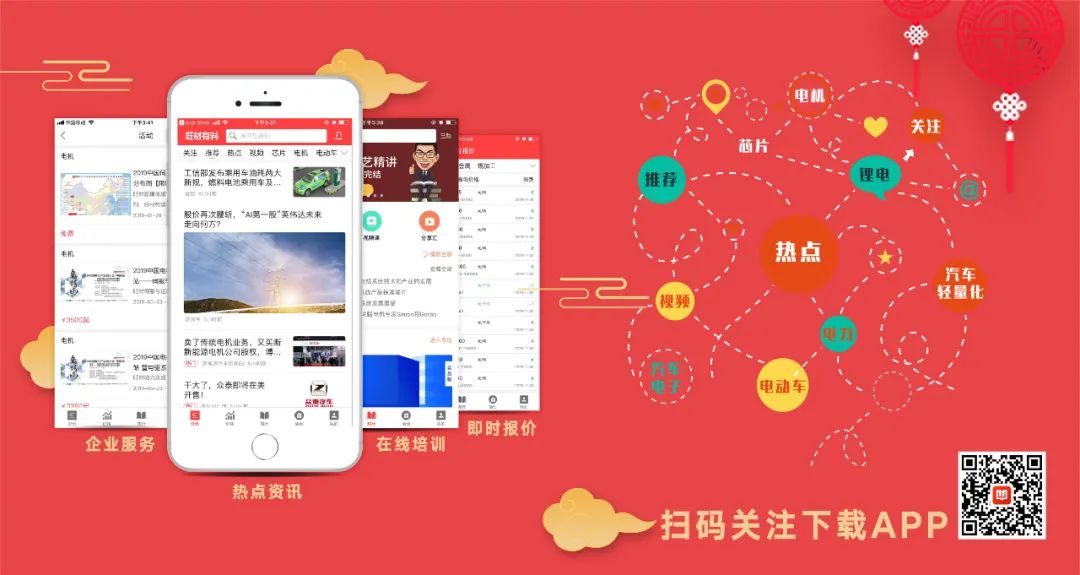
1 热管理系统设计
1.1 整体方案
该燃料电池热管理系统设计要求满足3.5kW散热功率,集成PTC电加热模块缩短冷启动时间,风扇和泵采用智能控制,温度控制精度要求±2℃,介质进出口温差小于10℃,利用高温余热对甲醇燃料进行预热。 基于上述要求,针对该电池进行了热管理系统方案设计,整体方案包括内、外双循环回路,内循环回路主要功能是甲醇燃料的预热汽化重整制氢,外循环回路的主要功能是智能冷却精确控温,稳定燃料电池电堆的工作温度,如图1所示。1.2 控制算法
采用了一种基于经验模型的拟合简化方程算法,先根据实测试验和设计经验建立经验计算模型,标定燃料电池不同输出功率时的产热曲线和风扇、泵等部件的理想控制曲线,后将风扇、泵等部件的理想控制曲线使用一元对数函数、二次函数等简单函数进行拟合,同时根据燃料电池的实时输出进行产热量的预计算,实现温度控制预判并提前给出控制量,以此缩短温度控制响应时间,保证温度控制的精确性与时效性。此控制策略的设计理念是在保证控温精度的前提下最大限度简化控制系统计算模型,使其能广泛应用于工程实际。