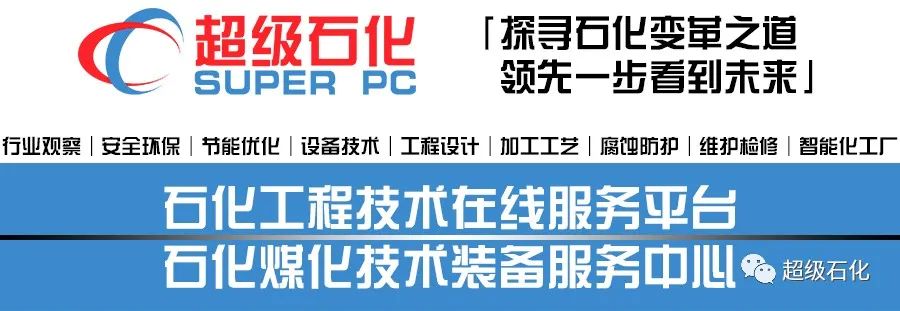
主要内容:基于异丁烯提纯反应精馏的特点,设计了塔顶蒸汽压缩式的热泵节能流程。利用Aspen Plus软件对全流程进行模拟,并提出了针对部分冷凝流程的热泵精馏模拟策略。从分析和技术经济的角度,全面对其进行能耗和经济性分析评价。案例研究结果表明:采用热泵节能技术的反应精馏过程,当压缩比为1.6时,能耗及总费用最低;与常规反应精馏过程相比,采用热泵节能技术后单位产品能耗降低87.5%,热力学效率提高32.7百分点,年操作费用下降64.4%,热泵投资回收期为1.5年。
关键词:热泵 反应精馏 模拟 能量分析 经济分析
基金项目:国家自然科学基金项目(21706198);湖北省技术创新专项重大项目(2017ACA179);煤转化与新型炭材料湖北省重点实验室开放基金项目(WKDM201712)。
热泵是一种广泛应用的节能技术[1]。根据工作方式划分,热泵精馏可以分为外部介质型、塔顶蒸汽压缩式和釜液节流式。其中塔顶蒸汽压缩式热泵精馏方式作为热耦合精馏技术中较为有效的节能手段,节能效果达20%~50%[2],已被广泛应用于近沸点物系的分离过程。此流程精馏塔塔顶蒸汽经压缩机压缩后升温升压,送入塔底再沸器提供热能。同时塔顶蒸汽部分或全部冷凝,突破传热过程中的温度“瓶颈”,具有跨夹点传热的特点,此构型适用于塔顶、塔底温差较小,压缩比及压缩功率较小的情况。
Annakou等[3]对丙烯精馏塔采用塔顶蒸汽压缩式的热泵精馏,年度总费用减少37%。李沐荣等[4]提出了带中间换热器的热泵精馏隔壁塔流程,以解决隔壁塔在分离宽沸程物系时出现的塔顶与塔底温差过高而不宜应用热泵精馏的问题。Felbab等[5]提供了一种快速评估方法,考察分离物系用于塔顶蒸汽压缩式热泵精馏的可行性,即在特定场合该工艺的热力学效率是否优于传统精馏方法。此外,塔顶直接蒸汽压缩式热泵工艺也可应用于其他特殊精馏,Kumar等[6]将塔顶直接蒸汽压缩式热泵应用于反应精馏,利用一股或多股被压缩后的塔顶蒸汽给不同塔板供热,新工艺在节能和经济性方面有很大提高。丁良辉等[7]基于外部反应精馏强化技术反应与分离更易优化操作的优势,提出将反应段与提馏段分开运行、反应段引入热泵的系统内部能量集成策略,并考察了其可能的最大的节能效果,减少年总成本47.9%。唐超等[8]提出了采取热泵精馏技术进行节能改造,并建立了异丁烷精馏的热泵精馏新工艺,能耗降低32.7%。
本研究以某石化企业C4抽余馏分的异丁烯提纯反应精馏塔为例,应用塔顶蒸汽压缩式热泵精馏技术,考察其对反应精馏的影响。根据异丁烯提纯反应精馏塔塔顶、塔釜传热温差小,跨夹点传热的特点,运用Aspen Plus流程模拟软件对基于异丁烯提纯反应精馏的热泵流程进行严格模拟,采用效率进行热力学评价,并通过单位产品能耗量化节能效果,从技术经济的角度分析其可行性。
