弯曲是利用压力使金属板料,管料,棒料或型材弯成一定的曲率,一定角度和形状的变形工序.弯曲工艺在冲压生产中占有很大的比例,应用相当广泛,如汽车纵梁,电器仪表壳体,支架,门搭铰链等,都是用弯曲方法成形的.
弯曲成形既可以利用模具在压力机上进行,也可以在其他专用设备,如弯板机,弯管机,滚弯机上进行.这些弯曲方法尽管使用的毛坯料和采用的工具及设备各不相同,但它们弯曲时的变形规律是一样的.
1. 弯曲的变形过程
图3.1-1所示为板料弯曲成V形件的成形过程.在弯曲开始阶段,当凸模下压与板料接触时,在此接触部分便加上了集中载荷,此载荷与对毛坯起支撑作用的凹模肩部的支撑力构成弯矩,使毛坯产生弯曲.随著凸模的下压,毛坯与凹模工作表面逐渐靠紧,弯曲半径由r0变为r1,弯曲力臂也由L0/2变为L1/2;凸模继续下压,毛坯弯曲半径继续减小,直到毛坯与凸模三点接触,此时曲率半径已由r1变为r2,毛坯的直边部分开始向回弯曲,逐步贴向凹模工作表面,到行程终了时,凸﹑凹模对毛坯进行校正,使其圆角﹑直边与凸模全部贴合,最终形成V形弯曲件.
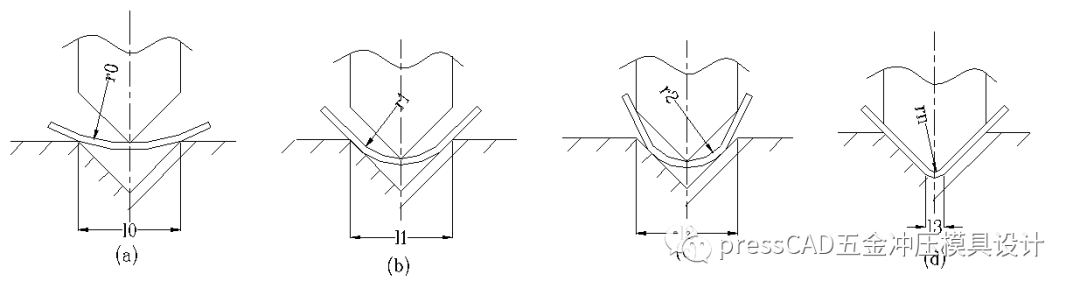
图3.1-1 弯曲过程
2. 弯曲的变形特点
为了分析板料在弯曲时的变形情况,可在一定厚度的板料侧面画出正方形网格,然后将板料进行弯曲,如图3.1-2所示.
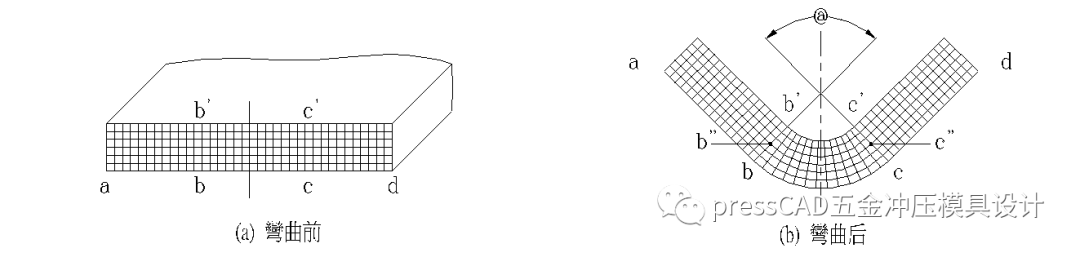
观察网格的变化,可以看出弯曲时变形的特点﹕
(1) 弯曲时,在弯曲角(α)的范围内,网格发生显著变化,而直边部分网格基本不变.因而可知,弯曲变形仅发生在弯曲件的圆角部分,直边部分不产生塑性变形,即弯曲时,圆角部分是变形区,直边部分是不变形区.
(2) 分析网格的纵向线条可以看出,变形区内侧网格线缩短,外侧网格线伸长,即在弯曲变形区内,縴维沿纵向变形是不同的.内侧材料沿纵向受到压缩,外侧材料受到拉伸,且压缩与拉伸的程度都是表层最大,向中间逐渐减小.在内,外侧之间必然存在著一个长度保持不变的中性层.
(3) 弯曲变形区的断面形状变化由图3.1-3可见,变形有两种情况.
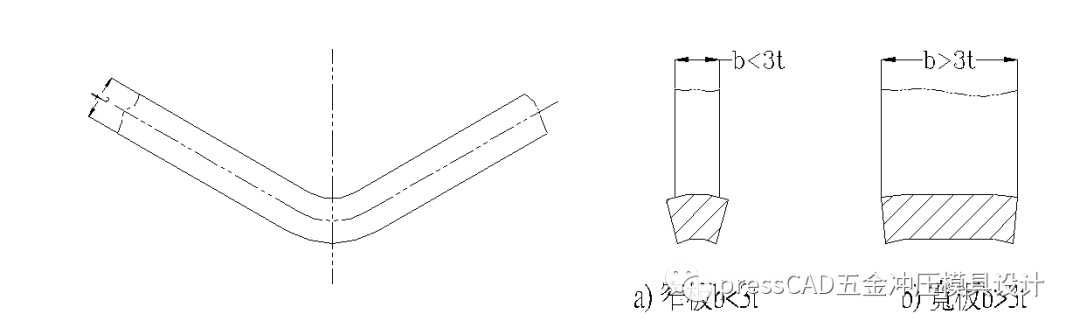
窄板(b<=3t)变形区断面畸变明显,由原来的矩形弯成上大下小的扇形,见图3.1-3 a).这是由于内侧金属受纵向压缩,内层材料必向宽度方向流动,使工件的横向宽度增加,外层材料受到切向拉伸后,材料之不足便由宽度,厚度方向来补充,致使宽度变窄.
(b) 宽板(b>3t)变形区断面无明显变化,仍为矩形,见图(3.1-3b).这是由于板料宽度较宽,在宽度方向不能自由变形所致.
(4) 弯曲变形区内毛坯厚度有变薄现象.无论是窄板还是宽板,其原始厚度t0变薄为t1.由于宽板弯曲时,宽向不能自由变形,而变形区又变薄,故其长度方向必然会增加.
此外,弯曲后工件的角度和圆角半径也往往与模具不一致.
2 弯曲零件的工艺性对弯曲件的工艺分析应遵循弯曲过程变形规律,通常主要考虑如下几个方面:
1. 最小弯曲半径
材料产生塑性变形才能形成所需的形状,为了实现弯曲件的形状,弯曲圆角半径最大值是没有限制的.例如,可以将0.3MM厚的铁板卷成300MM的圆桶,只需要计算或试验出其回弹量,就可制出所需的形状.