控制算法设计原理如图2所示。 基于上文分析,电池输出功率、温度传感器和压力传感器采集温度信号作为实时输入,控制系统根据各传感器数值及温度预判对电子风扇和循环水泵进行PWM控制,真正实现冷却系统按需而工作,满足燃料电池温控条件的同时尽可能减少能量损耗。系统控制逻辑如图3所示。此控制策略以极简化运算为设计思想,相较模糊PID、神经网络等智能算法,虽对于复杂工况的温度跟踪性较弱,但数学模型运算量小,系统响应更为迅速,适用于工况较为稳定的电池系统。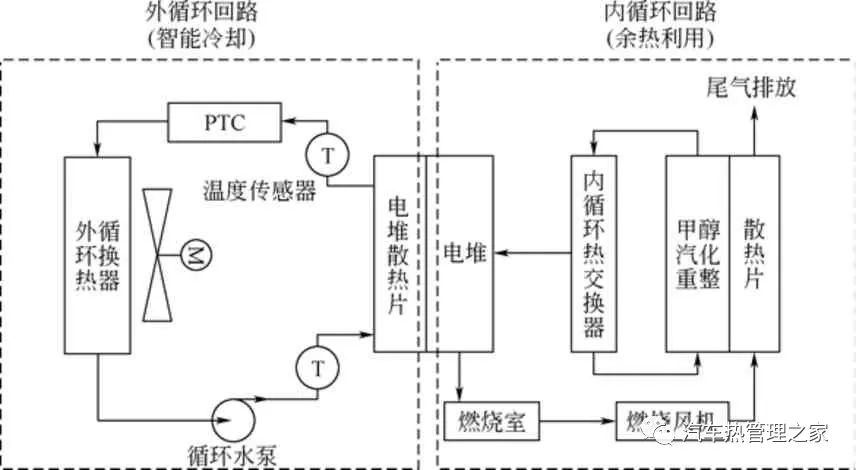
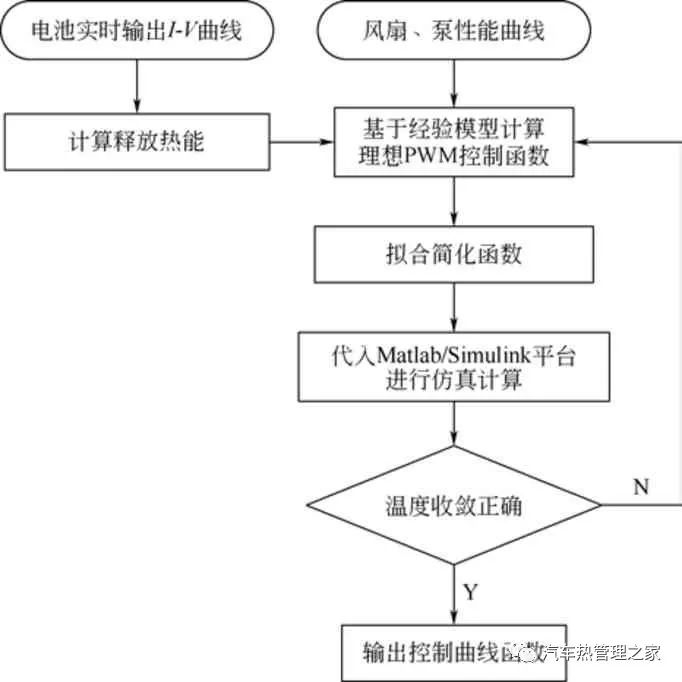
1.3 基于Matlab/Simulink平台的设计仿真
根据所提出的热管理系统控制逻辑,基于Matlab/Simulink 平台建立了热管理系统控制算法模型,主要模块有风扇控制模块(fan)、电子离心泵PWM 计算模块(bump)、燃料电池产热计算模块(FC HEAT)、散热量计算函数以及温度积分模块和温差计算自定义函数模块,如图4所示。 