1 热泵反应精馏模拟
1.1 模型的建立
异丁烯提纯工艺的原料为抽余C4馏分,其中异丁烯与1-丁烯的沸点极为接近,采用异构反应精馏法,利用丁烯的临氢骨架异构化反应,将1-丁烯转化为沸点较高的2-丁烯后,再通过普通精馏将两者分离。在Ni/Al2O3催化剂和微量氢气存在的条件下,会发生如下的一级液相反应[9]。
反应R1:t-C4H81-C4H8
反应R2:t-C4H8c-C4H8
反应R3:t-C4H8+H2n-C4H10
其中:反应R1是双键异构反应;反应R2是顺反异构反应;反应R3是加氢反应。
由于异丁烯提纯体系中反应精馏塔塔体温差较小,可采用热泵单塔能量集成技术,将塔顶蒸汽直接压缩提温加热塔底物料,设计如图1所示的热泵精馏流程。
图1 带有热泵的反应精馏流程
利用Aspen Plus流程模拟软件对基于异丁烯提纯反应精馏的热泵流程进行模拟[10],并提出一种针对塔顶有气相产品采出的部分冷凝的热泵精馏模拟策略。对于塔顶部分冷凝的精馏过程,模拟有气相产品采出的塔顶蒸汽压缩式热泵精馏流程时,除增加冷凝器将塔顶蒸汽冷凝,再经闪蒸罐外,添加1个辅助冷凝器,将液相物流温度降至入塔温度后作为塔顶回流。
1.2 物性选择及参数设定
反应精馏模拟的准确度与物性方法选择直接相关。对于丁烯异构反应精馏过程,本研究采用NRTL热力学方法,选用RADFRAC模块对异丁烯提纯过程进行稳态模拟计算。原料采用抽余C4,设进料量为15 t/h,进料热状态为泡点进料,进料温度为60 ℃,组成见表1[11],塔的操作参数见表2。
反应R1~反应R3均为一级反应,反应速率常数(R)和表现活化能(Ea)见表3[11]。
表1 进料组成
表2 反应精馏塔操作参数
表3 反应速率常数和活化能
1.3 模拟结果
将常规反应精馏与热泵反应精馏工艺进行对比,其参数见表4。
表4 常规反应精馏与热泵反应精馏工艺参数对比
1.4 压缩比分析
热泵精馏具有跨夹点传热的特点,适用于塔顶、塔底温差较小,压缩比较小的场合。压缩比对精馏塔能耗有显著影响。基于模拟结果,探究压缩比对压缩机功率、换热器费用及流程总费用的影响,分别如图2和图3所示。由图2可见,随着压缩机的压缩比增大,压缩机功率增大。经压缩的塔顶物流与塔釜物流之间的传热温差增大,换热器面积减小,换热器设备费用降低,但流程总费用仍随压缩比增大而增加,如图3所示。确定适宜的压缩比为1.6。
图2 压缩机功率与压缩比的关系
图3 换热器费用及总费用与压缩比的关系
2 用能分析
2.1 能量衡算
加入热泵后的流程是在原流程的基础上降低原冷凝器的热负荷,并增加了1个辅助冷凝器,冷却负荷QC=2 387.1 kW,再沸器热负荷Qr=0。增加了1个压缩机,假定效率为95%,压缩机的净功率为1 368.3 kW,实际功率为1 440.3 kW。压缩机对系统输入的能量QW=1 368.3 kW。采用热泵的反应精馏过程的C4抽余馏分进料位置、塔顶产品和塔底产品的流量及热力学主要参数见表5。