但板料弯曲的最小半径是有限制的,如果弯曲半径过小,弯曲时外层材料拉伸变形量过大,而使拉应力达到或超过抗拉强度,则板料外层将出现断裂,至使工件报废.因此,板料弯曲存在一个最小圆角半径允许值,板料弯曲圆角半径不应小于此值.
当弯曲件有特殊要求,其圆角半径必须小于最小弯曲圆角半径时,可设法提高材料的塑性,例如将材料退火或在加热状态下弯曲,在冲压工艺安排和模具设计上也可以采取一些方法,如厚板弯曲时要求弯曲半径小,可采用预先开槽或压槽的方法,使弯曲部位的板料变薄,能防止弯曲部位开裂.如图3.2-1所示.
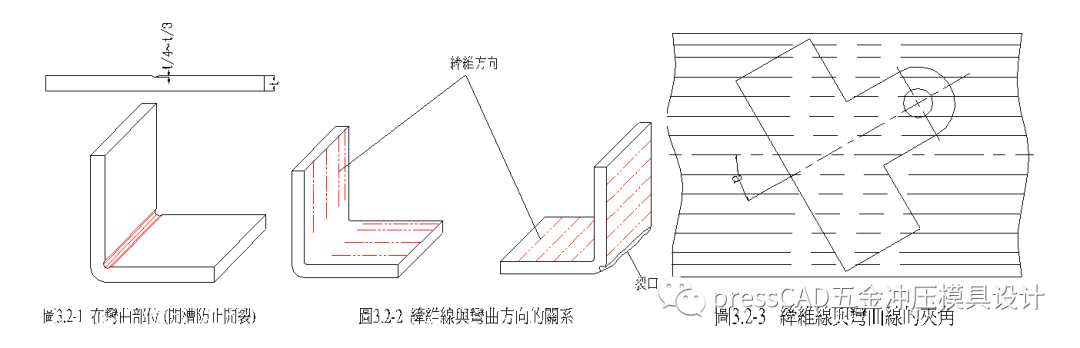
2. 弯曲件的縴维方向
用于冷冲压的材料大都属于轧制板材,轧制的板材在弯曲时各方向的性能是有差别的,縴维纹的方向就是轧制的方向.对于卷料或长的板料,縴维线与长边方向平行.作为弯曲用的板料,材料沿縴维线方向塑性较好,所以弯曲线最好与縴维线垂直.这样,弯曲时不容易开裂,如图3.2-2所示.
如果在同一零件上具有不同方向的弯曲,在考虑弯曲件排样经济性的同时,应尽可能使弯曲线与縴维方向夹角a不小于30度,如图3.2-3所示.
3. 弯曲件的最小弯曲高度
在进行直角弯曲时,如果弯曲的直立部分过小,将产生不规则变形,或称为稳定性不好.为了避免这种情况,应当如图3.2-4所示,使直立部分的高度H>2.5t.当H<2.5t时,则应在弯曲部位加工出槽,使之便于弯曲,或者加大此处的弯边高度H,在弯曲后再截去加高的部分.
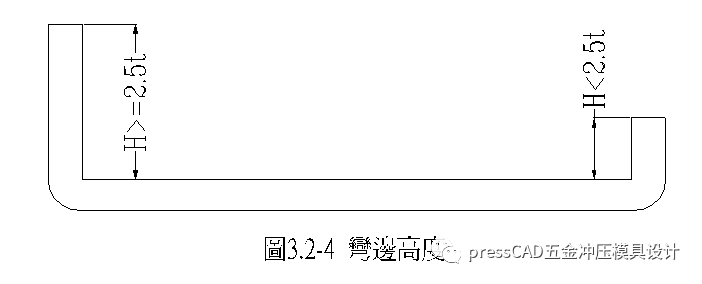
4. 弯曲件的工艺孔﹑槽及缺口
在一些弯曲工件的工艺设计中,为了防止材料在弯曲处因受力不均匀而产生裂纹,角部畸变等缺陷,应预先在工件上设置弯曲工艺所要求的孔,槽或缺口,即所谓工艺孔,工艺槽或工艺缺口.压弯后难以形成理想的直角,甚至将产生裂纹或使支架在H处变宽.若在该处弯曲前加工出M*N的缺口,则能得到较好的弯曲成形.在弯曲处K预冲工艺孔可以防止偏移,得到正确的形状和尺寸.
对于需经过多次弯曲才能成形的工件,可增加定位工艺孔,作为压弯工序的定位基准,这样虽然经过多次弯曲工序,仍能保証其对称性和尺寸要求.
5. 弯曲件的孔与弯曲处的最小距离
工件在弯曲线附近有预冲出的孔,在弯曲后由于弯曲时材料的流动,会使原有的孔变形.为了避免这种情况,必须使这些分布在变形区以外的部位.设孔的边缘至弯曲半径R中心的距离为l,则应满足下列关系:
当t<2mm时,l>=t.
当t>2mm时,l>=2t.
工件不能满足上述要求时,可采用其它的方法,以保証孔形的正确性.
6. 弯曲件的冲裁毛刺与弯曲方向
弯曲件的毛坯往往是经冲裁落料而成的.其冲裁的断面一面是光亮的,另一面是有刺的.弯曲件尽量使有毛刺的一面作为弯曲件的内侧,如图3.2-5a所示,当弯曲方向必须将毛刺面置于外侧时,应尺量加大弯曲半径,如图3.2-5b所示.
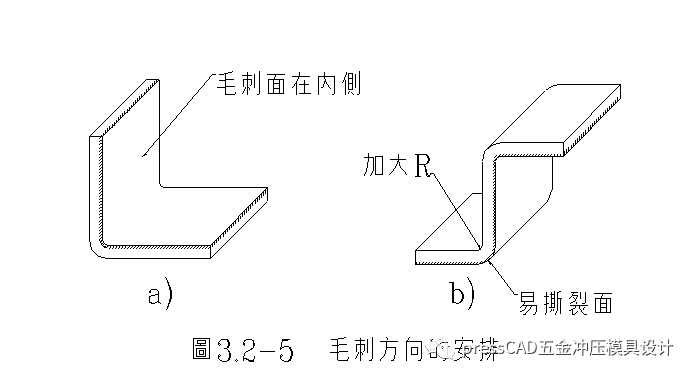
板料弯曲时,应变中性层的长度是不变的.因此,弯曲件毛坯尺寸可以根据弯曲变形前后应变中性层长度不变的原则来计算确定.
1. 弯曲件中性层的确定
当板料弯曲变形时,在弹性阶段中性层位于板厚的中间,冲压工件的弯曲变形主要是塑性变形.其中性层的位置.往往向弯曲的内侧偏移.如下图3.3-1所示.
