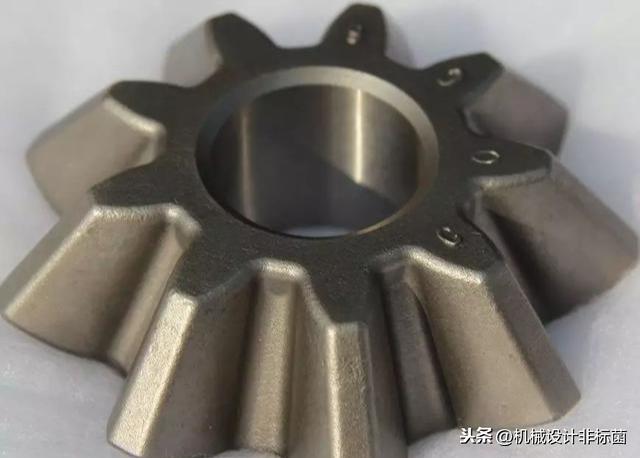
一、锥齿轮工作原理和磨损原因
直齿锥齿轮因具有传动平稳、效率高、承载能力强及齿形容易实现净成形等优点,已在交通、风电及装备制造业等基础产业、众多领域内得到广泛应用。
汽车、农机和装载机后桥中的差速器齿轮因长时间处于重载、冲击等复杂多变的工况环境,若能在净成形锥齿锻坯精度的前提下,对机加工工艺进行充分论证、优化,使得加工过程中的定位基准、检测基准及装配基准有机统一,确保其形位公差在一定范围内能够稳定控制,可有效提高机加工的效率和精度,进而提高锥齿轮的使用寿命,降低噪声,提高传动平稳性,具有非常重要的现实意义。
普通汽车差速器一般由四个行星齿轮、十字轴、两个差速器半壳、两个半轴齿轮及球面垫片、半轴齿轮垫片等相关附件组成(见图1)。
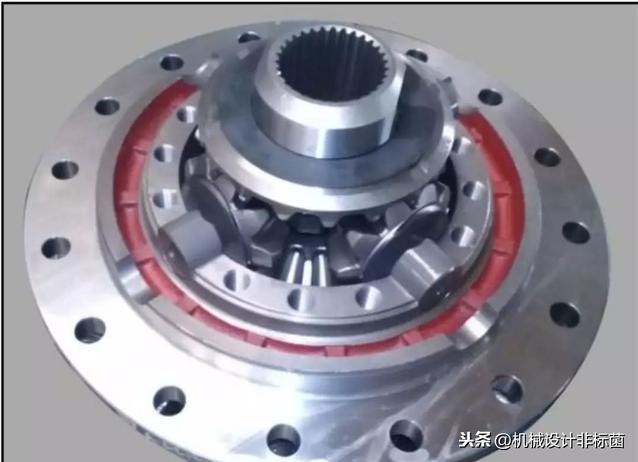
差速器壳体和行星齿轮十字轴连成一体,构成行星架。当汽车在平整路面直线行驶时,四个行星齿轮随同行星架绕两半轴齿轮轴线公转,此时行星、半轴齿轮处于相对静止状态。
当汽车转弯行驶时,必须适应转弯过程中外侧驱动轮行程大于内侧驱动轮行程的需要,两轮子转动的角速度就有差异,四个行星齿轮除随同行星架绕两半轴齿轮轴线公转外,还各自绕本身的轴自转,此时行星、半轴齿轮的锥齿开始啮合传动,相啮合的单齿受力并传递扭矩。
整个过程中随着各单齿受力大小不同(该力又可分解为齿轮齿面的圆周力和轴向力),各齿轮均产生不同程度偏离锥心的趋势,使得各行星、半轴齿轮分别压紧球面垫片和半轴垫片,两种垫片随着齿轮的旋转会同速或不同速地转动,此时垫片就会与齿轮接触面和壳体面产生摩擦,久而久之,垫片就会出现不同程度的磨损。
若齿轮以锥齿为基准检测的半轴齿轮安装面、行星齿轮的球面和内孔的形位公差超差严重,整套齿轮在差速工作状态下,就会对两种垫片产生交替无序的载荷,更加快了各垫片的无规律磨损。
整个差速器中的各零件,垫片本身就是易损件,但终端客户的汽车在行驶过程中,并不注重易损件的定期检查和更换,导致因垫片磨损,使齿轮在需要正常啮合处于工作状态时不能正常啮合传动,六个齿轮的锥心会出现不同程度的偏离,使齿轮的各单齿接触区严重偏离整个齿形中部而偏向齿顶和小端,随着此情况的加剧(有些垫片厚度会磨损一半或出现楔形),更加重了壳体面和轮齿面的的磨损,齿轮面就会出现点蚀、剥落或拉伤,更严重的会出现掉块或碎齿,造成齿轮损坏。
从以上差速器齿轮的工作原理和损坏原因描述,不难认识到差速器齿轮在机加工过程中控制各形位公差的重要性。
