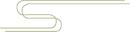
由于铸轧过程熔体流动和凝固传热更加复杂,铸坯质量的控制难度增加,铸轧工艺参数的可调范围减小,铸轧工艺参数的合理匹配已成为制约实现快速超薄铸轧,获得高质量铸坯的一个关键问题。高性能铝合金具有高的室温强度和良好的综合力学性能,已广泛应用于航空、国防、高铁等领域。由于高强铝合金在锻造变形过程中温度不均匀产生裂纹等缺陷,严重影响了铝合金的质量,因此,研究高强铝合金裂纹等缺陷的产生机理,确立抑制成形过程组织缺陷的调控方法,对于获得高质量铝合金具有重要的意义。
老路推荐这本书可以系统的学习一下《铝及铝合金铸轧成形与裂纹扩展》
图书特点:


系统地研究分析了铝及铝合金铸轧成形与裂纹扩展规律及其影响因素。基于元胞自动机法(CA),采用LGK模型模拟了晶粒生长的动态演变,用基于正态分布的形核模型和KGT生长模型,对铝铸轧凝固过程中晶粒的生长及微观组织的形成进行了模拟,模拟结果有助于从理论角度解释微观组织中出现枝晶间偏析、点偏析及微观缩松等缺陷的形成原因。基于有限元法(FEM),建立了铝铸轧过程整体模型,分析了铸轧参数对铸轧过程的影响。基于损伤理论,研究了辊套疲劳寿命预估。基于有限差分法(FDM),建立了铸嘴的流动模型,分析了铸轧参数对铸嘴型腔熔体流动、出口速度及出口温度的影响。通过水模试验及铸轧过程试验验证了模拟的有效性。基于分子动力学法(MD),采用嵌入原子势法(EAM),模拟了铝裂纹扩展行为,从裂纹扩展图观察到裂纹扩展的变化情况:裂纹尖端钝化、子裂纹的产生、孔洞的生成及长大过程以及裂纹和孔洞的汇集;探讨加载速度和初始裂纹长度对体系裂纹扩展行为的影响;分析了孔洞大小、数量及分布对铝裂纹扩展行为的影响;模拟铝合金粗大第二相Al2Cu拉伸变形行为,发现Al2Cu非常脆,应变ε=0.086时应力达到峰值6.4GPa,在拉伸初期不易产生位错,从而弹性变形阶段较长;探讨温度和应变率对体系拉伸变形行为的影响;分析了孔洞数量及分布对Al2Cu拉伸变形行为的影响。基于均匀化方法,建立了铝合金细观结构的数学模型,对铝合金细观结构响应进行了分析;并分析了温度、孔洞数量对裂纹扩展的影响。对7050铝合金进行均匀化热处理,分析热变形参数对7050铝合金流变应力的影响;通过热变形参数对微观组织演化规律的影响,对高温塑性变形条件下的变形机制进行研究。
拖动右侧滚动条可以查看全目录
▼
◆ 目录:◆
前言
第1章绪论1
1.1铝及铝合金铸轧成形与裂纹扩展研究意义1
1.2铝及铝合金铸轧成形与裂纹扩展研究发展状况1
1.2.1铝及铝合金铸轧成形研究发展状况1
1.2.2铝合金裂纹扩展研究发展状况4
1.3铝及铝合金铸轧成形与裂纹扩展数值方法及其研究发展状况5
1.3.1元胞自动机法5
1.3.2有限元法7
1.3.3有限差分法8
1.3.4分子动力学法9
1.4本章小结12
第2章基于元胞自动机的铝铸轧微观数值模拟13
2.1概述13
2.2微观组织数值模拟的元胞自动机模型14
2.2.1形核模型14
2.2.2生长模型15
2.2.3溶质扩散模型18
2.2.4元胞自动机法的捕获法则22
2.3基于元胞自动机的微观组织数值计算方法23
2.3.1晶粒生长的数值计算方法23
2.3.2微观组织形成的数值计算方法25
2.3.3边界条件的确定及相对运动的处理26
2.4程序方案设计27
2.4.1晶粒生长的程序方案设计27
2.4.2微观组织形成的程序方案设计28
2.5基于元胞自动机的微观组织数值模拟30
2.5.1基于元胞自动机的晶粒生长数值模拟31
2.5.2基于元胞自动机的微观组织形成数值模拟33
2.6本章小结36
第3章基于有限元的铝铸轧成形过程数值模拟38
3.1概述38
3.2铝铸轧成形过程数学模型及其求解38
3.2.1铸轧成形过程数学模型的建立38
3.2.2一些重要工艺参数的处理43
3.2.3边界条件的确定47
3.2.4数值计算47
3.3铝铸轧成形过程数值模拟分析48
3.3.1铸轧区流场、温度场、热应力场及热应变场48