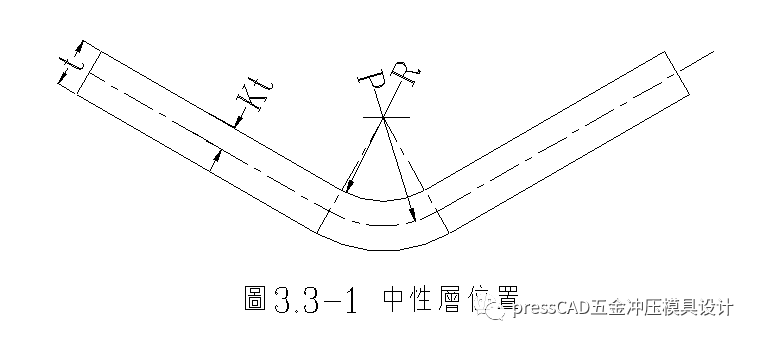
此时中性层半径的大小可按下式计算.
ρ=R+Kt
式中
ρ------中性层半径(mm)
R------弯曲内半径(mm)
K------中性层位置因数(mm)
t-------材料厚度(mm)
2. 弯曲件毛坯长度的计算
中性层位因数k可由下表3.3-1查出,当中性层半径确定以后,就可以按照几何方法计算中性层展开长度.进而计算出板料的展开长度.由于材料的性能和弯曲方法的不同,中性层一般通过试弯来确定,也可查阅有关计算资料.
表3.3-1中性层位置因数K与R/t比值的关系

弯曲力是指工件完成预定弯曲时需要压力机所施加的压力.弯曲不仅与材料品种,材料厚度,弯曲几何参数有关,并且同设计弯曲模所确定的凸、凹模间隙大小等因素有关.
1. 自由弯曲力的计算
V形弯曲件的计算:
F1=0.6 KB 2σb/R+t
U形弯曲件的计算:
F1=0.7 KB 2 /R+t
式中﹕
F1------自由弯曲力(冲压行程结束,尚未进行校正弯曲时的压力)(N);
B------弯曲件宽度(mm);
t------弯曲件材料厚度(mm);
R------弯曲内半径(mm);
σb------材料抗拉强度(Mpa);
K------安全因数,一般取k=1.3
2. 校正弯曲力的计算
校正弯曲的弯曲力计算公式:
F2=qA
表3.4-1所列数据是弯曲件校正所需要的压力.而实际压力值取决于压力机的调整和材料板厚的误差.
表3.4-1单位校正力q(Mpa)
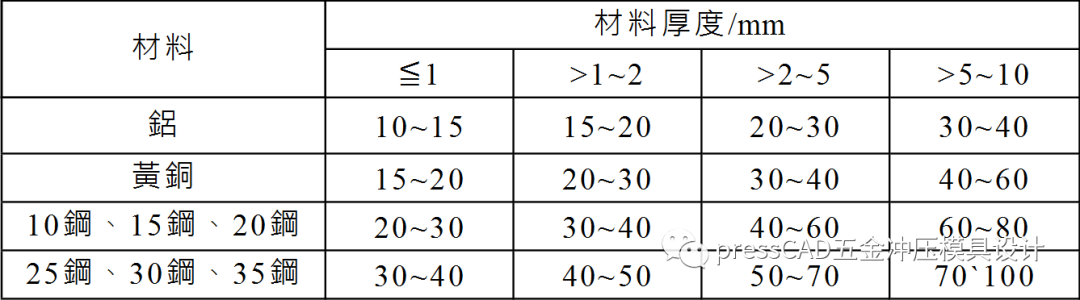
弯曲时压力机的压力是自由弯曲力与校正弯曲力之和.
F≧F1+F2
即式中F----压力机的压力.
校正弯曲时由于校正弯曲力比自由弯曲力大得多.故F1可以忽略,而F2的大小取决于压力机的调整.
5 弯曲件的回弹1. 回弹的定义
压弯过程并不完全是材料的塑性变形过程,其弯曲部位还存在著弹性变形,所以,压弯后制件的形状与模具的形状并不完全一致.这种现象称为回弹.回弹的大小通常用角度回弹量△θ和曲率回弹量△ρ来表示.角度回弹是指模具在闭合状态时工件弯曲角与从模具中取出后工件的实际角度θ0之差.即△θ=θ0 -θ;曲率回弹是指模具处于闭合状态时压在模具中工件的曲率半径ρ与模具中取出以后工件的实际曲率半径ρ0之差.即:△ρ=ρ0-ρ
2. 影响回弹的因素
(1) 材料的力学性能 回弹角的大小与材料的屈服点σs成正比,与弹性模量E成反比.
(2) 材料的相对弯曲半径R/t 当其他条件相同时R/t值越小,则△θ/θ与△ρ/ρ也越小.
(3) 弯曲的工件的形状 一般U形工件比V形工件回弹要小,回弹量与工件弯曲半径也有关,当比值R/t<0.2~0.3时,则回弹角可能为零.甚至达到负值.
(4) 模具间隙 U形弯曲模的凸凹模单边间隙Z/2越大则回弹也越大;Z/2
(5) 校正力 增加校正力可减小回弹量,对弯曲半径小(R/t<0.2~0.3)的V形工件进行校正弯曲时,角度回弹量可能为负值或零.
3. 回弹的确定
如前所述,由于影响回弹数值的因素很多,而且各因素往往又相互影响.故不能进行精确的计算或分析,在一般情况下,设计模具时对回弹量的确定大多按照经验值,或计算后在实际模具中再进行修正.
只有当弯曲工件的圆角半径R≧(5~8)t时,计算才近似正确.当要求工件的弯曲圆角直径为R时,则可根据材料有关参数.用下列公式计算弯曲模的圆角半径回弹补偿值.
