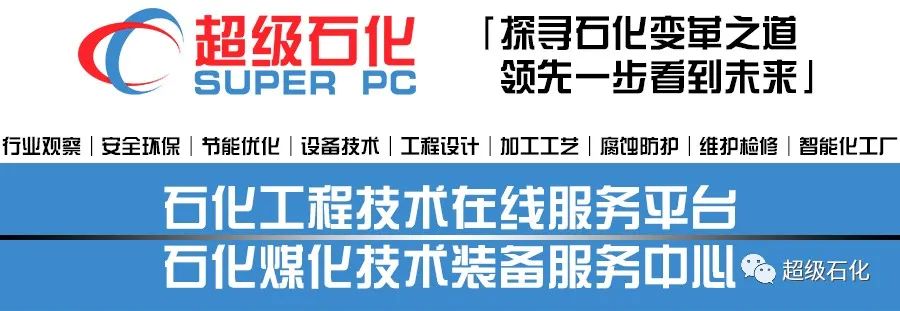
主要内容:某炼厂气变压吸附(PSA)提纯氢气装置吸附剂寿命短、吸附性能差、产品氢气纯度和氢气回收率低,故障自动诊断切塔专家系统设计有缺陷造成吸附塔压力大幅波动。通过更换全部吸附剂,提高产品氢气纯度和氢气回收率;通过更换故障自动诊断处理专家系统,消除装置故障切塔过程中的非正常压力波动,提升装置安全性;通过更换自适应优化控制系统,装置产品质量控制更稳定,提升装置运行经济性。改造获得了良好的效果,年增产高质量氢气产品超过1000万Nm3,改造后运行3年装置的各项操作指标均没有下降。
关键词:变压吸附(PSA);炼厂气;提氢;改造;吸附剂;专家系统
随着国家对燃料油的品质要求越来越高,几乎所有油品都要通过加氢改质或者加氢精制处理才能达到国家标准,因此各炼油厂都需要氢气作为加氢原料,并且氢气需求量越来越大。绝大多数炼油厂都会副产不少含氢炼厂尾气,例如重整气、低分气、催化干气等,从这些炼厂气中分离提纯氢气用作加氢原料,有着非常高的经济效益。在中国有数百座炼油厂,大多数炼油厂都有一套或者多套炼厂气变压吸附(PSA)分离提纯氢气装置,这些装置回收的氢气产生着巨大的经济效益。
由于炼厂气成份复杂,烃类组分多且含有C5+等高碳烃组分,这些烃类杂质组份相对分子质量和分子直径都较大,很容易被吸附在吸附剂的微孔表面,却不容易在常温下被解吸,最终堵塞吸附剂微孔造成吸附剂性能下降。因此,相比天然气、炼厂干气水蒸汽转化制氢装置配套的PSA分离提纯氢气装置,炼厂气PSA分离提纯氢气装置的吸附剂性能衰减速度明显更快,吸附剂寿命明显更短,正常的设计寿命不超过十年,不少装置只运行几年就需要更换吸附剂,有的装置甚至只运行几个月就更换了吸附剂。针对炼油和石化行业富氢混合气(如重整尾气、催化干气,加氢尾气等)中烃类组分多且含有C5+等高碳烃组分的特点,西南化工研究设计院有限公司(原四川天一科技股份有限公司)专门成立了处理这类气体的吸附剂研制攻关小组。经过大量的实验,终于研制出应用PSA技术一步除去炼油厂混合气除氢气以外所有杂质的专用吸附剂CNA-229[1]。解决了高烃类杂质组份在吸附剂上的吸附性能和解吸性能的平衡问题,在提升吸附剂吸附性能的同时,还能保证足够长的使用寿命。
1 装置概况
1.1 装置改造前现状
某炼化企业有一套国内其他PSA技术供应商设计的大型炼厂气PSA提纯氢气装置。该装置设计处理原料气量110500Nm3/h,氢气产量90000Nm3/h,吸附压力1.2MPa,氢气回收率≥96%,产品氢气纯度≥99.9%,产品氢气中杂质组份φ(CH4)≤0.1%,φ(CO+CO2)≤10×10-6。
装置采用10-2-5/V抽真空再生PSA工艺,由10台吸附塔、1台原料过滤器、1台原料分液罐、3台缓冲罐、1台混合罐、3台真空泵、3台解吸气压缩机、2台氢气压缩机、1套液压系统及一系列程控阀门组成。装置正常运行时始终有两台吸附塔处于吸附步骤,结束吸附步骤的吸附塔先通过五级均压降回收有效气体提高氢气回收率,均压降结束后先通过逆向放压将吸附塔内压力降至约20kPa,逆放结束后用真空泵对吸附塔抽真空至塔内压力达到-0.08MPa,通过持续的抽真空将吸附在吸附剂床层中的杂质组份解吸出来,吸附剂得以再生。吸附剂再生合格的吸附塔通过五级均压升将压力升至约1.0MPa,然后用产品氢气对该吸附塔进行最终升压将该塔压力升至吸附压力后再进行下一次吸附步骤。整个装置运行的工艺流程示意图见图1。
图1 工艺流程示意图
