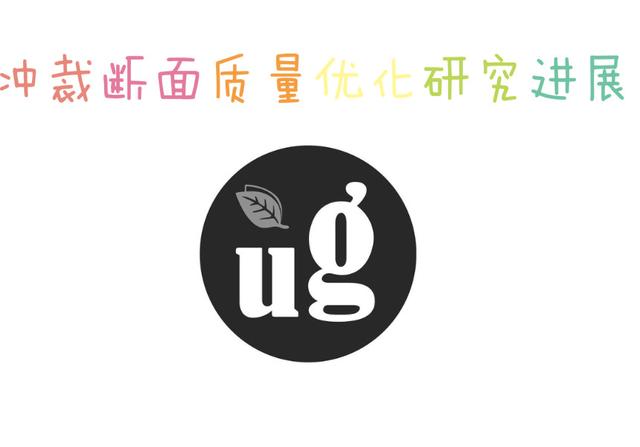
★交流讨论UG汽车模具设计遇到的问题★
★如果对模具设计有兴趣的话可以来的我的社群:785043381★
冲裁是借助冲模和压力机使金属材料产生塑性变形而分离,最终得到翘曲变形较小、互换性较好的冲压件的一种加工方式。冲裁过程中,模具零件需反复使用,将导致其磨损程度越来越严重,造成冲裁间隙的变化,最终降低冲裁件的精度及缩短模具的使用寿命。尤其是随着汽车、航空航天、造船等制造业的迅猛发展以及对冲裁零件高品质、高效益、低能耗的迫切需求,研究冲裁工艺参数对冲裁断面质量的影响,并提出优化冲裁工艺参数的方法至关重要。
现从冲裁过程考虑,介绍近几年学者在多种工艺参数对冲裁断面质量的影响方面开展的研究,并考虑工艺参数的耦合效应,对冲裁工艺参数组合优化方法做出的研究进行综述。
1
工艺参数对冲裁断面质量的影响
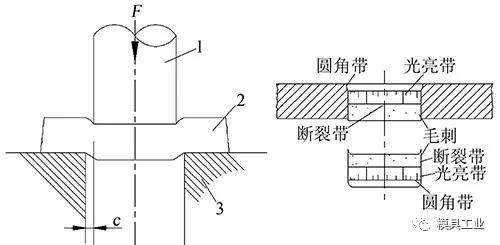
图1 冲裁件断面
1.凸模 2.板料 3.凹模
冲裁过程中冲裁变形区主要承受剪切作用,此外还受到弯曲、挤压、拉深等作用,应力应变状态较复杂。一般冲裁后,冲裁件的断面由四部分构成:圆角带、光亮带、断裂带和毛刺,如图1所示。断面质量主要受冲裁速度、冲裁间隙、模具零件刃口圆角半径、材料厚度和压边力等参数影响,目前许多学者对优化这些工艺参数做了研究。
冲裁速度的提高虽然会提高生产效率,但由于温度效应的存在,会对金属的塑性性能产生不同程度的影响。如果冲裁速度过快,模具零件的磨损会加快,影响工件的冲裁断面质量。
| 赵中华等通过建立物理模型和有限元模型进行模拟,确定合适的断裂准则和断裂因子,分析冲裁件在不同冲压速度下的光亮带宽度和毛刺高度,发现对于H1F60CS压力机,断面质量最好的冲裁速度为压力机最高冲裁速度的20%左右,速度继续下降时,断面质量下降,在分析规律的同时得出较为准确的冲裁速度数据。
| 刘明等通过Deform数值模拟,研究采用不同的冲裁速度时,其他因素对冲裁断面质量的影响,结果表明:冲裁速度在小于1000spm时,冲裁间隙、凸凹模粗糙度及刃口圆角较小时,断面质量较好;而冲裁速度超过1000spm时,冲裁速度是导致断面质量的主要因素,因为冲裁速度越快,剪切区内温升也越快,会引起模具零件材料和断面的温度软化效应。
冲裁间隙会对工件的断面质量及模具零件磨损产生显著影响。冲裁间隙较小时,会使工件与模具零件之间接触摩擦严重,加剧模具零件磨损;冲裁间隙过大时,冲压后的工件会产生较大的毛刺,对断面质量产生影响,此外冲裁间隙也是影响模具使用寿命的重要因素。
| 吴小蓉等以紫铜板为研究对象,运用ANSYS13.0有限元软件进行模拟仿真,得出采用不同冲裁间隙的情况下,冲裁断面质量的变化规律,结果表明:冲裁间隙是影响冲裁件横截面的质量主要因素。冲裁间隙不合理,容易产生细长尖锐的条状毛刺,因此需要设置合理的冲裁间隙保证断面质量。
| 郑海涛等通过改变凸模得到不同的冲裁间隙进行冲裁试验,随着冲裁过程的进行冲裁力不断变化,并测量光亮带宽度,拟合冲裁力与冲裁间隙和光亮带宽度之间的曲线,得出对厚度为6mm的T2紫铜进行冲孔时,最优冲裁间隙在16.67%料厚左右,此时冲裁断面较为光滑平直,且毛刺较少。
