
文/杨操,慧眼自动化科技(广州)有限公司
在芯片制造业中绝大部分生产线已实现自动化,但芯片中的光隔离元件因本身体积小、精密度高,对其外观检测一直是行业痛点,仍需大量人工检测。针对上述问题,慧眼自动化开发了基于深度学习的光隔离元件外观检测解决方案。
客户要求
我们的客户(暂称A公司)是一家致力于光电材料、高精密光学元件、光纤器件和光网络功能模块等光电子产品的研发、生产和销售的公司。在“用户至上、质量第一”的理念下,A公司不断推出满足用户需求的新产品,并持续改进制造工艺,力图在实现高品质产品的同时,兼顾降本增效。
在A公司的光隔离元件生产线上,目前采用的产品外观检测方法依然是人工通过显微镜目视检测。需要检测的缺陷包括划痕、脏污、破损、尺寸异常等。由于光隔产品的尺寸基本在0.3~0.7mm之间,缺陷尺寸在0.04mm左右,并且产品易碎,因此目前的显微镜目视检测方法存在以下弊端:
(1)人工用镊子夹取产品,速度慢,因此检测效率较低;
(2)操作员易疲劳,不利于产品质量的严格控制;
(3)产品易碎,容易造成二次损伤;
(4)操作员人工目视,检测标准难以控制;
(5)人工成本巨大,平均一颗产品的检测成本高达1元。
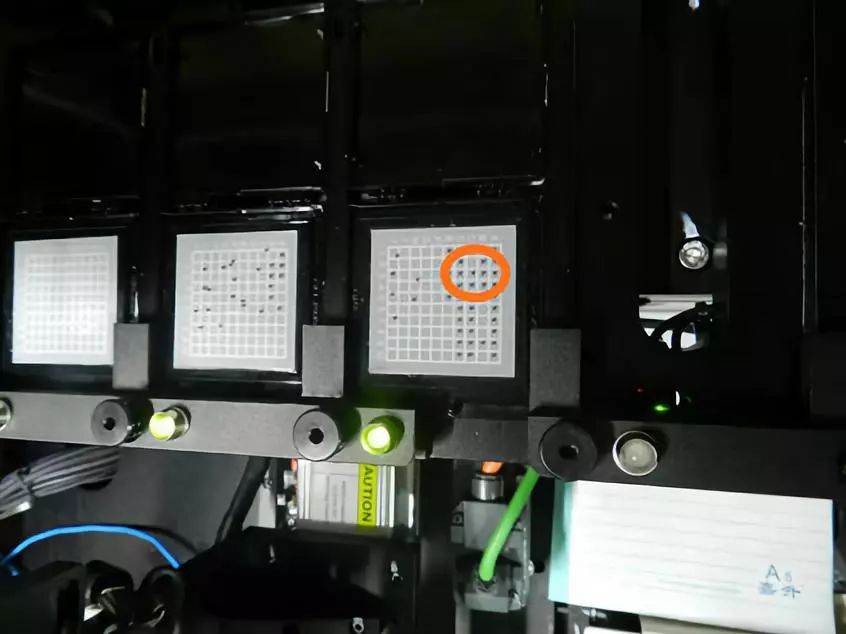
图1:被检测的光隔离元器件(红圈标识),体积非常小
设备结构及工作流程
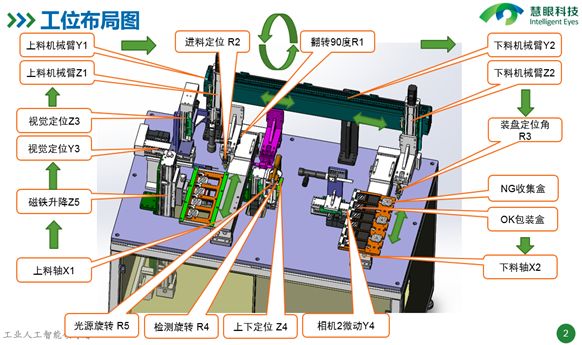
图2:慧眼科技的检测设备结构示意图
针对A客户的检测任务,慧眼科技开发的检测系统,硬件部署上分为上料、检测和下料三个工位(见图2)。
上料工位分为四个料仓,操作员用上游设备取出装载产品的载具,放入产品,每个载具可放入40颗产品。这个装载数量可以减少操作员上料的次数。在上料工位,有一个视觉定位系统,用于检测产品的尺寸,并获取产品坐标位置并发送给机械手。
机械手获取坐标位置后,吸取产品到检测工位。产品到达检测工位后,启动相机,从四个角度获取产品的图像,载入深度学习程序自动检测,然后将检测结果发送给PLC。PLC用于控制机械手,根据检测结果将产品放入不同的下料工位。
设备基本参数如下:
(1)兼容性:长0.45mm×宽0.45mm到长2mm×宽2mm
(2)检测效率:5s/PCS
(3)检测外观不良类型:点子、划痕、崩边、脱模、内裂
(4)漏检率:≤0.3%
(5)错检率:<10%
该高精度检测系统,能够实现对微观产品进行自动定位、吸取、上下料、外观检测,可以防止人工操作带来的二次损伤。
使用偏振相机取像,获得四个角度的图像,能够检测产品表面不同角度的划痕情况,提高检测覆盖率。这也是针对芯片行业中表面镜面产品的外观检测的创新应用。
深度学习的应用
在机器视觉应用中,外观检测一直是行业痛点。外观缺陷中的划痕、脏污、形态不一、大小不同、深浅和各种姿态都不同,很难用传统的视觉检测算法稳定检测。但是随着深度学习技术的发展,采用深度学习模式的外观检测程式,成为了外观检测的新方法。在A公司的这个案例中,我们也遇到了传统视觉算法难以解决的外观检测问题,我们的解决方案是采用深度学习搭配传统定位算法。
深度学习训练模式:
深度学习是一类模式分析方法的统称,就具体研究内容而言,主要涉及三类方法:
