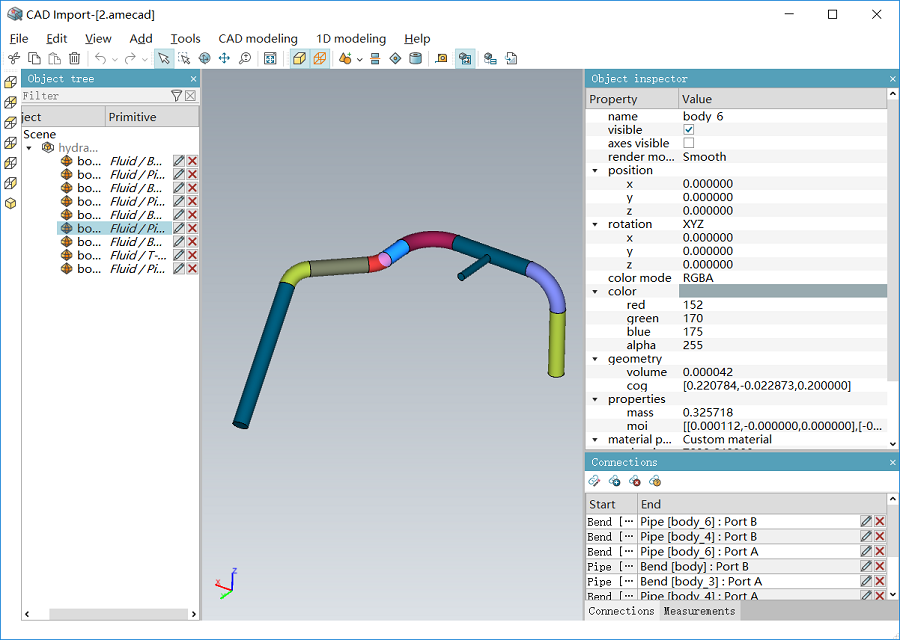
4) 生成一维模型。
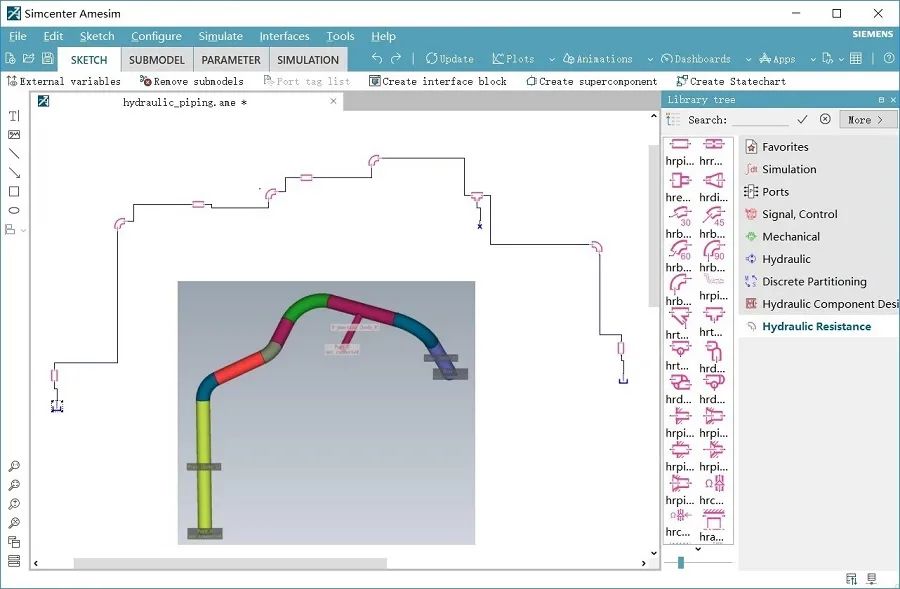
5) 重复上述操作,进行模型集成,另外针对特别的阀口或者特定的形状,需要手动按照经验更改。

项目创新点


实施成果

2) 利用批处理功能,计算元件模型在不同参数设定值下的仿真结果,很方便地进行系统参数研究和优化,实现了产品设计——系统仿真——设计优化的闭环迭代。
3) 通过系统仿真的手段,很好地解释产品的某些工作现象,探索引起流量波动故障的原因,为产品的优化方向提供仿真数据支撑。
4) 通过系统建模和分析,对燃油调节器系统的工作机理有了更深入的认识,提高工程师的设计信心,减少了部分物理实验,缩短了研制周期,提高了产品一次通过率。
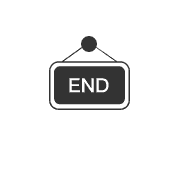