| R HAMBLI等采用Lemaitre损伤模型描述了板料的裂纹扩展过程,通过对冲裁过程的研究,不仅发现冲裁间隙对冲裁断面质量的影响规律,同时提出了优化冲裁间隙的方法,使预测包括损伤和断裂效应在内的最优间隙成为可能,提出的优化间隙算法最大限度地减小了冲模中裂纹萌生点连线角度与裂纹萌生方向夹角的差值。
模具零件刃口圆角大小影响刃口附近材料变形区的应力集中程度与材料的流动状况,因此选择适当的圆角,在工件端面及侧面的材料没有达到板料断裂极限值时,刃口前端材料发生断裂,进而抑制裂纹的产生与发展,此外模具零件刃口形状和凸模参数的不同也影响冲裁断面质量。
| 任莉新针对不同模具零件刃口形状的厚板冲裁进行了模拟,得出结论为模具零件刃口形状对冲裁力有影响,阶梯形刃口所需冲裁力较小,波浪形刃口冲裁断面质量较高,用平刃和波浪形刃口冲裁,板料的力学规律具有整体一致性。
| LUO S Y研究了不同外径、凸双剪角度、凸模长度和经表面处理的较大厚度圆形钢板凸模的冲孔工艺,结果表明:当使用经过表面处理的20°凸双剪角度的凸模时,冲孔的平直度和粗糙度更好,使用TiC涂层或研磨处理的凸模使用寿命更长。
材料厚度与冲压变形成正比关系,冲裁过程中,冲裁件的尺寸精度会受回弹的影响,薄料的回弹量大于厚料,薄料的冲裁间隙相对于厚料更小,冲裁断面与表面较垂直,厚料由于冲裁间隙较大,冲裁断面有斜度且粗糙不平。总体而言冲裁件的尺寸精度随着材料厚度的增加而降低。
| R HAMBLI通过试验研究了冲裁间隙和金属板料厚度之间的相互作用对冲裁力演变、剪切轮廓的几何形状和模具零件的磨损状态影响,结果表明,冲裁间隙与金属板厚度之间的比值减小,会引起冲裁力和模具零件磨损量增大。
| N HATANAKA等研究了材料硬度对于冲裁过程的影响,通过进行金属板料冲裁过程的数值模拟,模拟结果表明:随着凸模与工件间的间隙以及金属板料的加工硬化指数的增加,翻边长度增加;随着二者的减小,光亮带长度增加,毛刺高度增加,提出了一种根据间隙和加工硬化指数预测光亮带长度值的常规方法。
冲压过程中,经常需要调整压边力来提高冲裁件的断面质量,通过调节压边力,可以使摩擦阻力发生改变,增大板料内部的拉应力,控制材料流动,能避免工件边部或者凸缘起皱,如果压应力过大,工件也会产生裂纹以及模具零件发生磨损。
| 岳学虎等通过Deform3D软件研究了不同压力作用下的冲裁过程中压边力对断面质量的影响,得到冲裁力行程曲线和冲裁剪切断面图,通过MATLAB拟合得知,压边力较小时,圆角带的锥度、宽度、长度和毛刺高度随之增大而减小,当压边力超过某一临界值时,随其增大而增大,因此选用合适的压边力有助于提高断面质量。谢晖等运用板料拉伸、压缩失稳理论并结合有限元模拟,提出新的起皱临界应力法,由压力修正公式可以优化压边力,防止板料拉裂和起皱。
冲裁速度、冲裁间隙、模具零件刃口圆角半径、材料厚度和压边力等都会对工件断面质量造成影响,仅依靠单因素分析对单一工艺参数优化,虽可以改善断面质量,但效果并不显著。鉴于冲裁过程较为复杂,影响断面质量的参数难免存在耦合作用,因此需要考虑工艺参数间的相关性,进行工艺参数组合优化,找出最优组合以提高断面质量。
