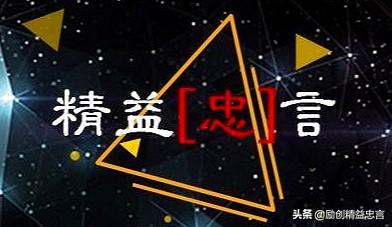
效率提升的利器
工业工程IE作为一门学科诞生于美国,却首先在日本得到了最大程度的践行与推广,成为了丰田生产方式TPS及精益制造LP的核心
现场IE中的4大核心(工程分析、动作分析、时间分析、布局分析)仍是所有IE的入门工具,被笔者称为“基础IE”,在人类的制造活动中至今仍然能够得到广泛的运用,成为提升工程效率、消除流程浪费的利器。被大野耐一先生称为“干毛巾中挤出水来”!
IE本身也在自我发展,衍生了众多的分支,在当今工业4.0、智能制造的浪潮中更是与高科技及其他的管理理论相辅相成,产生了更大、更深远的影响,被笔者称为“三度修炼”(高度、广度、深度)。仅从IE在企业中的实践程度上看,可以将IE区分为为三段境界而不断提升与深入,从而为企业的降本增效生存之道提供坚实的视角及实战工具
初级IE:基础IE改善
中级IE:制造方式变革
高级IE:全流程精益革新
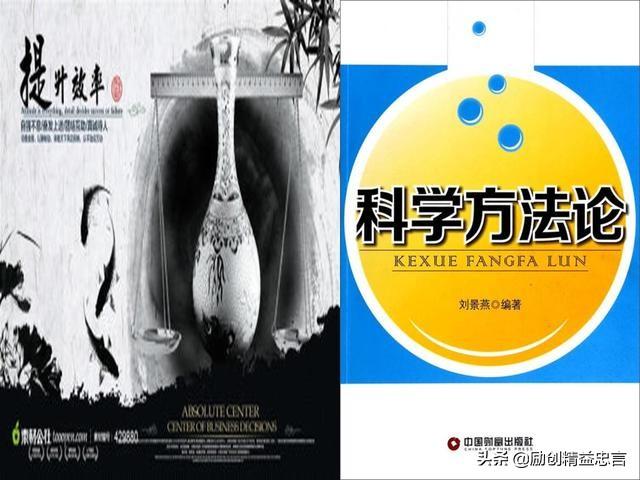
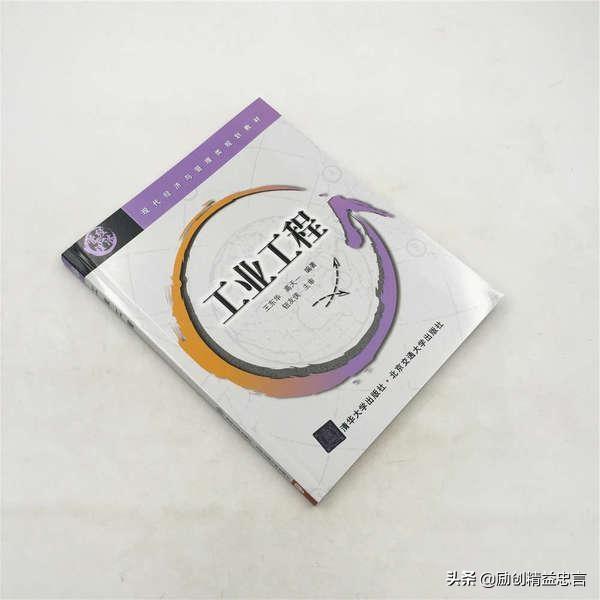
【IE简史】
一般认为泰勒(Frederick W.Taylor 1856~1915)和吉尔布雷斯(Frank B.Gilbreth 1868~1924)是IE的开山鼻祖。