先通过燃料电池热交换模型计算燃料电池在不同输出功率下的冷却系统余热,再由风冷板翅式换热器传热理论公式得出各工况下所需的空气质量流速,根据风扇性能曲线反推得到风扇PWM 理想控制曲线。拟合得到简化的风扇PWM 控制方程经验模型,见式(1)。



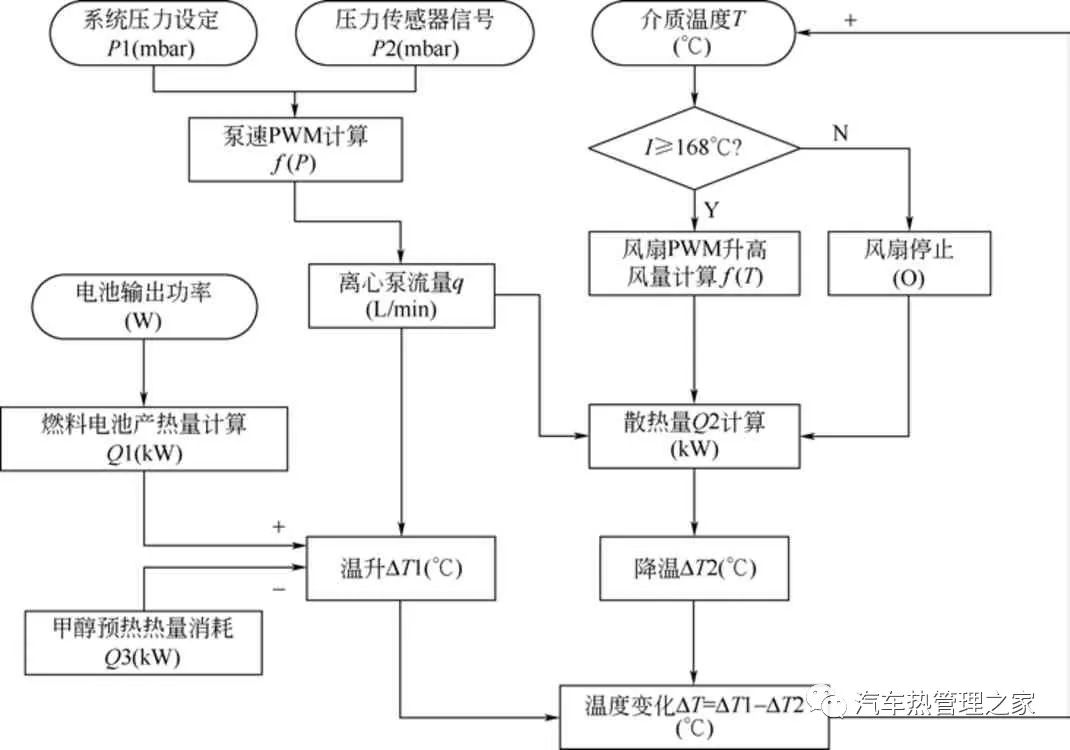
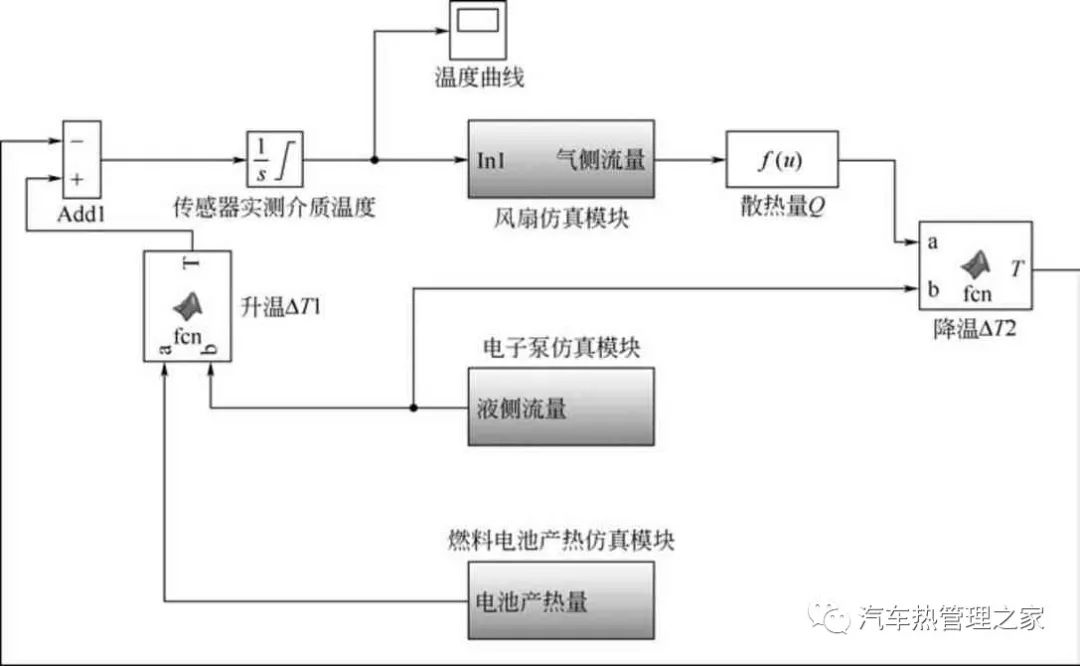
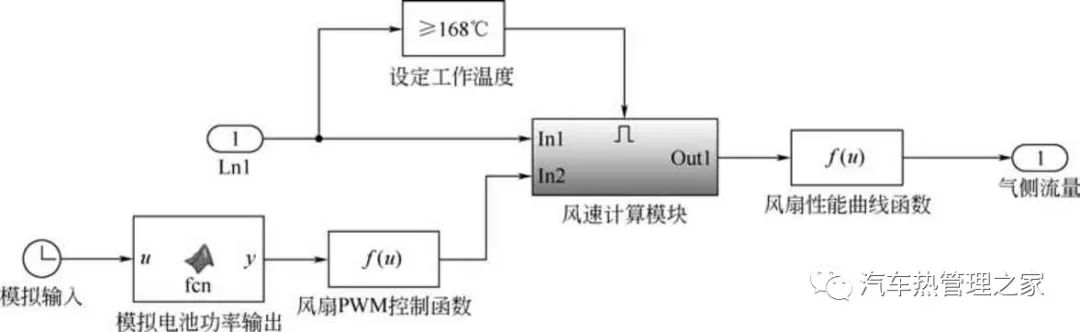
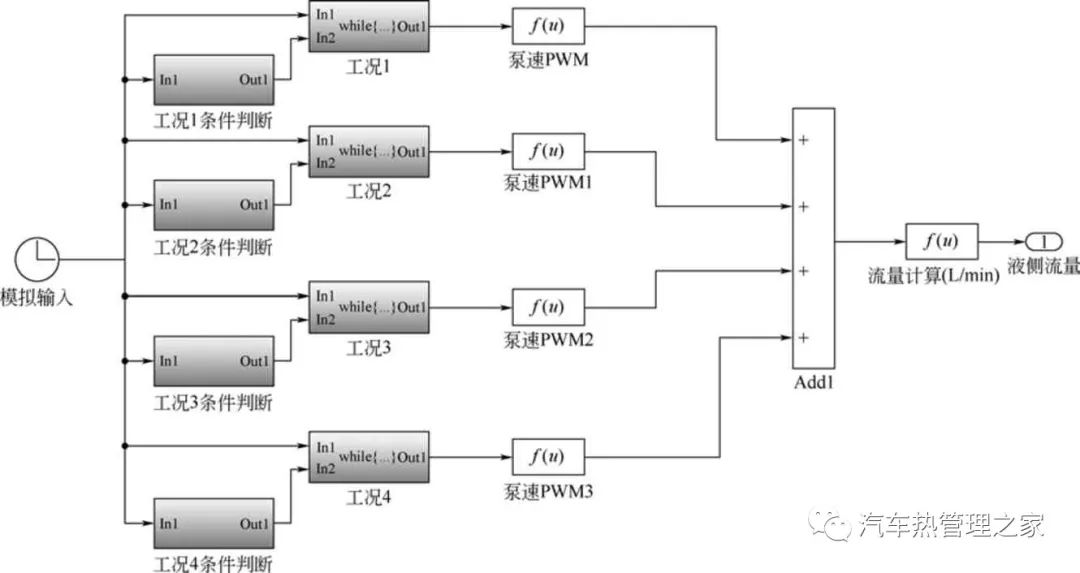
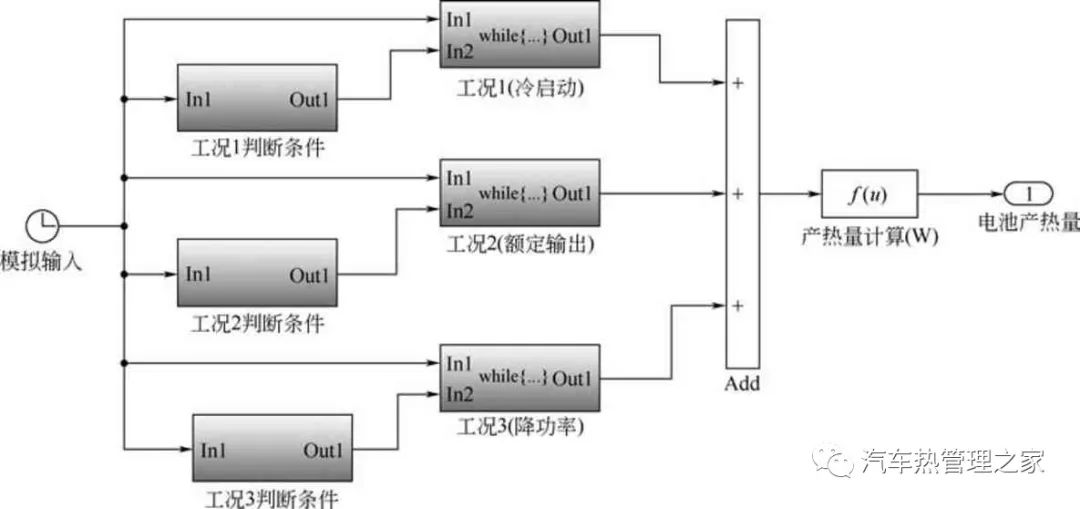
2 换热器设计
2.1 换热器结构
此前采用的换热器结构多为肋板式结构,体积和质量大,且介质容积大,不利于快速预热。本系统散热器为板翅式平行流散热器,见图8。散热器设计结构匹配燃料电池系统进出口,质量体积较之前大幅减小,散热容积尽量减小并配置6 根180W电加热棒实现开机快速升温,具体参数如表1所示。 表1 原换热器方案与优化方案参数对比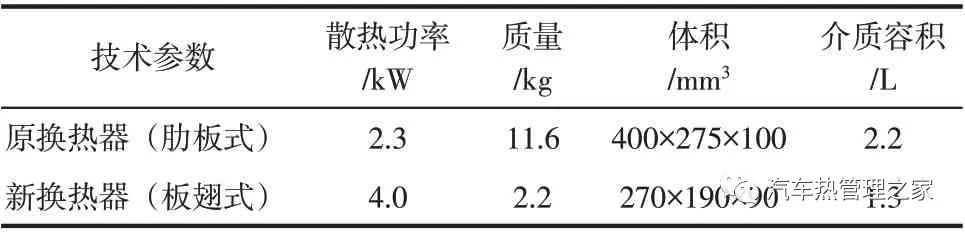