板材弯曲用右式计算 R凸=R/(1+3σsR/Et)
棒材弯曲用右式计算 R凸=R/(1+3.4σsR/Ed)
式中R R凸-------弯曲件弯曲模圆角半径(mm)
σs-------材料屈服点(Mpa)
E-------材料弹性模量 d-------棒材直径(mm)
当R
表3.5-1 V形弯曲回弹角(见图3.5-1)
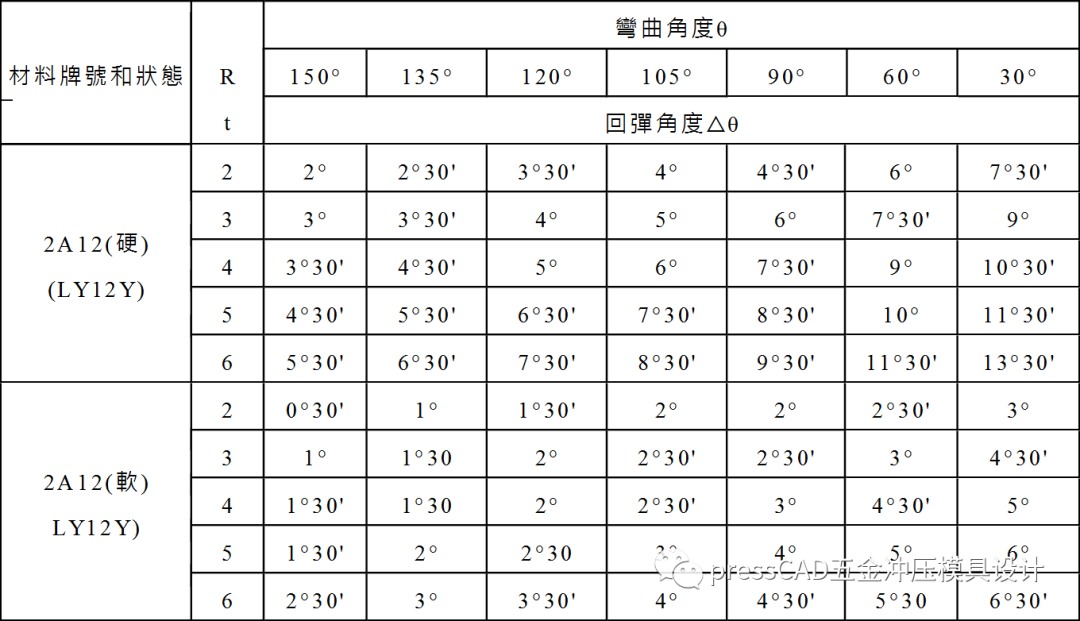
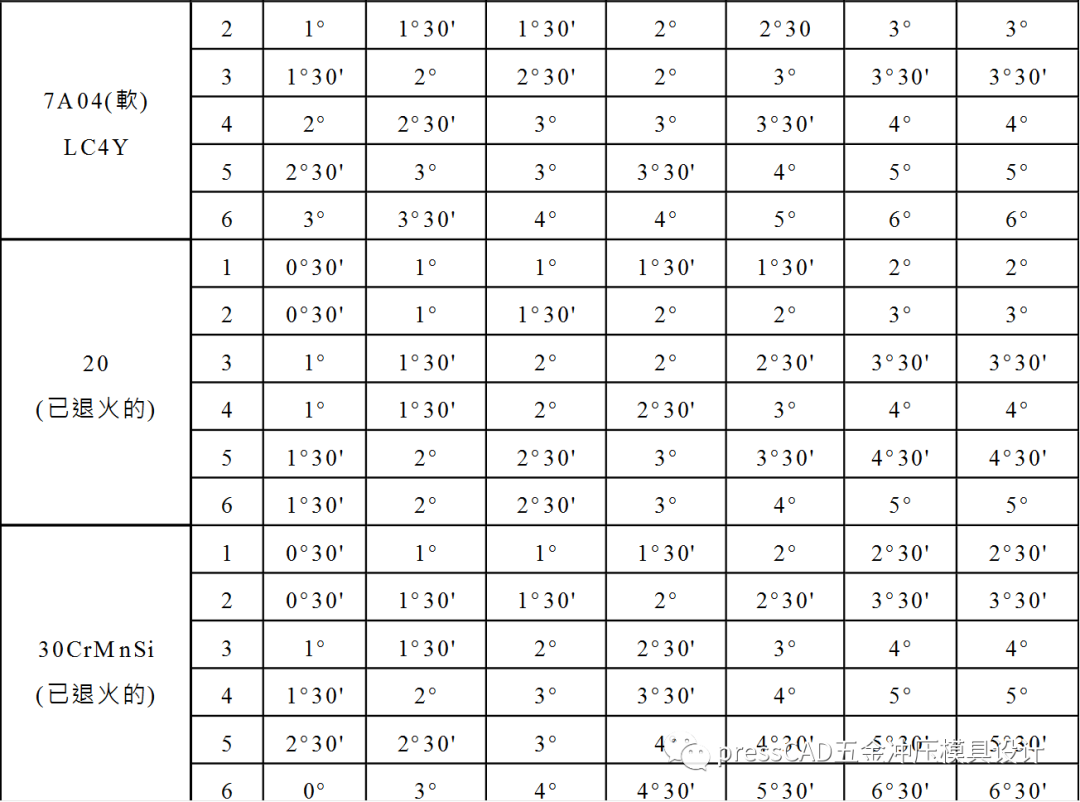
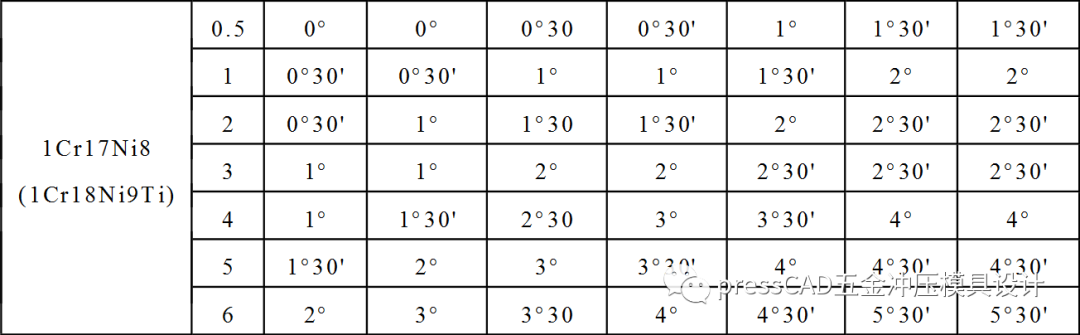
表3.5-2 U型弯曲回弹角(见图3.5-2)
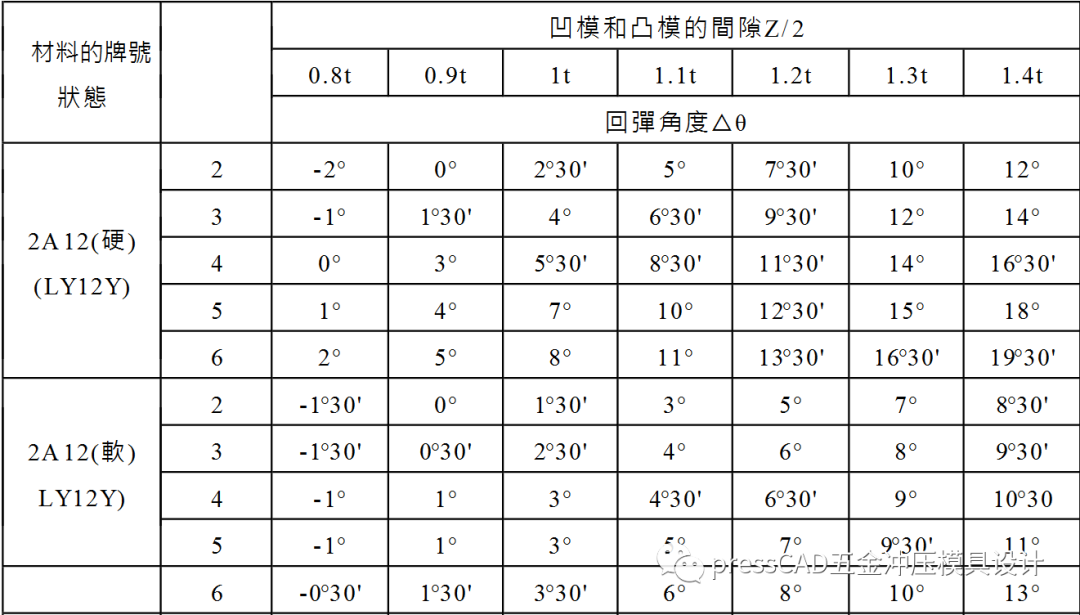
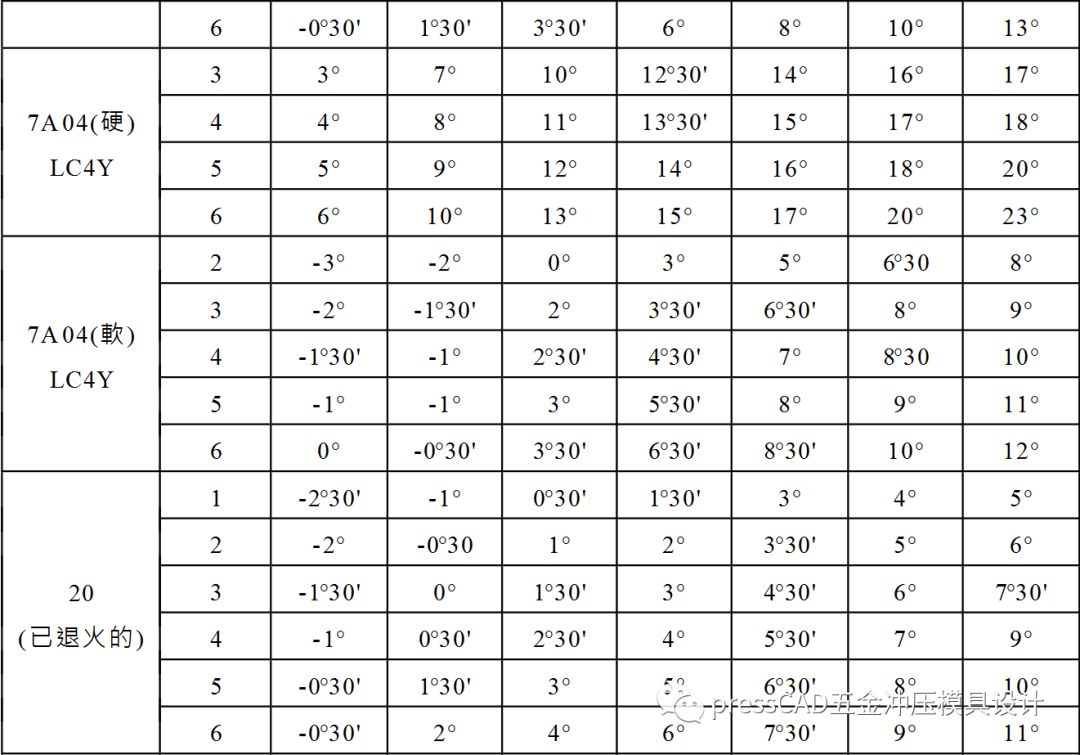
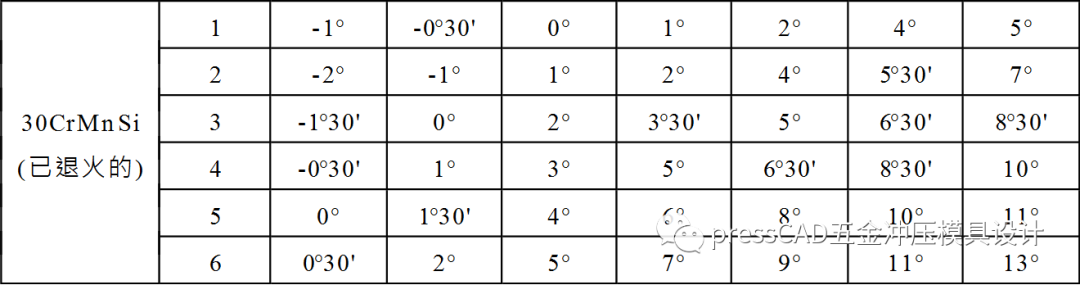