泰勒和吉尔布雷斯都是通过研究劳动者的作业方式,以扎实的资料为依据进行分析,而不是依赖直觉,进而提高生产效率。不过,两人的侧重点有所不同,泰勒偏重于“作业测定”(Work Measurement简称WM),吉尔布雷斯则以“方法改善”(Method Engineering简称ME)的始祖自居

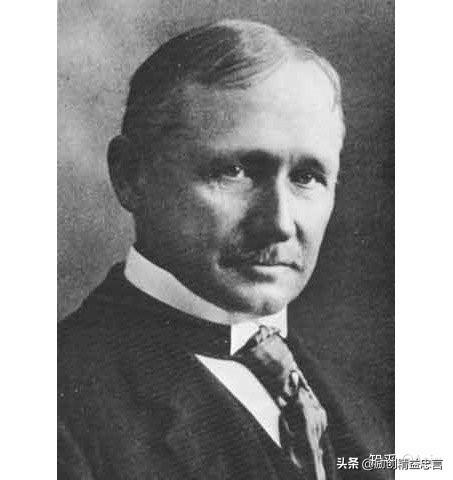
IE就是工业工程 ,即 INDUSTRIAL ENGINEERING。工业工程是对人员,物料,设备,能源和信息所组成的集体系统进行设计,改善和设置的一门学科,它综合运用数学,物理学和社会科学方面的专门知识和技术,以及工程分析和设计的原理与方法把技术和管理有机的结合起来,研究如何使生产要素组成更高效运行的系统,从而实现提高生产率的目标。IE的核心就是消除浪费、降低成本,提高生产质量和生产效率
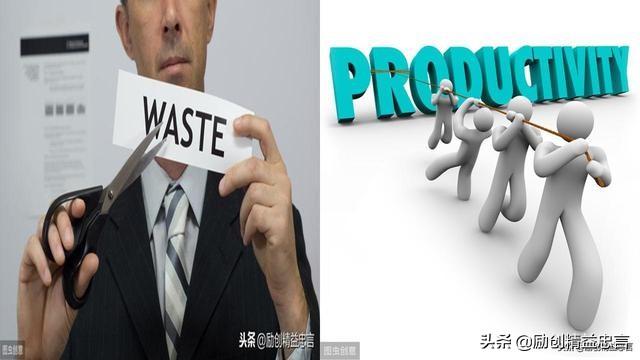
何为浪费?何为高效率?众多企业的管理者往往存在着片面、甚至错误的认知,将高效率定义为:动作飞快、争分夺秒、永不休息等。其实这是一种肤浅的形式主义,而忽略了对于作业方法合理性、流程整体的优化性、流程性浪费与无用功的深入研究,因此将导致“瞎干、白干、盲干”的低效作业
【PE与IE的视角差异】
PE是Production Engineering,它侧重于研究产品实现流程的工艺路径与品质保障手段
