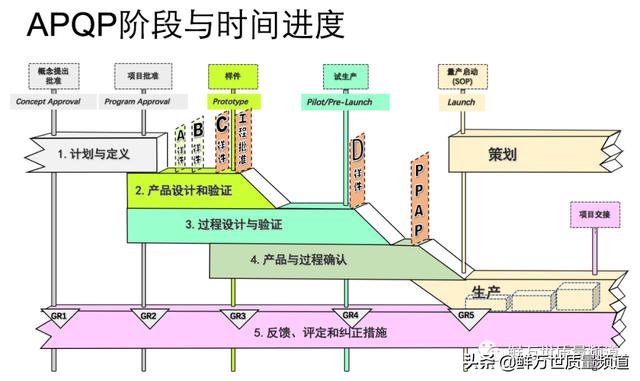
背景
目前市场竞争日益激烈、主机厂的质量要求越来越高、产品的市场生命周期越来越短。制造业的零件制造商如何摆脱这些困境,从产品开发来讲,产品复杂性不断地提高,产品开发数量日益增多,开发周期日益急迫。产品开发的成功,除了自身的研发技术能力之外,主要取决于新产品开发过程中出色且卓越有效的项目管理,这是每个企业成功的关键。也是难以模仿的,花钱也难以买来的核心竞争力之一,不论汽车主机厂的PEP产品诞生过程,还是汽车主机厂对零件厂的APQP、MLA,还是通讯行业华为的IPD,都对项目从策划到产品交货各阶段提出了明确的要求,也对制造业零部件的企业起到了很好的指导作用。说到APQP看似老生常谈,我们早就学过了,但在实际应用过程中大多数工厂只是依附于主机厂的要求,主机厂要什么我们提交什么,完全没有成形的项目管理机制和流程。新产品开发过程中,项目小组未真正有效运行,部门之间协调不好,产品开发职责不清,技术部认为样件提交合格就算研发完成了,质量部说我们是严格按产品验证计划进行试验和测试的,我们的测试工作完成了,工程部说新模具已经制作完成了,生产部最后说反正别影响我的产能就行了。大家错了吗?单个看来都没错,大家的KPI都实现了,好像各个部门都完成了工作任务,但到了批量生产就是漏洞百出,造成主机厂的整机质量问题不断,甚至带来严重的召回事件。特别是首次与主机厂合作,严重影响质量的同时,产品的开发周期不断延迟,产品迟迟不能上市,将给后续的合作带来极为不利的影响,甚至后续很难再度合作。
什么是APQP?
APQP是一个过程,是一种结构化、系统化的方法,用于保证开发的产品满足客户的要求所必须的步骤,促进项目所涉及的每一个人能确保分配的工作任务按时完成。有效的APQP也表达了公司的高层管理者对实现顾客满意的承诺。
APQP与IATF16949的相关条款或过程相结合,以达成产品实现的过程:
-产品实现的策划
-与顾客有关的过程
-设计和开发
-采购
-生产和服务的提供
-监视和测量设备的控制
APQP的目标:
-APQP确保有效地与项目团队成员进行沟通;
APQP支持建立跨职能功能的小组,小组成员包括了设计、工艺、制造、采购、质量、销售、现场服务、供方和顾客方面的代表,小组成员来自于各个部门,是一个横向跨部门的组织,小组成员充分的沟通是非常重要的,运用APQP确保有效地与小组成员进行沟通。
-准时完成分配的工作任务;
APQP支持项目计划,项目经理建立跨功能小组后第一项工作是制定项目计划,并绘制成项目进度表,也就是甘特图。所有的小组成员都应在每一个事项、措施和进度上取得一致意见。项目计划表列出工作任务、负责人、起始及完成日期,同时跟踪每一个工作任务的进展,记录每一个工作任务的实际进展。有效的状况报告监控工作任务的实际进展,确保准时完成分配的工作任务。