3.3.2铸轧辊辊套温度场与热应力场49
3.4铝铸轧参数对铸轧过程的影响51
3.4.1铸轧参数对铸轧区流场的影响51
3.4.2铸轧参数对铸轧区温度场的影响53
3.4.3铸轧参数对铸轧区热应力场的影响56
3.4.4铸轧参数对铸轧区热应变场的影响58
3.4.5铸轧参数对铸轧辊温度场的影响60
3.4.6铸轧参数对铸轧辊热应力场的影响62
3.5本章小结65
第4章基于损伤力学的铸轧辊辊套疲劳寿命研究66
4.1概述66
4.2损伤力学理论 67
4.2.1含损伤材料本构关系 67
4.2.2损伤演化方程 68
4.2.3理论理想疲劳曲线 69
4.2.4损伤参数确定 70
4.3裂纹形成与扩展的损伤力学方法71
4.3.1疲劳损伤耦合理论 71
4.3.2损伤力学——有限元法 72
4.4辊套疲劳寿命预估74
4.4.1辊套的应力场分析74
4.4.2辊套疲劳寿命预测77
4.5本章小结79
第5章基于有限差分的铸轧过程铸嘴型腔流动数值模拟80
5.1概述80
5.2铸轧过程铸嘴型腔熔体数学模型及其求解80
5.2.1铸轧过程铸嘴型腔熔体数学模型80
5.2.2铸轧过程铸嘴型腔熔体求解89
5.3铸轧过程铸嘴型腔熔体流动与传热数值模拟90
5.3.1铸嘴型腔熔体流动与传热分析90
5.3.2铸轧参数对型腔流场出口速度、出口温度的影响94
5.4铸嘴布流调节过程型腔熔体流动与传热数值模拟102
5.4.1超薄供料型腔非定常流特点及其处理方法102
5.4.2超薄供料型腔非定常流数学模型103
5.4.3超薄供料型腔非定常流数值仿真分析104
5.5本章小结111
第6章铝铸轧试验研究112
6.1布流系统水模试验112
6.1.1试验的基本准则112
6.1.2试验方案及实施114
6.1.3试验结果与分析116
6.2铸轧过程试验及组织分析119
6.2.1试验方法119
6.2.2试验结果与分析120
6.3本章小结125
第7章基于分子动力学的铝及铝合金裂纹扩展数值模拟127
7.1概述127
7.2分子动力学的基本原理和模拟方法127
7.2.1分子动力学的基本原理127
7.2.2LAMMPS简介135
7.3铝裂纹扩展行为的分子动力学模拟136
7.3.1不含孔洞的铝裂纹扩展行为的分子动力学模拟136
7.3.2含孔洞的铝裂纹扩展行为的分子动力学模拟140
7.4铝合金拉伸变形的分子动力学模拟146
7.4.1Al2Cu拉伸的分子动力学模拟146
7.4.2含孔洞的Al2Cu拉伸的分子动力学模拟153
7.5本章小结159
第8章基于有限元的铝合金细观结构响应及裂纹扩展数值模拟161
8.1概述161
8.2基于均匀化方法的铝合金细观结构响应分析161
8.2.1铝合金细观结构的数学模型161
8.2.2铝合金缺陷细观结构有限元建模165
8.2.3结果与讨论166
8.3铝合金裂纹扩展数值模拟173
8.3.1模型的建立173
8.3.2铝合金裂纹扩展过程中裂纹前缘应力场的数值模拟174
8.3.3复杂载荷作用下裂纹扩展与分析177
8.4本章小结181
第9章铝合金高温塑性变形条件下的变形机制183
9.1概述183
9.27050铝合金热处理183
9.2.1试验材料与试验方案183
9.2.2试验结果与分析184
9.37050铝合金的热压缩试验188
9.3.1试验材料与方法188
9.3.2不同变形条件下7050铝合金真应力-真应变曲线189
9.3.3热变形参数对7050铝合金流变应力的影响及流变应力本构方程192
9.4高温塑性变形条件下7050铝合金微观组织的演化196
9.4.17050铝合金微观组织特征196
9.4.27050铝合金在不同变形程度下微观组织的演化规律197
9.4.37050铝合金在不同变形温度下微观组织的演化规律199
9.4.47050铝合金在不同应变速率下微观组织的演化规律200
9.5本章小结202
参考文献203
热门图书排行
☞金粉最爱图书排行
☞机械图书排行
☞生产管理排行
☞设计软件排行
☞最新上架
欢迎加入金粉商城,机械人专享的商城