IE则完全不同,它侧重于研究任务完成中的“资源投入”而不是“工艺路径”,比如:标准工时、工作浪费、WIP、LT与时间利用率、生产单元平衡、单件流等等。一切过多的资源消耗都被认为是“浪费”特别是“隐形浪费“。按照大野耐一的说法:干毛巾中挤出水来!
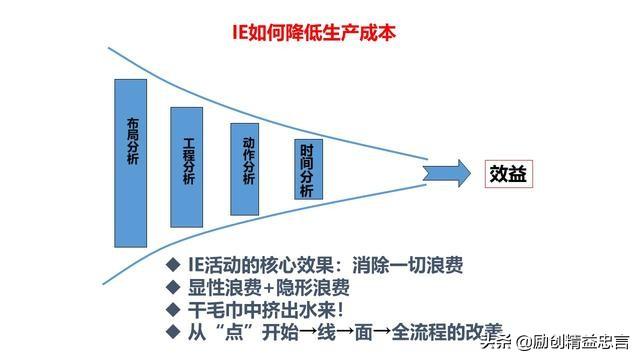
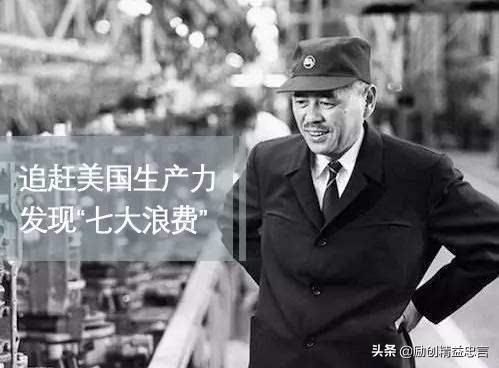
【现场IE4大利器】
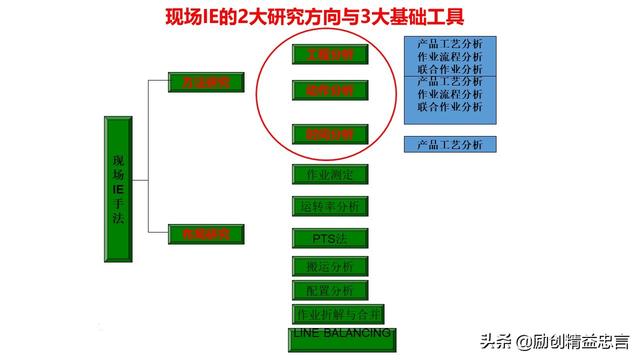
工程分析
针对单个制造工程(单个单元或单个产线)加以分析、调查,找出其中浪费、不均匀、不合理的地方,进而进行改善的方法,称之为工程分析
工程分析基本步骤
- 展开预备调查
- 使用标准符号制作工程流程图
- 测定各工序的必需项目,并把相应的数值记录在制品工程分析表中
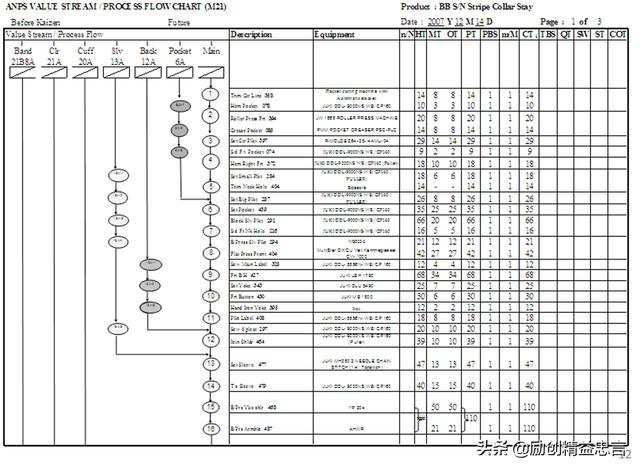
- 对测定结果进行整理,绘制出各工序价值流图或山积图(YAMAZUMI)
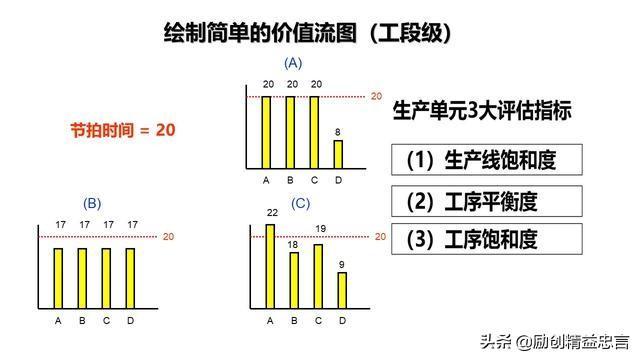
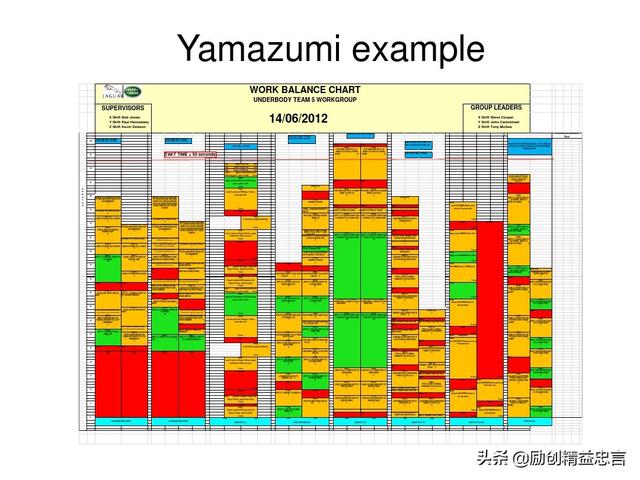
- 定量评估单个工程的价值利用率(效率)