二、行星齿轮加工工艺分析与改进
目前差速器行星齿轮机加工工艺流程大致为以下两种:
①合格的精锻件毛坯→冷切边→抛丸→钻孔→车内孔→车球面、背锥→热处理→磨内孔→磨球面。
工艺流程①的主要工序如图2所示。
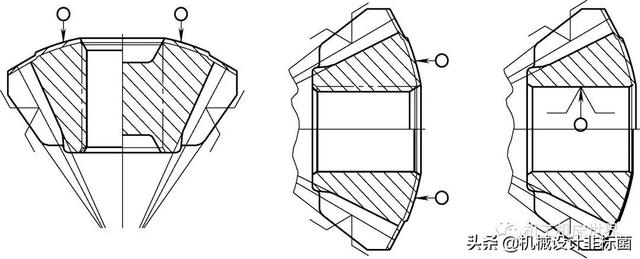
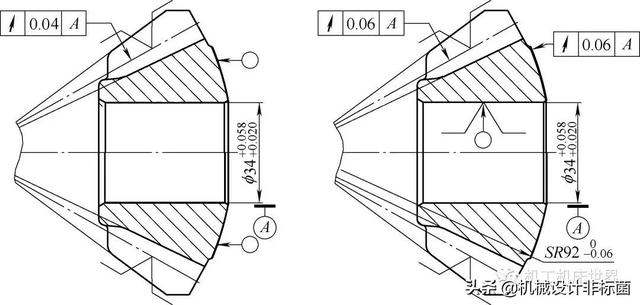
钻孔--车内孔--车球面、背锥--磨内孔--磨球面
②合格的精锻件毛坯→抛丸→车背锥→冷切边钻孔,车内孔、球面→热处理→精车内孔、球面。
工艺流程②中的主要工序如图3所示。
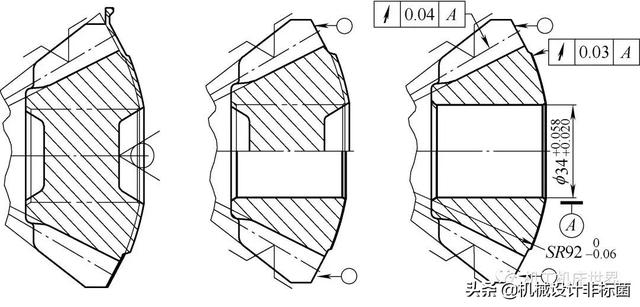
车背锥--钻孔,车内孔、球面--车内孔、球面
对比以上两种行星齿轮的热前、热后加工工艺不难看出,工艺流程①中工序较多,定位基准在齿形与内孔间偶有转换或出现过定位现象,导致机加工过程占用设备多、投入人力多以及半成品多次装夹,质量不易控制,且最终精加工过程中因出现过定位现象,导致形位公差超差严重。
而工艺流程②中工序较少,个别工序合并一次装夹切削成形,且始终以净成形的齿形为定位基准,并且热处理后精加工时,行星齿轮以齿形定位,压紧背锥,将内孔和球面一次精车成形,这样使得以内孔为基准,检测球面跳动时极易控制在0.03mm以内。这样在确保锻造工序锥齿齿形精度及热处理后精加工齿形定位体精度、找正准确前提下,加工内孔、球面至尺寸后,以内孔为基准检测锥齿齿圈跳动,可稳定地控制在0.04mm以内。
这样结合前述行星齿轮在差速器总成内的装配状态,及无论是其行星架绕半轴齿轮轴线公转,或行星齿轮在半轴齿轮外力作用下绕其自身轴线自转,均能传动平稳,噪声较小,也排除了球面垫片、壳体内球面SR的非正常磨损,提高了齿轮的使用寿命。
三、半轴齿轮加工工艺分析与改进
目前差速器半轴齿轮机加工工艺流程大致也有以下两种:
①合格的精锻件毛坯→冷切边→抛丸→钻孔→车小端面、内孔→车外圆、安装面、背锥→拉削内花键→热处理→磨削外圆、安装面。
工艺流程①中的主要工序如图4所示。
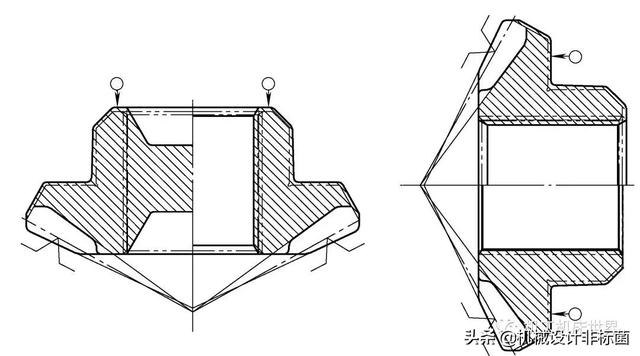
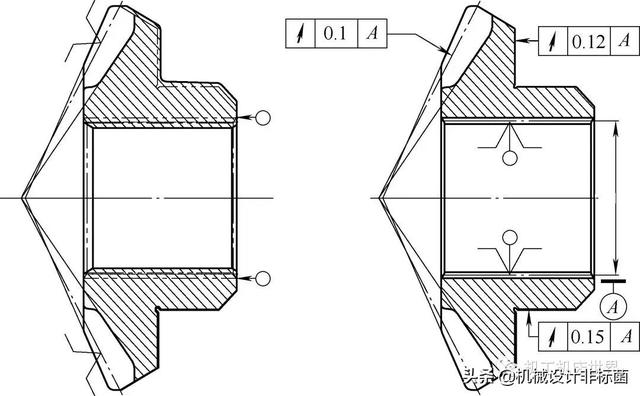
钻孔--车小端面、内孔--车外圆、安装面、背锥--磨削外圆、安装面
②合格的精锻件毛坯→抛丸→车小端面、外圆、安装面、背锥→冷切边→钻孔、车内孔→拉削内花键→热处理→磨削外圆、安装面。