天圣华信息多年来根植于国防军工行业,以对军工制造模式的深刻理解,数字化、自动化业务的丰富积累和“专注军工智能,鼎力中国制造”的坚定初心,服务于我们的客户。
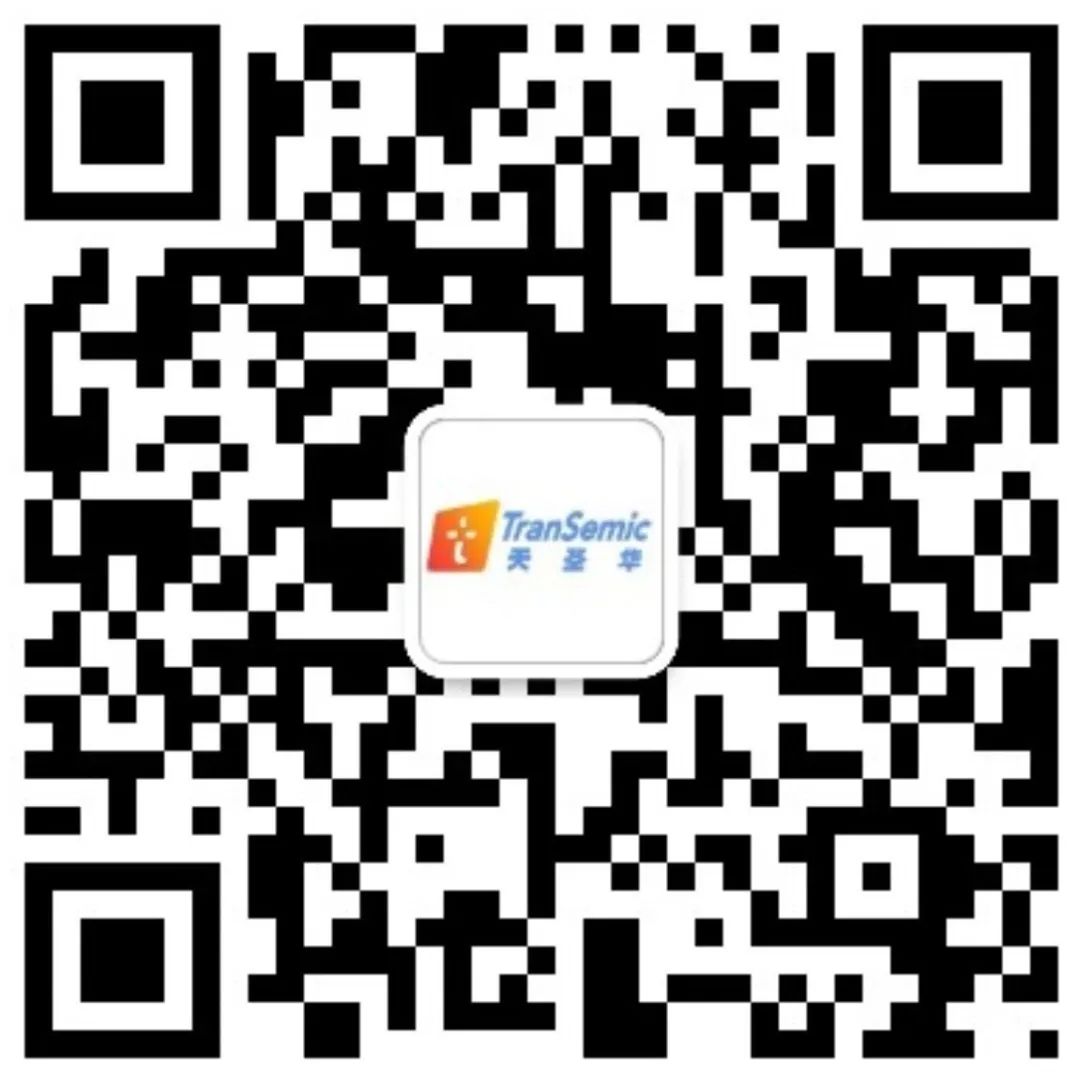
关 注 我 们
了 解 更 多
www.transemic.com
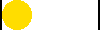