一、项目背景
钢铁工业是能源消耗最大的产业部门之一,烧结矿是高炉炼铁的主要原料,烧结过程中的能源消耗占钢铁企业总能耗的10%左右,仅次于炼铁;在可供利用的余热中仅环冷机废气及烧结烟气的显热约占烧结全部热支出的30%以上,充分回收利用这些烧结余热,是烧结节能的重要途径及发展趋势,冶金烧结工序内废气温度分布示意图如图一所示。
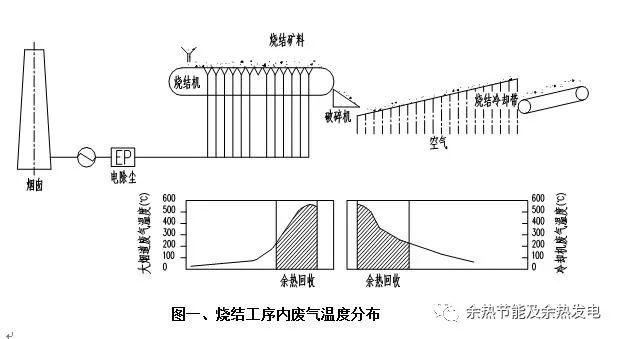
由图一所示,余热回收主要在烧结矿成品显热及烧结、冷却机的排气显热三个方面,热烧结矿显热和烟气显热占烧结过程热耗的50%以上,针对烧结机大烟道机尾区域热烟气及冷却机高温废气设置余热回收装置回收利用其余热,可大大地提高能源利用率,节约能源。
烧结机生产时,机尾区域大烟道烟气温度可达300~400℃。为保证烧结矿质量及输送设备运行安全,烧成的热烧结矿从烧结机尾部落下经破碎后,通过振动筛分后经溜槽落到冷却机传送带上,在溜槽部分热料矿温度达800℃以上,以辐射形式向外界散热,落到冷却带上料温很高。烧结冷却机上布置有冷却风罩,风罩内通过鼓风机使冷却风强制穿过料矿层,经料矿加热在风罩内冷却风温提高到350~450℃左右。
目前对烧结工序的余热利用大多限于烧结冷却机部分,并未对大烟道烟气余热进行回收。烧结冷却机的余热利用有两种方式:一类是热利用,即利用余热来产生热水或蒸汽以供暖、制冷、拌料用,或直接用于热风烧结等;另一类是动力利用,即将余热转换为电能或机械能。用于余热发电或带动透平机工作等。考虑到提高烧结工序节能量,减少产品单耗,本次余热发电方案对烧结、环冷排气两部分均进行余热回收。
二、案例说明
本项目为辽宁某钢铁集团公司300m2、360m2(分别简称为1#、2#烧结环冷机)烧结余热发电工程,烧结环冷机余热锅炉为双压锅炉,烧结机大烟道中也设置了热管式余热回收装置,其中生产出来的中压过热蒸汽与烧结环冷机余热回收装置所产的中压过热蒸汽会合作为主蒸汽送入双压补汽凝汽式汽轮机发电机组发电;低压蒸汽部分供自身除氧用外其余送至低压过热器过热,过热后送至补汽凝汽式汽轮机补汽口。
从环冷机来的高温烟气作为余热锅炉的工作介质,通过余热锅炉换热后降至120℃左右(方案二为135℃左右),然后通过循环风机再回到环冷机一段及二段底部冷却风箱。烧结机大烟道设置了热管式余热回收装置,大烟道出口烟气将降低20~30℃左右。
三、余热回收方案
3.1、烧结环冷机余热回收方案
按设备布置形式分为机上、机下两种;按照废气流程又分为烟气循环使用和烟气直排两种工艺形式,烧结系统的余热回收技术从其发展历程来看,经过了从机上布置到机下布置的过程。各种余热回收的优缺点总结如下:
机上布置:烟气直排技术