在大多数的IE教材中,都使用“工程平衡度”作为指标,这是十分科学但又十分不完整的指标。“平衡度”只能用于评价工程内各个工序所需作业时间之间的差异程度,但它并不涉及工程中的搬运时间(工序间传递)、工序内的等待时间。换言之、平衡度不能用于评价整个工程的时间利用率!所以必须使用3个指标而全面评估
- 工序平衡度
- 单个工序饱和度(单个工序作业时间/节拍)
- 工程整体饱和度(所有工序作业时间之和/工程LT)
改善4大基本手法ECRS
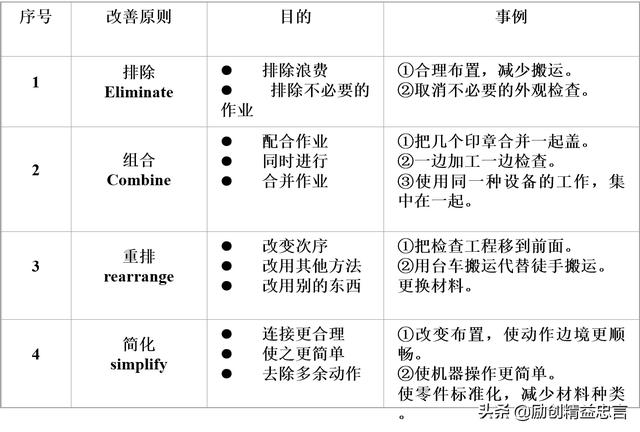
时间分析与标准工时
时间一去就不会回来,必须进行定量的分析,消除不必要的损耗,提高时间的利用效率
许多企业都知道要提高效率,却总是以定性的方法来进行,结果许多时间在不知不觉中浪费掉了却不感到可惜。须知,效率是以时间为基准来衡量的。对时间和产出进行定量的分析才是提高效率的堂堂正正之道。所谓时间分析,就是针对时间及产出做定量的分析,找出时间利用不合理的地方,从而进行改善的方法,是IE方法的一种基本方法
时间分析的意义
- 生产效率改善的重要手段
- 标准工时设定的重要依据
- 制造系统规划与改善的重要依据
- 作业者技能与管理水平评估的重要依据
- 成本分析的重要依据
时间分析的方法
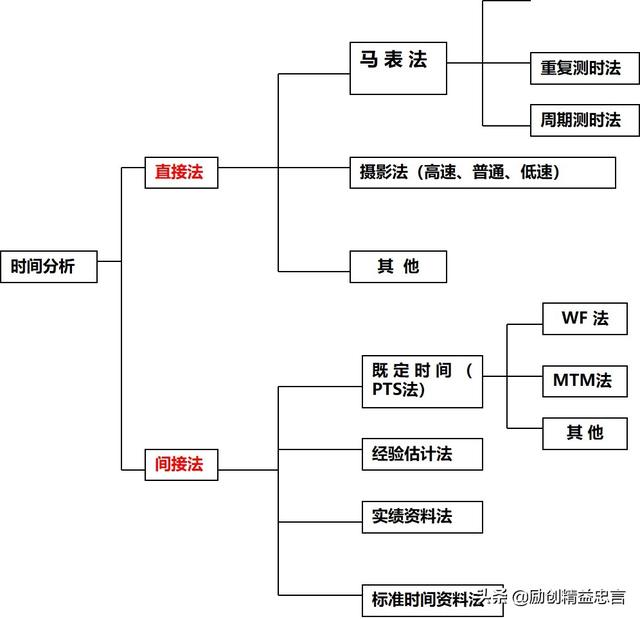
成熟的企业一般运用间接法,特别是PTS法设计标准工时
标准工时ST