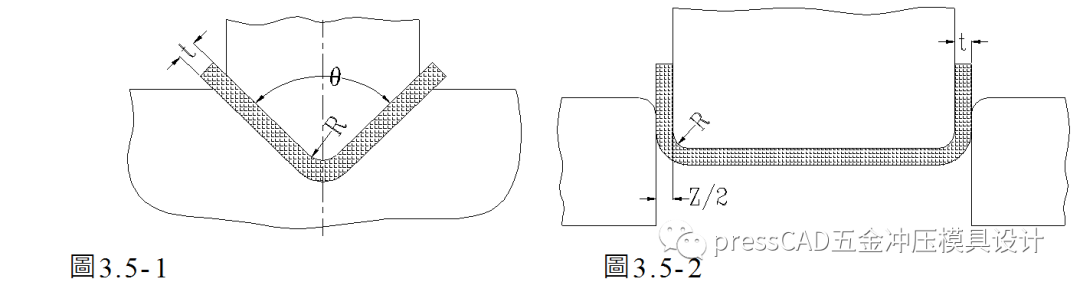
4. 减少回弹的措施
弯曲加工必然要发生回弹现象.如前所述,回弹大小与弯曲的方法及模具结构等因素有关,要完全消除回弹是极其困难的.消除回弹,常用的方法有补偿法和校正法.
(1) 补偿法: 补偿法要预先估算或试出工件弯曲后的回弹量,在设计模具时使工件的变形超出原设计的变形.冲压回弹后得到所需要的形状.
图3.5-3a所示为角回弹的补偿,根据已确定的回弹角,在设计凸模和凹模时减小模具的角度,作出补偿.图3.5-3b所示的情况采取两种措施:其一是使凸模向内侧倾斜;其二是使凸凹模单边间隙小于材料厚度,凸模将板料压入凹模后,利用板料的两侧都向内贴紧凸模,凸凹模分离后,工件回弹,两边恢复垂直.图3.5-3c所示,弯曲件在模具内底部凹入,出模的工件圆弧部分回弹为直线,同时其两侧也就向内侧倾斜使回弹得到补偿.