换热设备直接安装在烧结环冷机上部,高温烟气经除尘、换热后,直接排入大气,其优点是:设备直接安装在环冷机上部,可直接利用料矿的辐射热,且占地面积小、投资省、能耗抵、操作简单。缺点:受设备布置位置的限制,设备不能设置过大;烟气只能直排,不能最大限度的回收热量;回收效率低,热量回收有限;对环境有一定污染。
机下布置:烟气直排技术
废气直接排放,系统增设一台引风机作为克服余热回收系统阻力的动力源,废气经过除尘和余热回收后直接排放,原有环冷机下的鼓风机继续使用。
余热回收设备布置在烧结环冷机旁,高温烟气从烧结环冷机引出,经除尘、换热后,通过烟囱直接排向大气。其优点是:回收效率较高,较机上布置烟气直排方式回收热量多;能耗较低。缺点:占地面积大;一次投资较大;烟气直排,不能最大限度的回收热量;对环境有一定污染。
机下布置:烟气循环利用
实践证明,当冷却风温为50℃时废气温度提高15℃,冷却风温达120℃时,废气温度可提高45℃,通过烟气循环利用,提高了废气温度,有利于余热利用,且减少了粉尘的排放。
烟气循环利用系统需增设一台循环风机,循环风机提供克服料矿、余热回收系统的阻力,原环冷机下的鼓风机留做备用,实现废气的循环利用。余热回收设备布置在烧结环冷机旁,高温烟气从烧结环冷机引出,经除尘、换热后,烟气温度还有~140℃左右,增设烟气循环系统,可将该部分热量有效的利用起来,实现废气的循环利用。
优点:回收效率高,热量得到了充分利用;投资回收期短;烟气循环使用,有效的保护工作环境,减少对环境的污染。缺点:占地面积大;能耗较大;一次投资大。
上述各种余热回收方法各有利弊,应视建设条件的不同选用。对于本次项目改造,结合项目的实际情况,权衡经济效益、环保要求及安全生产等多种因素,300m2、360m2烧结环冷机系统采用将采用机上布置与机下布置烟气循环相结合的余热发电工艺技术。
·工艺技术成熟,充分利用了烧结工序中各段可利用的能量,最大限度的回收烟气余热,并将余热用于产汽或发电;
·设备布置合理,占地少,便于操作;
·减少了废渣、废气等气体的排放,切实有效地改善了环境;
·不消耗一次能源,经济效益不受燃料价格波动的影响;·采用高效、先进、结构合理的设备和可靠的材质;
·采用集散控制系统(DCS)对装置进行自动控制,实现在控制室的全CRT操作,影响到操作、安全等过程关键参数,均由计算机自动控制。
3.2、烧结大烟道余热回收方案 由于烧结大烟道机尾3~4各风箱部位废气存在温度高、含硫量大、露点温度高、含有大量矿物粉尘、废气温度随着工况在一定范围内波动、取热位置较为特殊等特点,以及热量移出后受再利用条件限制受等多种复杂因素的影响,因此给余热回收的工程设计带来了很大的难度。针对该烟气特点此次方案采用热管换热器。热管换热器插入大烟道内取热,由热管蒸汽发生器产生的饱和蒸汽经设置于环冷机上的过热器过热后与烧结环冷余热锅炉并网。
