库存(Stock)是用来提高交货速度、缓冲需求到单高峰的常用手段,通过按库存生产(MTS)的方法,用储备库存来满足客户需求、并按一定规则补货,无需等待生产周期,可极快地交付。相比按订单生产(MTO)的模式,采用安全库存可以有效控制风险。
但难免存在问题,诸如库存费用导致产品成本增加、销路不畅导致库存积压、短生命周期产品随存储时间增长而导致贬值、贵重产品做库存潜在风险高等。如何根据市场需求实时动态调整库存,即可以满足市场订单发货需求,又可以最大化地降低成本,保持渠道的新鲜度呢?笔者基于业务实践,尝试为您你呈现一种解决方案。
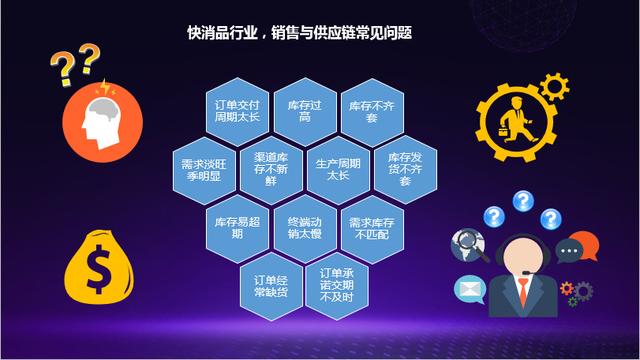
如何确定合理的库存模型?
库存设置的目的,本质是为了应对未来的市场到单需求,提高交付效率。评估库存设置是否合理,关键在于是否能够确保在低库存、高周转率的前提下,能够尽可能地准确满足未来的市场到单需求。
不同商品有各自的市场周期规律,再结合市场策略、发展目标、促销计划、重点客户与区域需求、不同产品的淡旺季等,可以做出一定程度的市场预测。不同商品又有各自的生产周期,加上经济批量、转产换型周期、品质周期、库存新鲜度要求等,结合上述市场预测,通过多因子模型可以构建出最佳的目标库存、安全库存以及补货频率。
接下来,我们以实际案例来谈谈如何根据销售预测应用排程易APS库存模型,动态制定合理的库存~ ☟☟☟
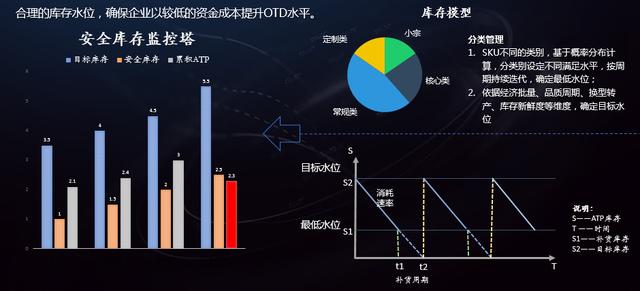
在示意图中,库存始终是有富余的,因为补货及时,需求也很均衡,库存低“水位”时触发补货需求,生产后迅速补货到目标“水位”。但实际市场需求是波动的,库存消耗速率也不断变化,比如一条产线可生产多个品种,一个品种可以有多条生产产线,各品种的市场需求结构实时变化,其补货周期随之动态更新,原本设定的库存最低水位和目标水位,往往需要根据市场实际情况进行快速动态调整。
库存最低水位=生产补货周期*预计消耗速率,那我们如何确定生产补货周期和预计消耗速率呢?
其中,预计消耗速率可以根据我们前面所讲的,基于多因子市场销售策略和周转策略的销售计划,再结合渠道库存周期天数、库存新鲜度等要求制定。简要来讲,如果一个月每天都出货,预计消耗速率=月度总量/当月天数,如果有若干天休息不发货,则可以扣减天数之后再计算平均出货速率,得出日均市场需求量(即理论出货速率)。
实际出货速率肯定会有波动,则可以通过排程易APS系统动态监测,实时调整库存水位,并在低于最小库存水位后触发补货排产,确保库存水位紧随市场需求动态变化,补货频率也根据市场需求变化情况实时调整。
什么是生产补货周期?
生产补货周期就是从生产指令下达,到货物入库可以发出给客户的这段周期。其中,不同商品生产周期不同,需要结合具体生产工艺流程制定,但如果多种产品共用产线的话,则在需补货产品投产前,等待其它排队的产品生产完成,怎么计算等待周期是关键!
等待生产的场景十分复杂,这里介绍其中一种计算方法:假如某产线以一周为一个循环周期,即要求每周都要把所有的产品生产一遍,那么等待周期就是在这一周里,等待其他产品生产所需的时间。这里我们取最长的等待周期,即将其他所有的产品都生产完成需要的时间,将其他产品的月度计划平均划分到周,然后按产线生产效率计算出一周计划的用时,加和便得出了等待周期。
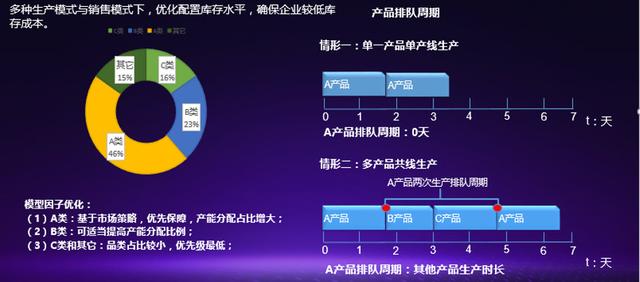
综合生产与等待周期、质检释放周期、转产换型周期、库存品质周期、经济批量等库存模型因子综合考虑,可以得出实际生产命令下达到发货给客户的生产补货周期。
基于多计划场景下的全价值链解决方案
至此,我们已完成了一个基于销售预测计划、以周为循环周期的生产模式的库存计划模型构建,尽管实际应用较多,但生产实际情况也是复杂多变,销售预测模型自然也多元,比如基于市场历史销售情况的大数据运算,计算各个SKU品种的销售概率分布等等,此处不再做展开。
库存模型在大宗快销品领域具有极强的适用性,适用于出货量大、较为均匀且客户需求周期短,而生产周期长的产品在具体应用上,不同行业属性、不同产品特点与生产销售模式,就需要根据实际情况,调整模型因子的各项配置,制定出适用于具体企业的合适的安全库存解决方案。
经过多年的发展,美云智数排程易APS累积了多行业龙头企业应用经验,可支持离散制造、流程制造等跨行业,多种计划模式、多种计划场景下的全价值链解决方案。