-预防缺陷、缩小变差和减少浪费;
APQP支持运用FMEA预防缺陷,运用SPC统计过程控制减少变差,在量产启动中运用精益技术与工具减少浪费。
-避免晚期变更,确保产品投产的质量风险降至最低;
APQP支持系统的运用FMEA工具,运用DFMEA分析系统、组件和零部件的失效模式及失效原因或机理,识别和分析可能的设计缺陷,采取措施以确保功能/要求的实现。运用PFMEA分析制造、装配和物流的失效模式及失效原因或机理,识别在制造过程中的影响因素,采取措施以确保过程和所需产品特性的实现。最终实现安全、可靠、经济的产品和过程。
-杜绝或减少质量问题;
APQP支持系统的应用QFD、FMEA、DOE等质量工具,确保产品的功能、可靠性及安全性得到满足。定义和识别特殊特性,并采取措施确保符合性。从原型样件和试生产阶段所获得的经验和教训进行记录,并在量产启动落实了这些措施,最终在量产中杜绝或减少质量问题。
-以最低的成本及时提供优质的产品;
APQP支持产能策划与分析,在量产启动中运用节拍生产、创建连续流作业,使用防错系统,将产品质量植入到生产过程中,不需要后续的检验来保证质量。精益生产就是通过完全排除浪费,在整个系统中实现最大程度的精简。并致力于在制造流程中保证质量,同时遵循降低成本这一原则。最终实现以最低的成本及时提供优质的产品。
-贯穿整个产品生命周期过程。
APQP支持在量产启动时,将APQP的成果移交至生产阶段,项目移交的前提条件是成功完成了PPAP批准。并确保控制计划、作业指导书等能得到落实,直至EOP产品退市。最终实现贯穿整个产品的生命周期过程。
APQP最重的输出是控制计划、PPAP
控制计划涵盖三个不同阶段:
1、原型样件控制计划:是对原型样件制造中的尺寸测量、材料和产品性能试验的描述。如果顾客要求时,组组应有原型样件控制计划。在一般情况下,对尺寸测量的描述使用全尺寸测量计划及报告来完成,材料和产品的功能性能试验,使用DVP&R设计验证计划及报告来完成。所以鲜老师认为,在逻辑上我们的控制计划有三类,涵盖了三个不同的阶段,但在原型样件阶段,一般采用全尺寸和DVP&R来代替原型样件控制计划。
2、试生产控制计划:是在原型样件后及正常生产前,进行的尺寸测量、材料和产品性能试验的描述。在正式工装准备就绪,试生产之前编制试生产控制计划,由于试生产是在一定有限的时间内,4-8小时或一个班的试生产,针对特殊特性按较高的比例进行抽样检验。
3、生产控制计划:是对产品/过程特性、过程控制、试验和测量系统全面文件化的描述。
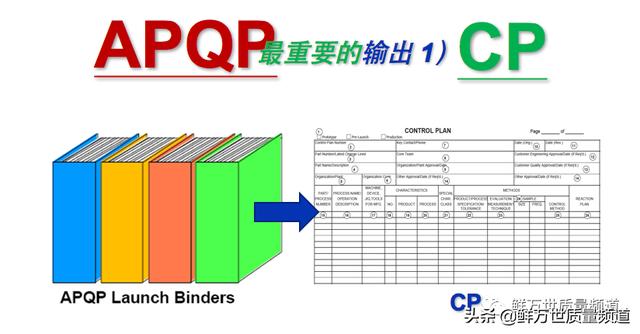
具体的差异可以见下的对比表:
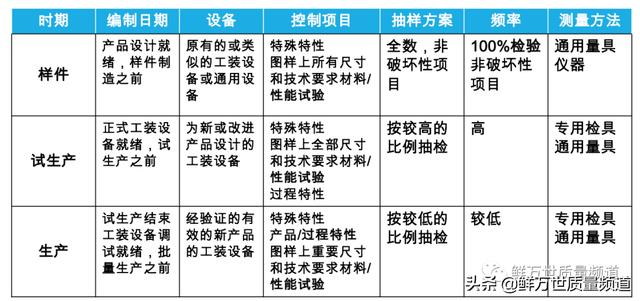