所谓的标准时间,就是指在正常条件下,一位受过训练的熟练工作者,以规定的作业方法和用具,完成一定的质和量的工作所需的时间
- 在规定的环境条件下
- 按照规定的作业方法
- 使用规定的设备、治工具
- 由受过训练的作业人员
- 在不受外在不良影响的条件下
- 达成一定的品质要求
- 一般而言是指完成1件
标准工时的构成
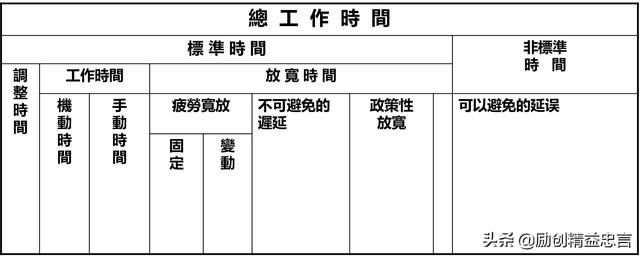
标准工时的详细计算公式
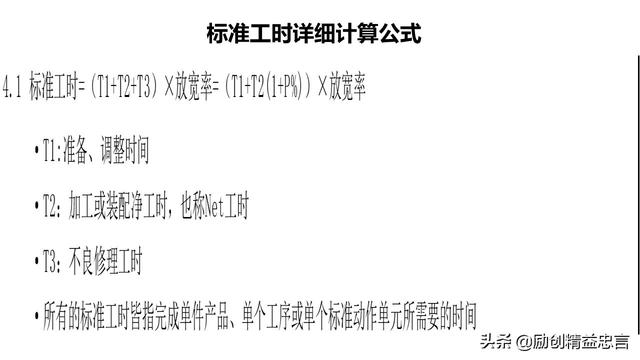
放宽量标准
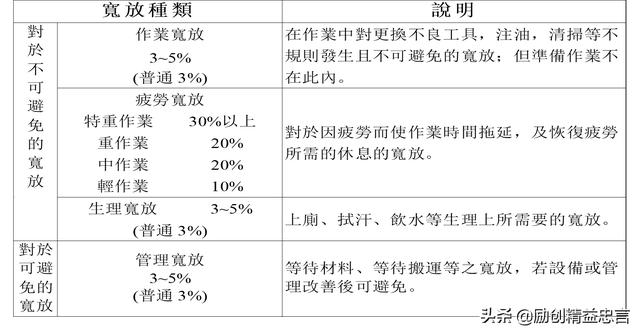
标准工时实战案例
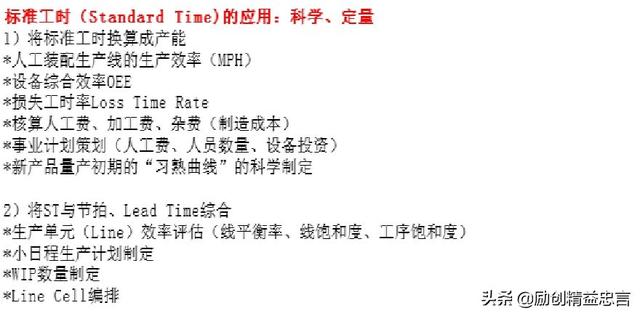
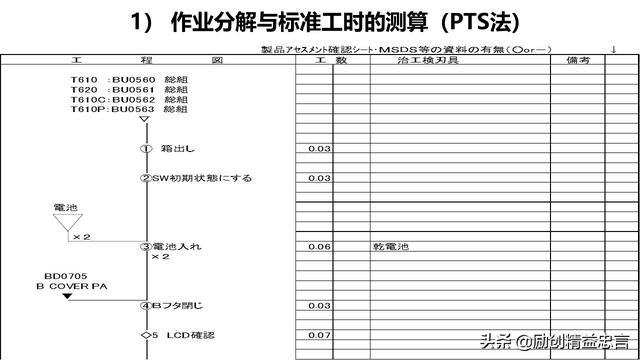
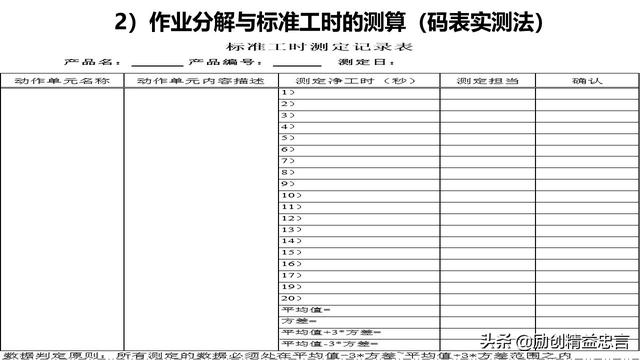
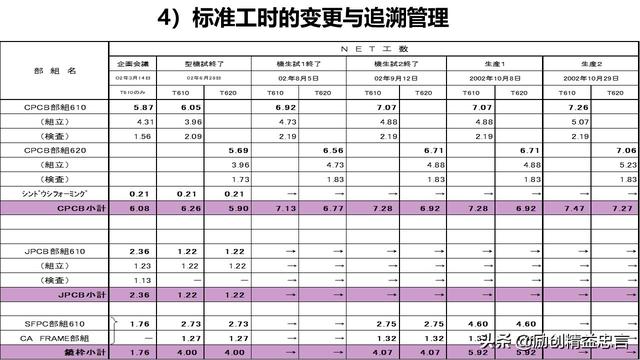
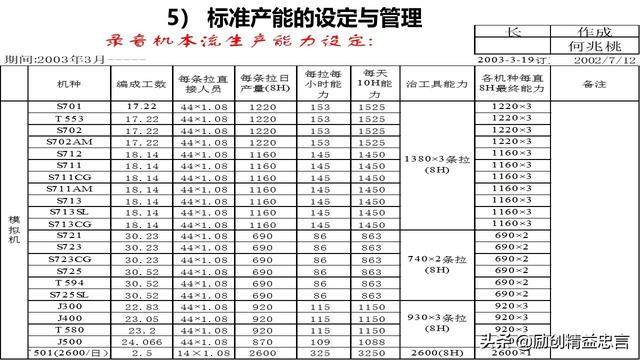
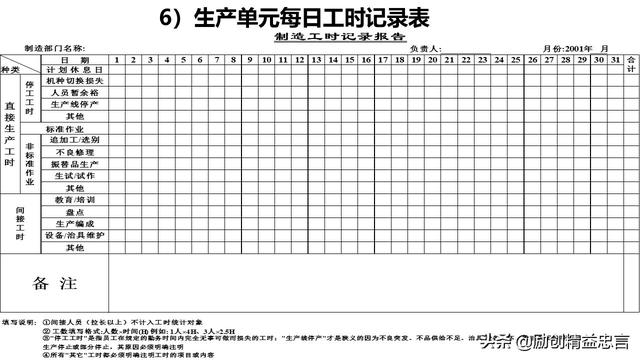
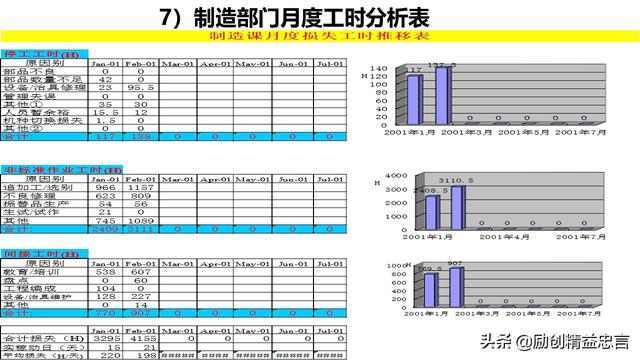
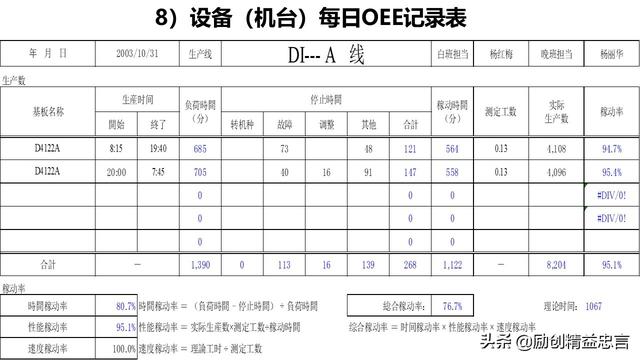