该装置原料气为多股炼厂气的混合气,分别有临氢装置富氢气体、加氢裂化富氢气体、连续重整装置重整气、PX装置含氢尾气、柴油加氢精制装置低分气等。装置设计原料气条件见表1。
表1 原料气条件
装置于2007年12月建成投产,于2009年6月进行了装置性能标定。标定时的原料气氢气含量相比设计数据偏高,氮气及其它烃类杂质含量均偏低,实际运行原料气条件优于设计原料气条件,详见表2。
表2 原设计条件及2009年标定时实际运行物料
1.2 装置存在的主要问题
标定持续了两天,从2009年6月17日8时开始至2009年6月19日8时结束共48h。标定的主要结论如下:
(1)产品氢气纯度未达到设计值。标定期间产品氢气纯度在线分析仪检测的平均氢气纯度99.05%,最低值98.6%。质检中心取样色谱分析检测的平均氢气纯度99%,最低值98.3%,均没有达到设计要求的≥99.9%的产品氢气纯度。
(2)产品氢气中CO+CO2体积分数控制精度未达到设计值。色谱分析检测平均值为22.7×10-6,超过设计要求的≤10×10-6的控制指标。
(3)氢气回收率未达到设计值。在产品氢气纯度不合格的情况下,平均氢气回收率仅92.64%,远低于设计要求的≥96%。
(4)产品氢气、解吸气带吸附剂粉尘,影响后续氢气压缩机和解吸气压缩机长周期稳定运行。
(5)F、B塔吸附剂吸附效果差。产品氢气纯度在每一循环周期内都有两次降低,经分析原因是F、B塔吸附效果相比其它吸附塔明显差。
从这次标定的数据看,装置所用吸附剂的性能不佳,对关键杂质组份CH4、CO、CO2的控制精度偏低。产品氢气中CH4体积分数高达0.9%,远高于设计要求的≤0.1%的控制值;CO+CO2体积分数平均值为22.7×10-6,远超设计控制值10×10-6。在产品氢气纯度低的情况下,对应的氢气回收率才92.64%。如果要将CH4、CO、CO2控制到设计限值以内,氢气回收率还会下降,预计会下降至90%以下。
由于吸附剂性能在开车后很快就出现衰减,该装置在2010年至2016年间一直在进行频繁的在线吸附剂热再生。热再生时将吸附性能严重恶化的某台吸附塔切出下线,用现场增设的一台电加热器将氮气加热至约120℃从吸附塔顶部进入吸附塔,从上往下对吸附剂床层进行加热吹扫再生。每次热再生以后吸附剂的性能会有所提升,但每次运行几个月便再次恶化。由于吸附剂性能严重下降,2015年装置氢气回收率已经降至85%以下,解吸气中氢气体积分数超过60%。
该装置程控阀架设计过于追求紧凑,吸附塔分组过于简化。10台吸附塔只分为两组,每组5台,需要切除一整组的5台吸附塔并关闭分组隔离手阀才能对某一台故障程控阀进行拆检,此时装置的处理能力会大幅下降至满负荷的60%以下。另外,两组吸附塔之间的隔离手阀大量采用蝶阀,实际运行情况是这些三偏心硬密封蝶阀绝大多数都内漏,无法实现设计要求的隔离要求,因此当某台程控阀出故障时只能先切出与该程控阀对应的吸附塔,装置调整为辅助流程带病运行,等待合适的时机再停车拆检故障程控阀,这大大降低了装置的安全性、稳定性、经济性。
该装置液压程控阀的稳定性和维护性较差。主要程控阀故障是漏油点多以及油管接头容易被高压液压油冲脱,每次油管脱落时操作人员必须在5 min以内赶到现场手动关闭对应的液压油管根部阀,否则就会因为液压油全部泄漏造成整套装置所有程控阀无法动作,装置运行失控。