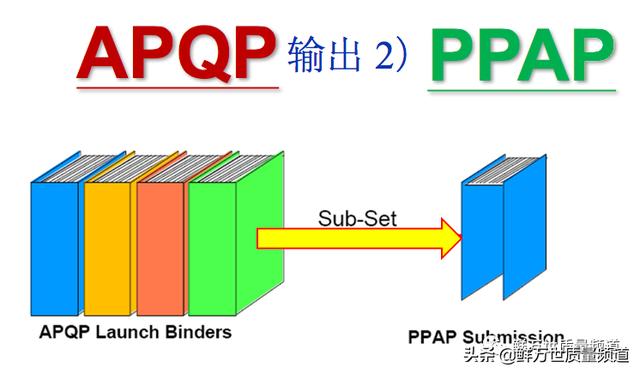
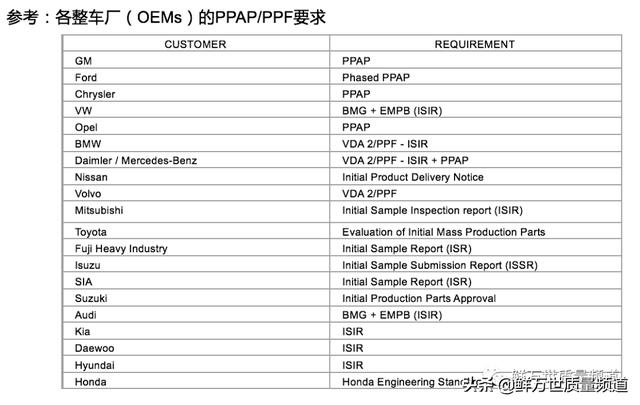
在新产品开发项目管理中,把项目划分为若干阶段,并设若干里程碑,里程碑是指项目开展过程中关键的时间节点,具体标识性的交付物,如样件提交、PPAP通过等,代表着项目开展有实质性的进展。把项目的全过程分为若干阶段,如APQP将项目管理分为五大阶段。AIAIG的APQP在各个阶段进行总结项目交付物,及时发现并评估项目风险,便于项目的管控。
AIAG的APQP将产品开发划分为五大阶段:
1、计划与定义
2、产品设计和验证
3、过程设计和验证
4、产品与过程确认
5、反馈、评定和纠正措施
同时,将产品开发设立了五个里程碑:
1、概念提出批准
2、项目批准
3、样件
4、试生产
5、量产启动
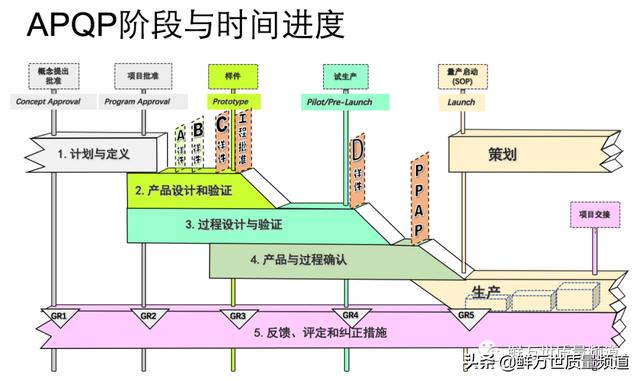
鲜老师建议不要去直接拷贝APQP的五大阶段,企业在新产品开发中,须结合企业的实际情况,定义组织的开发阶段,并结合顾客的里程碑,确定各阶段的时间节点或里程碑,包括关键路径。具体开展行动任务,落实各项开发任务,产生必要的各项设计输出。
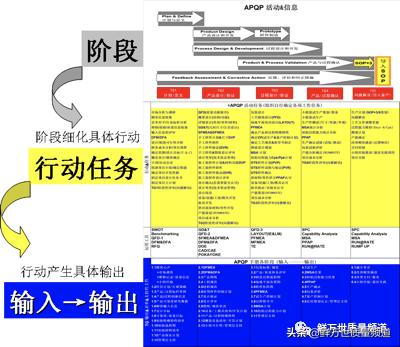
Prototype 原型样件或手工样件
-产品开发过程,进入产品DV 阶段进行prototype样件试制,这个阶段主要目的是尺寸验证,一般手工样件会做2-3 次左右,为正式开模打下良好的基础。
-手工样件依据3D 数模为基础,利用手工方式或借助简单工具由研发工程人员制作。然后对样件进行尺寸,进行性能、材料的验证。(性能为大体性的参考性能标准,材料一般出具原材料报告就可以,不是很严格)。
-在DV阶段验证完毕后,一般图纸就正式冻结了,意味着设计完成。DV阶段可以使用软工装或简易工装,而后面的阶段都是使用硬工装。软工装是指临时的,试验性质的工装,没有大规模生产能力,寿命短。
工装样件
-在产品开发过程中,处于设计阶段的后半程。主要用于性能、制造可行性及品质可行性方面的评价,只是没有将生产节拍纳入考量。
-DV阶段以后,由于设计基本已经确定,OTS的主要的目的就是验证硬工装的能力(主要是模具和夹具方面),一般为20到30件。
-只有获得此验证或认可才说明制造过程已经初步具备了大规模生产要求的硬工装和生产条件了。
-OTS必须是以后量产时要用的硬工装,尽量使用批量生产的条件去制作工装样件,只不过在操作者,现场,设备和工作单元等方面可以与量产时有所不同。
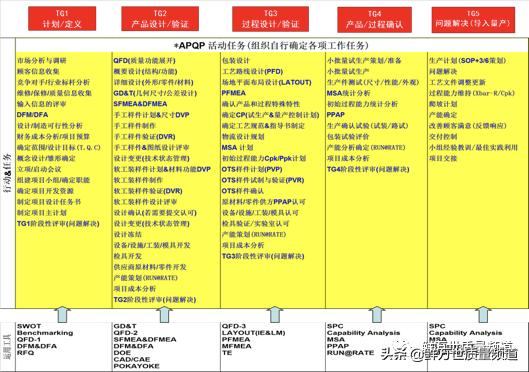
APQP虽然将新产品开发划分为五大阶段,但没有分配具体的工具任务,以上的APQP的活动任务,企业自行确定各个阶段的工作任务,并在各个阶段各项工作任务中,应利用适当的工具/技术方法。