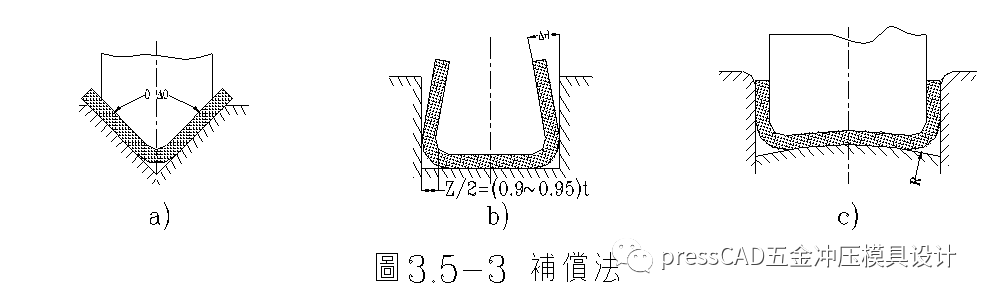
校正法:校正法是在模具结构上采取措施,让校正压力集中在弯角处,力求消除弹性变形,克服回弹.
图3.5-4a,b所示为弯曲校正力集中作用在较小的接触面积,使工件的圆角部分材料变薄,达到消除回弹效果.
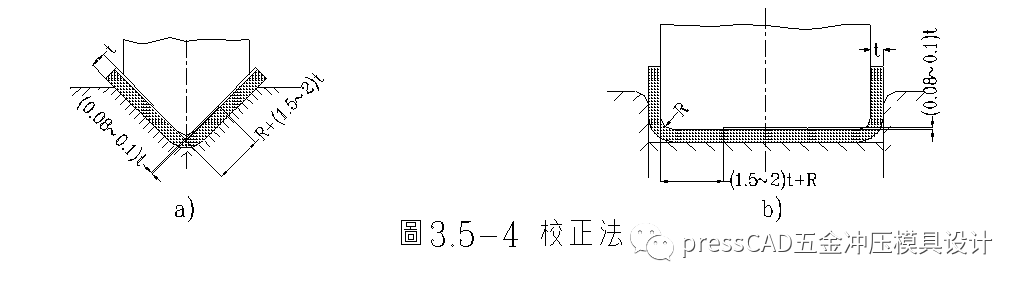
1. 弯曲模设计要求
弯曲模结构设计应在选定弯曲工艺方案的基础上进行.为了保証达到制件的要求,在进行弯曲模结构设计时,必须注意以下几点:
(1) 毛坯放置在模具上应保証可靠的定位;
(2) 在弯曲过程中,应防止的滑动和偏移;
(3) 为了减少和消除弯曲后的回弹,在变形结束时应使制件在模具中得到校正;
(4) 弯曲模的结构应考虑到制造和维修中消除回弹的可能;
(5) 毛坯放到模具上和弯曲成形后从模具中取出应方便;
2. 常见弯曲件的模具结构
(1) V形件弯曲模;
(2) U形件弯曲模;
(3) 圆筒形件弯模;
(4) 铰链件弯曲模;
3. 弯曲模工作部分尺寸计算
弯曲时凸模与凹模之间的间隙,弯曲V形工件时,凸凹模间隙是靠调整压力机闭合高度来控制的,不需要在模具结构上确定间隙,U形件的弯曲,则必须选择适当的间隙,间隙的大小对于工件质量和弯曲力有很大影响,间隙越小,弯曲力越大.间隙过小,会使工件壁变薄,并降低凹模寿命.间隙过大则回弹较大,还会降低工件的精度.
(1) 弯曲模工件部分尺寸计算﹕
弯曲有色金属时,间隙值用下式计算
Z/2=Tmin+nt
弯曲黑色金属时,间隙值用下式计算
Z/2=t(1+n)
式中Z/2------凸、凹模间的单面间隙
Tmin------材料的最小厚度;
t------材料的公称厚度;
n------因数,其与弯曲件高度H和弯曲线长度B有关,见表
表3.6-1 因数n值
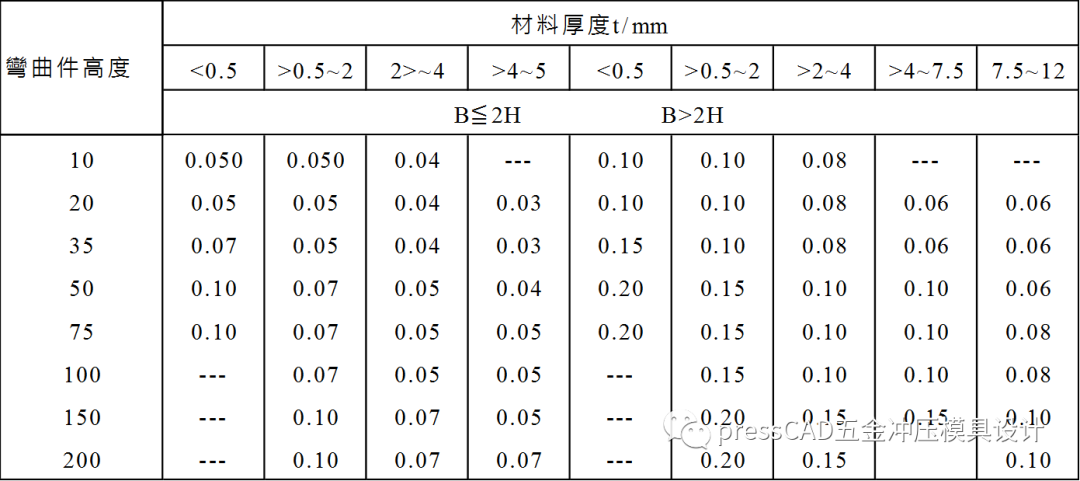
) 凸凹模工作部位尺寸.由于弯曲件尺寸的标注和尺寸的充许偏差不同,所以凸凹模工作部位尺寸的计算方法也不同.
对于表示外形有正确尺寸的工件,其模具的尺寸如图3.6-1所示,计算公式如下:
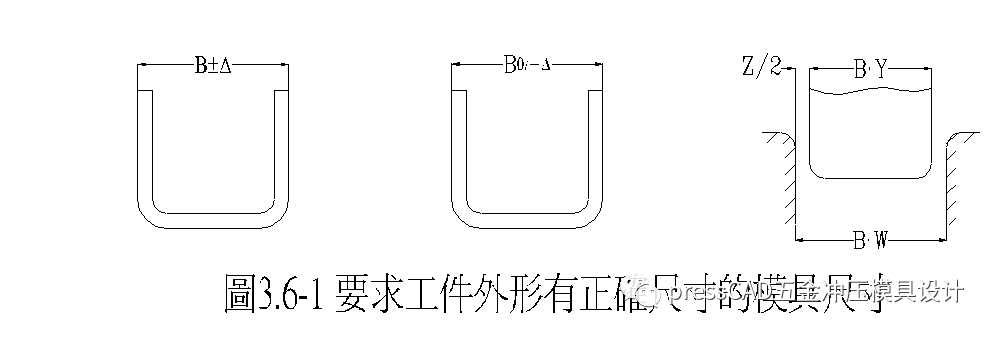
零件尺寸标注双向偏差时,凹模尺寸为
B凹=(B-1/2△)+δ0凹
零件尺寸标注单向偏差时,凹模尺寸为
B凹=(B-3/4△)+δ0凹
凸模尺寸B凸根据单面间隙Z/2按凹模尺寸配制.