表5 采用热泵的反应精馏过程的部分参数
对采用热泵的反应精馏过程进行能量衡算,满足ΔH=0。
(HC4+HH2+QC+Qr+QW)
(1)
式中:ΔH为焓变,kW;HC4,HH2,HD,HW分别为C4、H2、塔顶产品和塔底产品的焓值,kW。
2.2
衡算[12]
有效能的变化(ΔB)为:
(2)
对于净功消耗(W净),需要以外界加热和冷却介质的操作温度进行计算,见式(3),热力学效率见式(4)。
(3)
(4)
式中:T0为环境温度,一般取298 K;TC1为冷凝器冷却介质进口温度,K;TC2为辅助冷凝器冷却介质进口温度,K;TR为再沸器加热介质进口温度,K;QC1为冷凝器负荷,kW;QC2为辅助冷凝器负荷,kW;η为热力学效率,%。
2种反应精馏过程的热力学计算结果见表6。由表6可见,与常规反应精馏过程相比,采用热泵的反应精馏过程的净功消耗减少,热力学效率提高32.7百分点。
表6 2种反应精馏过程的热力学计算结果
2.3 能耗分析及比较
表7为2种反应精馏过程的公用工程能耗(以异丁烯产量计)对比。由表7可见,常规反应精馏过程的能耗为15 436.74 MJ/t,采用热泵的反应精馏过程的能耗为1 933.25 MJ/t,比常规反应精馏过程下降了87.5%。
表7 2种反应精馏过程的能耗 MJ/t
3 经济性分析
投资回收期是反映项目财务上投资回收能力的重要静态指标,是以项目的净收益抵偿全部投资所需要的时间,计算式如下[13-14]:
(5)
式中:TAC为年度总费用,万元;OC为年操作费用,万元;CC为总设备投资,万元;θ为投资回收期,a。装置的年开工时间按8 000 h计,电价按0.8元/(kW·h)计,0.35 MPa低压蒸汽按120元/t计,循环冷却水按0.3元/t计。表8为采用热泵的反应精馏与常规反应精馏过程的操作费用对比。
表8 2种反应精馏过程的操作费用 万元/a
从表8可以看出,常规反应精馏过程的年操作费用为2 870.6万元,采用热泵的反应精馏过程的年操作费用为1 020.6万元,比常规反应精馏过程减少了1 850.0万元,下降了64.4%。由于新流程增加了压缩机、换热器以及闪蒸罐,需增加一定的设备投资,以下为设备费用估算。
(1) 压缩机设备费用的估算式为[15]:
(6)
式中:CPC为压缩机费用,$;QCQMP为压缩机功率,22
(2) 换热器设备费用的估算式为[15]:
(7)
式中:HEC为换热器设备费用,$;Q为换热器负荷,kW;U为换热器传热系数,kW/(m2·K);Δtm为对数平均温差,K;C′为换热器类型因子,取值见表9[15]。
表9 换热器类型因子C′的取值
(3) 对于气液分离器等非标设备,采用下式计算设备费用[15]:
VC=MC+NC=2.5ab
(8)