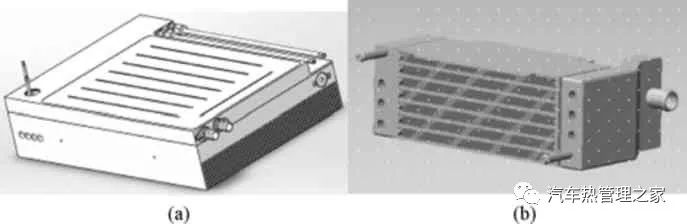
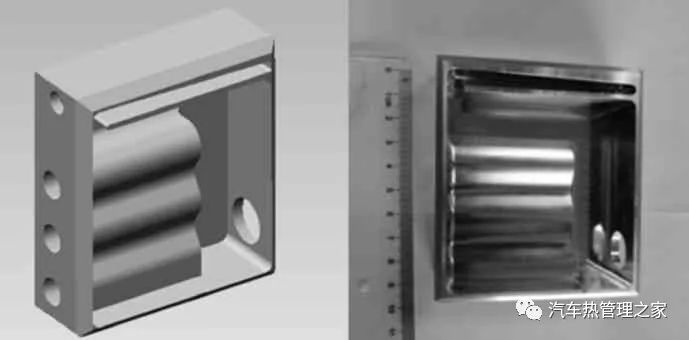
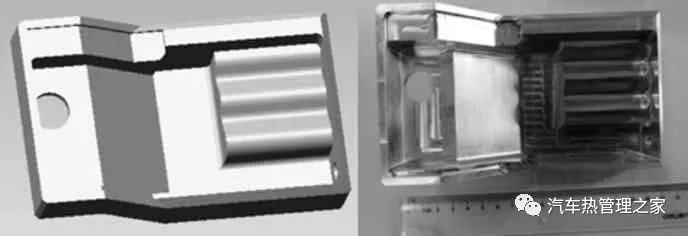
2.2 换热器传热计算
本系统中冷侧介质为空气,热侧介质为三乙二醇。利用H2O 热力学性质的统一基本方程[9]、IAWPS 公式[10]结合AP1700 网站MARS 模型求解得该系统中冷、热侧介质的物性参数。 设计换热器冷热侧f因子、j因子经验公式参考文献中的经验关联公式[11-12]分别见式(5)~式(8)。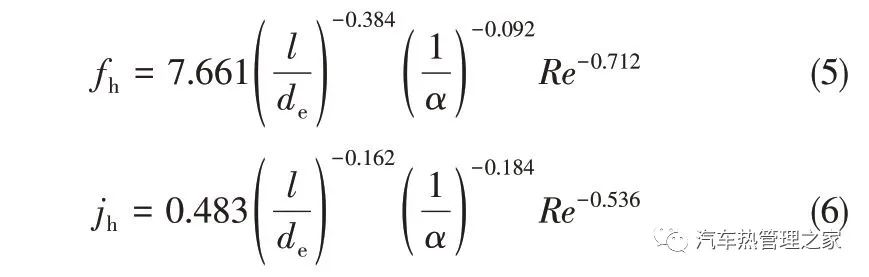
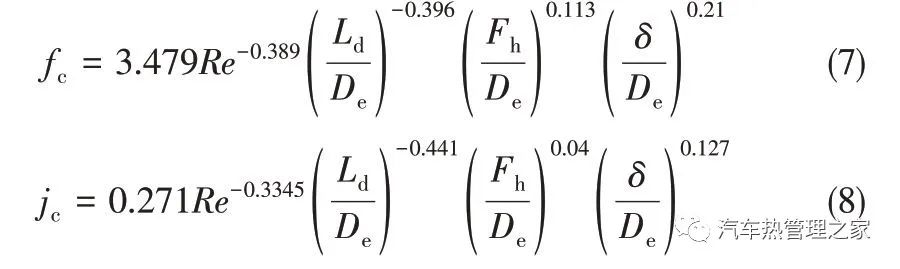
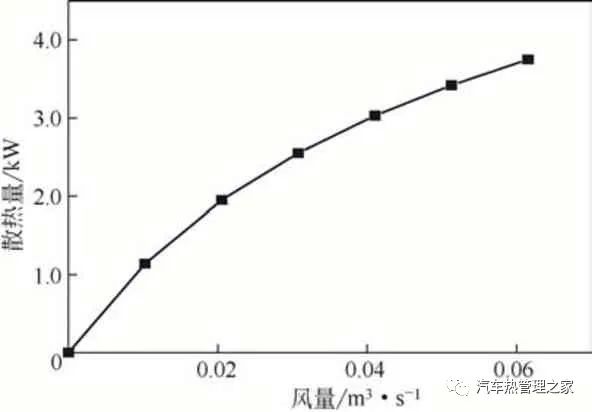

3 装机试验数据分析
3.1 试验平台介绍