动作分析与动作改善
世 界 上 最 大 的 浪 费,莫 过于 动 作 的 浪 费--吉尔布雷斯
“动作经济原则”又称“省工原则”,是使作业(动作的组成)能以最少的“工”的投入,产生最有效率的效果,达成作业目的的原则。“动作经济原则”是由吉尔布雷斯(Gilbreth)开始提倡的,其后经许多工业工程的专家学者研究整理而成。熟悉掌握“动作经济原则”对有效安排作业动作,提高作业效率,能起到很大的帮助
人体工程学2大基本认知
- 动作幅度与疲劳度
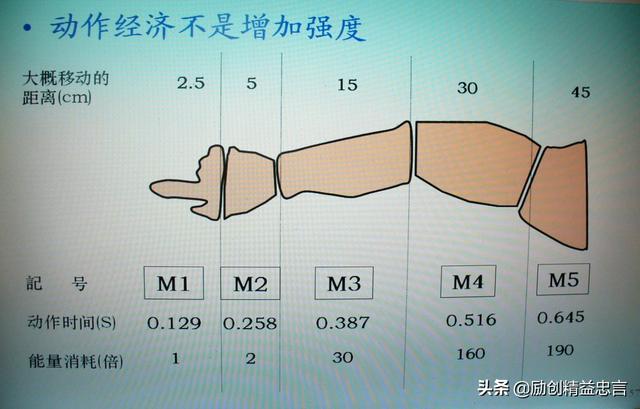
- 极限幅度
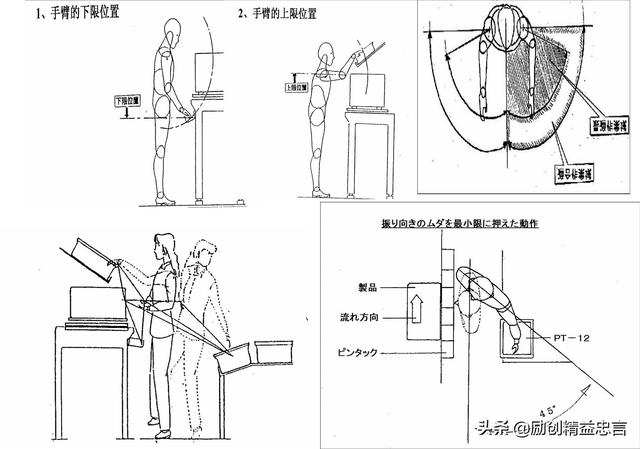
动作经济4项基本原则
- 追求动作平衡
- 減少动作数量
- 缩短动作距离
- 舒适的工作环境
动作改善20项原则
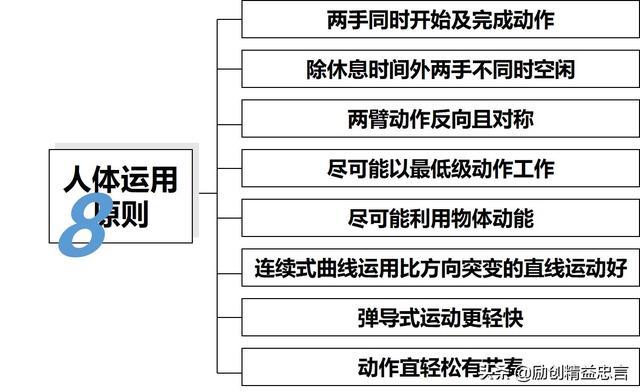
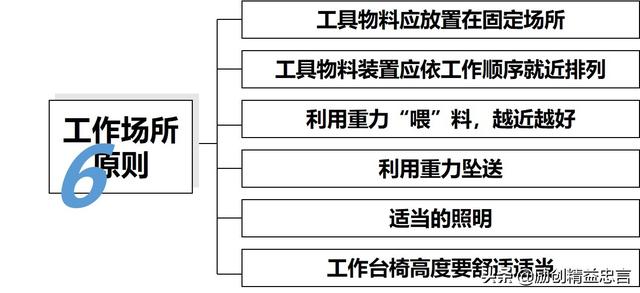
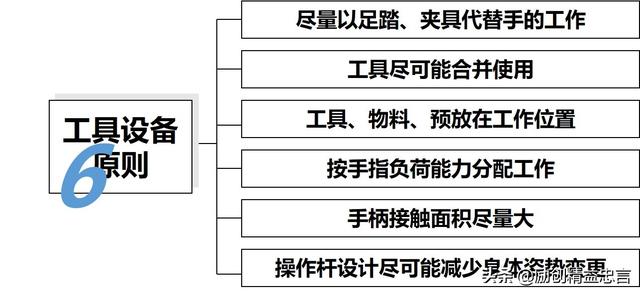
动作改善实战案例
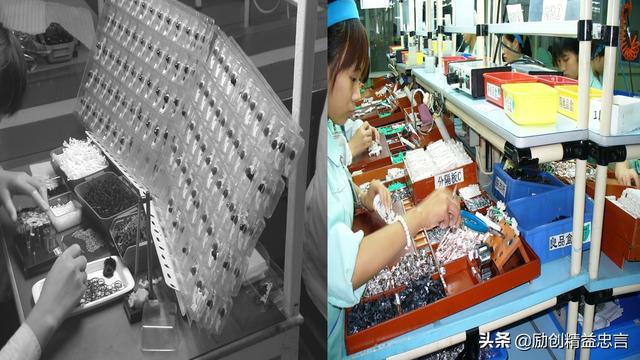
作业台面科学布局
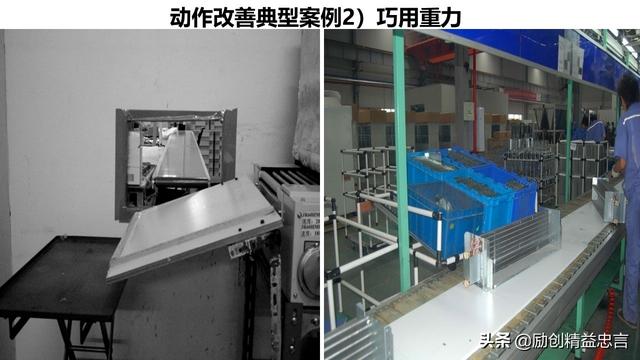