图3.6-2所示为要求内形有正确尺寸的工件
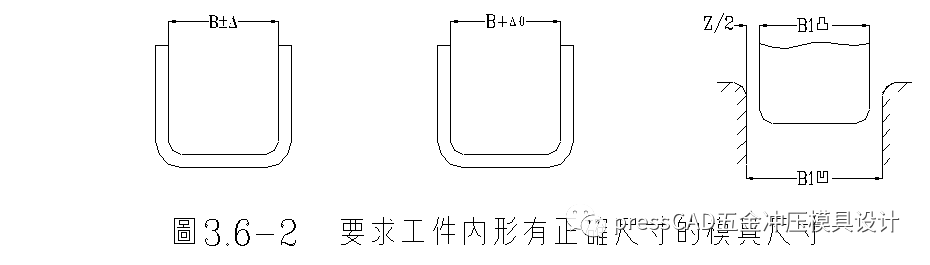
零件尺寸标注双向偏差时,凸模尺寸为
B1凸=(B1+1/2△)-δ0凸
零件尺寸标注单向偏差时,凸模尺寸为:
B1凸=(B1+3/4△)-δ0凸
凹模尺寸B1凹应根据单面间隙Z/2按凸模配制.
式中B凹、B1凹------凹模工作部位尺寸(mm);
B凸、B1凸------凸模工作部位尺寸(mm);
B、B1------弯曲件的尺寸(mm);
△------弯曲件的尺寸公差:(mm);
Z------凸模与凹模的双面间隙(mm);
δ0凸、δ0凹------凸模、凹模的制造偏差(mm);
(3) 模具圆角半径的确定
a 凸模圆角半径
一般情况下,凸模圆角半径等于或略小于工件内侧的圆角半径,对于工件圆半径较大(R/t>10).而且精度要求较高时,应考虑回弹的影响,将凸模圆角半径根据回弹角的大小作相应的调整,以补偿弯曲的回弹量
b 凹模圆角半径
工件在压弯过程中,凸模将工件压入凹模而成形.凹模口部的圆角半径R凹对于弯曲力和零件质量产生不明显的影响,凹模圆角半径R凹的大小与材料进入凹模的深度,弯边高度和材料厚度有关(见图3.6-3),在一般情况下,可用式(4-11)确定R凹
R凹=(2~6)t
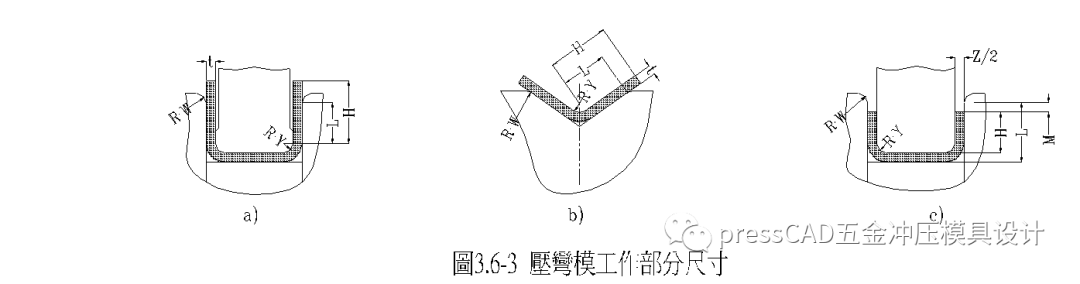
在实际应用中也可根据制件的弯边高度H和弯曲深度L以及材料厚度t等因素,按表3.6-1选取R值.
表3.6-1 凹模圆角半径R凹选用表
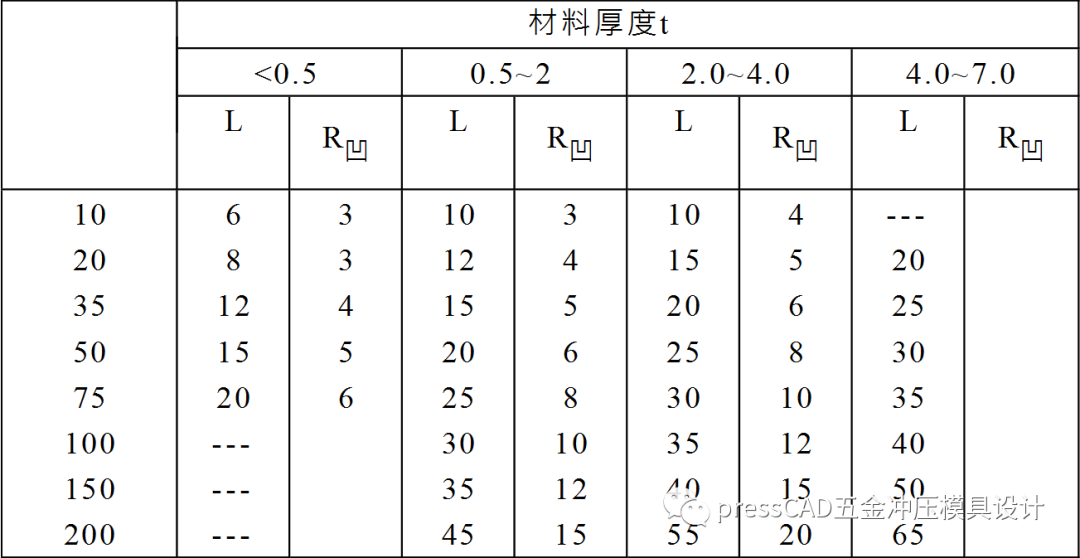
对于校正弯曲,如图3.6-3c所示,图中凹模M值可根据材料厚度在表3.6-2中选取
表3.6-2 校正弯曲时M值的选用表

成形是依靠材料流动而不是依靠材料分离使材料改变形状和尺寸的冲压工序的统称﹒包括抽凸,压印,翻边(抽芽),胀形,缩口等.下面以我们经常遇到的几种形状作一介绍.
1 抽凸1. 抽凸成形是一种使材料发生拉伸,形成局部的凹进或凸起,借以改变毛坯形状的方法
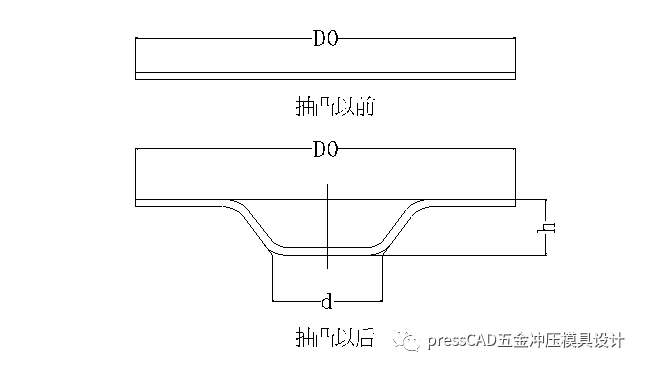
如上图,毛坯的外形(D0)并未发生变化.