2
工艺参数组合优化方法
工艺参数组合优化可以改善单因素分析法的缺点,考虑各参数间的相互影响,使优化结果更准确,与实际生产更贴合,提高工作效率和减少模拟的时间,现主要介绍正交试验法、响应曲面法、BP神经网络与遗传算法以及灰色关联分析法。
01
正交试验法
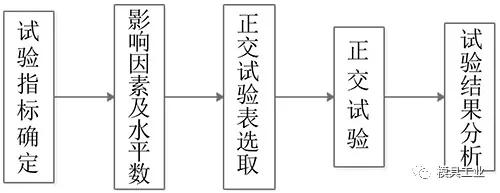
图2 正交试验法步骤
正交试验法是利用正交表、基于多因素多水平试验的一种数理统计方法,一般包括5个步骤,即试验指标的确定、影响因素及其水平数、正交试验表的选取、正交试验、试验结果分析,如图2所示。
| 周旻珺以S形帽形钢为研究对象,通过将正交试验法与Deform数值模拟相结合,分析压边力、摩擦系数、冲压速度对冲压件最小厚度和回弹量的影响,构建3因素5水平的正交表,进行较少次数的模拟试验后,通过最小厚度和回弹量的方差分析,得到3个影响因素对二者的影响程度顺序并获得最优工艺参数组合。
| 臧其其等运用Dynaform软件对轿车铝合金底板梁的拉深成形进行模拟分析,研究压边力、摩擦系数、冲压速度和凸、凹模间隙对底板梁成形的影响规律,赋予4个参数合适的水平,建立正交表,以最大减薄率和最大增厚率为目标变量,进行各组数据的模拟仿真。利用综合评分法,将多目标优化转换为单目标优化,分别对最大减薄率和最大增厚率进行评分,并将总和作为最终得分,在考虑极差顺序并综合评分结果的情况下,得到最优参数组合。正交试验法相较于单因素分析法,不仅试验次数少,缩短试验周期,而且还能分析影响因素的主次顺序。
02
响应曲面法
响应曲面法结合数学方法和统计方法,通过进行响应输出和相应影响因素之间的函数关系拟合,将每个影响因素对系统响应值进行优化,得到使响应变量达到最优的一组影响参数组合。
| 孙静利用响应曲面法构造了一个函数表达式,该表达式由自变量冲裁速度、冲裁间隙、模具零件刃口圆角半径、因变量预减振钢片冲裁断面光亮带宽度等组成,经检验满足误差范围后,运用该函数表达式分析工艺参数对光亮带宽度的交互式影响,并进行影响程度排序,得到最优的冲裁工艺参数组合。
| 刘静等采用台阶式凸模进行冲裁模拟试验,在一系列参数中利用2水平试验筛选,对影响不明显的因素和断面率进行筛选,随后利用响应曲面法构建预测模型,并结合遗传算法进行修正,最后得到冲裁间隙C=0.036mm、台阶高度H=0.1mm、台阶宽度W=0.5mm的最优工艺参数组合,与试验值一致性较好,表明模型具有较高的精度。
| 刘奎武等针对C75S高强度弹簧钢,利用响应曲面法构建了工艺参数与模具零件的最大磨损深度之间的响应曲面模型,得出参数的交互影响顺序及最优的冲裁工艺方案,结合实际试验,利用毛刺高度替代模具零件磨损量,得出实际值与模型计算间的误差为14.19%。
上述方法克服了线性回归的大量数据要求及计算时间长的缺点,克服了正交试验法不能给出全部区域上寻找参数最优组合的缺点,能规避回归稀疏的问题。但由于工艺参数与目标变量之间的函数关系式较为复杂,应用一般的数学表达式容易造成较大误差。
03
BP神经网络加遗传算法