所搭建的试验平台见图12,主要包括电池安装台架、5kW 甲醇重整燃料电池单元模块、电控系统、冷却系统、电池输出负载调节系统和电池监控系统。电池安装台架为铝合金框架结构,整体结构分为3层,上层为电控系统电路板安装;中层为燃料电池重整室、燃烧室、电堆等系统安装;下层为冷却系统的安装。 电池运行试验方法是将各模块安装好之后开机,根据电池监控系统显示的温度、压力等参数通过负载调节系统对电池进行自动或手动搭载,电池运行时通过电池监控系统监控各关键部位进出口的温度传感器、压力传感器采集信号,数据采集时间间隔为2s。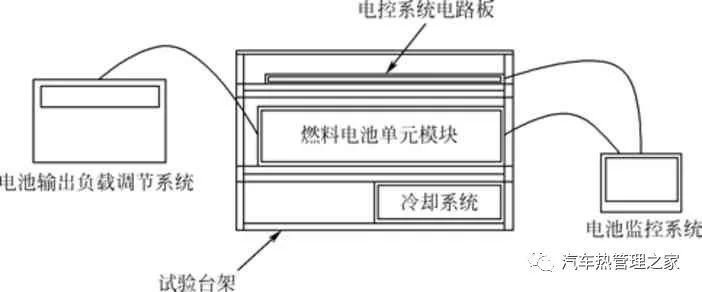
3.2 仿真温度曲线与实测温度曲线对比
利用搭建的Matlab/Simulink系统模型进行控制系统仿真运行试验,得到热侧介质温度曲线与电池实际工作热侧介质曲线如图13 所示。仿真系统中稳定工况温度设定为163℃,迭代运算中温度收敛于165.1℃。在此次实测中,温度稳定于163.5~165.5℃,实测温度误差基本可以稳定维持在±2℃以内,但仍然存在温度振荡幅度较大区域;电加热棒的局部加热作用使得电池预热时间短于预期值;实测温度趋势基本与系统仿真结果相同,因此该控制系统算法及仿真过程具有设计参考价值。3.3 热管理系统优化前后温度曲线对比