程控阀故障多,经常会有程控阀开关不到位或开关速度缓慢,在设定的时间内故障自动诊断系统未能接收到阀位传感器的检测信号而报警,导致吸附塔切出,并引起各吸附塔内压力大幅波动,切出的吸附塔越多,波动越大,最多时整个系统有3台吸附塔被切除下线。故障自动诊断系统的切塔程序设计存在缺陷,当程控阀出故障需要切除对应吸附塔时,对压力波动的判断以及部分切换步位的选择不合理,切塔时的高压差气流强烈冲击造成吸附塔、真空泵地脚螺栓松脱甚至断裂失效。
解吸气中携带大量吸附剂粉尘,造成压缩机气阀经常堵塞,活塞环、导向环和填料组件磨损加剧,机组故障率高,维修频繁,见图2。
图2 解吸气压缩机气阀被聚积的吸附剂粉尘堵塞
本装置于2007年12月底开始运行至2008年7月底,期间有8次开停工[2]。自初始运行以来,该装置常态化开停工及切塔运行,装置的安全性、稳定性、经济性都存在问题,该炼厂决定于2016年对其进行改造。
2 改造方案与优化效果
2.1 改造方案
经过竞标,四川天一科技股份有限公司(现西南化工研究设计院有限公司)获得了该装置的改造合同。四川天一科技股份有限公司在对装置进行实地详细考察后针对装置现存的一系列问题制定了整套的解决方案,主要从以下几个方面对装置进行改造:
(1)通过对原设计资料的核算发现,该装置原设计96%的氢气回收率过高,在设计操作条件下是不可能实现的。如果要将该装置产品氢气纯度控制在99.9%以上,产品氢气中CH4含量控制到0.1%以下,在吸附压力只有1.2MPa、采用10-2-5/V工艺的真实氢气回收率不会超过93%。考虑到本次改造并非全面改造,存在诸多限制条件,故改造方案按92%氢气收率核算。
(2)通过装置运行情况以及吸附剂再生情况分析,装置所用吸附剂不适应炼厂气原料。炼厂气原料中的C4以上烃类杂质相比CH4更容易被吸附,但却更难解吸,很容易在吸附剂微孔中累积,造成吸附剂活性下降甚至失活。国内有很多炼厂气提纯氢气PSA装置宣称吸附剂寿命可以保证20年,但实际运行的吸附剂寿命却不长,大多只有5年左右,有的甚至不到1年就更换了吸附剂。主要原因就是选用的吸附剂不是耐高烃杂质的PSA专用吸附剂。
通过对原供应商所用活性炭吸附剂堆密度、微孔分布等数据分析,该活性炭吸附剂是常规的煤基活性炭,较适用于天然气、炼厂干气水蒸汽转化制氢装置配套的变换气提纯氢气PSA装置,不适合用在富含高烃杂质的炼厂气提纯氢气PSA装置。而变换气中的主要杂质组份为CO2和CH4,长期运行都不会对活性炭吸附剂造成损害。常规的煤基活性炭用在炼厂气提纯氢气PSA装置上,在运行初期吸附效果也可以,但运行一定时间以后就很容易因为微孔堵塞和再生困难而出现性能衰减,整体使用寿命很短,通常不超过5年。特别是当装置为了追求运行经济性需要卡边操作甚至降低产品氢气纯度操作时,寿命会进一步缩短,这也是为什么有的炼厂气提纯氢气PSA装置一个大修周期不到就需要更换吸附剂的主要原因之一。
本次改造所用炼厂气提纯氢气专用活性炭类吸附剂CNA-229,是20世纪90年代初期西南化工研究设计院在CNA-210高性能PSA专用活性炭类吸附剂的基础上深度活化和调孔改进而来。通过特殊加工工艺实现了微孔孔径精确控制,增加中孔比例,减少小孔及大孔比例,以更好适应复杂多变的炼厂气原料。
深度活化以及更复杂的调孔工艺使CNA-229活性炭的生产成本大幅提升,但该吸附剂在以炼厂气为原料的提纯氢气装置上的使用寿命也大幅增加,保证了装置长期运行的稳定性、经济性;CNA-229型吸附剂在其他多套大型炼厂气提纯氢气PSA装置上均有超过10年的使用寿命业绩。