工艺流程②中的主要工序如图5所示。
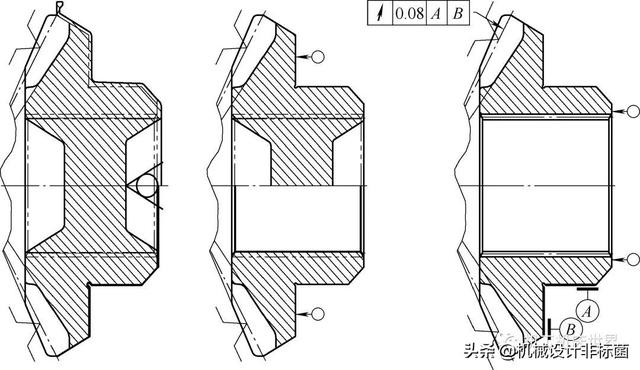
车小端面、外圆、安装面、背锥--钻孔、车内孔--磨削外圆、安装面
对比以上两种半轴齿轮的热前、热后加工工艺可以看出,工艺流程①中热前工序较多,导致加工过程占用设备多、投入人力多,质量不易控制。
而两个工艺流程中的热后精加工工序,从字面上看没有任何区别,但从工序图中可以看出,两者的根本区别在于加工时的定位基准不同。
工艺流程①是以内花键键侧定位磨削加工的,执行该工艺的厂家,仅是为了满足图样要求及迎合车桥厂家机械地按图验收的应付行为,是没有从差速器的工作原理、齿轮的工作状态及传递力和扭矩的情况认真分析而采取的短期行为。半轴齿轮的内花键是与汽车半轴的外花键相配的,属间隙配合,仅传递左右两车轮转弯行驶时而造成的两根汽车半轴自转角速度不同而产生的扭矩。
如果按照用户的图样机械地照抄照搬,为了应付以内花键为基准,检测安装端面、外圆的端、径向跳动,势必会因内花键的花键变形(鉴于国内目前的原材料、淬火油及淬火工艺现状,热处理花键变形很难像国外一样得到有效而稳定的控制)而削弱对齿圈跳动的控制。
另外,以内花键定位胀紧的热后加工方式,常常会因内花键变形大小不一、形状无规则,使花键孔出现的锥度、椭圆度不同而导致件件齿轮在锥度花键轴上的轴向位置不一,由此而磨削出来的齿轮安装面高低也会出现散差较大的现象,从而导致磨削加工出的同批次半轴齿轮安装距尺寸极不稳定,而使装配出的差速器总成半轴齿轮的轴向间隙不稳定,经常出现转动过程中的点卡现象及间隙较大,使流水线上的装配工人频繁更换调整垫片,影响装配效率。或因装配疏忽时,没有发现间隙过大,会造成差速器转动异响,导致最终拆解总成。
而工艺流程②中,是以齿形定位、压紧小端面,磨削安装面和外圆的,安装面相对于外圆轴颈的垂直度或端面跳动极易保证,同时以外圆、安装面为基准,反测锥齿齿形的齿圈跳动,也较容易地控制在0.08mm以内,这样就很好地保证了锥齿轮外圆、安装面、齿形等形位公差的特殊特性,同时也与齿轮最终综合检测时的检测基准达到了统一,即以半轴齿轮的外圆和安装面为基准,以行星齿轮的内孔和球面为基准,在锥齿轮专用综合检测仪上检查以上对滚,检测一对齿轮的安装距变动范围、侧隙大小、齿面接触区大小及位置等,类似于在差速器壳体内装配、检测、工作状态的真实再现。
这样就基本实现了差速器锥齿轮加工过程中的定位基准、检测基准与装配基准或工作基准的高度统一,有利于提高齿轮的加工精度,避免基准转换造成的精度损失,从而提高齿轮的使用寿命。