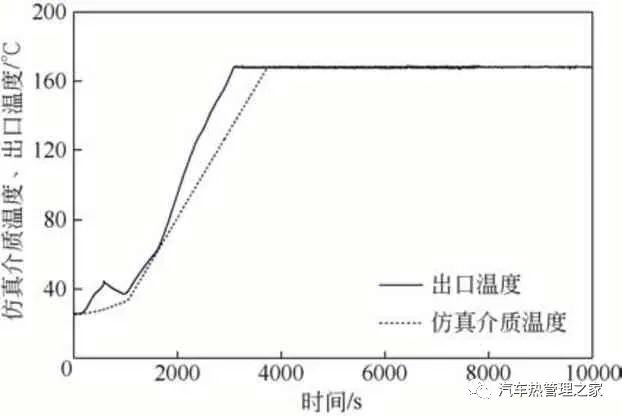
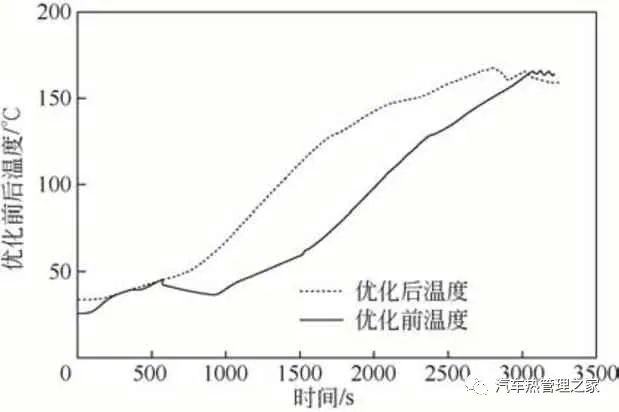
3.4 换热器温度均匀性测试
本系统散热器集成了电加热装置,进出口两侧每侧3根电加热棒,热源比较集中,因此在进出口型腔内部结构设计时需要考虑加热棒向介质的传热效率,避免局部温度过高引起的局部沸腾,同时也更为合理地利用能量,防止电能浪费。 本系统要求三乙二醇换热器进出口温差控制在10℃以内,实测三乙二醇进出口温差如图15所示,可以看出在一般工况下可以满足系统要求,但是在电池较长时间运行时进出口温差最大为12.5℃,因此对介质的流量控制函数是今后系统进一步优化的关键问题。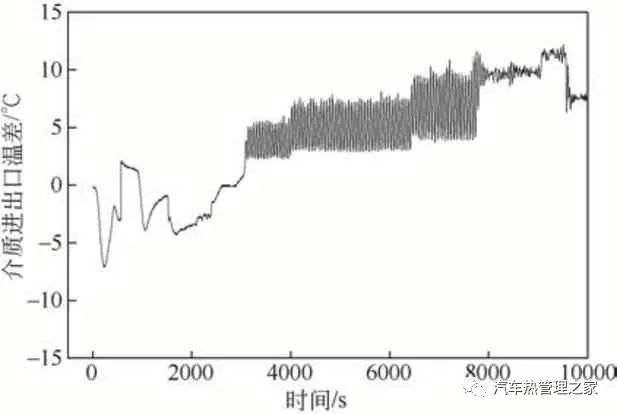

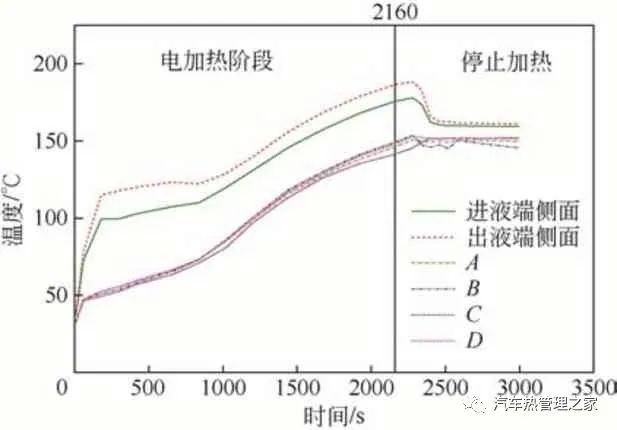
4 结论