热管换热器具有对温度变化大的适应性和在换热过程中对热流密度的可调性,大幅度提高了工程的可靠性。热管式蒸汽发生器充分利用热管在热传导中的超导特性,来进一步降低废气排放温度,从而回收更多的热量,以满足该系统的长周期稳定运行要求,并达到降温、除尘、余热利用的目的。
四、项目基本参数及要求
4.1、设计参数
充分利用烟气余热本次共做了两套方案。
4.1.1、烟气参数(1#环冷机、2#环冷机参数相同,以1#为例)
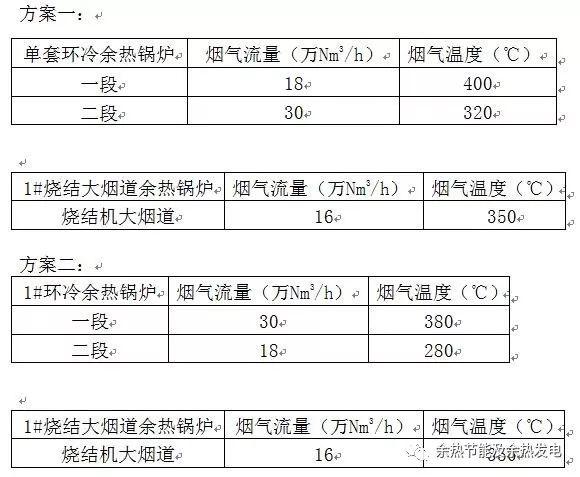
注:1、烟气量工况波动按-20%~+10%考虑,烟温按±20℃考虑。2、烟气成份:N2、O2、H2O,其中N2占78%,O2占21%,H2O占1%,烟气含灰量为1~3g/ Nm3。成分为铁矿石烧结熟料,粒径为100μm。
4.1.2、1#、2#烧结环冷余热锅炉及大烟道余热锅炉主要参数(1#、2#锅炉参数一致)
方案一: 表3. 烧结环冷余热锅炉参数(此为1#锅炉)
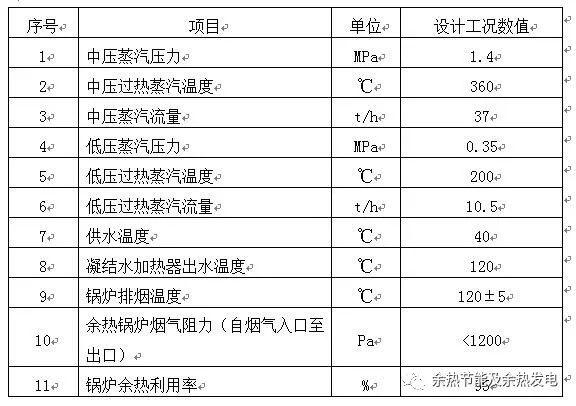
表4. 大烟道余热锅炉参数(此为1#锅炉)
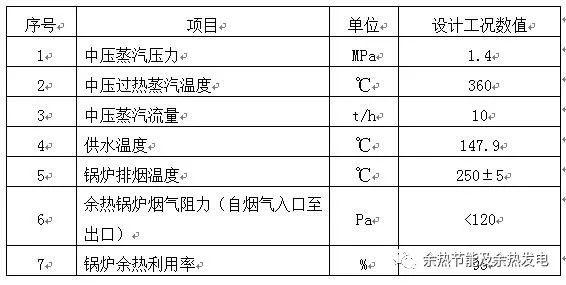
方案二 表5. 烧结环冷余热锅炉参数(此为1#锅炉)
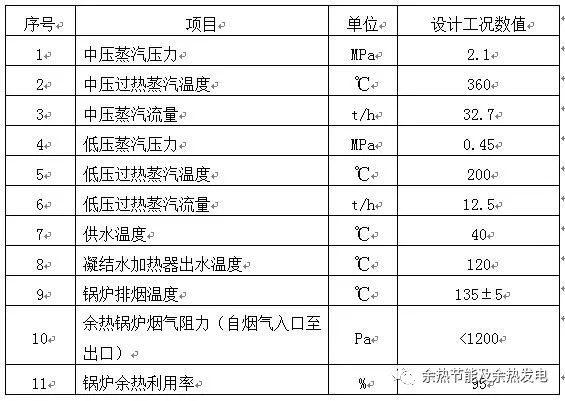
表6. 大烟道余热锅炉参数(此为1#锅炉)
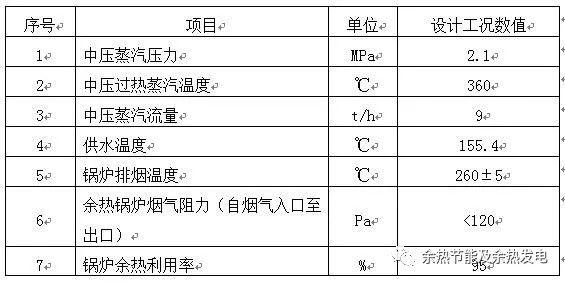
4.1.3、锅炉给水品质
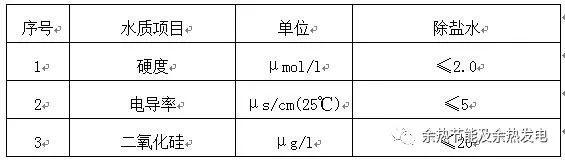
给水品质符合GB/T12145-2008火力发电机组及蒸汽动力设备水汽质量
4.1.4、电源
高压 10.5kV AC 50Hz
低压 380V/220V
直流电源: 24V DC
五、余热锅炉技术
余热锅炉是本次余热回收项目的关键设备之一,针对本项目的特点,集多年成功经验,余热锅炉设计分为中、低压两段复合型,具有对温度变化的高适应性、低温差传热的超导性和模块化分块维修的高机动性,采用模块化组合式设计的型式。组合式余热回收技术的应用充分发挥了翅片管式蒸汽发生器对温度变化的适应性和热管在热传导中的超导特性。
·烧结环冷机余热锅炉主要部件一:翅片管蒸汽发生器