由于程控阀故障切塔时的气流冲击造成设备地脚螺栓松脱,存在安全隐患,改造有必要更换原装置的故障自动诊断处理专家系统。西南化工研究设计院开发的PSA装置故障自动诊断处理专家系统,通过对程控阀阀位回讯、各吸附塔在不同工艺步骤时的压力变化趋势以及内部数据库比对等多个判断条件进行综合分析和判断,相比早期的专家系统可以更精确判断出故障程控阀位号和吸附塔位号,并选择在更安全的步位切除故障程控阀及对应的吸附塔,尽可能减小切塔过程中的压力波动和气流冲击。
对装置操作人员进行深入的操作培训,强化操作人员对涉及吸附剂以及装置安全的基本原理的理解,深入讲解故障自动诊断处理专家系统、自适应优化控制专家系统的设计理念,避免因为操作失误造成吸附剂性能衰减或设备故障。
2.2 优化效果
装置改造后于2016年9月一次开车成功,2016年11月2日开始性能标定及考核。标定持续72h,标定结果如下:
(1)平均氢气纯度99.12%。虽然相比2009年标定时的平均氢气纯度99.05%提升不大,但主要原因是实际运行原料气中的N2含量相比原设计条件大幅增加。2009年时的原料气中只有少量N2,2016年时的原料气中N2体积分数高达1.28%。由于同一种吸附剂在相同的吸附压力下,对N2的吸附量比对CH4的吸附量小得多,故原料气中氮气含量大幅增加对产品氢气纯度的影响非常大。
(2)产品氢气中关键控制组份CH4的平均体积分数仅0.16%,相比2009年标定值的0.99%大幅下降。有害杂质组分CO+CO2总体积分数平均值仅11×10-6,优于改造方案设计保证值20×10-6,也优于2009年标定结果22.7×10-6。这说明本次改造所用吸附剂对关键杂质组份的吸附性能相比原吸附剂有大幅的提升。
(3)平均氢气回收率93.18%,高于设计值92%,也优于2009年标定值92.64%。如果考虑产品氢气中关键杂质组份含量差异,该装置改造后的氢气回收率相比2009年时的氢气回收率实际上是有更大的提升。
(4)在装置投运后对故障自动诊断及处理专家系统、自适应优化控制专家系统进行了多轮测试和完善。装置在切塔过程中压力波动得到有效控制,减小了对吸附塔以及真空泵的气流冲击。自适应优化控制专家系统降低了操作人员的工作强度,不再需要操作人员对装置进行频繁调节。
表3 装置改造方案及2016年标定时实际运行物料平衡
通过这次改造,达到了满意的结果;装置改造后标定结果与改造前2009年原标定值的比较见表3。而且,PSA提氢装置一直稳定运行至今。
3 结论
通过本次改造,成功提升了装置的稳定性和运行经济性。装置不再需要频繁切换至辅助流程对吸附剂进行热再生,极大改善了装置的稳定性和安全性,也大幅降低了操作人员的工作强度。产品氢气回收率、产品氢气中的有害杂质组份CO+CO2控制精度均得到大幅改善,每年增产超过1000万Nm3的氢气将为企业带来数百万元的直接经济效益,更高品质的氢气产品也更能保证后续多套油品加氢装置的平稳运行。
本次改造采用了炼厂气提纯氢气专用CNA-229型活性炭吸附剂,并优化了各类型吸附剂配比,吸附剂的吸附性能和解吸性能更平衡,确保了吸附剂有更长的使用寿命。通过对2016年9月至2019年9月连续3年的运行数据跟踪分析发现装置的各项指标均没有下降,证明了改造所用吸附剂的优异性能和吸附剂床层配比的正确性。(作者:伍 毅1,徐培泽2,秦建峰2,杨 军2,杨劲翔3,陈中明1,黄 炼1,1.西南化工研究设计院有限公司;2.中国石化股份有限公司金陵分公司;3.四川石化有限责任公司)
感谢作者的辛勤付出和贡献!本文引自天然气化工(C1化学与化工),超级石化整理发布,供参考了解,转载请注明出处。本文如果对您有帮助,请点击下方在看,留言交流!
