摘 要:白车身典型截面的设计直接影响着整个白车身各项性能,在概念设计阶段,传统方法对如何设计典型截面具体尺寸可以提升白车身弯扭刚度、模态性能没有明确方向,对提升性能同时控制车身质量也没有系统研究。通过对标杆车白车身不同位置的典型截面设置几何参数,得到不同参数截面下白车身弯扭刚度、模态及质量的灵敏度结果,进而根据灵敏度结果,经过多轮多目标优化,提升弯扭刚度、模态,降低车身质量,在概念阶段给典型截面尺寸设计提供量化指导方向。该方法已经应用于传祺系列车型的开发应用中,实现了典型截面设计指导和减重降本的效果。
关键词:典型截面;多目标优化;概念设计阶段;弯扭刚度;模态;轻量化
1 引言
在轿车的概念设计阶段,如何有目标的正向量化设计轿车关键区域的典型截面一直是一个难题,通常情况都是单独的评价该典型截面的惯性参数,随着一些有限元技术的发展,把白车身简化成梁结构的有限元模型,然后根据梁结构的白车身简化模型进行灵敏度分析[1],国内外一些学者通过有限元法对车身梁截面尺寸进行了自动优化设计并已发表大量文章[2-8],也有学者从理论上用解析公式分析梁结构的截面参数和材料特性对其刚度的影响[9]。但少有人对典型截面的具体几何尺寸作为设计参数,同时考虑梁截面的几何尺寸对弯扭刚度、模态以及质量的影响,而这种设计思路,在整车开发流程中的概念设计阶段的正向开发中起着关键的作用,能够有效缩短设计开发流程,节约设计成本及试验验证成本。在车身开发概念设计阶段,引入了典型截面的几何尺寸作为参数变量,综合考量白车身典型截面的几何尺寸对弯扭刚度、模态以及质量的贡献度,通过多目标优化,求解最佳弯扭刚度及模态以及最小质量下的典型的截面尺寸,继而为新款车型的典型截面设计提供数据计算结果,作为指导方向,真正实现了概念设计阶段典型截面设计的全正向开发。
2 含截面参数的白车身有限元模型
现以广汽研究院某款车型为基础车型,建立有限元模型,模型以NASTRAN模板,焊点单元通过CWELD单元连接,焊缝单元通过 REB2 连接。选取其典型截面 SL06、SL07、SL08、SL12、SL13、SL15、SL16、SL17、SL19、SL20、SL21、SL23、SL32 以及 BO03、BO05、BO09,如图2所示。共16个,截面形状,如表1所示。输入图1中的白车身有限元模型到Meshworks软件中,作为同一平台车型的基础车型,建立实体网格控制单元,如图2所示。图2中的实体单元作为控制单元包裹参数所在的白车身典型截面梁区域,如图3所示。
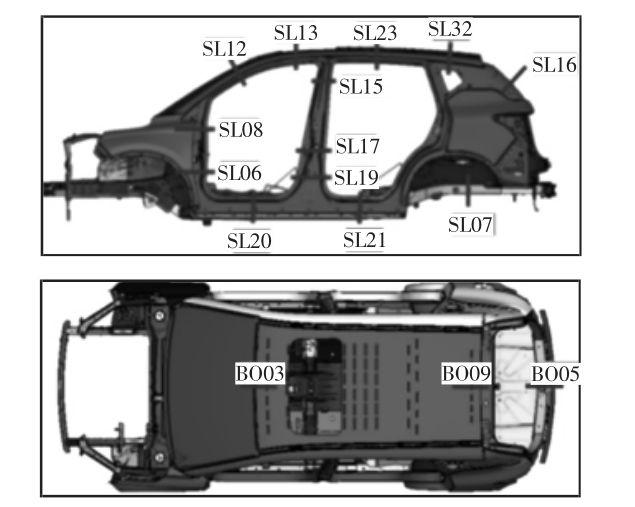
图1 白车身及其关键的典型截面
Fig.1 BIW and Typical Section
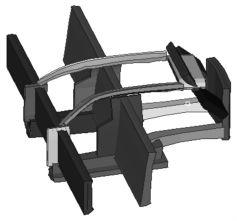
图2 形状控制单元
Fig.2 Shape Prarmeters of Control Element
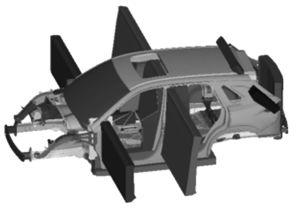
图3 含22个形状参数的白车身有限元模
Fig.3 BIW Model with 22 Shape Parameters
通过Morph功能改变上述截面的尺寸,这些尺寸的改变通过定义16个截面的几何形状参数来实现,该基础车型不同位置的典型截面,如表1所示。
表1 基础车型不同位置的典型截面
Tab.1 Typical Section of Different Position in Base Model