蒸汽发生器设计为上下集箱翅片管型式,是一种新型的蒸汽发生装置,它采用高频焊接翅片管作为换热元件,通过翅片来强化传热,整套装置传热效率高,设备结构紧凑,热侧流体流动阻力小。其基本特点是汽包和产汽部分分离,水的受热和汽化在翅片管内完成,众多翅片管通过上下集箱组成一片,再通过联络管与汽包连接,这就使本套装置有别于一般上下锅筒结构的余热锅炉。产汽套管与汽包间用导管相连,管道可任意调整长度,现场布置灵活,设计计算时充分考虑到废气温度的大范围的变化特点,设置合理的换热强度范围,从而适应大温变工作状况,适应了复杂现场的要求。全套设备除给水系统外,无运转部件,运行可靠,操作维修方便。 全套设备除给水系统外,无运转部件,运行可靠;设备操作维修方便。
·大烟道余热锅炉主要部件二:热管式蒸汽发生器 随着废气的温度的降低,低温差范围的换热采用热管——热超导元件,提高热利用率。大烟道余热回收部分设置有分离套管式热管蒸汽发生器。
5.1、热管简介
热管蒸汽发生系统的核心部件是热管。热管是一种具有高传热性能的传热元件,它通过密闭真空管壳内工作介质的相变潜热来传递热量,因此,它具有传热能力大,传热速度快、效率高的特点。典型的重力热管如下图所示,在密闭的管内先抽成一定的负压,在此状态下充入少量工质。在热管的下端加热,工质吸收热量汽化为蒸汽。
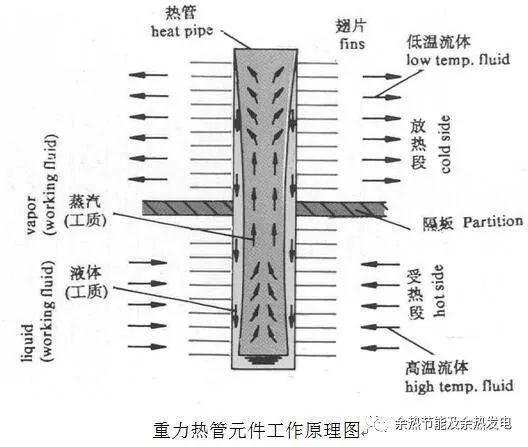
在微小的压差下,上升到热管上端,并向外界放出热量,且凝结为液体。冷凝液在重力的作用下,沿热管内壁返回到受热段,并再次受热汽化,如此循环往复,连续不断地将热量由一端传向另一端。由于是相变传热,因此热管内热阻很小,所以能以较小的温差获得较大的传热功率,且结构简单,具有单向导热的特点,特别是由于热管的特有机理,使冷热流体间的热交换均在管外进行,并可以方便地进行强化传热。
热管这种传热元件,可以单根使用,也可以组合使用,根据用户现场的条件,配以相应的流通结构组合成各种形式换热器,热管换热设备具有传热效率高、阻力损失小、结构紧凑、工作可靠和维护费用少等多种优点,它在空间技术、电子、冶金、动力、石油、化工等各种行业都得到了广泛的应用。
5.2、热管蒸汽发生器的基本结构及工作原理
热管蒸汽发生器是由若干根特殊的热管元件组合而成。其基本结构如下图所示。
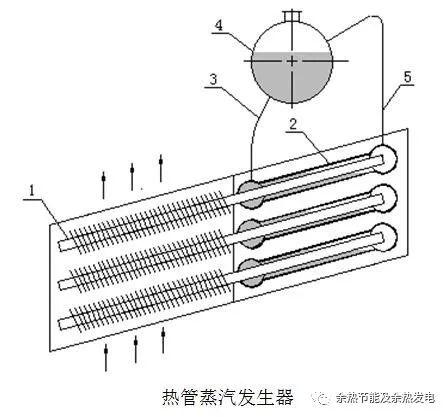
热管的受热段置于热流体风道内,热风横掠热管受热段,热管元件的放热段插在水—汽系统内。由于热管的存在使得该水—汽系统的受热及循环完全和热源分离而独立存在于热流体的风道之外,避免了水—汽系统受热流体的直接冲刷,汽水分离在汽包中完成,这就不同于一般的烟道式余热锅炉。它的工作原理是:
废气的热量由热管①传给水套②内的饱和水(饱和水由下降管③输入),并使其汽化,所产蒸汽(汽、水混合物)经蒸汽上升管⑤达到汽包④,经集中分离以后再经蒸汽主控阀输出,汽包内的水则由水预热器直接供给。这样由于热管不断将热量输入水套,通过外部汽—水管道的上升及下降完成基本的汽—水循环,达到将废气余热及料矿辐射热降温,并转化为蒸汽的目的。