巧用重力
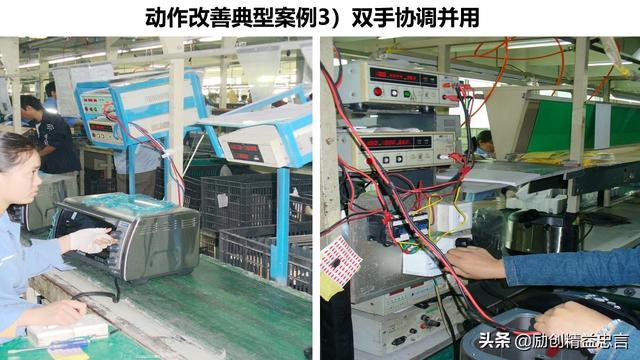
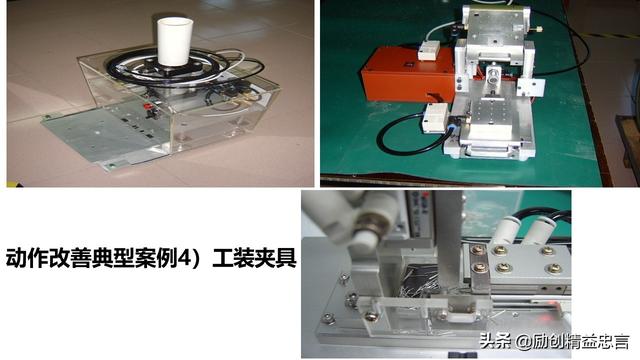
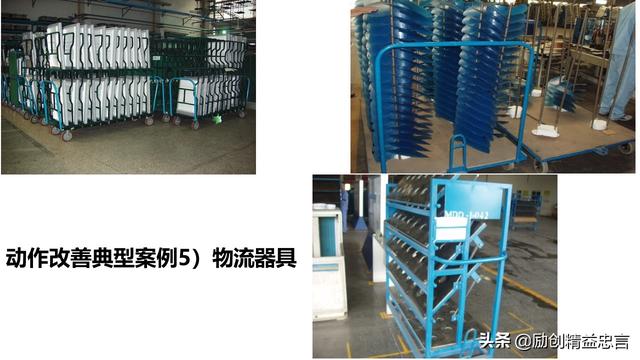

上料辅助工装
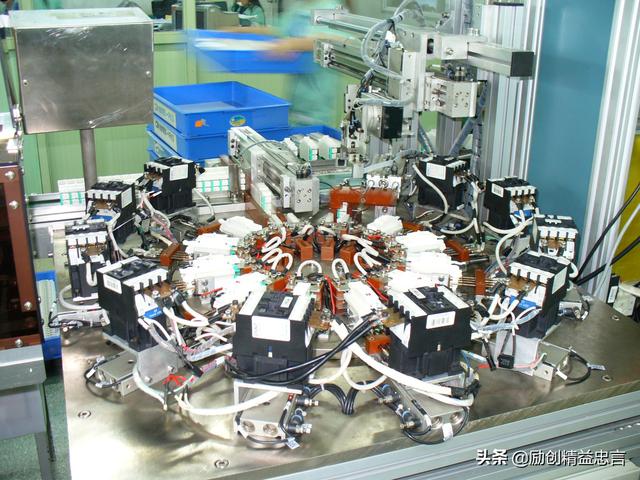
简便智能自动化LCIA
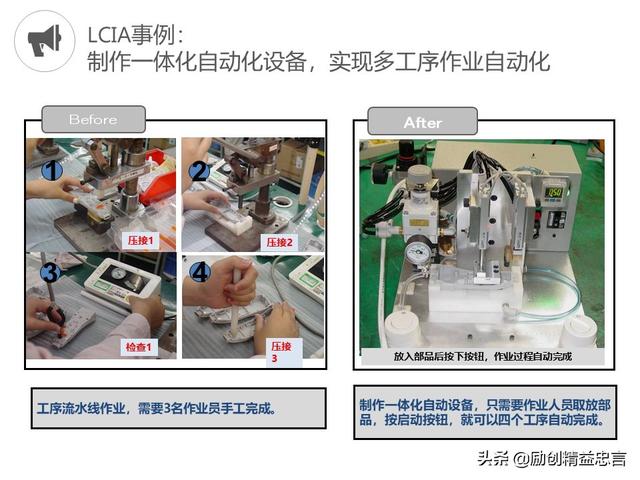
3P布局设计与优化
生产准备流程3P是英文单词 Production Preparation Process的首字母缩写,是由日本顾问Nakao(中尾千寻)创建的一种精益设计方法。它将精益设计和改善文化融入到产品设计和制程设计的过程中,形成一套模块化的布局Layout设计方法。它不仅仅关注产品和制程的设计,同时关注QDTC(The Best Quality,At The Demand Volume, Proper Timing (TAKT Time),Proper Cost)等精益思维的注入
运用3P技术可以缩短新产品投产时间,完善作业布局和物流,降低设备投资额,降低运作成本
3P通过整合准时化原则(JIT)进行流程设计,避免许多事后改善的成本
通过突破性改善方法的的执行,可以促进生产的制程和设备变得尺寸合适且很有柔性
3P布局设计流程