式中:VC为设备价格,万元;MC为材料总价格,万元;NC为设备加工费用,万元;a为材料价格,万元/t;b为设备质量,t。
采用热泵的反应精馏工艺流程与常规反应精馏工艺流程相比,增加了1台压缩机、2台小型换热器以及2个气液分离器。压缩机的压缩比为1.6,功率为1 440 kW,由式(6)估算出压缩机费用为2 704.5万元。冷凝器的负荷为677.9 kW,对数平均温差为32.3 K;辅助冷凝器的负荷为1 709.2 kW,对数平均温差为24.5 K。由于循环冷却水在管内流动,取换热器传热系数为6 kW/(m2·K)。冷却器换热面积为3.5 m2,辅助冷凝器换热面积为11.6 m2。根据工艺流程及公用工程数据,由式(7)计算得到换热器总费用为39万元。气液分离器等其他费用按非标准费用计算,总费用为84万元。反应精馏流程增加热泵后,设备费用增加了2 827.5万元。将常规反应精馏过程的年操作费用作为年度总费用,将采用热泵的反应精馏过程的年操作费用作为年操作费用,采用热泵技术需增加的设备费用作为总设备费用,依式(5)计算得到热泵投资回收期为1.5年。
4 结 论
采用Aspen Plus模拟软件对异丁烯提纯的反应精馏及采用塔顶蒸汽压缩式热泵精馏的过程进行了严格模拟。采用热泵节能技术的反应精馏过程,在压缩比为1.6时,能耗以及总费用最低。在保证分离精度的前提下,采用热泵精馏技术的反应精馏过程会显著降低换热器的热负荷,从而降低公用工程用量,其单位能耗降低约87.5%,热力学效率提升,具有良好的节能效果。相较于常规反应精馏过程,采用热泵节能技术后设备费用增加2 827.5万元,年操作费用降低1 850.0万元,热泵的投资回收期为1.5年。(作者:钱诗卉,邓 一,姜佳文,颜家保,雷杨 武汉科技大学化学与化工学院 煤转化与新型炭材料湖北省重点实验室)
咚咚咚!重要会议推荐:由中国化工学会主办,中国石油信息管理部、中国石化信息管理部、中国海油信息管理部、中化集团信息管理部、延长石油科技与信息化管理部联合主办的“2020年(第二届)中国智慧炼化高峰论坛”定于2020年9月2-4日在浙江宁波举办,届时两院院士及400位专业人士将深入探讨以人工智能、 大数据为代表的新一代信息技术在炼化行业“ 智慧炼化” 建设中的应用方法、 价值、 途径和解决方案。如有意向协办、宣讲、展示及参会,欢迎勾搭马先生 15101023809(微信),期待来电狂响么么哒!(另外由中国化工学会主办的“ 2020年中国石油化工设备检维修技术大会”,定于9月23-25日在南京举办。还有少许发言和展示名额,有意参加请尽快联系!)
感谢作者的辛勤付出和贡献!本文引自石油炼制与化工,超级石化整理发布,供参考了解,转载请注明出处。本文如果对您有帮助,请点击下方在看,留言交流!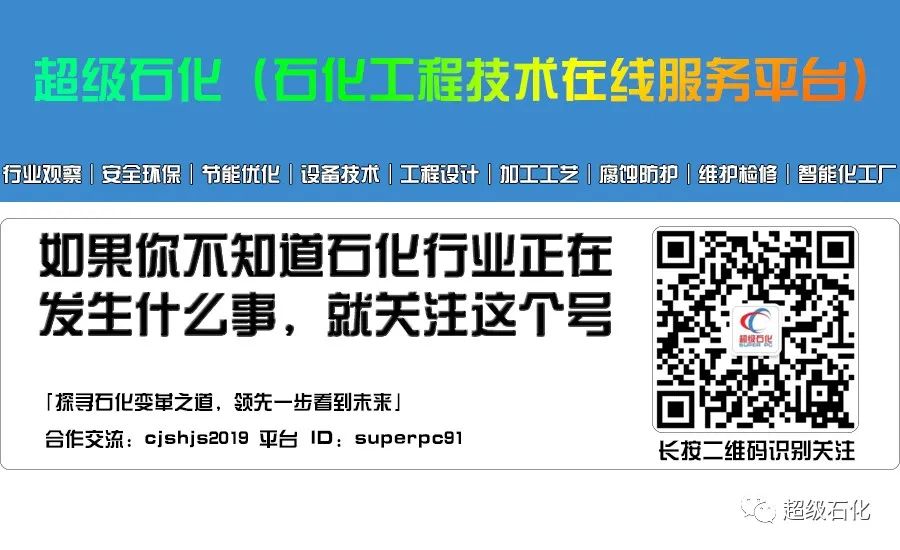