5.3、余热锅炉的基本特点
由于采用热管作为传热元件,汽包和热管产汽套管部分分离,整个汽水系统的受热及循环完全和热流体隔离而独立存在于热流体烟道以外,这就使本系统有别于一般余热回收装置,布置更灵活,运行更安全;
设计时调节热管两端的传热面积可有效地调节和控制热管壁温,在一定的范围内防止换热管管壁温度过高或抬高管壁温度,采用一般材料即可防止换热管超温或防止低温酸露点腐蚀的发生;
设备中热管元件间相互独立,热流体与蒸汽发生区双重隔离互不影响,即使单根或数根热管损坏,也不影响系统正常运行,同时水、汽也不会由于热管破损而进入热流体;(这是与烟道式余热回收装置完全不同的地方)。
热量从废气转移到水,完全由热管元件完成,水-汽被间接加热;
热管热侧采用高频翅片焊强化传热,传热效率高,热侧阻力小,设备结构紧凑;
由于热管的单向导热性,热量的传输只能由废气传至水中,而不会由水汽中传到废气;
热量的输送过程不需任何外界动力,运行管理非常简单;
能最大限度回收热量,安全可靠运行,满足工艺要求。
5.4、余热锅炉设备结构特点
锅炉整体结构型式为立式、自然循环、双压余热锅炉结构,系统采用一体化除氧器。考虑到余热锅炉设备的运输和安装以及运行安全可靠性等因素,本次余热锅炉设计为模块化结构。1#、2#余热锅炉均为单列立式布置,设备上设有吹灰口、四周设有检修清灰通道,每套锅炉本体包括各换热设备模块、锅炉钢架与烟道过渡段、平台扶梯、中压锅筒一只、一体化除氧器一只;烟气由锅炉顶部进入,经过各受热面后由锅炉低部排出,设备底部设有灰斗及卸灰阀。
方案一:锅炉呈露天布置,锅炉钢结构按7度地震烈度设防。中压蒸汽过热器安装在环冷机一段余热回收口上方。烟气流经中压过热器换热后经烟道引至在机下,与二段来烟气混合后一起进入余热锅炉,考虑到安装、检修、膨胀的问题,沿气流方向依次经过中压蒸汽发生器、低压蒸汽过热器、中压给水预热器、低压蒸汽发生器及冷凝水加热器。
方案二:较方案一相比将中压蒸汽过热器放置在机下,一段烟气经过过热器及一级中压蒸发器后与二段烟气混合后一起进入后续余热回收装置。
5.4.1、换热设备模块
锅炉本体换热设备包括中压过热器,中、低压蒸发器,中压给水预热器及冷凝水加热器。设备由换热单元和壳体组成。
换热单元由换热元件和上下集箱组成,水平倾斜放置于烟道中,每个上下集箱之间的翅片管组成错列的对流管束。
壳体由型钢和钢板组成,具有一定的承压能力(不小于±5.8kPa),当循环风机出现瞬间最大抽力时,设备本体和烟道过渡段不出现永久变形。
各换热单元制成模块式整体出厂,方便现场安装。
5.4.2、各设备间由过渡段连接,过渡段设有膨胀节用来吸收设备热膨胀;设备侧及过渡段上设有检修观察人孔,同时预留吹灰器接口,接口尺寸由招标方提供。