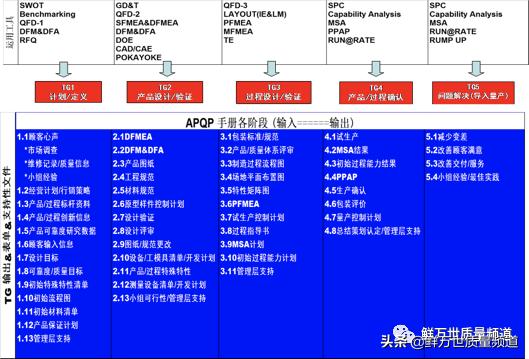
在APQP的各项工作任务中,利用适当的工具/技术方法,输入和输出49项文件。鲜老师认为由于AIAG无法统一所有企业的工作任务,只能规定了49项输入和输出文件。这样统一了质量策划的输出文件,是一项非常突出的成果,为中小企业规范化地进行先期质量策划活动是非常有利的,但这样也大大限制了APQP的发展,多数公司以为产品开发的核心工作是输出这49分文件,那就是大错而特错了。
建议的做法是企业根据自己的特点,制定了新产品开发所需的工作任务,然后在产品开发时间节点设置了关键的里程碑,小组成员在完成每一项工作任务时,输出了所规定的文件,文件只是完成活动的证据,我们要将精力集中在工作任务上。
比如:过程流程图就是一份文件,是在第三阶段过程开发时输出的,试问一下,是什么工作任务输出了过程流程图呢?难道大家想到的是“制作过程流程图”、“绘制过程流程图”吗?鲜老师认为不是这样的,在过程开发阶段,工艺开发的第一步,就是进行工艺路线设计,根据初始的工艺路线,将工序分解到过程步骤或工位,确定每一过程步骤或工位要达成的产品特性或工艺目的。也就是说,过程开发的工作任务是“工艺路线设计”,输出了“过程流程图”。APQP除了缺少工作任务之外,核心的49份文件中缺少了供应商开发、新设备工装开发与验收、新检具开发与验收等相关的重点内容。不论APQP如何的不尽人意,但作为汽车行业零部件的质量策划的基础,还是不错的。
APQP重要说明了产品和过程设计开发的五个阶段,明确了每个阶段的输入和输出的文件要求,但缺少里程碑时间节点。实际上APQP只是项目管理的初级阶段,规定了每个阶段的输出文件,并没有工作任务,也没有成熟度评价的要求,而MLA更像是一个提高班,我们无法确定每一个组织要做什么具体的工作任务,因为具体的工作任务与要开发的产品相关。但我们规定了里程碑的时间节点上,进行评审,从而确保产品在开发过程的成熟度水平。
最近几年,随着5G诞生、移动互联网、电气自动化等前沿技术不断的推层出新,使整个行业从整机厂主导向终端消费者转型,如新能源汽车的“四化”转变不断地向消费者的需求转型,电梯主机厂主导的市场也不断有房地产商来介入,如今的项目越来越复杂,越来越不好管,不论是实际还是方法论,都需要项目管理得到提升,甚至是变革。随着IT行业人才的引入,敏捷项目管理也在影响我们传递的制造业保守的项目管理机制,我们与业界的专业人员一起与时俱进、拥抱变化、不断探索出一条既能发挥传统项目管理的优势,又融入了新兴敏捷项目管理及精益项目管理实践的变革之路。我们的项目管理软件,教会项目经理如何利用有限的资源,以最快的速度、最高的质量、最低的成本将产品顺利量产,并推向市场,这才是项目管理的真谛所在。