(1)所提出的热管理系统控制方法在本系统中可以实现有效地控制介质温度,满足系统进出口温差及温度稳定性需求,缩短系统冷启动预热时间,可为今后热管理系统的控制系统设计提供参考依据。 (2)基于Matlab/Simulink 的热管理系统设计仿真结果与实测数据相比,结果表明,冷却介质温度趋势基本相同,温度误差在±2℃以内,达到系统设计要求。 (3)板翅式平行流换热器相较于肋板式换热结构具有明显性能优势,且避免温度分布均匀,进出口温度一致性高,是目前单模块燃料电池理想的换热结构。 (4)电加热系统集成到散热系统会带来随着温度升高温升速度变慢的问题。因此,双回路(加热回路、冷却回路)系统将成为今后燃料电池热管理系统的主要解决方案。 作者:李毅1,袁永熠1,2,廖中亮1 1湘潭大学机械工程学院 2苏州浩擎新能源科技有限公司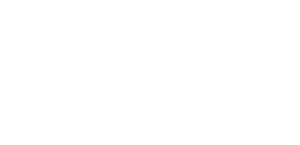
往猜你喜欢的文章
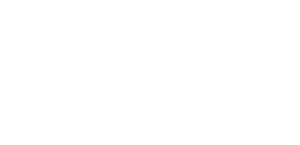

37页PDF燃料电池报告限时下载 | 燃料电池市场应用报告
干货&关于加氢设备技术76个问题与解答(值得收藏)
免费领取!氢燃料电池PPT合集(燃料电池/电堆系统/应用手册/双极板/质子交换膜/设计图)