2. 抽凸过程中要求校核材料的延伸率
(L1-L)/L<=(0.7~0.75)δ
式中 L1-----抽凸成形后沿截面的材料长度,单位为mm;
L------抽凸成形前材料原长,单位为mm;
δ-----材料的延伸率.
对不符合上面延伸率要求的成形要增加工序,先压成如下图(a)形状,再整形压成如下图(b)形状.
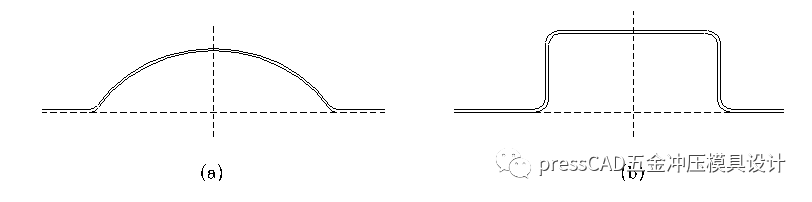
3. 对薄料(t<1.5mm)的小零件(面积<2000mm2)作抽凸成形时的压力可用以下经验公式计算
F=AKt2
式中 F------抽凸成形时所需的压力,单位为N
A------抽凸成形的面积,单位为mm2
K------系数,对于钢为200~300N/mm4
t-------料厚,单位为mm
2 翻边1. 圆孔的翻边(抽芽)
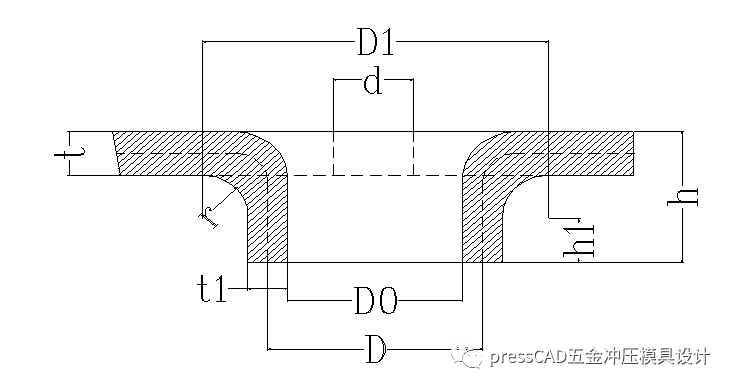
翻边系数
K=d/D
式中 K------ 系数
d-------预冲孔直径
D------抽芽后直边的平均直径
K值愈大,变形程度愈小; K值愈小,变形程度愈大.
对低碳钢K值大约为0.4
对硬铝K值大约为0.85
b.毛坯计算
预冲孔直径: d=D1-[π(r+t/2)+2*h1]=D-2*(h-0.43*r-0.72*t)
翻边高度: h=(D-d)/2+0.43*r+0.72*t
=d/2*(1-d/D)+0.43*r+0.72*t
=D/2*(1-K)+0.43*r+0.72*t
翻边后 t1=t*sqrt(d/D0)
c.翻边力的计算
F=1.1*π*t*δ(D-d)
式中 F------翻边力,单位为N
δ-----材料的屈服强度,单位为Mpa
D------翻边直径,单位为mm
d------毛坯预冲孔,单位为mm
t------毛坯厚度,单位为mm
无预孔的翻边力要比有预孔的翻边力大1.3~1.7倍.
d.翻边凸模与凹模之间的间隙
一般圆孔翻边凸凹模之间的间隙(单边)可控制在(0.75~0.85)t,使直壁稍为变薄以保証竖边成为直壁.
2. 非圆形孔的翻边
非圆孔翻边预冲孔的大小和形状要根据翻边的形状分段考虑,直线部分可按弯曲变形,凹圆弧部分可为翻孔变形,凸圆弧部分可为拉深变形,最后将展开后的线段平滑连接.
非圆孔翻边时的翻边系数要比圆孔翻边时的翻边系数小些,一般
K’=(0.85~0.9)*K
3. 变薄翻边

a.变薄翻边要有强有力的压边,试验証明:一次工序中的可能变薄量达
t/t1=2~2.5
b.对中型孔的变薄翻边,一般是采用阶梯形环状凸模在一次行程内对坯料作多次变薄加工来达到产品要求的.
c.预冲孔尺寸的计算方法:
当r<3时
d0=sqrt((d3*d3*t-d3*d3*h+d1*d1*h)/(h-h1-r))
当r>=3时
d0=sqrt((d1*d1*h-d3*d3*h1+π*r*r*D1-D1*D1*r)/(h-h1-r))
4. 外缘翻边
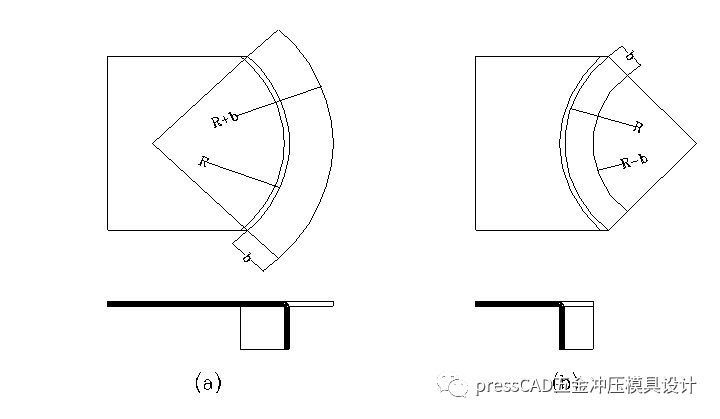
a.有两种形式:
凸轮廓翻边,也叫压缩类翻边,如上图(a)所示;
凹轮廓翻边,也叫拉伸类翻边,如上图(b)所示;
b.变形程度用下式表示:
压缩类: E=b/(R+b)
拉伸类: E=b/(R-b)
c.有压边的外缘翻边力可以下式计算:
F=L*t*δ*K+F压=1.25 *L*t*δ*K
式中
F------翻边力
L------弯曲线长度
t-------料厚
F压----压边力,为(0.25~0.3)F
K------系数,近似为0.2~0.3
3 压印1. 压印零件的厚度精度一般可达到±0.1mm,最高可达到±0.05mm,压印所需的压力,可以按下式计算
P=q*S
式中 S------零件的投影面积(mm2)
q------单位面积压力(公斤/mm2)
2. 如果压入深度h≦(0.3~0.4)t,则压印在光面凹模上进行;如果压入深度h>0.4t,需在凹模上按凸模作出相应的凹槽