(1)基于卷积运算的神经网络系统,即卷积神经网络(CNN)。
(2)基于多层神经元的自编码神经网络,包括自编码(Auto encoder)以及近年来受到广泛关注的稀疏编码(Sparse Coding)。
(3)以多层自编码神经网络的方式进行预训练,进而结合鉴别信息进一步优化神经网络权值的深度置信网络(DBN)。
通过多层处理,逐渐将初始的“低层”特征表示转化为“高层”特征表示后,用“简单模型”即可完成复杂的分类等学习任务。由此可将深度学习理解为进行“特征学习”(feature learning)或“表示学习”(representation learning)。
以往在机器学习用于现实任务时,描述样本的特征通常需要由人类专家来设计,这称为“特征工程”(feature engineering)。众所周知,特征的好坏对泛化性能有至关重要的影响,人类专家设计出好特征也并非易事;特征学习(表征学习)则通过机器学习技术自身来产生好特征,这使机器学习向“全自动数据分析”又前进了一步。
近年来,研究人员也逐渐将这几类方法结合起来,如对原本是以“有监督学习为基础的”卷积神经网络,结合自编码神经网络进行无监督的预训练,进而利用鉴别信息微调网络参数形成的卷积深度置信网络。与传统的学习方法相比,深度学习方法预设了更多的模型参数,因此模型训练难度更大,根据统计学习的一般规律知道,模型参数越多,需要参与训练的数据量也越大。
20世纪八九十年代,由于计算机计算能力有限和相关技术的限制,可用于分析的数据量太小,深度学习在模式分析中并没有表现出优异的识别性能。自2006年Hinton等提出快速计算受限玻耳兹曼机(RBM)网络权值及偏差的CD-K算法后,RBM就成了增加神经网络深度的有力工具,导致后面使用广泛的DBN(由 Hinton等开发并已被微软等公司用于语音识别中)等深度网络的出现。与此同时,稀疏编码等由于能自动从数据中提取特征,也被应用于深度学习中。基于局部数据区域的卷积神经网络方法今年来也被大量研究。本案例中的具体实现方式如下:
(1)收集大量缺陷样品图像和OK样品图像
(2)人工标注缺陷位置、范围
(3)算法自动根据标注内容自动学习
(4)载入训练好的检测程式,嵌入传统视觉程序中
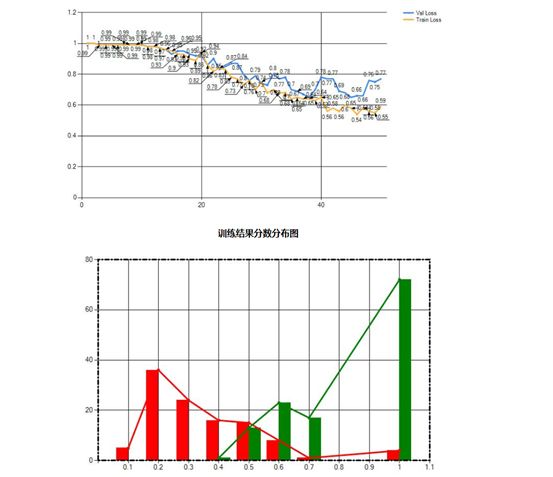
图3:模型训练结果统计图
人机交互界面
为了使检测过程可视化,设备加入了交互界面(见图4),界面中主要包括菜单选择、标记、显示数据库统计等。界面在设计上充分考虑了界面设置的易操作性和显示的直观性,方便操作人员学习和操作。

图4:交互界面示意图
总结
这套基于机器视觉技术的外观检测系统已成功投入到客户的生产流水线上使用。运行数据显示,该系统运行效率保持在6s/PCS,无漏检;误检率不超过0.005%。这套系统将原来的5~6个人工工位缩减到2个人工工位(上料和下料),一台设备可以替代一个外观检测小组。同时,该系统还解决了产品信息存储、追溯等问题。
本项目的成功开发,解决了客户人工成本高、误检率高的难题,并有效保证了产品质量,极大提升了生产效率,有效降低了客户的管理和生产成本。
End
近期活动
视觉系统设计用户单位,免费听会