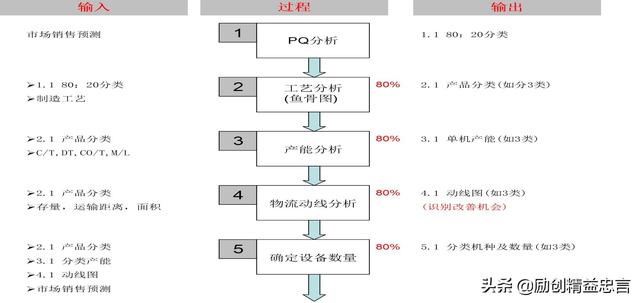
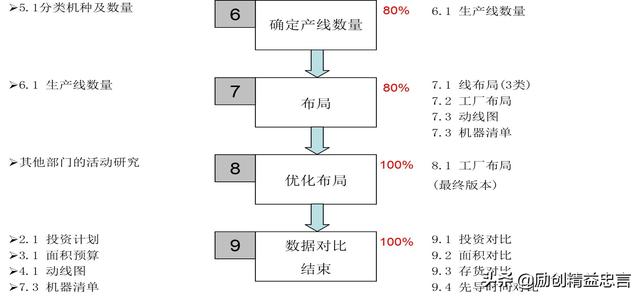
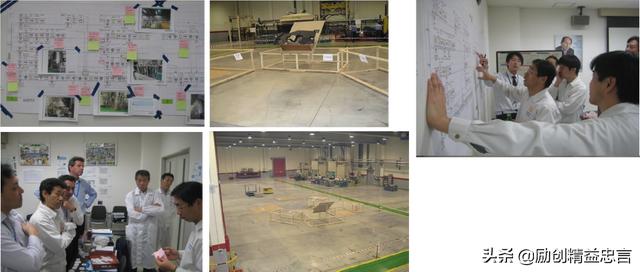
精益布局10大基本原则
- 相邻原则
- 充分利用立体空间
- 统一原则
- 最短距离原则
- 物流顺畅原则
- 减少存货原则
- 便于信息的流动原则
- 安全满意原则
- 灵活机动原则
- 环境美观
【总结语】
何为浪费?何为高效率?众多企业的管理者往往存在着片面、甚至错误的认知,将高效率定义为:动作飞快、争分夺秒、永不休息等。其实这是一种肤浅的形式主义,而忽略了对于作业方法合理性、流程整体的优化性、流程性浪费与无用功的深入研究,因此将导致“瞎干、白干、盲干”的低效作业
现场IE正是一种科学方法论,通过对制造流程中的各类浪费进行逐层细化的定量分析,从而发现问题的症结,并且以合理的手段加以改善。这正是众多制造型企业所急需的思维方式及实战工具。大野耐一所言“干毛巾中挤出水来”可谓一针见血
【匠心宣言】
专注、专研、专耕精益制造与精益管理二十余载,深知中国制造业过去的成长与崛起,更深感未来全球竞争之艰巨!实业兴邦之使命感一直深埋于心,每日催促我努力前行
阅后如果有兴趣不要忘记点击右上角“关注”,这样就可以每天获取本头条号专栏分享的知识
欢迎关注、评论、收藏、转发与交流