据统计,75%的电子研发项目因PCB设计缺陷导致延期,而免费打样服务正成为破解这一难题的利器。
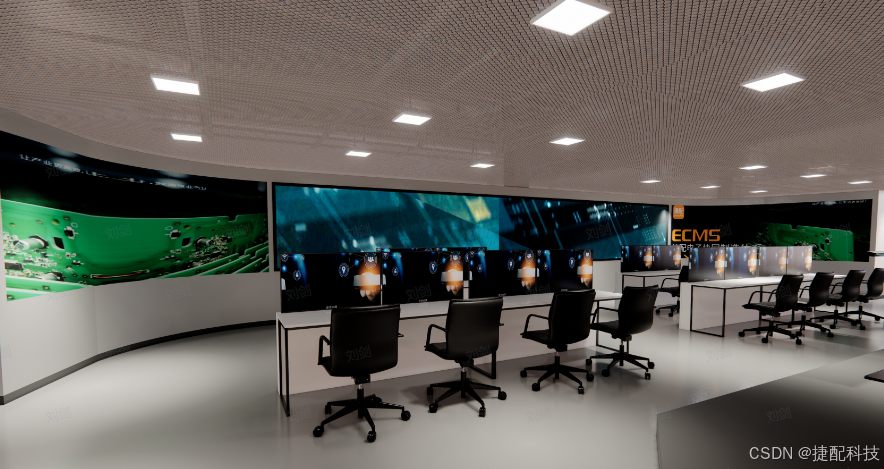
一、PCB打样有什么用?
不同于传统认知中的"简单试产",现代打样已演变为工程验证系统:
- 功能验证:某无人机厂商通过10次迭代打样,将陀螺仪信号干扰降低40dB
- 工艺验证:在Mini LED背光模组中,0.2mm超薄板打样发现钢网变形问题
- 成本验证:某IoT企业通过对比4种板材,将BOM成本降低28%
二、尺寸设计原则:
1. 标准尺寸的经济性
主流免费打样服务多采用10×10cm基准尺寸,超出部分按面积阶梯收费。建议:
- 优先采用100×100mm标准尺寸
- 拼板设计时保留3mm工艺边
- V-cut分割线宽度控制在0.4mm以内
2. 特殊场景的尺寸策略
- 可穿戴设备:建议采用异形板设计
- 高频电路:保持关键信号距板边≥3mm,避免边缘效应
- 高密度布局:8层板建议最小线宽/线距4/4mil
三、如何科学规划及选择?
1. 文件优化三原则
- Gerber文件采用RS-274X格式
- 钻孔文件区分PTH/NPTH
- 阻焊层开窗扩大0.1mm
2. 工艺选择的门道
- 普通消费电子:选用FR-4板材1.6mm厚度
- 高频场景:优先选择罗杰斯4350B(捷配PCB库存常备)
- 柔性需求:选用0.2mm厚聚酰亚胺基材
3. 质量检验清单
- 使用4线检测法测量阻抗
- 进行3次热循环测试(-40℃~125℃)
- 用10倍放大镜检查焊盘完整性
四、常见误区
误区1:层数越多越好
某工业控制器项目盲目采用8层板,后经工程师建议改用6层盲埋孔设计,成本下降40%且性能达标。
误区2:过度追求最小线宽
在12V电源模块中,将0.2mm线宽改为0.3mm,载流量提升50%且良率提高。
误区3:忽视表面工艺
经对比测试,选择沉金工艺的接触点寿命比OSP工艺延长3倍,更适合高频连接器场景。
五、打样到量产该如何实现?
建议采用三阶段验证法:
1. 功能验证板(1-2pcs)
2. 工程验证板(5pcs含不同批次物料)
3. 生产验证板(带批次号追踪)
支持阶梯报价体系的厂商,可确保从5pcs到5000pcs的无缝过渡。其特有的云端协同平台,能实时同步DFM检查结果,平均缩短开发周期18天。