BP神经网络具有非线性函数逼近的功能,通过使用大量现有数据训练,建立符合因变量与自变量之间函数关系的网络,预测未知量,与运用有限元模拟仿真软件相比,可以缩短求解时间,降低冲裁试验的成本。将影响因素作为输入,将目标变量作为输出,将70%的数据用于训练,30%的数据用于预测,构建满足影响因素与目标变量之间的隐形函数关系式,可计算待求数据组的结果,结构如图3所示。
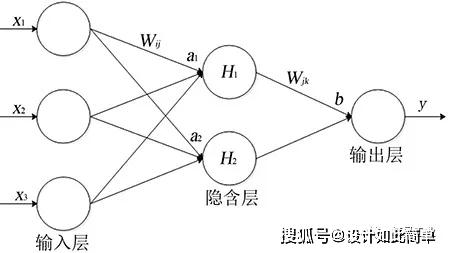
图3 BP神经网络结构
遗传算法是以自然界生物的遗传机制为基础模拟种群的进化过程,并具有能够并行随机搜索的优化方法。这种方法遵循自然界优胜劣汰和适者生存的原则,在编码群体中将优化参数引入,随后在所选择的适应度函数的基础上通过遗传中的选择交叉和变异进行筛选,将适应度好的个体留下,并淘汰适应度差的个体。随后经过几代进化,获得继承上一代群体的信息并优于上一代群体的新群体,重复该循环,直到满足条件为止。遗传算法的优点在于能跳出局部最优解,进行全局搜索的能力较强,步骤如图4所示。
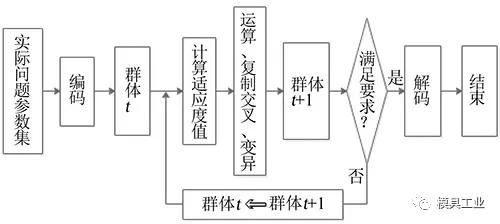
图4 遗传算法流程
| 黄菊花等以方形空心件为研究对象,将坯料内圆角半径和内孔尺寸2个影响因素进行参数化处理,运用有限元软件进行仿真模拟得到足够多的数据,实现了批量处理,节约了用户时间。然后利用此数据构建BP神经网络,得到2个影响因素与目标变量翻边高度之间的映射关系。在采用适应值评价函数的基础上,利用遗传算法进行多参数组合优化,最终获得工艺参数的最优组合。
| 龙仕彰以类U形件为研究对象对冲压成形中的回弹问题进行研究,将材料性能、冲压工艺和回弹角反映的关键型面尺寸作为试验的工艺参数,运用正交试验法进行数值模拟,得到的数据分为人工神经网络的训练及验证数据,训练得到的神经网络作为遗传算法的适应度函数,进行并行搜索,最终得到最优工艺参数组合。
构建BP神经网络需要大量的数据,但是由于时间和经济的原因,进行的次数较少,存在较大的预测误差,此外遗传算法容易发生早熟收敛,表现为群体中的所有个体之间有较高的相似度,使进化缓慢甚至终止,不一定能找出最优值和最优参数组合。
04
灰色关联分析法
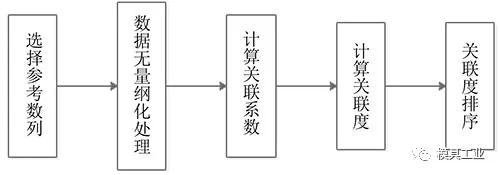
图5 灰色关联分析法步骤
灰色关联分析法是在分析因素之间发展趋势相似程度或相异程度的基础上,衡量因素间关联程度的方法,这种方法提供了一个系统发展变化态势量化的度量,完成相关统计数据的几何关系的比较,然后获得参考数列和每个比较数列之间的灰色关联度。比较数列与参考数列相关性越大,比较数列的发展方向和速率越接近参考数列,二者关系越紧密,步骤如图5所示。
| 陆林以车身前翼子板为研究对象,进行拉深成形仿真试验,将工件的最大减薄率和最大增厚率的最小值作为参考序列,运用灰色关联分析法计算各个工艺参数与优化的单目标之间的关联度系数、多目标函数关联度及参数对目标质量平均关联度,全面衡量各个参数对工件成形质量的影响,确定最优参数组合方案。
灰色关联分析方法对样本容量的要求简单,可应用于不规则数据,减少信息不对称造成的损失,并适合动态历程分析,此外量化结果与定性分析结果一致,但确定各项指标最优值具有较强的主观性是此方法的缺点。