来源丨华创证券
导读
全球方形电池代表企业:宁德时代、比亚迪、三星SDI等;软包电池代表企业:LG、SKI、AESC;圆柱电池代表企业:松下、LG、三星SDI等。未来动力电池技术路线的比较,或将中期维度影响各类企业市场份额的变化。
在行业早期进行电池包设计过程中,根据经验统计,圆柱电芯的模组成组效率约为87%,系统成组效率约为65%;软包电芯模组成组效率约为85%,系统成组效率约为60%;方形电芯的模组成组效率约为89%,系统成组效率约为70%。虽然之后经过数代的方案迭代,逐步提高了模组和系统的电芯成组效率,但是由于其在动力电池成本绝对值中依然占有较大比例,所以该环节持续推进的结构设计优化,对降低动力电池成本依然有重要意义。
一、Pack结构优化有助于动力电池成本降低
(一)Pack结构优化对降低电池成本有较大空间
1、从电芯(Cell)到模组(Module)再到电池包(Package),电池Pack基本情况介绍
通过大量公开信息,我们可以知道新能源汽车中动力电池包是单体电芯(cell)通过串并联组合之后,外加一些管理、冷却系统后,形成的驱动汽车行驶的能源储存单元。在当前主流的电池包结构中,一款新能源汽车动力电池包主要由电池包→电池模组→电芯三个层级构成。
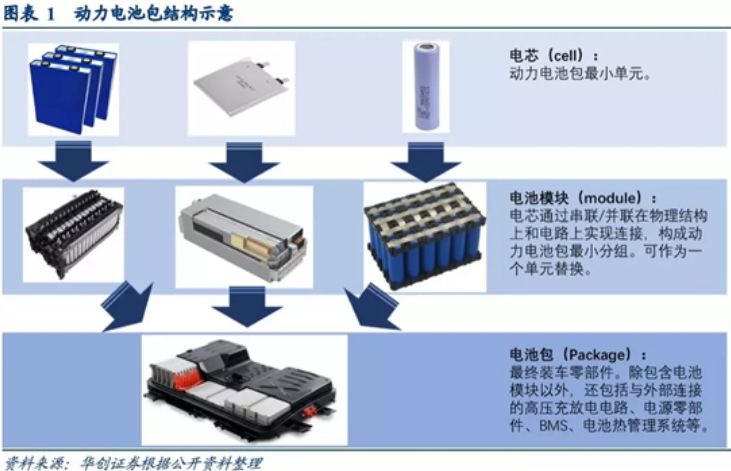
电池通过模组形式安装于电池包中,其物理结构设计可以对电芯起到支撑、固定和保护作用,方便对电芯进行机械强度,电性能,热性能和故障处理等方面管理。
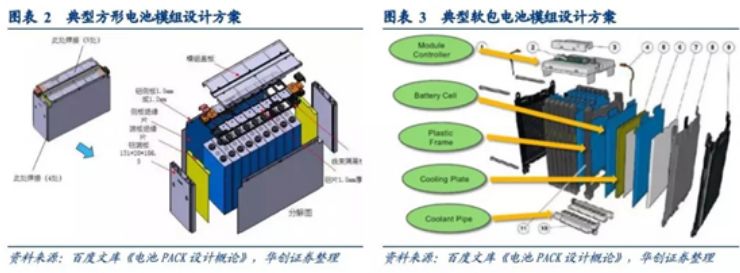
在动力电池包设计过程中,需要考虑结构电气系统安全可维护,电池热管理系统耐久有效,电池包结构防尘/防水设计、电池安全失效泄压及应急处理等等,所以在主流车企在最初进入该领域积累设计和使用经验时,均会优先实现在实现设定功能情况下,预留一定的冗余空间。此过程,自然在推高动力电池包BOM成本同时,降低电池包的能量密度和使用性能。
2、电池Pack加工环节成本占比大,具有降低空间
在行业早期进行电池包设计过程中,根据经验统计,圆柱电芯的模组成组效率约为87%,系统成组效率约为65%;软包电芯模组成组效率约为85%,系统成组效率约为60%;方形电芯的模组成组效率约为89%,系统成组效率约为70%。虽然之后经过数代的方案迭代,逐步提高了模组和系统的电芯成组效率,但是由于其在动力电池成本绝对值中依然占有较大比例,所以该环节持续推进的结构设计优化,对降低动力电池成本依然有重要意义。
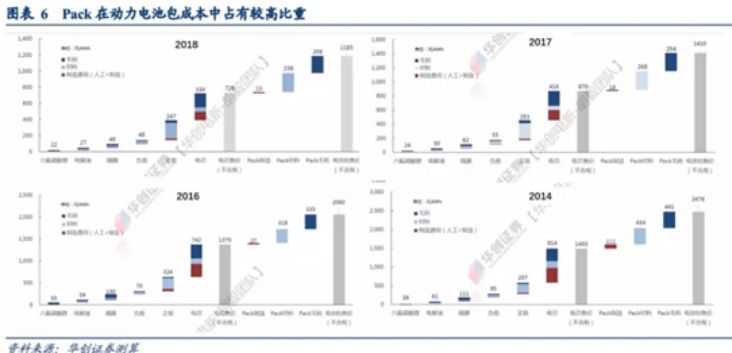
(二)新能源