5.4.3、锅筒
锅筒为横置式,布置于换热器钢架旁的副跨上。锅筒设计严格按锅炉标准和规范进行,内部设置有旋风分离器等,保证供汽质量符合GB12145-2008《火力发电机组及蒸汽动力设备水汽质量标准》。汽包容腔的大小在设计时考虑紧急状态下能提供20分钟运行所需的安全水量。
汽包材料满足GB713-2008,内部设置有旋风分离器、挡板、波形板、多孔板等汽水分离装置,进入汽包的汽水混合物,首先经挡板受阻后,进入旋风分离器,进行一次分离,然后进入波形板进行二次分离,为提高汽水品质,装有加药管和排污管,为防止下降管带汽在下水管入口处加装十字栅格。为汽水分离留有足够空间,汽包正常水位保持在中心线以下。
为保证机组的安全运行,其系统设计具备下列自动保护措施:
汽包超压和高低水位保护:当锅炉汽包压力超过允许值或汽包水位高于或低于极限水位时,按停机顺序,自动紧急停炉。
汽包高水位联锁:当锅炉汽包水位超过允许值时,自动开启汽包紧急放水电动阀(恢复到正常水位时,放水阀自动关闭)。
汽包就地水位计应采用双色玻璃水位计,在运行情况下就地水位计之间偏差应≤20mm,汽包水位平衡容器为双室平衡容器。
汽包筒体所有开口均加强处理,
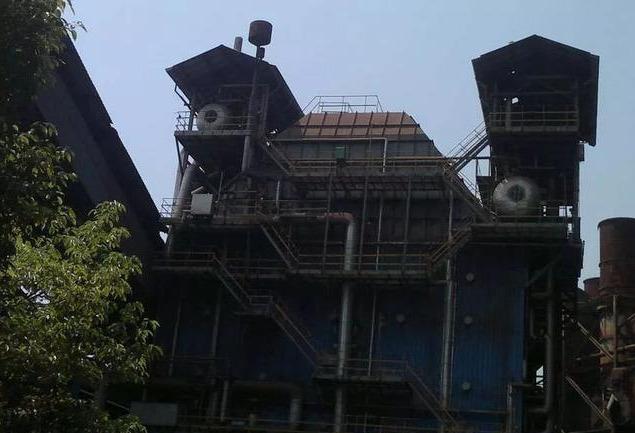
5.5、锅炉钢架
锅炉本体支撑采用多层单框架全钢结构,钢架采用H型钢制成,以将整套锅炉运行时所产生的允许载荷以及风载、地震等载荷平稳的传递至地面基础,确保锅炉在允许载荷范围内长期安全运行。
5.6、清灰装置
由于热侧废气中约1~3g/Nm3含尘,为受热面更好地进行换热,防止灰堵,各级受热面都设有激波吹灰器。 烧结环冷余热锅炉及烧结大烟道余热锅炉配置了激波吹灰器及振打器,此外锅炉设备采用下述组合办法进行清灰:
(1)在保证阻力损失允许的前提下尽量提高废气在换热面管间的流速,保证流体自清灰能力;
(2)根据废气含尘的性质选择合理的翅片间距,防止积灰搭桥;
(3)本体侧面开设侧门或人孔、底部设置灰斗,灰斗安息角60°,便于检修时进行人工清灰; (4)安装辅助的在线激波清灰器。激波清洁器具有非常好的清灰效果,且气量消耗少,操作简单。其清灰原理是:其原理是利用可燃气体如煤气、天然气、液化石油气、乙炔等,与空气经各自的管路调控后均匀混合,在特殊设计的燃烧室内产生爆燃、爆轰,经输出管上的喷口发射出脉冲激波。能量以高温、高速的气流伴随巨大的声强作用于换热器管束表面,通过波形扰动、气流冲刷、高温膨胀、声压震荡以及冲击振打等多种作用模式的综合作用,达到清除管束表面积灰的目的。
(5)设备底部设有灰斗及卸灰阀,灰斗角度≥60度。
5.7、除氧装置 锅炉给水采用一体化除氧。