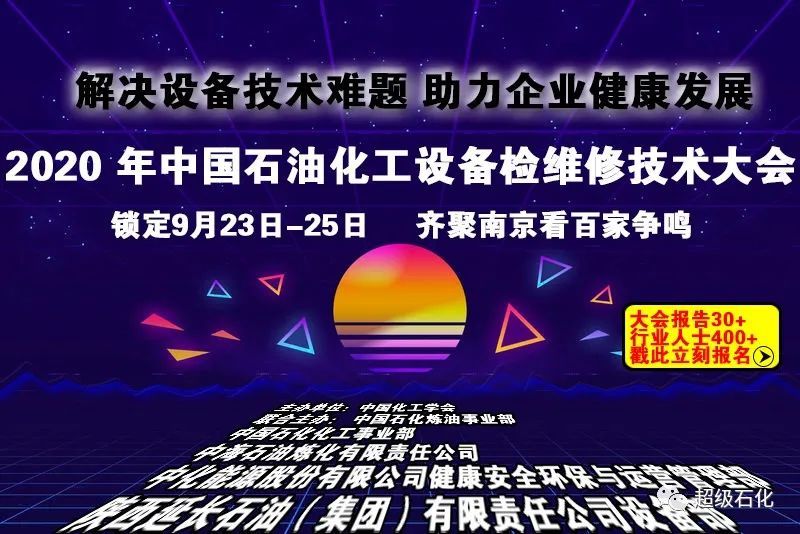
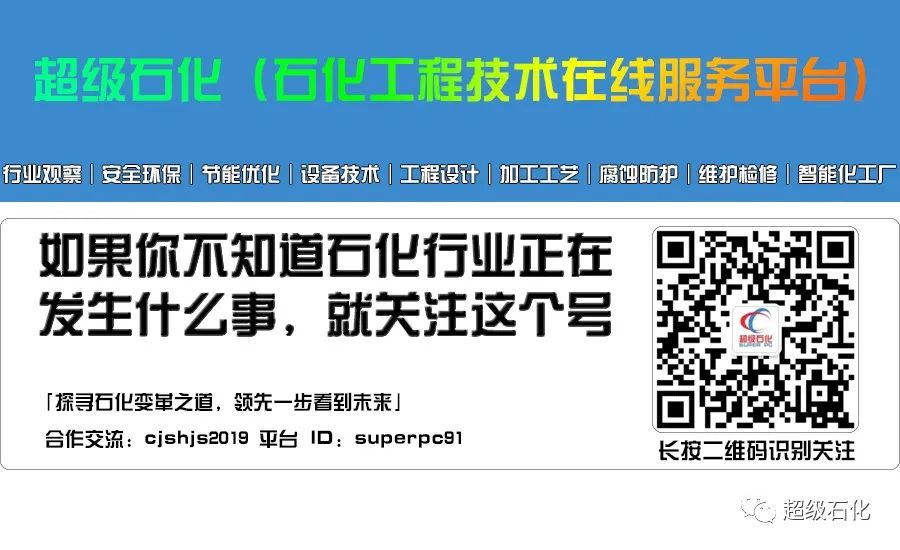