收费报告!丰田Mirai、本田Clarity、现代NEXO最全资料合集!
燃料电池系统解析
氢能源汽车设计图PPT
DC/DC电源详解PPT
39页PPT氢燃料电池报告
燃料电池汽车系统安全防控分析
氢燃料发动机工作原理介绍PPT
44页PPT—燃料电池电动汽车
燃料电池应用手册(横河)JAPAN
氢燃料电池电堆系统控制方案pdf
氢燃料电池产业链分析(1)
氢燃料电池产业链分析(2)上游材料
氢燃料电池产业链分析(3)中游集成
氢燃料电池产业链分析(4)下游应用
63页PPT看懂燃料电池的分类及应用
63页PPT看懂质子交换膜燃料电池
一文搞懂燃料电池系统的设计与研究
36页PPT了解氢能与氢燃料电池产业链
PPT | 氢燃料汽车系统及部件结构详解
燃料电池电动汽车术语大全(含中英文对照)
106页PPT看懂燃料电池工作原理、分类及组成

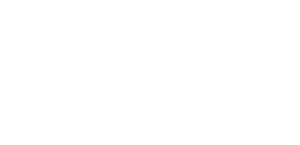
【免责声明】文章为作者独立观点,不代表旺材氢燃料电池立场。如因作品内容、版权等存在问题,请于本文刊发30日内联系旺材氢燃料电池进行删除或洽谈版权使用事宜。